Revolution im Automobilbau
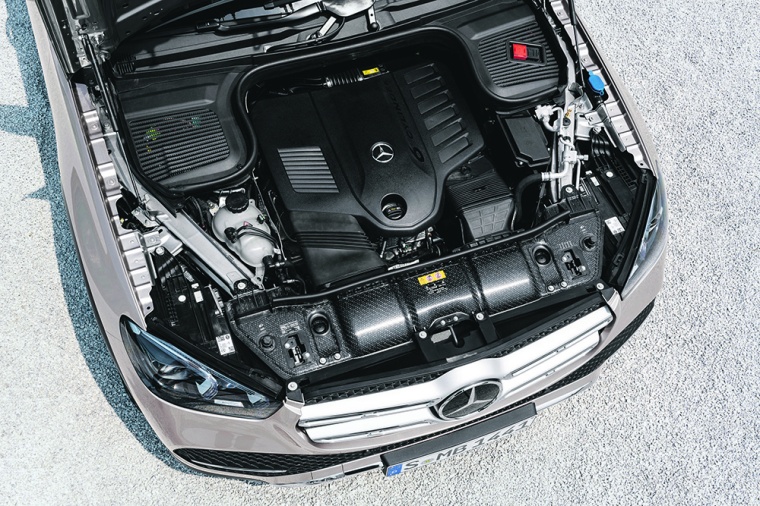
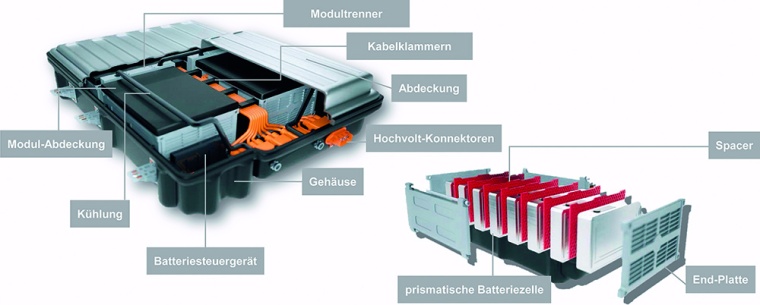
Die Klimaziele der Europäischen Union (EU) zu erreichen, erweist sich als Herkulesaufgabe. Sie verlangt ein globales Umdenken sowie konkrete Maßnahmen wie die Substitution von Verbrennungsmotoren durch effiziente, emissionslose Antriebstechnologien. Innovative Produktlösungen leisten einen wichtigen Beitrag zur richtungsweisenden Modernisierung von Mobilität, Transport und Straßenverkehr.
Die Einführung emissionsloser Kraftfahrzeuge – sowohl auf der Straße als auch auf dem Wasser – auf Basis von Elektroantrieben oder der Brennstoffzellentechnologie erweist sich im Kontext der aktuellen Klimaentwicklung und -ziele als sinnvoll und richtungsweisend. Schließlich zählt der Straßenverkehr mit zu den Hauptverursachern des Treibhausgases Kohlendioxid (CO2). Hinzu kommt die Tatsache, dass sich Fahrzeuge künftig autonom, sprich führerlos durch den Straßenverkehr bewegen sollen. Prototypen, die diese neuen Anforderungen adressieren, offenbaren den Bedarf an neuen Materialien und Technologien, etwa zur Herstellung intelligenter Sensoren oder gleichsam leichter und formstabiler, bruch- und zugfester Kunststoffe für Karosserie, Batteriegehäuse oder Fahrgastzelle. Kurz gesagt, nachhaltiger Automobilbau stellt hohe und zunehmend komplexere Anforderungen an die eingesetzten Werkstoffe. Ihre Umsetzung gleicht bei genauer Betrachtung einer kleinen Revolution.
Orange ist das neue Schwarz
„Elektroantriebe erfordern eine andere Konzeption des Antriebsstrangs, als wir ihn von Benzin- und Dieselfahrzeugen her kennen“, sagt Axel Tuchlenski, Leiter der globalen Forschung und Entwicklung im Lanxess-Geschäftsbereich High Performance Materials (HPM). Der Spezialchemiekonzern leistet mit innovativen Kunststofflösungen einen wertvollen Beitrag für die Automobilindustrie und ihre Zulieferer und damit für eine nachhaltige, sichere Mobilität von morgen.
Der Blick unter die Motorhaube macht den Unterschied augenfällig: „Statt schwarzer Kunststoffbauteile, durch die in Otto- und Dieselaggregaten die benötigten Medien fließen, dominieren Elektrokabel in Kunststoffummantelungen mit orangefarbenen Steckverbindungen das Bild des elektrischen Antriebsstrangs“, erklärt Tuchlenski. Die für den Antrieb von Elektroautos erforderlichen elektrischen Spannungen zwischen 300 V und 800 V bedingen eine besondere Sicherheits- und Schutztechnik sowie Polymerwerkstoffe, die mehr als die Funktion elektrischer Isolatoren erfüllen.
„Lanxess bietet für die Hochvoltanwendungen in der Elektromobilität eine breite Palette an orange eingefärbten Polyamid- und Polybutylenterephthalat-Compounds an, die über das in Elektromobilen benötigte Eigenschaftsprofil verfügen“, erläutert Tuchlenski. Der Kunststoffexperte hebt ein besonderes Talent der orangefarbenen Compounds hervor, das sich in puncto Sicherheit als zentral darstellt: „Die Standardausführungen zeigen nach 1.000 Stunden Alterung bei 130 °C noch eine ausreichend hohe Farbstabilität. Wärmestabilisiert haben sie sogar das Potenzial, 1.000 Stunden bei 150 °C zu überstehen, und zwar ohne dass sich der orangene Farbton in relevanter Weise verändert“, erklärt Tuchlenski.
Die Farbstabilität des Materials ist ein besonders wichtiger Parameter. Denn es ist wichtig, dass sich auch noch nach Jahren sicherheitsrelevante Stellen im Antriebsstrang rasch erkennen lassen und Unfälle vermieden werden.
Aus Polyamid-6-Compounds lassen sich zudem halogenfrei additivierte, glasfaserverstärkte, hochfeste, flammgeschützte Konstruktionswerkstoffe für Strukturbauteile herstellen, etwa Gehäuse, Zellrahmen und Endplatten von Batterien oder Hochvoltsteckern, die über eine hohe mechanische Stabilität verfügen müssen. Durch Zugabe geeigneter Additive gelingt es auch, die Kriechstromfestigkeit der Compounds sowie ihre Widerstandskraft gegen Elektrokorrosion zu erhöhen.
„Nachhaltiger Automobilbau stellt hohe und zunehmend komplexere Anforderungen an die eingesetzten Werkstoffe.“
Weniger Gewicht, mehr Funktionalitäten
Am Standort Dormagen entwickelt der Geschäftsbereich HPM die Eigenschaften seiner Hochleistungskunststoff-Compounds stetig weiter, nicht zuletzt im Kundenauftrag. Eine zentrale Triebfeder, die Unternehmen der Automobilbranche mit Lanxess kooperieren lässt, ist das Ziel, polymerbasierte Verbundwerkstoffe einzusetzen, die über das gewünschte oder geforderte Eigenschaftsprofil verfügen, allerdings leichter im Gewicht sind als die üblicherweise eingesetzten metallischen Werkstoffe. „Häufig geht es nicht nur um Substitution, sondern obendrein auch um optische und funktionelle Verbesserungen gegenüber konventionell hergestellten Bauteilen sowie eine Steigerung der Produktivität bei deren Herstellung“, berichtet Tuchlenski.
Im GLE-SUV von Mercedes-Benz z. B. wird ein Frontendträger aus dem Faserverbundwerkstoff Tepex von Lanxess verbaut. Bei der Entwicklung des Bauteils ging es nicht allein um Gewichtseinsparung, sondern auch um die Herstellungsweise. Gefertigt, umgeformt und mit zahlreichen Funktionen ausgestattet wird das zweischalige Tepex-Bauteil in der Hybrid-Molding-Technologie auf einem Werkzeug und im Anschluss mittels eines Schweißverfahrens gefügt.
„Dieser hochintegrierte One-Shot-Prozess – der sich im Übrigen auch zur Herstellung von Türstrukturen, Stoßfängern, Elektronik- und Laderaummulden, Batteriegehäusen und -abdeckungen, Unterbodenverkleidungen und anderen Fahrzeugstrukturbauteilen bestens eignet – ist sehr wirtschaftlich und zeichnet sich durch kurze Zykluszeiten aus. Der Frontendträger wiegt rund 30 % weniger als vergleichbare Ausführungen in Metall und weist eine exzellente Crash-Performance sowie Torsionssteifigkeit auf“, erklärt Henrik Plaggenborg, Leiter der Abteilung Tepex Automotive im Lanxess-Geschäftsbereich HPM. Obendrein, sagt er, ließen sich Lackierschritte einsparen sowie weitere Funktionalitäten integrieren, was sich unter dem Strich vorteilhaft auf die Herstellungskosten von Fahrzeugen jeglicher Art auswirken kann.
Als weiteres Beispiel nennt Plaggenborg den Audi A8, der mit zwei elektrisch verstellbaren Einzelrücksitzen angeboten wird, deren Sitzschalen aus einem Polyamid-6 basiertem Tepex, die auch durch die Anwendung der o. g. Hybrid-Molding-Technologie, hergestellt werden. Konventionell werden für die Sitze Metallschalen verwendet, die auf die Unterkonstruktion verschraubt werden. Deren Herstellung erweist sich allerdings als aufwändig, bestehen sie doch aus zahlreichen Einzelteilen, die in mehreren Arbeitsschritten u. a. durch Schweißen zusammengefügt werden müssen. Die Sitzschale aus Tepex hingegen wird in großer Serie in nur einem einzigen Prozessschritt zu einem montagefähigen Bauteil verarbeitet und mit zahlreichen Funktionalitäten ausgestattet. Das Resultat, ergänzt Tuchlenski, vereinfache nicht nur die Montage und Demontage im Servicefall, sondern führe zudem zu einer Einsparung von Kosten und einer Gewichtsreduktion von 45 % gegenüber konventionellen Sitzschalen.