Henkel: Gezieltes Investment für mehr Gesamtanlagen-Effizienz
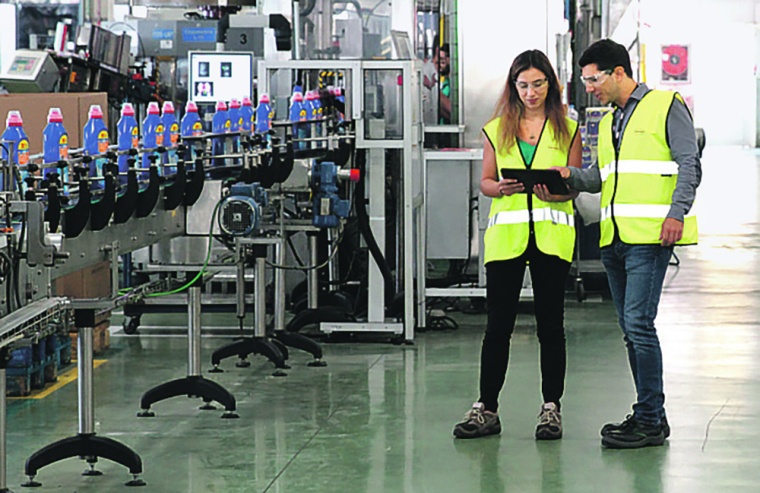
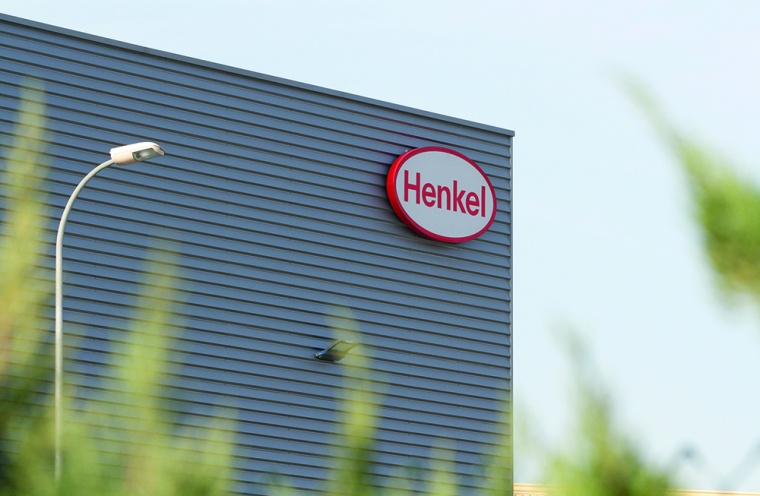
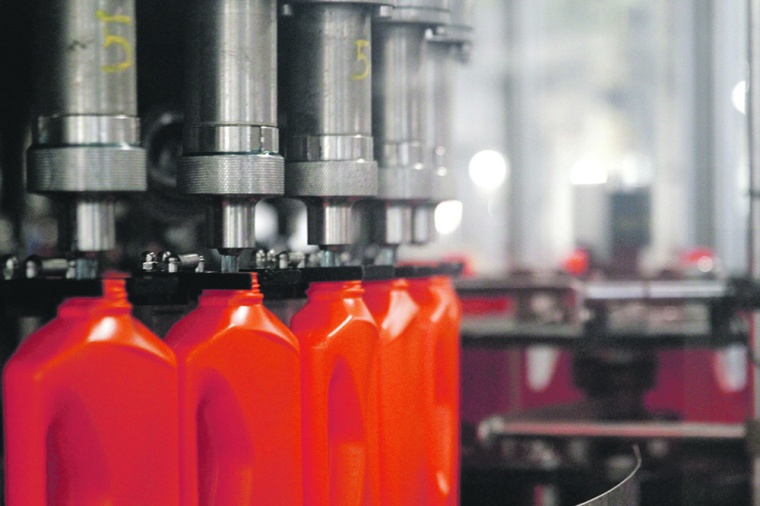
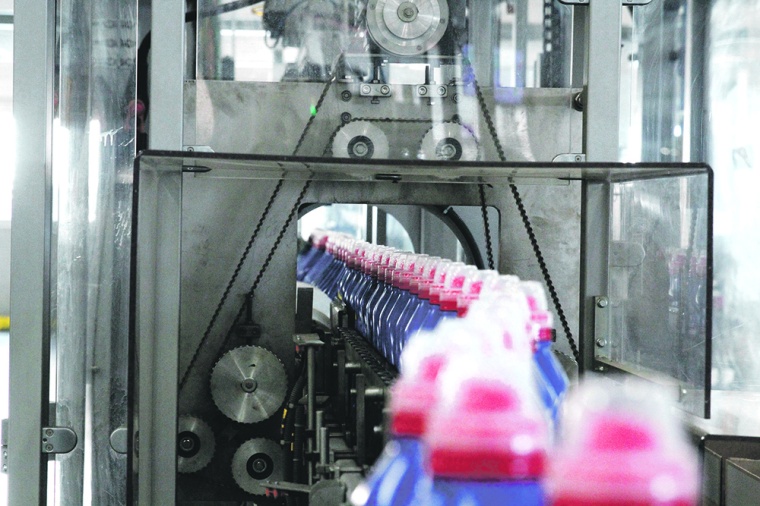
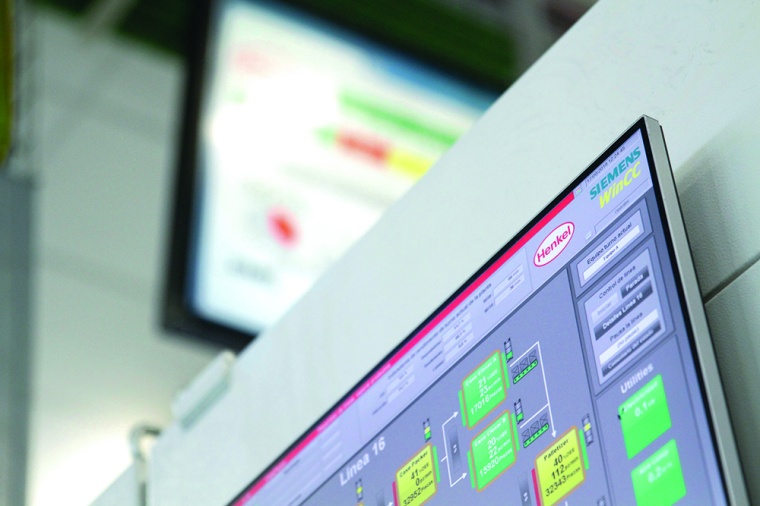
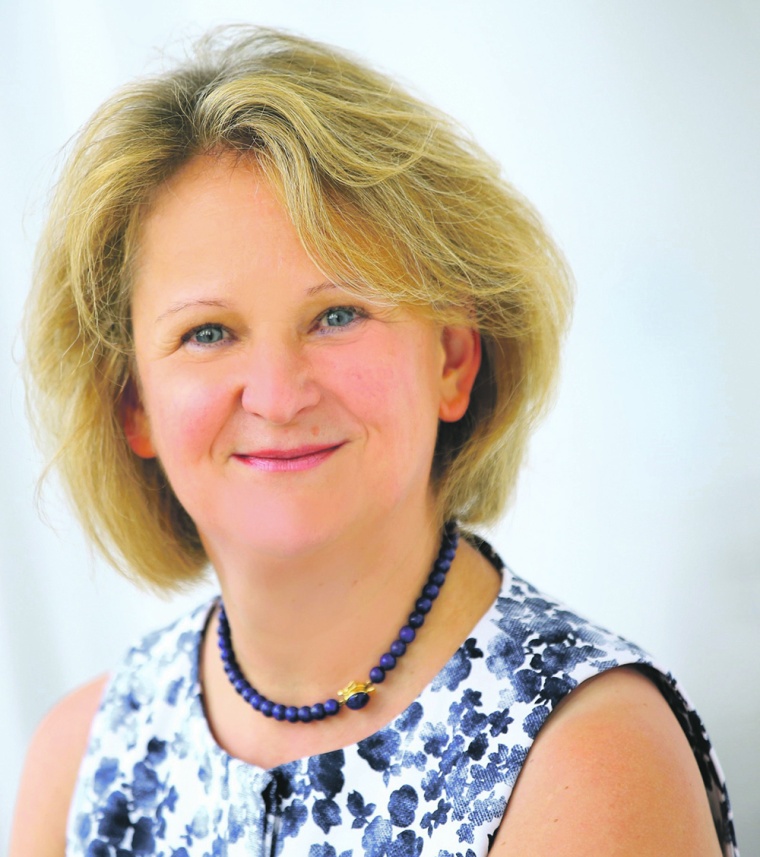
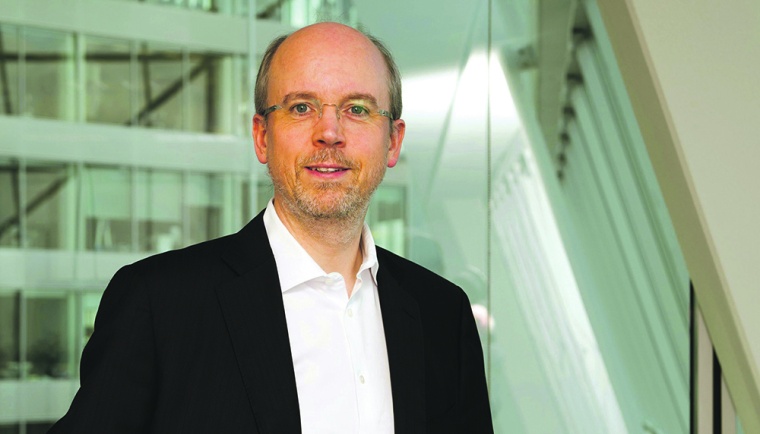
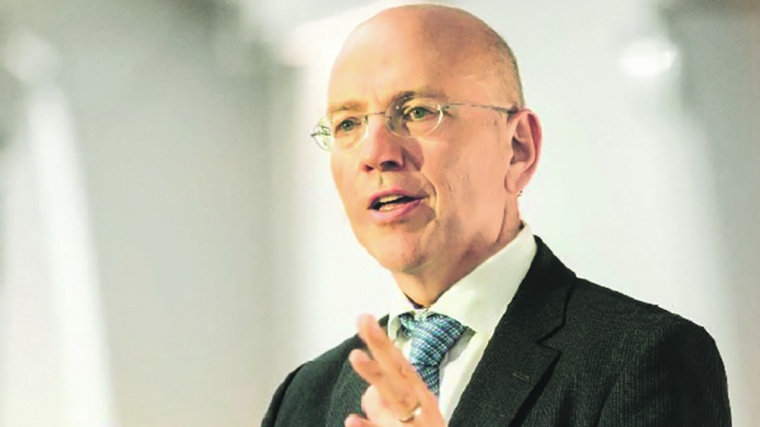
Als globaler Konzern produziert Henkel an mehr als 30 Standorten weltweit Wasch- und Reinigungsmittel. Eine der strategischen Prioritäten von Henkel ist es, die Digitalisierung des Unternehmens zu beschleunigen einschließlich einer integrierten Supply Chain. Möglichst alle Informationen sollen in das Henkel Digital Backbone (globales System zur Sammlung und Visualisierung aller produktionsrelevanten Daten) einfließen und dort die Nutzung von Netzwerkeffekten und Best Practice Sharing ermöglichen.
Bei den Abfüll- und Verpackungslinien für Flüssigwaschmittel wurde eine maßgeschneiderte Lösung von Siemens implementiert. Diese führt im Werk in Montornés bei Barcelona, Spanien, zu Produktions- und Qualitätsverbesserungen. Hervorzuheben sind die Standardisierung von Schnittstellen, die Liniensteuerung der einzelnen OEM-Maschinen sowie Datenanalyse und Reporting, durch welche sich die Verbesserungspotenziale identifizieren lassen.
Digitalisierung als Teil der
Unternehmensstrategie von Henkel
„Accelerate Digitalization“ ist Teil der Unternehmensstrategie von Henkel. Dank Industrie-4.0-Anwendungen wird die digitale Transformation der globalen Supply Chain und der gesamten Organisation vorangetrieben. Die Ziele sind eine kürzere Time-to-Market durch eine lernende Produktion, Plug & Play Equipment, die Reduzierung der Reaktionszeiten beim Auftragseingang sowie eine Verbesserung der Qualität bis hin zur Null-Fehler-Produktion.
Dirk Holbach, Corporate Senior Vice President International Supply Chain Henkel Laundry & Home Care: „Für die Digitalisierung der Lieferkette setzen wir auf weitere Automatisierung, vor allem mit dem Einsatz von Robotik, mit der Nutzung von Sensorik sowie mit der Visualisierung von Daten und deren analytische Verarbeitung. Unser Ziel ist es immer, konkrete Handlungsvorgaben abzuleiten und unsere KPIs bezogen auf Kosten und Service zu verbessern. Die digitale Transformation bietet uns große Möglichkeiten, diese entlang der gesamten Lieferkette zu optimieren – von der Planung über die Produktion bis hin zur Logistik.“
Zusätzlich zu den kontinuierlichen Produktionsverbesserungen konnten durch Digitalisierung und insbesondere durch Echtzeiterfassung und -vergleich von Energieverbräuchen die Energiekosten seit 2010 nachweislich bereits um etwa 30 % reduziert werden.
Wolfgang Weber, Corporate Director International Engineering and Digital Transformation bei Henkel Laundry & Home Care, äußert sich dazu: „Die Digitalisierungslösung im Werk Montornés del Vallés war für uns ein strategisch wichtiger Schritt. Wir haben nicht nur unsere Produktionsmaschinen mit dem ERP-System verbunden, sondern auch die Kommunikation der Maschinen untereinander ermöglicht. Zusammen mit einer einzigartigen Lösung zur Steuerung der Linie können wir die Anlageneffizienz besser analysieren und sie mit Hilfe künstlicher Intelligenz in Echtzeit positiv beeinflussen. Anhand von Algorithmen können simultan Verbesserungen des Betriebszustandes berechnet und angewendet werden. Die effizientere Nutzung unserer Maschinen ermöglicht es uns, Produktionskosten gering zu halten und damit die Wettbewerbsfähigkeit unserer gesamten Lieferkette zu steigern.“
Mehr Effizienz durch Vernetzung der Maschinen
Bisher kommunizierten die Maschinen einer Abfüll- und Verpackungslinie von Flüssigwaschmitteln wenig systematisch und eher individuell miteinander. Unterschiedliche Hardware und heterogene Kommunikationsstrukturen erschwerten die Integration, den Datenaustausch und damit die Vergleichbarkeit der einzelnen Linien. 2015 wurde gemeinsam mit Siemens-Experten von Digital Industries aus Deutschland, Österreich und Italien eine Lösung entwickelt, um die Abfüll- und Verpackungslinien effizienter zu gestalten. Das umfasste zum einen die Definition einer Standard-Schnittstelle und die Integration der Steuerungen in der Produktion. Diese Phase war stark von der Zusammenarbeit und dem Austausch mit OEM und Maschinenlieferanten geprägt. Die Linieninformation (Monitoring und Visualisierung) als weiterer Schritt der digitalen Transformation beinhaltete die Überwachung, Steuerung und Kontrolle der Abfüll- und Verpackungsanlagen vor Ort.
Das System wurde unter anderem im Henkel-Werk in Montornés del Vallés (bei Barcelona, Spanien) implementiert, wo Henkel Flüssigwaschmittel für den europäischen Markt herstellt. Die Produktion in diesem Werk ist eine der modernsten und am stärksten automatisierten des Unternehmens.
Der Verpackungsprozess folgt im Anschluss an den eigentlichen Herstellungsprozess des Waschmittels. Die Packaging Line startet mit der Zuführung der Flaschen, die entsprechend ausgerichtet werden. In der nächsten Maschine werden die Flaschen befüllt und die Verschlusskappe aufgeschraubt. Dies passiert bei bis zu 300 Flaschen Produktleistung pro Minute, was hohe Anforderungen an die Maschine stellt. Das Waschmittel muss in der korrekten Menge und mit dem vorgegebenen Druck eingefüllt werden, dabei ist jedoch die Dehnung der Kunststoffflaschen zu berücksichtigen. Im nächsten Arbeitsschritt werden die Label appliziert. Währenddessen faltet eine Maschine Kartonverpackungen auf, in welche die befüllten und etikettierten Flaschen nun roboterunterstützt einsortiert werden. Ist die Schachtel voll, wird diese automatisch verschlossen und mit den erforderlichen Informationen bedruckt. Schließlich werden die Kartons palettiert und die volle Palette foliert. Zwischen den einzelnen Verpackungsstationen sind Kontrollpunkte eingerichtet, die z. B. die Füllmengen oder die korrekte Positionierung des Labels überwachen.
Dabei variieren sowohl die Art des Waschmittels als auch die Flaschengröße – und damit auch Kartonverpackung, Etikettierung und das Packmuster der Palette. Ein Wechsel von Produkt- bzw. Verpackungsgrößen erfordert zum Teil auch ein mechanisches Umrüsten der Maschinen.
Harmonisierung mit Kommunikationsstandards
Ziel von Henkel war es, die OEM-Maschinen unterschiedlicher Hersteller mit eigenen Softwarelösungen zu harmonisieren und zuverlässige Kommunikationsstandards festzulegen. Die Maschinendaten – z.B. Energiewerte, Status- oder Produktionsdaten – werden über eine Schnittstelle an das zentrale Datensystem übertragen und dort ausgewertet. Der Informationsaustausch zu und von der einzelnen Maschine wurde vereinheitlicht und steht nun als modularer Baukasten zur Verfügung. Die einzelnen Maschinen stehen zudem im Verbund mit vor- und nachgelagerten Maschinen, tauschen über die standardisierte Schnittstelle Daten untereinander und mit überlagerten Systemen, unter anderem dem ERP-System, aus. Als gemeinsame Automatisierungsplattform wurden Totally Integrated Automation sowie Netzwerk- und Kommunikationskomponenten wie Profibus, Profinet, TCP/IP oder S7-Kommunikation festgelegt.
Das plattformunabhängige Protokoll OpenTCP mit optimierter Übertragung vereinfacht die herstellerübergreifende standardisierte Kommunikation, reduziert den Programmieraufwand und schafft Transparenz über die Effizienz und Auslastung der Linien. Man muss lediglich das OPC UA Protokoll kennen, ohne detaillierte Informationen zur Anlage und deren Geräte zu berücksichtigen.
Die Maschinenintegration und -automatisierung wurde standardisiert, die Implementierung und Bedienung der Maschinen signifikant vereinfacht und damit die betriebliche Effizienz verbessert. Jede Maschine verfügt nun über dieselbe PLC-Schnittstelle, und es ist sichergestellt, dass Daten nur über die PackML-Schnittstelle der OMAC (Organization for Machine Automation and Control) ausgetauscht werden. Der große Vorteil für Henkel ist, dass mittels Standardisierung sowohl auf der Maschinen- als auch auf Datenseite eine Vergleichbarkeit verschiedener Abfüll- und Verpackungslinien – innerhalb eines Werkes und global – erreicht wird. Einzelne Maschinen bzw. Komponenten innerhalb der Verpackungslinie können bei Bedarf über Linien und Werke hinweg flexibel ausgetauscht und neue Maschinen schnell eingebunden werden, ohne dass Veränderungen am MES-System bzw. bei der Erfassung der Kennzahlen nötig sind.
Effizienzkontrolle mit Line Monitoring
Das Line Monitoring System (LMS) wurde installiert, um definierte Kennzahlen zu bestimmen. Erfasst werden Qualität (in Form der Höhe des Ausschusses), Verfügbarkeit der Maschinen (in Form des Verhältnisses der produktiven zur Gesamtzeit) und die Produktionsleistung (in Form des Verhältnisses der aktuellen zur maximalen Geschwindigkeit). Aus diesen drei Werten wird die Gesamtanlageneffektivität in Abhängigkeit des verpackten Produktes errechnet. Das übergeordnete MES-System reagiert flexibel auf die Gegebenheiten und berücksichtigt geplante Pausen für die Wartung, Unterbrechungen für Produktwechsel und ungeplante Stillstände. Die Auswertung kann einzelne Tage, Wochen, Schichten etc. je nach Anforderung flexibel abrufen und visualisieren. Der Vorteil: Aus den Reports sind Verbesserungspotenziale rasch ersichtlich, z. B. wenn eine Maschine innerhalb der gesamten Verpackungslinie nicht optimal eingestellt ist.
Das LMS ist die Basis dafür, die Abfüllung und Verpackung zu optimieren. Früher kam bei kurzzeitigen Problemen auch an nur einer Maschine meist die gesamte Verpackungslinie zum Stillstand. Das wurde verbessert. Da die Geschwindigkeit des Verpackungsprozesses aus verschiedenen Gründen schwanken kann, können auch einzelne Maschinen innerhalb der Verpackungslinie in ihren Geschwindigkeiten flexibel an die Gegebenheiten angepasst werden, also angemessen und kontrolliert gebremst und nach Beheben der Fehlerursache wieder beschleunigt werden. Maschinenfehler können schnell identifiziert und die Linie nach Stillständen rasch wieder hochgefahren werden. Ist ein Start-/Stopp etwa im Zuge eines Produkt- oder Verpackungsgrößenwechsels erforderlich, werden die einzelnen Maschinen innerhalb der Verpackungslinie sinnvoll und nach jeweils vorgegebenen Mustern praktisch auf Knopfdruck herunter- bzw. wieder hochgefahren. Durch die kontinuierlichere Fahrweise der Abfüll- und Verpackungslinien ergeben sich Vorteile für die Anlageneffizienz durch weniger Verschleiß und verbesserte Qualität bei der Produktverpackung.
Globale Transparenz der Produktion
Der dritte wesentliche Teil der Lösung ist die lokale Visualisierung der Betriebszustände. Bisher musste der Bediener nach einem Stillstand zuerst an den Bediengeräten der betroffenen Maschinen die Fehlerursachen lokal identifizieren. Nun werden Abweichungen automatisch übersichtlich in einem zentralen Visualisierungssystem angezeigt. Auch Auftragsdaten sind für das Bedienpersonal direkt verfügbar. Dank weltweit standardisierter Darstellung für jede Linie und jedes Henkel-Werk sind Betriebszustände, Abweichungen, Produktionsziele und deren Zielerreichung einfach zu erkennen. Digitalisierung schafft Transparenz, ermöglicht schnelle Reaktionen, verbessert die Produktqualität sowie Anlageneffizienz.
Das Visualisierungssystem stellt zudem Informationen für das Henkel Digital Backbone (globales System zur Sammlung und Visualisierung aller produktionsrelevanten Daten) zur Verfügung und ermöglicht die Nutzung von Netzwerkeffekten und Best Practice Sharing. Die Erfahrungen aus den Maschinenverbesserungen bei realisierten Linien können auf neue Anlagen übertragen werden. Lässt sich deren Hochlaufzeit und Inbetriebnahme reduzieren, steigert das die Effizienz und reduziert Kosten, z. B. weil Bedienpersonal auf eine Dokumentation zurückgreifen kann, Schulungs- und Trainingsaufwände in der Instandhaltung geringer anfallen oder Standardisierung zu deutlichen Einsparungen in Einkauf und Ersatzteilhaltung führt. Die Gesamt-Digitalisierungslösung eingebettet in das Henkel-IT-System, das konsequente Minimieren von Effizienzverlusten und damit verbunden das Optimieren von Investments, führte zu einer Effizienzsteigerung von über 10 %.
OT goes IIoT
Henkel und Siemens sind mit der digitalen Transformation der Abfüll- und Verpackungslinien von Flüssig-Waschmitteln noch lange nicht am Ende. Erweiterungen des bestehenden LIS/LMS um neue Produktinnovationen und digitale Funktionen für eine noch stärker zukunftsweisende Industrie-4.0-Lösung sind in der konkreten Planung. Angedacht sind z. B. eine stärkere Roboter-Integration an den Verpackungsstationen oder die Simulation und Einführung eines digitalen Zwillings. Condition Monitoring und Predictive Maintenance können helfen, Störungen an der Maschine zu vermeiden oder zumindest besser vorher zu sehen und damit Stillstände zu verringern sowie die Produktqualität weiter zu verbessern. Hier kommen dann auch Smart Sensors oder Smart Data Applikationen sowie die weitergehende Analyse der Daten aus dem Henkel Digital Backbone ins Spiel.