Erfolgreiche Kristallisation durch das passende Rührsystem
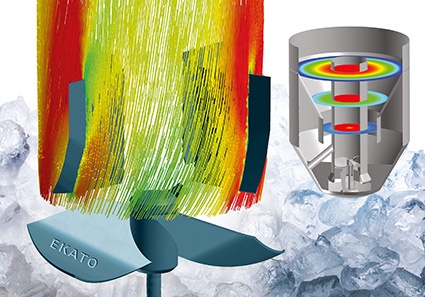
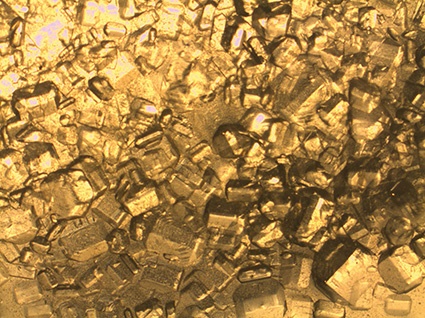
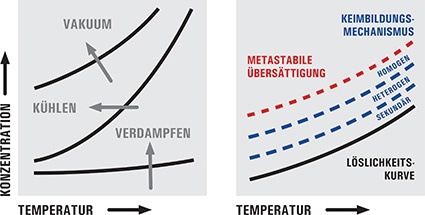

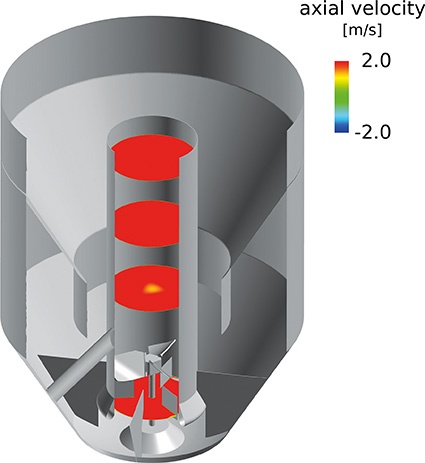

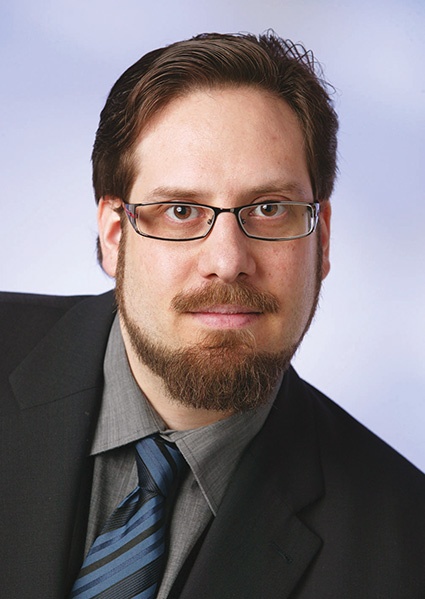
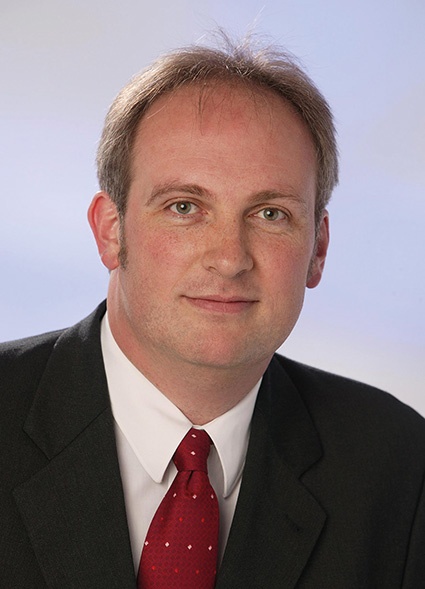
Kristallisation wird durch Kühlung, Verdampfung oder durch Fällung ausgelöst. Dieser Beitrag geht auf die Auswahl des geeigneten Rührsystems und die unterschiedlichen Anforderungen ein.
Kristallisation ist ein Prozessschritt, der in einem weiten Bereich von Anwendungen und Branchen eingesetzt wird, so z. B. in der Chemie, Pharmazie, im Lebensmittelbereich sowie bei der Fällung von Metallsalzen. Die einfachste Methode ist eine statische Kristallisation wie sie etwa bei der Lithium- oder Kochsalzgewinnung eingesetzt wird. Dabei wird in großen Becken, den sogenannten Ponds, das Wasser per Sonnen- und Windenergie über Monate hinweg verdampft. In „Forced Circulation (FC)“-Kristallisatoren wird die Suspension mittels einer Pumpe im Ring gefördert. Das Lösungsmittel wird im Kopfraum abgedampft und mittels Kondensator wieder verflüssigt. Bei gerührten Systemen haben sich zwei Hauptsysteme durchgesetzt. Zum einen der Rührkessel mit vorwiegend axial fördernden Rührsystemen, zum anderen – in erster Linie für die Massenkristallisation – der Leitrohrapparat.
Qualitätsrelevante Parameter in der Kristallisation
Um einen Kristallisator möglichst effizient auslegen zu können, müssen die relevanten Parameter für die Anwendung bekannt sein. Zunächst gibt es drei Hauptrouten um eine Übersättigung zu erzielen: Kühlung, Verdampfung und Fällung. Für die Kühlungs- und Verdampfungskristallisation steht überwiegend die Erzeugung einer bestimmen Zielpartikelgröße im Vordergrund, meist im Bereich von 100 µm bis >2.000 µm.
Ein schonendes Rühren mit hohen Umwälzraten ist erforderlich, um die Kristalle nicht übermäßig zu belasten. Durch die Optimierung des Kühlungs- oder Verdampfungsprofils kann in vielen Fällen die Partikelgrößenverteilung (PGV) positiv beeinflusst werden. So kann z. B. das Band in der Verteilung in die gewünschte Richtung geschoben und gleichzeitig die Verteilung enger eingestellt werden. Auch das Impfen mit Kristallen kann die Qualität in Bezug auf Größenverteilung und Reinheit weiter verbessern. Im Vergleich dazu resultieren aus Fällungsprozessen eher kleine Partikel im Bereich von 1 bis 10 µm. Hierbei kommt es naturgemäß zu Agglomeration, was je nach Prozess erwünscht oder unerwünscht sein kann. Bei der Partikelgrößenbestimmung unterscheidet man deshalb zwischen Primärpartikeln und Agglomeraten, was häufig mittels einer Mikroskopie visualisiert werden kann. Die Rühraufgabe ändert sich in Richtung hoher lokaler Energiedissipation, ggf. in Kombination mit der Dispergierung von Gas. Typische Anwendungsfälle sind gefälltes Kalziumcarbonat (PCC) oder die Fällung in der Aufreinigung von Erzlösungen. Prozessunabhängig bietet ein angepasstes Rührsystem, das Behälter mit Einbauten sowie Zugabe- und Abzugspunkte beinhaltet, deutliche Verbesserungen bei PGV und Energiebedarf.
Kontrollierte Kristallisation
Für eine erfolgreiche Kristallisation muss zunächst das bestgeeignete Verfahren und damit die Methode der Übersättigung festgelegt werden. Ein hilfreiches Tool ist hierbei die Sättigungskurve der Lösung, die die Konzentration des gelösten Feststoffs über der Temperatur darstellt. In Abhängigkeit des Temperatureinflusses auf die Konzentration wird Kühlung (hoher Einfluss) oder Verdampfung (geringer Einfluss) gewählt. Ist die Abhängigkeit im mittleren Bereich, ist eine Vakuumkristallisation sinnvoll. Hier wird gleichzeitig verdampft und gekühlt, da der Siedepunkt des Lösemittels gegenüber dem Normaldruck herabgesetzt ist. Als zweiter wichtiger Parameter dient der metastabile Bereich. Charakteristisch für die Kristallisation ist die Tatsache, dass es nicht sofort zur Keimbildung kommt, sobald man in die Übersättigung eintritt. Je nach Stoffsystem bedarf es der Aufklärung weiterer signifikanter Parameter wie Keimbildungs- und Kristallwachstumskinetik, maximaler lokaler Energieeintrag, Option zur Impfung der Kristallisation etc.
Die Breite des metastabilen Bereichs ist ein Indikator wie empfindlich die Lösung auf Übersättigung reagiert. Grundsätzlich gilt, je mehr Übersättigung möglich ist, desto besser kann man die Kristallisation kontrollieren. Die Kristallisation kann sich durch Scherung (Sekundär), an Fremdstoffen wie Verunreinigungen aber auch an der Behälterwand oder Einbauten (heterogen) oder durch Impfen (homogen) initiieren. Innerhalb des metastabilen Bereichs laufen meist alle drei Formen parallel ab. Ist der Grad der Übersättigung zu groß, dominiert die Keimbildung das Kristallwachstum deutlich, der Prozess wird unkontrollierbar. Dieser Effekt kann zu einer breiten Partikelgrößenverteilung bei gleichzeitig übermäßigem Feinanteil führen.
Der Einfluss des Rührens
Ein optimiertes Rührsystem beeinflusst positiv das Prozessergebnis. Kurze Mischzeiten reduzieren Temperatur- und Konzentrationsgradienten und helfen möglichst gleichmäßige Bedingungen herzustellen. Scherarme Rührorgane reduzieren unkontrollierte Keimbildung durch gleichmäßigen Leistungseintrag und vermindern Kristallbruch. In der Folge werden weniger Feinanteile erzeugt. Die Ausbeute erhöht sich, u. a. weil weniger Feststoff wieder in Lösung gebracht und rezirkuliert werden muss. Auch die nachfolgende fest-flüssig Trennung und die Trocknung vereinfachen sich deutlich, wenn die Partikel gleichmäßig groß sind und das Risiko einer Blockierung der Filter durch Feinanteil wird deutlich verringert.
Batch oder kontinuierlicher Betrieb?
Bei kleineren Anlagenkapazitäten oder bei Mehrzweckanlagen wird üblicherweise im Batchbetrieb gefahren. Es dominiert die Kühlungskristallisation, da die Prozesssteuerung im Vergleich zur Verdampfung deutlich einfacher ist. So kann z. B. über die Kühlstrategie, die unterschiedliche Kühlraten oder auch Haltepunkte beinhalten kann, das Kristallwachstum und die Ausbeute optimiert werden. Der gezielte Einsatz eines Frequenzumformers zur Einstellung der Rührwerksdrehzahl spart im Prozessverlauf Energie. So wird am Anfang nur wenig Energie benötigt um die Lösung umzuwälzen. Erst später, wenn die Kristalle bereits deutlich gewachsen sind, erhöht sich der Energiebedarf, da nun die Partikel in Schwebe gehalten werden müssen um ein gleichförmiges Wachstum zu gewährleisten und gleichzeitig Ablagerungen im Bodenbereich zu verhindern. Bei großen Kapazitäten ist es häufig ökonomischer auf einen kontinuierlichen Prozess umzustellen. Hierbei schlagen kleinere Apparategrößen und verminderter Energiebedarf im Vergleich zu Batch-Anlagen mit vergleichbarer Kapazität zu Buche. Des Weiteren ermöglicht die stationäre Fahrweise auch die Vereinfachung der nachfolgenden Prozessschritte.
Im kontinuierlichen Betrieb kann die Übersättigung auch ökonomisch durch Verdampfen, bei Bedarf unterstützt durch Anlegen von Vakuum, erfolgen. Hauptsächlich kommen Forced Circulation und Leitrohrapparate („Draft Tube Baffled“ Kristaller DTBs) zum Einsatz. Ist das Produkt temperaturempfindlich oder eine Kühlungskristallisation besser geeignet, ist eine Kaskade von gerührten Behältern eine gute Alternative. Das Partikelwachstum kann durch die Verweilzeit in den einzelnen Behältern und die jeweilige Temperatur gesteuert werden.
Leitrohrapparate in der Kristallisation
Ein Sonderfall bei gerührten Kristallisationen stellen die kontinuierlich betriebenen Leitrohrapparate (DTB) dar. Das Rührorgan befindet sich innerhalb eines Leitrohres, das für eine stark gerichtete, axiale Strömung mit möglichst wenig Verlusten sorgen soll.
Gerade für Produkte, die in großen Jahrestonnagen hergestellt werden, ist ein Leitrohrapparat eine effiziente Lösung. Pottasche, ein Düngemittel, ist eine klassische Anwendung, aber auch Polyethylentherephthalat (PET), der Hauptbestandteil der meisten Getränkeflaschen, wird in einem DTB hergestellt. Neben der hohen Umwälzmenge sind gleichbleibende Produktqualität und ein klassierender Produktabzug der Feststoffpartikel in Zielgröße Vorteile dieser Apparate. Zu kleine Partikel werden aufgrund der geringeren Sedimentationstendenz einfach weiter zirkuliert, bis sie groß genug sind und über den Bodenablass abgezogen werden. Der Ekato Torusjet ist ein 3-flügliges Rührorgan, das speziell für den Einsatz im Leitrohr optimiert wurde. Die großen Rührflügel in Verbindung mit der mittels CFD-Analyse verbesserten Strömungscharakteristik erhöhen die Effizienz, d. h. der Anteil der Energie, die in axiale Strömung umgesetzt wird, signifikant.
Weitere Anpassungen sind die druckverlustarme Ausführung des Leitrohrs und der strömungslenkenden Einbauten. Generell ist es ratsam sich nicht auf einzelne Gewerke zu reduzieren, sondern das gesamte System im Auge zu behalten. Im Vergleich zu weniger effizienten Systemen macht sich der bis zu 20 % reduzierte Leistungsbedarf bei gleicher Umwälzrate bemerkbar, was sich in geringeren Anschaffungs- und Betriebskosten auswirkt. Als Nebeneffekt werden die Kristalle schonender zirkuliert, da es aufgrund des geringeren Leistungseintrages zu weniger Produktbelastung kommt. Die Überprüfung der mechanischen Lasten und Eigenschwingungen des Apparates in der Designphase mittels Finiter Elemente Analyse (FEA) respektive Modal Analyse sichert auch bei hohen Belastungen langfristig einen störungsarmen Betrieb.
Und was bringt die Zukunft?
In den vergangenen Jahren hat sich der Bedarf an effizienten Rührsystemen deutlich erhöht. Die Reduzierung des Energiebedarfs liegt dabei genauso im Fokus wie eine Optimierung der Prozess- und Produktparameter. Konkret für die Kristallisation stehen Ausbeute, Reinheit und Partikelgrößenverteilung im Mittelpunkt. Eine gesamthafte Betrachtung der Prozesskette wird unabdingbar, um alle Potentiale ausschöpfen zu können. Um den Anwender über das Rührwerk hinaus beraten zu können, arbeitet Ekato mit Partnern aus vielen Bereichen, so z. B. der fest-flüssig Trennung zusammen. Auch wird das Wissen der Schopfheimer Spezialisten durch Teilnahme an Fachkongressen und durch die Zusammenarbeit mit Kunden ständig erweitert. Die erstmalig im großen Stil eingesetzte CFD Unterstützung bei der Entwicklung eines strömungsoptimierten Rührflügelprofils hat alle Erwartungen übertroffen und die Testarbeit im Labor stark verkürzt. Sie wird deshalb zukünftig ein fester Bestandteil bei Neuentwicklungen sein. Auch neue Fertigungsmethoden wie Additive Manufacturing werden aufmerksam beobachtet, möglicherweise ergeben sich lang erträumte Freiheiten im Design, die bisher durch gängige Herstellungsverfahren limitiert waren.
Referenzen
Crystallization: Basic Concepts and Industrial Applications, 20.02.2013, Wolfgang Beckmann (Ed.)
Ekato Holding GmbH 2012. Ekato . The Book, ISBN 978-3-00-037510-1. Emmendingen: Druckerei Hofmann.