Druckluft, aber richtig günstig
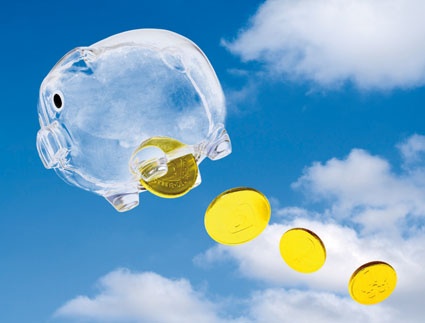
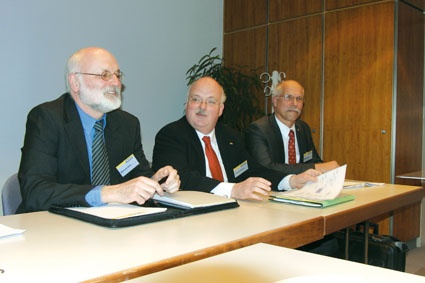
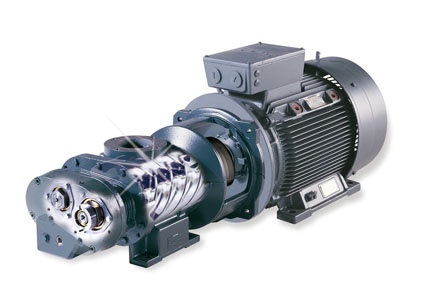
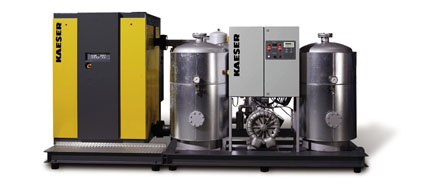
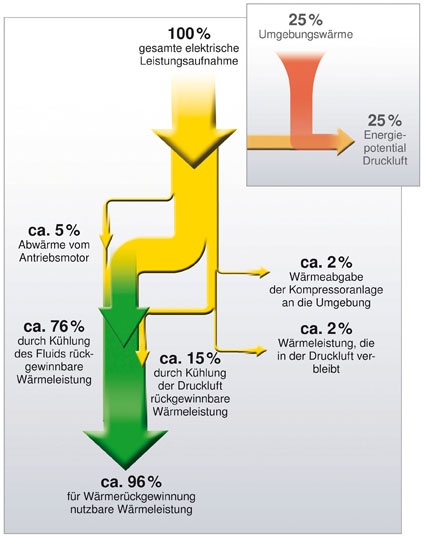
Durch systematisches Nutzen der Optimierungsmöglichkeiten, die beim Kaeser Energiesparkongress in Coburg Ende Oktober mehr als 200 Teilnehmern vorgestellt wurden, könnten die Betreiber von Druckluftsystemen in Europa wenigstens 25 Mrd. kWh pro Jahr einsparen. Würden nur die Hälfte aller Betreiber in Europa ihre Kompressoren mit einem System zur Wärmerückgewinnung ausstatten, so ließen sich jährlich weitere 32 Mrd. kWh einsparen. Dieser Beitrag gibt einen Überblick über die verschiedenen möglichen Maßnahmen.
Bereits heute bietet die Technik den Druckluftanwendern vielfältige Möglichkeiten, erheblich weniger Energie zu verbrauchen und auch weniger CO2 zu emittieren als bisher. Dass der Energieverbrauch den Löwenanteil der Druckluftkosten verursacht, war bereits Anfang der 70er Jahre, um die Zeit der ersten Ölkrise, ein Thema in der Druckluftbranche. Damals begann sich der Schraubenkompressor als Standardtechnik für industrielle Drucklufterzeugung durchzusetzen. Der Hersteller Kaeser Kompressoren hatte diesen Trend frühzeitig erkannt und nicht nur Schraubenkompressoren in sein Produktionsprogramm aufgenommen, sondern auch ein eigenes, energiesparendes Schraubenläuferprofil, das Sigma Profil, entwickelt. Mehr Druckluft mit weniger Energie, war schon damals der Slogan.
Doch in den Vordergrund rückte das Thema Energieeffizienz erst Ende der 90er Jahre, als das Kyoto-Protokoll die Industriestaaten zur Verringerung der Treibhausgas-Emissionen verpflichtete. Etwa zeitgleich legte die EU das Programm „Save II" auf. Eine in deren Rahmen erstellte Studie regte die Kampagne Druckluft effizient an, eine in den Jahren 2000-2004 durchgeführte Gemeinschaftsaktion von VDMA, Fraunhofer ISI, der Deutschen Energieagentur (Dena) und Unternehmen der Druckluftbranche.
Über 30 Prozent Einsparpotential
Für die in Europa installierten Druckluftsysteme hatte die Studie ein durchschnittliches Energie-Einsparpotential von knapp 33 % ermittelt. Die im Zuge einer Messkampagne durchgeführten Druckluft-Audits ergaben je nach Situation für die Druckluftversorgung in den untersuchten Betrieben Einsparpotentiale zwischen 18 und 70 %. Heute ist festzustellen, dass trotz mancher Verbesserungen die Druckluftsysteme in nicht wenigen Betrieben noch immer mehr dem Stand der 70er Jahre ähneln als dem einer zeitgemäßen energieeffizienten Versorgung.
Erweiterte Möglichkeiten der Effizienzsteigerung
Mit dem Energiespar-Kongress griff Kaeser Kompressoren nicht allein das Thema Energieeffizienz in der Druckluftversorgung erneut auf. Vielmehr machten die Vorträge auf neue technische Möglichkeiten aufmerksam und demonstrierten, wie diese sich zur weiteren Steigerung der Energieeffizienz des Gesamtsystems Druckluft nutzen lassen.
Elektrische Antriebe mit erhöhtem Wirkungsgrad
In den letzten Jahren ist es gelungen, Elektromotoren mit noch höheren Wirkungsgraden zu entwickeln als bisher. Um die verschiedenen Energieeffizienzstandards für Asynchronmotoren weltweit zu vereinheitlichen, hat die International Electrotechnical Commission (IEC) die internationale Norm IEC 60034-30 geschaffen. Darin sind die Wirkungsgradklassen IE1 bis IE3 festgelegt. IE3 ist die höchste Klasse. Für Antriebe mit Leistungen von 7,5 - 375 kW werden Motoren, die dieser Premium-Efficiency-Klasse entsprechen, ab 1. Januar 2015 Pflicht. Der Hersteller Kaeser beginnt bereits ab dem Jahr 2010 damit, IE3-Motoren in neue Schraubenkompressoren einzubauen. Nach und nach wird dann auch das übrige Modellprogramm entsprechend ausgestattet werden.
Energiesparende Kompressoren
Moderne Kompressoren sind Paradebeispiele für hoch entwickelte mechatronische Systeme. Ihre Effizienz wird also nicht nur von einem möglichst optimalen Zusammenspiel mechanischer und thermodynamischer, sondern auch elektrischer und elektronischer Komponenten bestimmt. Eine wichtige Funktion hat die Kraftübertragung. So kommen moderne 1:1-Antriebe, bei denen Antriebsmotor und Kompressorblock mit gleicher Drehzahl laufen, ohne die Übertragungsverluste eines Getriebes oder Riemenantriebs aus. Aber auch die Energieausbeute des Kompressorblocks selbst kann durch weiteres Optimieren des Schraubenläuferprofils, der Nebenaggregate für die Kühlung und durch das Minimieren interner Druckverluste noch erhöht werden.
Flexible kompressorinterne Steuerung
Ein weiterer wichtiger Effizienzbaustein ist die interne Steuerung des Kompressors. Während früher hierfür oft nur eine Steuerungsvariante eingesetzt wurde, ermöglichen es moderne Systeme auf Industrie-PC-Basis, mit bis zu fünf programmierten Varianten zu arbeiten und so die Förderleistung des Kompressors genau dem Druckluftverbrauch anzupassen. Die von Kaeser neu entwickelte Steuerung Sigma Control 2 bietet darüber hinaus weitere Vorteile: Variable Schnittstellen und erstmals auch steckbare Kommunikationsmodule erhöhen die Flexibilität beim Anbinden an maschinenübergreifende Druckluft-Managementsysteme, an Computernetzwerke und/oder an Ferndiagnose- und Fernüberwachungssysteme wie den Teleservice. Ein großes Display vereinfacht die Kommunikation mit der Anlage am Einsatzort. Zudem ermöglicht ein modernes RFID-Lesegerät eine Standardisierung des Service sowie eine professionelle Sicherung und eine deutliche Erhöhung der Servicequalität.
Hohe Servicequalität
Diese Steuerungen bieten zudem durch Betriebsüberwachung der Kompressoren wie auch der Druckluftfilter eine gute Basis für vorausschauende, bedarfsorientierte Wartung. Letztere muss Bestandteil eines umfassenden Servicekonzepts sein, dessen Ziele höchstmögliche Betriebssicherheit und Verfügbarkeit sowie optimierte Energie- und Wartungskosten sind. Der Service darf sich natürlich nicht nur auf die Kompressoren und weitere Komponenten beschränken, sondern muss sich auf das Druckluftsystem als Ganzes erstrecken. Die Frage, welchen Einfluss die Servicequalität auf die Effizienz des Druckluftsystems hat, war ebenfalls Gegenstand eines Referats.
Energieeffiziente Drucklufttrocknung
Auch die Druckluftaufbereitung hat einen nicht zu unterschätzenden Einfluss auf die Energieeffizienz der Druckluftversorgung. Dies trifft vor allem auf die Trocknung zu. Bei dem wirtschaftlichsten, am weitesten verbreiteten Verfahren, der Kältetrocknung (für Drucktaupunkte bis + 3 °C), hat es in den letzten Jahren erhebliche Fortschritte gegeben. Hier haben Kältetrockner mit energiesparenden Aussetzregelungen und optimierter Anpassungsfähigkeit an den tatsächlichen Druckluftverbrauch sowie der Einsatz neuer Kältemittel zu deutlichen Energieeinsparungen geführt. Doch auch für Druckluft mit wesentlich höherem Trockenheitsgrad (Drucktaupunkte bis - 40 °C) gibt es inzwischen mit der Kälte-Adsorptionstrocknung ein energiesparendes Kombiverfahren. Es kann in zahlreichen Fällen die erheblich energieaufwendigere reine Adsorptionstrocknung ersetzen. Unter gewissen Umständen besteht auch die Möglichkeit, Kompressorabwärme zur Regeneration des Adsorptionsmittels einzusetzen.
Analyse des tatsächlichen Druckluftbedarfs
Höchstmögliche Energieeffizienz jeder einzelnen Druckluft-Systemkomponente ist zwar eine notwendige, aber noch keineswegs hinreichende Voraussetzung für die optimierte Energieeffizienz des Gesamtsystems „Druckluft". Es kommt vielmehr darauf an, jede Komponente auch optimal in das System zu integrieren. Computergestützte Bedarfsanalysen wie etwa die „Analyse der Druckluft-Auslastung" (ADA) bieten dabei wertvolle Unterstützung: Mit ihrer Hilfe lässt sich ermitteln, wie der Druckluftbedarf im Zeitverlauf aussieht, wie wirtschaftlich eine Druckluftstation wirklich arbeitet und inwiefern ihre Verfügbarkeit und Effizienz noch erhöht werden kann. Eine spezielle Planungssoftware wie etwa das „Kaeser-Energie-Spar-System" (KESS) kann zudem verschiedene Systemvarianten simulieren, miteinander vergleichen und Einsparpotentiale ermitteln.
Optimiertes Druckluft-Management
Auch im Bereich Steuerung und Regelung von Druckluftstationen steckt ein hohes Energieeffizienzpotential, das es zu nutzen gilt. Moderne maschinenübergreifende Steuerungen und Managementsysteme wie der „Sigma Air Manager" (SAM) sind in der Lage, einen Großteil dieses Potentials auszuschöpfen. Dank einer neuartigen adaptiven 3-D-Regelung kann die jüngste SAM-Version das besonders gut. Diese von Kaeser zum Patent angemeldete Regelung berücksichtigt die drei für die energieeffiziente Steuerung von Kompressoren entscheidenden „Dimensionen": 1. die mit Start und Stillsetzung der Kompressoren verbundenen Schaltverluste, 2. den zusätzlichen Energieaufwand für Druckerhöhungen über den Bedarfsdruck und 3. die Regelverluste in Form von Leerlauf- und FU-(Regel-)Verlusten. SAM analysiert unter Berücksichtigung dieser drei Dimensionen ständig, mit welcher Steuerstrategie sich der erforderliche Energieeinsatz minimieren lässt, und steuert die Kompressoren entsprechend. Darüber hinaus ermöglicht er umfassende Kostentransparenz und optimierte vorbeugende Wartung des Druckluftsystems.
Nutzung der Kompressorabwärme
Ein zusätzliches, ganz erhebliches Energieeinsparpotential erschließt sich über Wärmerückgewinnung: Bis zu 96 % der einem Kompressor zugeführten Energie lassen sich als Abwärme ein zweites Mal nutzen. Wer diese Energiemenge in sein betriebliches Versorgungskonzept integriert, kann zusätzlich erhebliche Kosten einsparen und die Umwelt durch verringerte CO2-Emissionen entlasten. Die Einsatzmöglichkeiten sind vielfältig - sie reichen von der Raumheizung über die Versorgung von Warmluftschleusen, Brauch- und Prozesswassererwärmung bis zur Vorerwärmung von Brennerluft.
Minimieren von Leckagen
Die von Leckagen im Druckluft-Leitungsnetz hervorgerufenen Energieverluste sind durchaus mit einem kräftigen Aderlass vergleichbar: Üblicherweise liegen die Leckageraten bei 10 - 25 %. Leckverluste können im Verlauf eines Jahres zu beträchtlichem kWh-Mehrverbrauch und entsprechenden Mehrkosten führen. Mithilfe moderner Suchgeräte lassen sich Leckagen heute gut orten und anschließend beheben. So ist es möglich, die Verluste zu minimieren - ganz zu vermeiden werden sie nie sein.
... und viele kleine andere Mängel
Darüber hinaus gibt es weitere Ursachen von Energieverlusten und großen Druckdifferenzen im Leitungsnetz. Dazu zählen etwa Verunreinigungen in den Rohren, zu enge Rohrquerschnitte und strömungstechnisch ungünstige Verlegung der Rohrleitungen. Auch diese Mängel sollten beseitigt bzw. vermieden werden.