Die Entwicklung der Hochofentechnologie
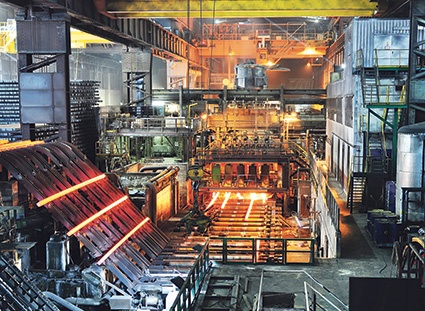
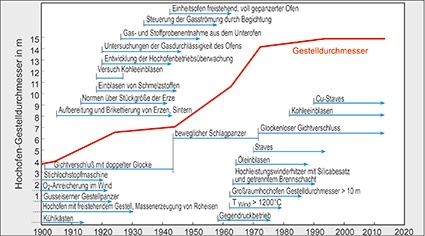
Der Hochofen ist ein kontinuierlich arbeitender Schachtofen, bei dem durch Reduktionsgas der in den Eisenerzen (Sinter, Pellets, Stückerze) enthaltene Sauerstoff abgebaut wird. Das Reduktionsgas CO wird durch Reaktion von Kokskohlenstoff mit Windsauerstoff im Hochofen erzeugt. Die weiteren Begleitelemente der Einsatzstoffe werden im Wesentlichen in der Schlacke abgetrennt. Als Produkt wird flüssiges Roheisen mit einer Temperatur von 1.500°C erzeugt, welches im Oxygenstahlkonverter zu Rohstahl gefrischt wird.
Hochöfen arbeiten nach dem Gegenstromprinzip. Den am Oberofen, der Gicht, chargierten festen Einsatzstoffen Eisenerze und Koks (Möller) strömt das im unteren Teil des Ofens gebildete Reduktionsgas entgegen. Flüssiges Roheisen und flüssige Schlacke werden im Unterofen abgestochen, das Prozessgas (Gichtgas) wird über die Gicht abgezogen und nach Reinigung für Beheizungszwecke oder zur Stromerzeugung genutzt.
Abbildung 1 stellt die Vergrößerung des Gestelldurchmessers der Hochöfen und damit der Ofengröße sowie die verfahrens- und anlagentechnischen Erneuerungen in den jeweiligen Zeiträumen der letzten 110 Jahre dar und dient somit als roter Faden in der Beschreibung der Entwicklung von Hochöfen.
Steigerung von Größe und Leistung
Während um 1900 bei Gestelldurchmessern von 3,0 m Tageserzeugungen von 400 t Roheisen möglich waren, werden heute in dem größten Hochofen Deutschlands, dem Hochofen Schwelgern 2 der ThyssenKrupp Steel Europe, mit einem Gestelldurchmesser von 14,9 m rd. 12.000 t Roheisen täglich erzeugt.
Auch den Hochöfnern vor 110 Jahren war schon klar, dass zur Senkung des Koksverbrauches und damit zur Verbesserung der Wirtschaftlichkeit des Verfahrens z.B. die Optimierung der Schüttgutverteilung und das Einblasen von Koks-Ersatzreduktionsmitteln einen unmittelbaren Beitrag leisten können.
Es sollte noch fast 70 Jahre dauern, bis die Entwicklung der Werkstoffeigenschaften und Steuerungstechnik weit genug fortgeschritten war, den glockenlosen Gichtverschluss zur optimalen Schüttgutverteilung und das Einblasen von Kohlenstaub in die Betriebspraxis umzusetzen.
Die Hochofengröße erreichte um 1920 bereits 6,0 m Gestelldurchmesser. Unter den Zwängen des zweiten Weltkrieges wurde vom Hochofenausschuss des VDEh ein Einheitshochofen mit 6 m Gestelldurchmesser, 750 m3 Nutzvolumen und einer Tageserzeugung von 1000 t Roheisen vorgeschlagen. Erstmalig war hier die Ausführung eines geschweißten, den gesamten Ofen umfassenden Blechpanzers vorgesehen.
Von 1955 bis 1970 wurden die ersten Neubauten von Hochöfen mit Gestelldurchmessern von 9.0 bis 9,5 m durchgeführt sowie die Möllervorbereitungsanlagen erweitert und verbessert.
In die Folgezeit fallen die Steuerung der Schüttgutverteilung durch Einführung von verstellbaren Schlagpanzern, der Einsatz von Schweröl, die Steigerung der Windtemperatur durch Verbesserung der herkömmlichen Winderhitzer oder durch den Neubau der Winderhitzer mit außenstehendem Brennschacht, die Sauerstoffanreicherung des Windes und die Anwendung des Gegendrucks.
Die Weiterentwicklung der Ofengröße war in Deutschland dem Wagemut einzelner Hochöfner anvertraut, die allerdings auch für die Durchführung solcher Projekte nach Japan schauten. Dort wurde der Aufbau der damals jungen Stahlindustrie direkt mit dem Neubau sehr großer Hochofenanlagen durchgeführt.
In den frühen 70er Jahren nahm in Deutschland die Ofengröße auf bis zu 13,6 m Gestelldurchmesser bei einer Leistung von rd. 11.000 t/d zu. Die Windtemperaturen erreichten bis zu 1.300°C und die spezifische Öleinblasrate konnte auf 140 kg/t Roheisen erhöht werden.
Durch die Einführung des glockenlosen Gichtverschlusses mit Drehschurre, die von der Ofenperipherie bis in die Ofenmitte jedes Schüttungsprofil einstellen kann, wurden Schüttgutverteilung und Durchgasung deutlich verbessert mit entsprechender Auswirkung auf den spezifischen Reduktionsmittelverbrauch. Rechneranlagen ermöglichten die Datenerfassung und die Prozessoptimierung.
Im Jahre 1993 ist mit dem Neubau des Hochofens Schwelgern 2 von ThyssenKrupp Steel Europe der in Westeuropa größte Hochofen in Betrieb gegangen. Dieser Hochofen hat einen Gestelldurchmesser von 14,9 m, ein Nutzvolumen von 4769 m3 und erzeugt rd. 12.800 t Roheisen pro Tag.
Steigerung der Effizienz
Die Arbeiten der Hochofenbetreiber und Anlagenbauer führten nicht nur zu einer Leistungssteigerung der Hochöfen, sondern auch zu einer Absenkung des Koks- bzw. Reduktionsmittelverbrauches. Bis Mitte der 1960er Jahre ist Koks noch das einzige Reduktionsmittel der Hochöfen gewesen. In dieser Zeit war eine Absenkung des Koksverbrauches wegen der verhältnismäßig komfortablen Koksversorgung und günstiger Kokspreise nicht immer eine der vorrangigen Aufgabenstellungen der Hochofenbetreiber. Während Anfang des vorigen Jahrhunderts der Kokssatz spezifisch bei 1000 kg/t Roheisen und darüber lag, konnte er insbesondere nach 1945 deutlich verringert werden und liegt heute bei nur noch 330 kg bei einer Einblasrate von 170 kg/t Roheisen an Ersatzreduktionsmitteln, vorrangig Kohlenstaub. Dieser Rückgang ist auch im besonderen Maße dem Einsatz von hochwertigen Möllerstoffen zuzuschreiben.
Vor 200 Jahren betrug eine Hochofenreise, d.h. die Zeitdauer seines Betriebes zwischen zwei Neuzustellungen, ganze 8 Wochen. Vor 30 Jahren lag sie bei 6 bis 8 Jahren. Die heute geforderte hohe Betriebsbereitschaft von Großhochöfen und die hohen Kosten einer Zustellung verlangen Ofenreisen von 20 Jahren und mehr, und sie werden erreicht. Voraussetzung hierfür ist, neben entsprechender konstruktiver Ausbildung des Ofens, ein stabiler und kontinuierlicher Ofenbetrieb.
Handlungsbedarf für die künftige Entwicklung
Bei der Entwicklung der Hochofentechnologie im Verlauf der letzten 110 Jahre gab es immer wieder Stimmen, die das Ende des Hochofens als Basis der Stahlherstellung prophezeiten. Als Gründe wurden seine Abhängigkeit von hochwertigem Koks sowie der hohe Investitionsaufwand für den Hochofen selbst und seiner Vorstufen genannt. Die ausgereifte Verfahrenstechnik des Hochofens und seine ständigen Weiterentwicklungen sind jedoch Garanten für seine Dominanz bei den Verfahren der Eisenerzreduktion. Lediglich seine Abhängigkeit von Kohlenstoff basierten Reduktionsmitteln und die damit verbundenen CO2-Emissionen erfordern bei den derzeitigen politischen Diskussionen Handlungsbedarf für die Umsetzung technischer Lösungen.
Mehr zum Thema ...
... bietet die aktuelle Ausgabe der Ullmann's Encyclopedia unter dem Stichwort Iron, 2. Blast Furnace Process