TÜV Süd entwickelt dynamisches Risikomanagement
Bei TÜV Süd Industrie Service steht modernes Risikomanagement im Mittelpunkt. Mit der Entwicklung von iaHAZOP bietet TÜV Süd eine zeitgemäße Lösung zur Bewertung und Kontrolle von Risiken in verschiedenen Anlagen. Das Verfahren kombiniert traditionelles Wissen mit digitalen Innovationen, um die Sicherheit und Effizienz Ihrer Prozesse zu gewährleisten.
Autoren: Michael Pfeifer, Seniorexperte Adaptive Safety und Alexander Kurdas, Maschinensicherheitsingenieur, TÜV Süd Industrie Service, München
Der Industrie Service bedient sich eines Verfahrens, mit dem die Risikobewertung so dynamisch wird wie die Prozesse selbst
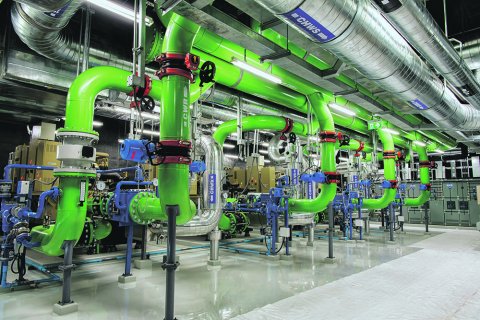
Für die Weiterentwicklung des bewährten Hazop-Verfahrens (Hazard and Operability) zum interaktiven, digitalen und teilautomatisierten interactive Hazop (iaHazop) gab es mehrere Gründe. Einer davon ist, dass eine Anlage nur produzieren darf, wenn eine gültige und passende Risikobewertung vorliegt. Mit der zunehmenden Modularisierung von Produktionseinheiten und dem schnellen Wechsel von Produkten, die in kleinen Losgrößen gefertigt werden, muss das Risikomanagement ebenfalls flexibel sein. Andernfalls drohen ungewollte Stillstände. Gleichzeitig wird es immer schwieriger, das vorhandene Wissen im Unternehmen zugänglich zu machen – und zu halten. Dies wird zusätzlich erschwert durch hohe Personalfluktuation und den Fachkräftemangel, was nicht zuletzt am demografischen Wandel liegt.
Viele Informationen sind isoliert voneinander und in Aktenordnern „versteckt“. Fehlen dann die Menschen, die über diese „Wissenssilos“ den Überblick haben, geht viel Erfahrung verloren. Dynamische Prozesse und ihre Sicherheitsbewertungen lassen sich ohnehin analog und auf Papier nur schwer abbilden. Die Folge sind Dokumentationen von „Worst-Case-Szenarien“, die aber keine alltagstaugliche Grundlage für das Risikomanagement darstellen – das dementsprechend träge und fehleranfällig wird.
Interactive Hazop – so funktioniert es
Mit iaHazop werden alle für das Risikomanagement relevanten Informationen digital festgehalten und gebündelt. Digitale Modelle bilden einzelne Komponenten bis hin zum gesamten Prozess ab. Dadurch ergeben sich vielfältige Nutzungsszenarien, z. B. Unterstützung für die Risikoanalyse während der Planungsphase oder die Auswertung im laufenden Betrieb. So stellt das Verfahren eine Basis für adaptives Risikomanagement dar. Sensoren liefern alle relevanten Daten zum Status der Komponenten. Mit dieser Lösung findet ein Abgleich der gemessenen Werte mit voreingestellten Grenz- oder Schwellenwerten statt. Die umfassende Vernetzung liefert Erkenntnisse über die Relation der Prozessparameter untereinander. Ergänzt wird das Verfahren durch die Nutzung eines digitalen Zwillings, der auch für Prognosen möglicher Zustände genutzt werden kann. Ein mögliches Überschreiten der Grenzwerte wird dank dieser Risikoberechnung frühzeitig erkannt, und der Betreiber kann entsprechend rechtzeitig mit Maßnahmen reagieren und das Eintreten sogar ganz verhindern.
Weiterlesen mit kostenfreier Registrierung
Registrieren Sie sich jetzt kostenfrei und Sie erhalten vollen Zugriff auf alle exklusiven Beiträge. Mit unserem Newsletter senden wir Ihnen Top-Meldungen aus der Chemie-, Pharmaindustrie. Außerdem erhalten Sie regelmässig Zugriff auf die aktuellen E-Paper und PDFs von CHEManager.
Anbieter
TÜV SÜD AGWestendstr. 199
80686 München
Meist gelesen
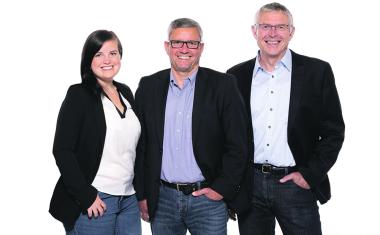
Waste2Resources&Energy
Das Viernheimer Start-up Curenergy wurde 2023 mit dem Ziel gegründet, den rein elektrisch beheizten Recyclingprozess der Hochtemperaturpyrolyse für ein 100%-Recycling zu industrialisieren.
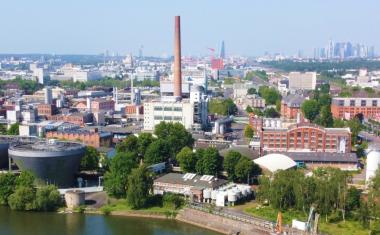
WeylChem Fine Chemicals: Globaler CDMO mit Produktionskapazitäten auf drei Kontinenten
Ein neuer Akteur betritt die Bühne der Feinchemie: WeylChem Fine Chemicals (WCFC), eine global aufgestellte Organisation für die kundenspezifische Entwicklung und Herstellung von Spezialchemikalien (CDMO).
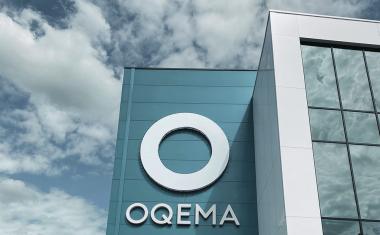
„Wir stellen uns für die Zukunft auf“
Zurück im Familienbesitz rüstet sich Oqema, um die sich bietenden Chancen in der Chemiedistribution zu ergreifen.
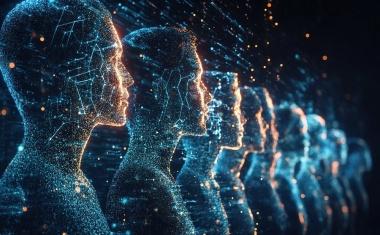
CHEMonitor 01-2025 – Künstliche Intelligenz und Demografie
Das aktuelle Trendbarometer CHEMonitor beleuchtet das Zusammenwirken des demografischen Wandels und den Einfluss der künstlichen Intelligenz (KI) auf die Chemie- und Pharmaindustrie.
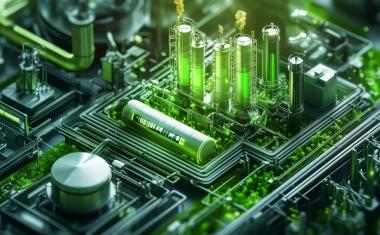
Die Zukunft der Chemieindustrie
Die Chemieindustrie in Deutschland und Europa steht vor erheblichen Problemen. Die hohen Energiekosten und die Nachfrageschwäche setzen viele Unternehmen unter Druck und belasten ihre Wettbewerbsfähigkeit.