Zu den Besten gehören!
Um im Wettbewerb wirtschaftlich zu produzieren, versuchen Anlagenbetreiber eine Top-Quartil-Performance zu erreichen, also im Branchenvergleich eine Betriebs- und Kapitalperformance zu erreichen, die im oberen Viertel liegt.
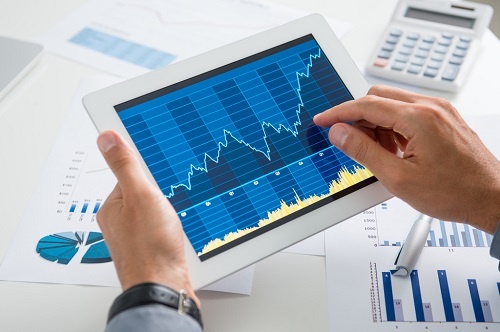
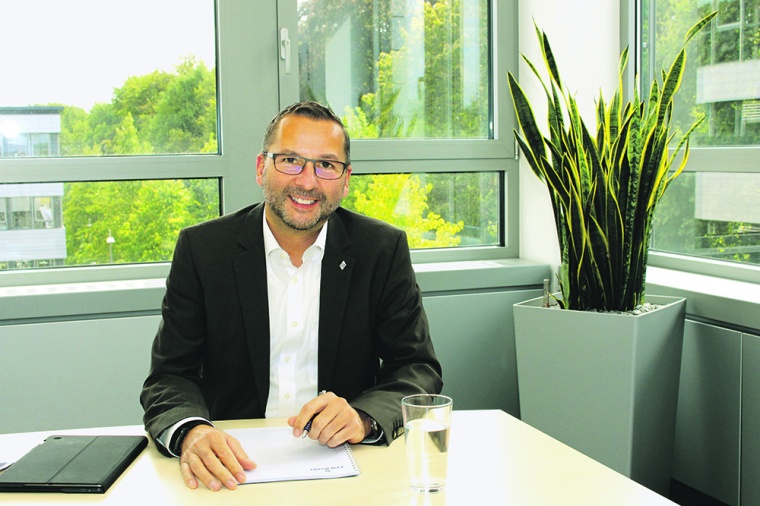
Wie man diese Performance erreichen kann, diskutierte CHEManager mit Andreas Fuchs, General Manager, Emerson Automation Solutions Deutschland. Das Gespräch führte Volker Oestreich.
CHEManager: Herr Fuchs, Emerson ist seit über 50 Jahren in Deutschland tätig und hat in den letzten zwei Jahren mehrere bedeutende Akquisitionen und Allianzen getätigt. Was bedeutet das für Ihre Kunden?
Andreas Fuchs: Die Akquisitionen, die wir getätigt haben, erlauben es uns, ein noch breiteres Spektrum an Automatisierungslösungen, Hardware, Software, Services und Beratungsleistungen anzubieten. Zum Beispiel hat der Kauf des Valves & Controls Bereichs von Pentair ein umfassendes Ventilgeschäft geschaffen mit einem globalen Netzwerk von mehr als 200 Service-Centern.
Mit der Simulationssoftware von Mynah und deren Erfahrung in der Bedienerschulung können wir unseren Kunden bessere Prozesssimulations- und Schulungslösungen anbieten. Diese Akquisition wird durch unsere Allianz mit AspenTech ergänzt und wir sind in der Lage, kostengünstige Digital-Twin-Lösungen zu schaffen, die unsere Kunden von der Projektierung über die Bedienerschulung bis hin zur Produktionsoptimierung nutzen können. Durch das Hinzufügen der ProSys können wir außerdem innovative Regelungslösungen und effiziente Werkzeuge zur Bedienerunterstützung bereitstellen, um den Anlagenbetrieb noch effektiver und sicherer zu machen.
Zum 1. Februar 2019 konnte die Akquisition von General Electric‘s Geschäftsbereich Intelligent Platforms abgeschlossen werden, womit wir unser Potenzial als Anbieter von kompletten Automatisierungslösungen von der Prozess- bis zur Fertigungsautomatisierung weiter ausgebaut haben.
Sie haben Ihre Initiative „Project Certainty“, mit der sie die Projekt- und Planungskosten bei ihren Kunden reduzieren wollen, zu „Operational Certainty“ erweitert. Was genau verbirgt sich dahinter?
A. Fuchs: Die „Project Certainty“ Initiative bietet Lösungen, um die Risiken bei der Projektabwicklung von Planung bis Inbetriebnahme zu reduzieren. Damit sind aber noch nicht alle Probleme gelöst und Möglichkeiten ausgeschöpft. Die Betriebsphase einer Anlage beträgt Jahrzehnte und ist um ein Vielfaches länger als die Projektphase. Pro Jahr verliert die Industrie über 1 Billion US-Dollar aufgrund von suboptimaler Performance in Bezug auf Sicherheit, Zuverlässigkeit, Durchsatz und Energieverbrauch. Um dies zu vermeiden, versuchen Anlagenbetreiber eine Top-Quartil-Performance zu erreichen, dies bedeutet als Unternehmen im Branchenvergleich eine Betriebs- und Kapitalperformance zu erreichen, die im oberen Viertel liegt. Möglich ist dies, indem die Verfügbarkeit der Anlagen maximiert wird, das Auftreten aufzeichnungspflichtiger Sicherheitsvorfälle beseitigt wird, der Energieverbrauch gesenkt und die Effizienz und Qualität der Produktion gesteigert wird. Unsere „Operational Certainty“ Initiative hilft Kunden, die Ursachen für suboptimale Leistung zu erkennen, Maßnahmen zu priorisieren, die eine größtmögliche Verbesserung bewirken und einen skalierbaren Plan mit weiteren Optimierungen zu definieren.
Mit unserem „Operational Certainty Consulting“ helfen wir unseren Kunden, dieses Potenzial zu erkennen, zu quantifizieren, einen Maßnahmenkatalog zu erstellen, zu priorisieren und einen umsetzbaren Plan zu entwerfen.
In Zusammenarbeit mit unseren „Operational-Certainty“-Beratern wird eine Strategie entwickelt, die auf die spezifischen Anforderungen des Kunden abgestimmt ist. Die Umsetzung kann dann in mehreren Teilprojekten erfolgen, in denen die Emerson Produkte und Lösungen implementiert werden bzw. Dienstleistungen zur Anwendung kommen, was sich letztendlich dauerhaft positiv auf den Betrieb und die Wartung der Anlage auswirken wird.
Mit einer anderen Initiative, nämlich Integrated Operations (iOps), wollen Sie organisatorische und räumlich übergreifende Funktionalitäten unterstützen.
Was genau ist diese Initiative und wie wird sie vom Markt angenommen?
A. Fuchs: Aufgrund des zunehmenden Fachkräftemangels und der begrenzten Verfügbarkeit von erfahrenen Spezialisten setzt die Industrie mehr und mehr auf „Integrated Operations“ (iOps). Mit den mittlerweile vorhandenen Technologien ist es möglich, die richtigen Experten mit aktuellen und relevanten Informationen zu versorgen, unabhängig davon, wo sie sich befinden. Sie können somit adhoc ein lokales Team bei der Problemlösung vorort unterstützen und mit ihnen über Audio und Video kommunizieren, was die Reaktionszeit extrem beschleunigt. Dazu werden Prozess- und Anlagendaten lokal gesammelt, ausgewertet und Probleme werden frühzeitig erkannt, bevor sich diese auf den Anlagenbetrieb auswirken können. Die zuständigen Mitarbeiter werden alarmiert, informiert und können reagieren. Möglich ist dies durch unser Plantweb Digital Ecosystem, welches Daten, Applikationen und Organisationen miteinander verbindet. Es entspricht der NAMUR Open Architecture (NOA) für die Überwachung und Optimierung des Anlagenbetriebs, ist leitsystemunabhängig, skalierbar und kann implementiert werden, ohne den Anlagenbetrieb zu stören.
Eine zentralisierte, auf aktuellen Daten basierte Überwachung führt zu optimierten Wartungsplänen und -budgets. Die Betriebsleitung kann lokal mit Wartungs- und Produktionspersonal und mit Experten von anderen Standorten zusammenarbeiten und die Produktionsplanung und -optimierung kann an zentralen Standorten im Unternehmen erfolgen.
„Mit unseren Technologien ist es möglich, die richtigen Experten mit aktuellen Informationen zu versorgen, unabhängig davon, wo sie sich befinden.“
Wir sehen auch, dass die Nachfrage nach entsprechenden Lösungen enorm gestiegen ist. Es gibt kaum eine Firma, die nicht an der Digitalisierung arbeitet, an Industrie 4.0 Lösungen interessiert ist und eine mögliche Fernüberwachung oder Kollaboration aktuell in Betracht zieht oder gar erprobt. Wir hatten jedenfalls kein Problem für unseren Plantweb Optics Piloten, eine neue Version mit erweiterter Funktionalität, für den Feldtest Interessenten zu finden. Und wir können erfreulicherweise auch sagen, dass das Feedback von Kunden, die eine iOps Lösung betreiben, nach wenigen Monaten schon extrem positiv ist, und dass diese dann schon über Erweiterungen nachdenken.
Beide Initiativen, „Operational Certainty“ oder „iOps“, sind verbunden mit der Digitalisierung aller Abläufe – also Bausteine auf dem Weg zu IoT, dem Internet of Things, oder Industrie 4.0?
A. Fuchs: Die Digitalisierung erschließt uns neue Möglichkeiten und dazu gehören „Operational Certainty“ und „iOps“. Neue Technologien, höhere Speicherkapazität und Rechenleistung, höhere Übertragungsraten, sichere Übertragungswege und neue Sensorik ermöglichen heute viele Dinge, die man in bisherigen Automatisierungs- und Überwachungsstrategien nicht realisieren konnte. Diese helfen den Anlagenbetrieb effizienter, sicherer und verfügbarer zu machen. Unternehmen, die Industrie 4.0 Lösungen einsetzen, die Daten sammeln und analysieren und diese ganz gezielt an die unterschiedlichsten Empfänger verteilen und die die Zusammenarbeit über weite Entfernungen hinweg ermöglichen, können schneller und besser auf Ereignisse reagieren und verschaffen sich dadurch einen enormen wirtschaftlichen Vorteil. Da gibt es noch einiges an Potenzial, was erschlossen werden kann.
„Unternehmen, die Industrie 4.0 Lösungen einsetzen, können schneller und besser auf Ereignisse reagieren.“
Die Digitalisierungsstrategie von Emerson besteht darin, unseren Kunden die breiteste und tiefste Industrial-Internet-of-Things (IIoT) Plattform anbieten zu können. Unser Plantweb System, die dazugehörenden Lösungen und Dienstleistungen und Integrated Operations liefern messbare Ergebnisverbesserungen. Dieses Potenzial kann durch unsere Berater bereits im Vorfeld ermittelt und kalkuliert werden und erlaubt es die Notwendigkeit der erforderlichen Problemlösungen zu begründen und das wichtige Return-of-Investment zu bestimmen.
Mehr Information bedeutet irgendwie auch zunehmende Komplexität – genau das wollen aber die produzierenden Betriebe in der Prozesstechnik eigentlich nicht. Wie können Sie da helfen?
A. Fuchs: Unsere Berater für „Operational Certainty“ helfen zunächst, die Bereiche zu identifizieren, in denen Verbesserungen möglich sind. Die Daten sind dann Mittel zum Zweck und es werden nur die Daten gesammelt und verarbeitet, die für eine Überwachung oder Optimierung notwendig sind. Der Anwender oder Kunde sollte mit diesen Rohdaten nicht in Berührung kommen. Für ihn gibt es eindeutige graphische Anzeigen, die zum Beispiel auf dem Smart-Phone oder Tablet angezeigt werden können und klar aufbereitete Informationen und konkrete Alarme liefern.
Bei Bedarf kann auch eine kontinuierliche Überwachung durch Emerson Spezialisten aus der Ferne erfolgen. Wir bezeichnen dies als „Connected Services“. Die Zustandsüberwachung von Equipment kann dabei in einem As-a-Service Vertrag geregelt werden und der Kunde wird regelmäßig über die gemachten Beobachtungen und Maßnahmen informiert, sowie unmittelbar beim Auftreten von Störungen mit konkreten Handlungsanweisungen alarmiert. Der Vorteil ist, dass lokal keine Experten vorgehalten werden müssen, die sich um alle Details kümmern und die Fülle an Daten oder Lösungen beherrschen. Dies reduziert die Komplexität lokal um ein Wesentliches und man kann sich dort auf seine Hauptaufgabe, den Anlagenbetrieb, konzentrieren.
Welche Lösungen bieten Sie genau an, um von „Big Data“ zu „Smart Data“ zu gelangen?
A. Fuchs: Konkrete Beispiel sind die Plantweb Insight Anwendungen für die Überwachung von Wärmetauscher, Pumpen, Kühltürme, Kondensatableitern und anderen Applikationen. Die Anzahl verfügbarer Applikationen steigt ständig. Mit der Pumpen App werden Rohdaten überwacht. Dies können verschieden Drücke und Temperaturen sein, Drehzahl, Schwingungen und der Energieverbrauch. Die App zeigt dann den Gesundheitszustand des Aggregates an und kann konkret Lager- oder Gleitringdichtungsfehler erkennen und bei Verstopfung, Undichtigkeit und Kavitation warnen. Die Interpretation der Daten erfolgt durch die App. Man kann hier schon fast von künstlicher Intelligenz sprechen, da einiges an Expertenwissen in die Entwicklung der App und der darin enthaltenen Analysen geflossen ist. Ein Vorteil ist auch, dass die App rund um die Uhr ihre Überwachungsaufgabe erfüllt und selbst ein kurzfristiger Ausfall keinen negativen Einfluss auf den Anlagenbetrieb hat.
Weiter Beispiele ist der Plantweb Performance Advisor für die Überwachung von Kompressoren, Turbinen, Feuerungsanlagen und Dampfkesseln. Die Leistung dieses kritischen Prozess-Equipment kann sich im Laufe der Zeit verschlechtern. Dies führt zu Effizienzverlust, erhöhtem Energieverbrauch und reduziertem Durchsatz. Wichtig ist es hier frühzeitig Abweichungen von der ursprünglichen Auslegung des Equipments zu erkennen, was entscheidend für die Rentabilität der Anlage ist. Der Plantweb Performance Advisor ermöglicht diese Überwachung und nutzt dazu thermodynamische Modelle erster Ordnung, die kontinuierlich mit den gemessenen Werten verglichen werden. Der Energieverbrauch, die Performance und der Gesundheitszustand des Equipments werden dabei in leicht verständlichen Grafiken den Auslegungsdaten gegenübergestellt, so dass Abweichungen einfach zu erkennen sind.
„Digital-Twin-Lösungen helfen den Anwendern von der Projektierung über die Bedienerschulung bis hin zur Produktionsoptimierung.“
Mit Plantweb Optics kommen ausgewählte Anlagen- und Equipment-Daten in einfacher und übersichtlicher Form zum Nutzer auf das Smart-Phone. Die Weiterleitung von Warnmeldungen, Informationen, Graphen, Bildern und Notizen erfolgt dabei rollenbasiert und vereinfacht komplexe Workflows und die Integration in Computergesteuerte Instandhaltungsmanagementsysteme. Die Daten können dabei aus verschiedenen Quellen zur Verfügung gestellt werden. Eine OPC UA Schnittstelle ist ebenso vorhanden. Eine Demo der Plantweb Optics App ist über den Appel App Store oder Google Play für Interessenten verfügbar.
Wie genau können Informationen, die an einem Produktionsstandort gewonnen werden und letztendlich irgendwo im Prozessleitsystem versteckt sind, auf andere Produktionsstätten des Unternehmens übertragen werden - selbst wenn dort ein anderes Prozessleitsystem eingesetzt wird?
A. Fuchs: DeltaV Mobile bietet sicheren Zugriff auf Echtzeit- und historische Prozessdaten von DeltaV-Systemen und anderen Datenquellen, einschließlich Systemen von Drittanbietern. Es verbindet Smartphone-Technologie mit Prozesssteuerungsdaten, um Betriebsinformationen rund um die Uhr weltweit verfügbar zu machen. Im Wesentlichen werden dadurch die Grenzen des Kontrollraums aufgehoben und digitale Mitarbeiter - Manager, Ingenieure, Bediener und Fachexperten - können den Betrieb überwachen und kritische Betriebsdaten anzeigen, wann, wie und wo sie wollen, ohne manuelle erstellte Berichte abzuwarten oder an einen Computer gebunden zu sein. DeltaV Mobile integriert Daten aus OPC-Datenquellen und macht Daten von verschiedenen Steuerungssystemen, einschließlich DeltaV, auf mobilen Geräten überall verfügbar.
Weltweit vernetzte Prozessindustrie, IoT, Industrie 4.0 oder Cloud Computing: Neue Systeme bieten neue Möglichkeiten, aber auch neue Risiken: Was ist mit Cyber Security? Wie stellt Emerson die Prozesssicherheit sicher?
A. Fuchs: Cyber Security, die Sicherheit der Informationen, der Schutz von Computersystemen, deren störungsfreier Betrieb ohne Beeinträchtigung der von ihnen bereitgestellten Dienste ist essentiell für die Prozessautomatisierung, den sicheren Anlagenbetrieb, die Anlagenüberwachung und Optimierung. Umso wichtiger wird dies, wenn man Vorteile aus der Digitalisierung ziehen will. Sowohl unser DeltaV System als auch Plantweb Digital Ecosystem haben verschiedene Schutzmechanismen. Zum Standard sollten organisatorische und systemische Maßnahmen, wie zum Beispiel Zutrittsbeschränkung, Passwortschutz, Firewalls, Virenscanner etc. gehören.
Plantweb beinhaltet eine sichere erste Meile „Secure First Mile“, also die sichere Verbindung zur Übertragung von Anlagendaten an die entsprechenden Anwendungen, Services oder mobilen Nutzer. Dies kann über verschiedene Wege erreicht werden: durch eine Reihe von Sicherheits-Services sowie robuste, sichere und flexible Server, Gateways und Datendioden. Wobei die bestehenden Systeme und Datensammler von Emerson genutzt werden können, zu denen verteilte Steuerungssysteme wie etwa DeltaV, Remote Terminal Units (RTU) und Asset Management Systeme (AMS) gehören. Die Secure First Mile Architektur ermöglicht einen sicheren, direkten Datenexport aus diesen Systemen in das Internet und ermöglichen dem Anlagenbetreiber eine strikte Kontrolle über die exportierten Daten.