Vestanat PP für den Automobilbau
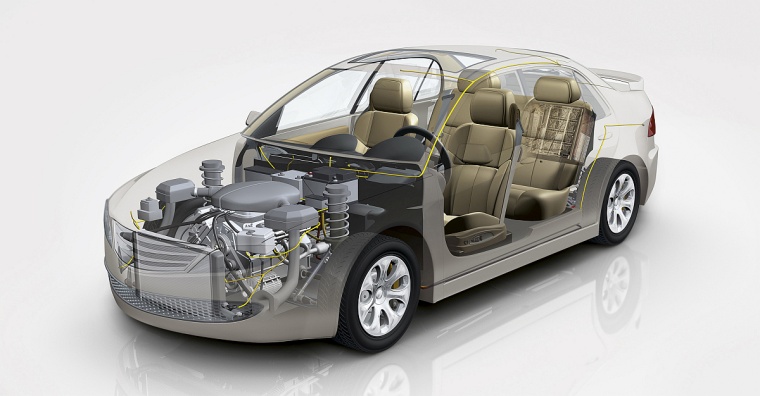
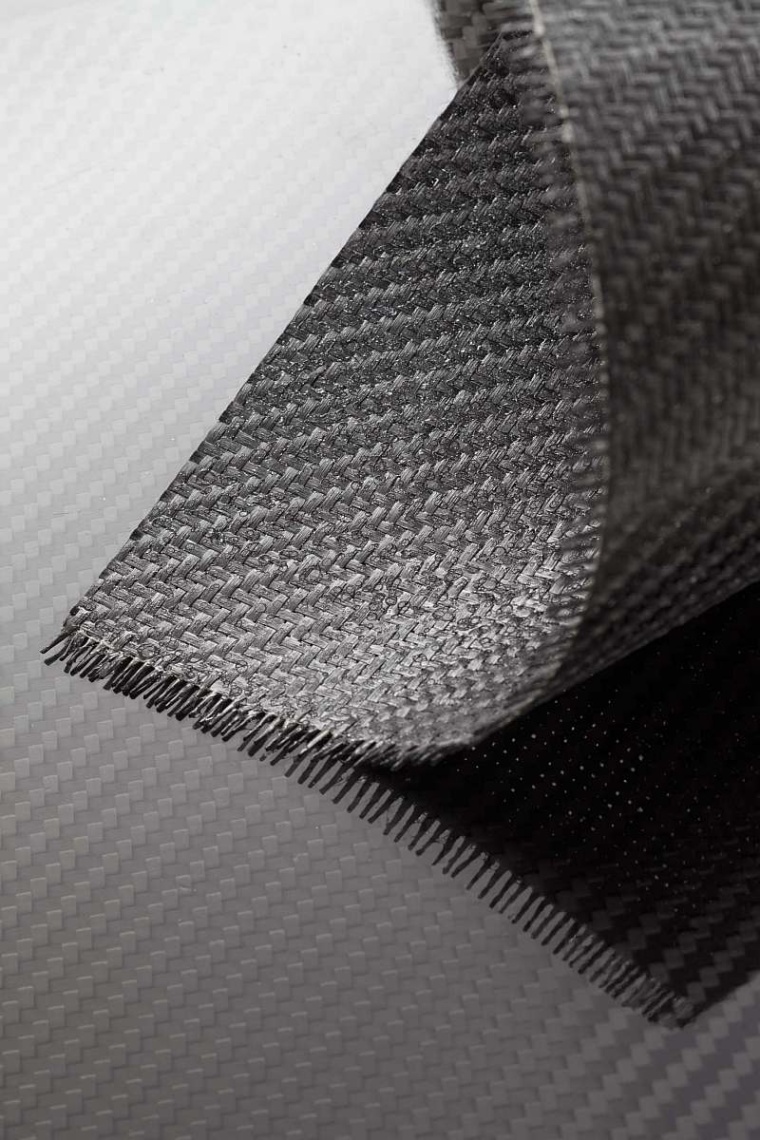
Glas- und Carbonfasern bieten enormes Leichtbaupotenzial – und sind damit besonders interessant für den Fahrzeug- oder Flugzeugbau. Bislang kann das Potenzial der Fasern jedoch nicht voll ausgeschöpft werden. Der Grund: Der Herstellungsprozess bis zum Verbundwerkstoff ist komplex und kostenintensiv. Mit Vestanat PP hat Evonik nun eine Technologie entwickelt, die sowohl die Prozessführung erleichtert als auch Material und Kosten einspart. Mehrere Projekte mit großen Autoherstellern, die die Technologie in der Produktion ihrer Zukunftsmodelle einsetzen wollen, sind bereits gestartet.
Vorstandsvorsitzender Klaus Engel zeichnete die Entwicklung mit dem Innovationspreis des Unternehmens für neue Produkte/neue Systemlösungen aus. „Für Innovationen brauchen wir die Kreativität, den Einsatz und den Mut unserer Mitarbeiter“, sagte Engel. „Der Erfolg von Vestanat PP zeigt, dass sich Vertrauen in die Idee, Beharrlichkeit gepaart mit der richtigen Portion Risikobereitschaft und technologische Kompetenz, auszahlen.“ Der Konzernchef verwies auf die Bedeutung von Innovation als strategischem Eckpfeiler für Wachstum bei Evonik. So will das Spezialchemieunternehmen in den nächsten zehn Jahren mehr als 4 Mrd. EUR in Forschung und Entwicklung investieren. Im Blick hat das Unternehmen dabei strategische Innovationsfelder wie Verbundmaterialien, Membrane, Tiernahrung oder Medizintechnik.
Eines der bislang üblichen Verfahren zur Herstellung von Verbundwerkstoffen für den Leichtbau ist das sogenannte Resin Transfer Molding, kurz: RTM. Dieses Verfahren erlaubt jedoch nur eine chargenweise Produktion von Bauteilen, keine kontinuierliche. Zwar kontinuierlich, aber nicht ganz einfach ist die Herstellung über Prepregs, also mit Harz und Härter bereits vorimprägnierte Fasern. „Gängige Prepregs haben die Nachteile, dass sie nur bei -20 °C gelagert werden können und sehr klebrig sind“, erklärt Guido Streukens, Senior Manager Business Development Crosslinkers.
Diese Nachteile werden von dem neuen Werkstoff ausgeschaltet: „Im Vergleich zu sonst üblichen Matrixsystemen, die aus den Fasern Verbundwerkstoffe werden lassen, erleichtert Vestanat PP die weiteren Produktionsschritte erheblich“, sagt Streukens. Verantwortlich dafür ist ein chemischer Trick: eine spezielle Kombination aus Katalysatoren. Diese Formulierung sorgt dafür, dass Prepregs nicht mehr kleben und beeinflusst zugleich den Vernetzungsprozess des Materials. Bei normalen Temperaturen ist es dadurch trocken und lagerstabil, ab 80 °C wird es thermoplastisch verformbar – ohne zu vernetzen - und erst oberhalb von 140 °C beginnt die Aushärtung. Weitere Vorteile der neuen Technologie sind die sehr guten mechanischen Eigenschaften des Matrixsystems; sie erlauben es, mit weniger Material die gleichen Bauteileigenschaften wie bei anderen Systemen zu erzeugen.
Damit kann der Einsatz des Materials den Herstellungsprozess von der Glas- oder Carbonfaser zum fertigen Bauteil deutlich vereinfachen, die Kosten senken und schließlich dazu beitragen, dass das Potenzial der Fasern industriell effektiver genutzt werden kann.
Meist gelesen
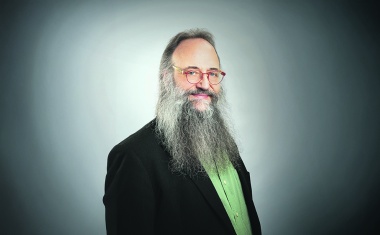
Erneuerbarer Kohlenstoff
Wenn die Chemie auf alternative Rohstoffe umsteigt, wirkt das dem Klimawandel effektiv entgegen.
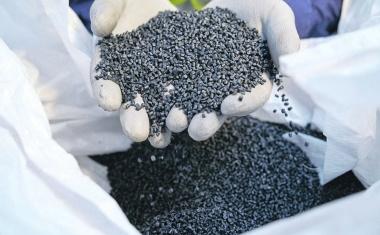
Best Practices für mehr Rezyklat im Auto
Die End-of-Life Vehicle Regulation (ELV) soll Automobilhersteller in der EU ab 2030 dazu verpflichten, 25 % der Kunststoffe in neuen Fahrzeugen aus Post-Consumer-Rezyklat (PCR) zu beziehen.
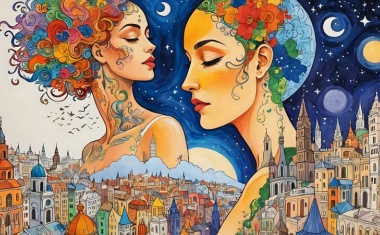
Engagagement für eine bessere Chemie
Interview mit Stefan Brejc, Global Vice President im Segment Coatings & Adhesives bei Clariant
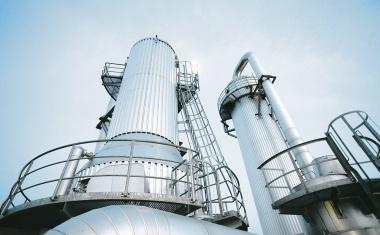
Kraftstoffe und Chemikalien aus Biomasse
Europas größter Zuckerproduzent, der Südzucker-Konzern mit Sitz in Mannheim, setzt auf erneuerbare Chemikalien und nachhaltige Agrarwirtschaft.
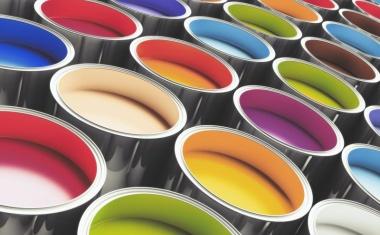
Antimikrobielle Technologien
Regulatorischen Rahmenbedingungen sind eine zentrale Herausforderung für Anwender und Hersteller antimikrobieller Technologien.