Treibhausgase messen statt berechnen
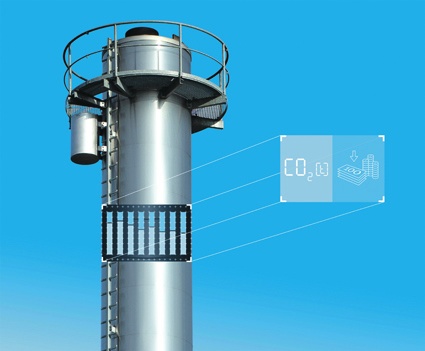
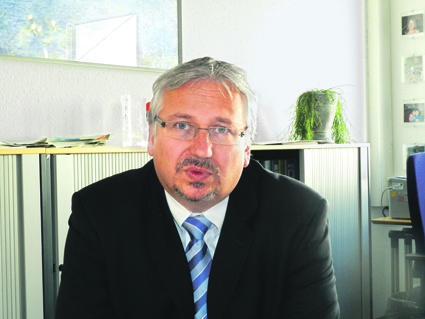
Lange vor der ersten Emissionsverordnung entwickelte Erwin Sick ein Rauchdichtemessgerät.
Wie es 65 Jahre nach der Firmengründung mit der Analysentechnik bei Sick bestellt ist, wollte CHEManager von Dr. Michael Markus, Head of Marketing & Sales, Sick Maihak, wissen. Das Gespräch führte Dr. Volker Oestreich.
CHEManager: Welchen Stellenwert besitzt die Prozessautomation heute bei Sick - das geht bestimmt weit über die Rauchdichtemessung hinaus?
Dr. Michael Markus: Willy Brandt hat im Jahr 1961 mit seinem Ausspruch „Der Himmel über Berlin muss wieder blau werden" den Grundstein für eine staatliche Umweltpolitik in Deutschland gelegt. Damals war die Überwachung und Minderung von Staubemissionen der erste Schritt zur Verbesserung der Luftqualität in industriellen Ballungsräumen.
Sick war seit den 1950er Jahren Pionier in der Staubmesstechnik und ist hier nach wie vor Markt- und Technologieführer weltweit. Ende der 1970er Jahre brachte man die ersten In-situ-Gasanalysatoren in den Markt - bis heute eine Domäne von Sick. Durch innovative Eigenentwicklungen und durch gezielte Akquisitionen wurde das Angebotsspektrum in der Umwelt- und Prozessmessetechnik insbesondere in jüngerer Vergangenheit deutlich erweitert.
Heute verfügen wir über ein umfangreiches Portfolio von Sensorprodukten und -lösungen für die Prozessautomation: Staubmesstechnik und Gasanalytik für Emissionsüberwachung und Prozesssteuerung, hochpräzise Durchflussmessung von Gasen mittels Ultraschall oder Laser-Scanner zur Überwachung von Schüttgutmengen auf Förderbändern, um nur einige Bespiele zu nennen. Eine breite Diversifizierung in den Anwendungsbranchen ist für Sick als Sensorspezialist eine notwendige Vorrausetzung für ein stabiles und nachhaltiges Wachstum.
Neben den Segmenten Fabrikautomation und Logistikautomation bildet die Prozessautomation eine wichtige dritte Säule der Geschäftstätigkeiten der Sick Gruppe. Im letzten Geschäftsjahr 2011 waren unsere Aktivitäten in der Prozessautomation für rund 18 % des Konzernumsatzes von insgesamt 903 Mio. EUR verantwortlich.
Mit Ihren Analysegeräten sind Sie besonders da im Einsatz, wo etwas verbrannt wird. Wie sieht Ihr Branchenfokus genau aus?
Dr. Michael Markus: Verbrennungsprozesse sind nach wie vor für viele Bereiche der Prozessindustrie elementar, sei es bei der Strom-und Wärmeerzeugung aus fossilen Energieträgern, bei der thermischen Verwertung von kommunalen oder industriellen Abfällen, bei der Produktion von Zement, Glas und Keramik oder in der Stahlerzeugung. Die Analyse von Rauchgasen ist daher ein wichtiger Anwendungsschwerpunkt für unsere Prozessanalysengeräte. Neben den genannten Branchen fokussieren wir uns aber auch auf die Bereiche Chemie, Petrochemie, Öl & Gas und Zellstoffherstellung.
Die Erfüllung der umweltgesetzlichen Auflagen gehört zum Pflichtprogramm unserer Kunden. Die gesetzlichen Anforderungen an die Emissionsüberwachung sind dabei regional wie branchenspezifisch sehr unterschiedlich. Wir optimieren all unsere Komplettlösungen auf eine hohe Verfügbarkeit bei gleichzeitig geringen Wartungsanforderungen und damit auf Sicherheit und Kosteneffizienz über die gesamte Lebenszeit der Messeinrichtung.
Darüber hinaus bieten wir maßgeschneiderte Lösungen zur Prozessoptimierung in vielen Bereichen unserer Zielbranchen. Unsere Prozessgasanalysatoren messen dabei direkt in den verfahrenstechnischen Anlagen, insbesondere in ungereinigten Rauch- oder Prozessgasen. Dabei müssen gegebenenfalls Druck- und Temperaturschwankungen, Partikelbeladung, Gasfeuchte, sowie korrosive, toxische oder explosive Bestandteile des Gasstroms toleriert werden können. Hier stehen gute Performance und hohe Robustheit der analytischen Lösungen an erster Stelle.
Die genannten Branchen sind dann ja im Wesentlichen auch die, die von der neuen IED, der Industrieemissionsrichtlinie der EU, betroffen sind?
Dr. Michael Markus: Ja, das ist richtig. In Deutschland gibt es bereits seit dem Jahr 1964 die „Technische Anleitung zur Reinhaltung der Luft", kurz TA Luft, die für alle genehmigungspflichtige Industrie- und Gewerbebetriebe verbindliche Höchstgrenzen für die Freisetzung von Schadstoffen festlegt. Auf europäischer Ebene wurden bislang Genehmigungsrichtlinien für den Schadstoffausstoß bestimmter Anlagen erlassen, darunter für Kraftwerke und Müllverbrennungsanlagen. Mit der Industrial Emissions Directive (IED) 2010/75/EU gibt es nunmehr auch auf europäischer Ebene eine alle wesentlichen Industriebereiche umfassende Richtlinie. Diese muss nächstes Jahre auch in nationales deutsches Recht überführt werden. Nationale Gesetze können dabei über die Anforderungen aus den gesamteuropäischen Vorschriften hinausgehen.
Als Folge der im Kyoto-Protokoll festgelegten Klimaschutzziele ist der EU-Emissionshandel entstanden mit dem Ziel, die Treibhausgasemissionen unter minimalen volkswirtschaftlichen Kosten zu senken. Wie unterstützen Sie Ihre Kunden bei diesem Thema?
Dr. Michael Markus: Mit Jahresanfang 2013 tritt Europa in die dritte Handelsperiode des EU Emissionshandels ein. Die Menge der Verschmutzungsrechte in Form von CO2-Emssionszertifikaten wird bis zum Jahr 2020 sukzessiv jedes Jahr um 1,74 % gesenkt. Verschmutzungsrechte werden also über die nächsten Jahre ein zunehmend knapperes und damit teureres Gut. Damit rückt die Ermittlung und Beschaffung der für den Betrieb einer Anlage benötigten CO2-Zertifikate mehr und mehr in den Fokus der Betreiber. Die Ermittlung des Kohlenstoffanteils in sämtlichen für die Emissionen relevanten Stoffströmen erweist sich aber in der Praxis als nicht unproblematisch, insbesondere für Anlagen mit wechselnden oder komplexen Betriebsstoffströmen.
Glücklicherweise stellt der Gesetzgeber es den Betreibern inzwischen frei, ob die CO2-Emissionen rechnerisch aus Stoff- und Betriebsdaten oder mittels geeigneter Messtechnik an den Emissionsstellen ermittelt werden. Die zulässigen Gesamtunsicherheiten für die Ermittlung der Treibhausgasfrachten stellen dabei hohe Anforderungen sowohl an die Berechnung als auch an Messtechnik. Für Anlagen mit mehr als 500.000 t CO2 Emissionen pro Jahr soll die Gesamtunsicherheit der Bestimmungsmethode den Wert von 2,5 % nicht überschreiten. Durch die Kombination zweier etablierter und hochpräziser In-Situ-Messverfahren für die Gasanalytik und die Volumenstrommessung an der Emissionsstelle kann Sick als derzeit einziger Messtechnik-Anbieter diese Hürde nachweislich nehmen. Damit wird die Formel „Treibhausgase messen statt berechnen" zu einer echten Alternative für die Betreiber.
Dabei kommen dann also überwiegend kontinuierlich arbeitende Messsysteme zum Einsatz. Wann und wo werden denn In-situ Verfahren eingesetzt und wann kalt- oder heiß-extraktive Verfahren?
Dr. Michael Markus: Moderne In-Situ-Verfahren zeichnen sich durch geringe Betriebskosten bei gleichzeitig hoher Verfügbarkeit aus. Und dies auch in anspruchsvollen Prozessapplikationen, wo es auf hohe Messgeschwindigkeit und Robustheit ankommt . Da die Messtechnik direkt an der Messstelle sitzt, entfallen auch die Kosten für spezielle Analysenhäuser. Auch eine Probenstromentnahme und -aufbereitung wird nicht benötigt. So entfällt auch der damit verbunden Wartungsaufwand, der erfahrungsgemäß bis zu 2/3 des Gesamtaufwands für ein automatisches Messsystem (AMS) ausmacht. Demgegenüber sind die Anschaffungskosten für In-Situ-Geräte je nach Anzahl und Kombination der notwendigen Messgrößen im Vergleich zu kalt-extraktiver Messtechnik oft etwas höher.
Bei der kalt-extraktiven Messtechnik wird der Probengasstrom hinsichtlich Temperatur, Druck und Partikelbeladung konditioniert und der Feuchteanteil des Probenstroms wird in einem Messgaskühler entfernt. Auf diese Weise können preisgünstige Analysengeräte zum Einsatz kommen. Für die Gesamtkostenbetrachtung ist jedoch der Aufwand für die Anschaffung und den Betrieb des Probennahmesystems und des Analysenhauses zu berücksichtigen.
Gaskühler können nicht zum Einsatz kommen, wenn die Gasfeuchte selbst oder wasserlösliche Gaskomponenten wie z.B. HCl, NH3 oder HF gemessen werden sollen. Neben der In-Situ-Messung können dann heiß-extraktive Verfahren zum Einsatz kommen. Hier wird der Probengasstrom durchgängig, von der Entnahmesonde bis zum Analysengerät, bei ca. 200°C und damit über allen relevanten Taupunkten gehalten und nur mittels eines Filters in der ebenfalls beheizten Entnahmesonde von Partikeln befreit. Auf diese Weise kann man z.B. auch in unverdünnten Rauchgasen mit hohen Säuretaupunkten messen.
Und wie ist Sick bei diesen Verfahren aufgestellt?
Dr. Michael Markus: Sick produziert seine Analysengeräte in vier Werken in Deutschland, wobei jedes Werk seine eigene, langjährige Technologiekompetenz besitzt. Aus der Zentrale in Reute bei Freiburg i.B. kommen die In-Situ-Gasanalysatoren aber auch Geräte zur Luftqualitätsüberwachung in Straßentunneln.
Am Standort Reute aber auch an einigen anderen Stellen in der Welt, so z.B. in China oder in Brasilien, entstehen auch Komplettlösungen nach Kundenspezifikation. Aus dem Standort Hamburg, der ehemaligen Maihak AG, kommen unsere kalt-extraktive Messgeräte, FID-Analysatoren und Datenerfassungssysteme. Der Standort Meersburg, 1999 von Perkin-Elmer übernommen, steht für heiß-extraktive Messtechnik für Gase, Flüssigkeiten und Quecksilber. In der Nähe von Dresden werden neben unseren bekannten Ultraschall-Gaszählern die Staubmessgeräte gefertigt.
Im Frühsommer dieses Jahres wurde die Kooperation von Sick und Yokogawa auf eine noch breitere Basis gestellt. Welche langfristige Zielsetzung verfolgen Sie damit?
Dr. Michael Markus: Die Zusammenarbeit mit Yokogawa besteht in Europa seit mehr als 3 Jahren und wird seit diesem Jahr weltweit etabliert. Das strategische Ziel dieser Allianz ist die Verbreiterung der Lösungskompetenz beider Partner im Sinne unserer Kunden durch Nutzung des jeweils komplementären Produktspektrums. Sick bietet das breiteste Angebot an kontinuierlicher Gasanalytik und verfügt über eine umfassende Kompetenz hinsichtlich der legislativen Anforderungen an Anlagenbetreiber.
Yokogawa verfügt demgegenüber über eine langjährige Expertise in der Gaschromatographie, einer Schlüsseltechnologie insbesondere für Analytiklösungen in der Chemie und in der Kohlenwasserstoff verarbeitenden Industrie. Darüber hinaus kann Yokogawa in der Zusammenarbeit mit Sick komplette Prozessautomatisierungslösungen bestehend aus Leitsystem, Feldgerätetechnik und Prozessanalytik anbieten. Viele Kunden erwarten diese umfassende Lösungskompetenz aus einer Hand. Als Messtechnik-Spezialist könnte Sick dies alleine nicht darstellen.
Wie soll Ihr Unternehmen in zehn Jahre aussehen und welche Randbedingungen im Markt werden sich in dieser Zeit ändern?
Dr. Michael Markus: Im Vergleich mit einem Druck- oder Temperaturtransmitter ist die Anmutung eines Analysensystems oft noch weit entfernt von der landläufigen Vorstellung von einem einfachen Sensor. Analysenhäuser nennen wir daher scherzhaft „begehbare Sensoren". Moderne Verfahren wie z.B. die Laserspektroskopie erlauben aber auch heute schon Gerätekonzepte, z.B. für die Messung von Sauerstoff in Prozessanlagen, die „transmitter-like" verwendet werden können: anschrauben, anschließen, anschalten, messen. Diesen oft genannten Kundenwunsch nach einfacher und dennoch leistungsfähiger Prozessanalytik wollen wir auch in Zukunft weiter ausbauen. Auf der legislativen Seite wachsen auch zukünftig die Anforderungen hinsichtlich der Anzahl der zu messenden Komponenten und deren Nachweisgrenzen.
Mittels hochintegrierter Messsysteme machen wir komplexe Multi-Sensorik für das Anlagenpersonal leicht handhabbar und neben den jährlichen Routinechecks nahezu wartungsfrei.
Am Ende dieses Geschäftsjahres wird Sick Maihak, die als Tochtergesellschaft von Sick mit Fokus auf die Branchen der Prozessautomation aufgestellt wurde, in den Gesamtkonzern re-integriert werden. Ein starkes Signal dafür, dass Sick die Prozessautomation und mit ihr die Analysentechnik als integralen Bestandteil seiner auf Wachstum ausgerichteten Strategie begreift. Wir konzentrieren uns dabei heute wie auch in 10 Jahren ausschließlich auf den Bereich der industriellen Sensorik.
Das Marktumfeld erscheint uns auch langfristig attraktiv: Unsere Kunden investieren weltweit in Prozessanlagen und deren Modernisierung, um der wachsenden Nachfrage insbesondere aus den Schwellenländern nachzukommen. Dabei nimmt der Stellenwert von Prozessanalytik mit jeder Anlagengeneration zu, sei es zur Erfüllung gesetzlicher Auflagen, zur Erhöhung der Anlagensicherheit oder zur Verbesserung der Prozesseffizienz. Sensorik und insbesondere Prozessgasanalytik ist ein Expertengeschäft - und Sick ist der Global Player unter den reinrassigen Gasanalytik-Experten.