Pulsationsreaktor – periodisch instationär
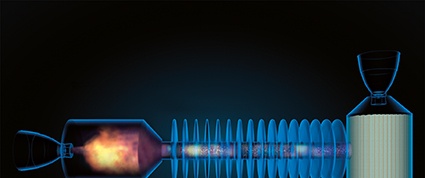
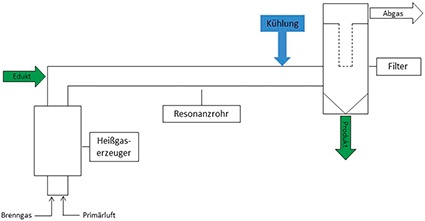
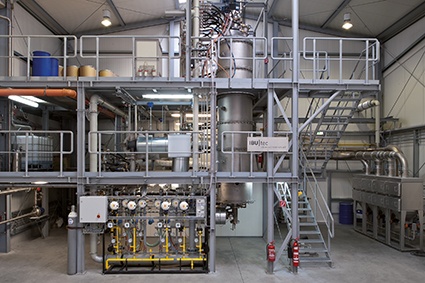
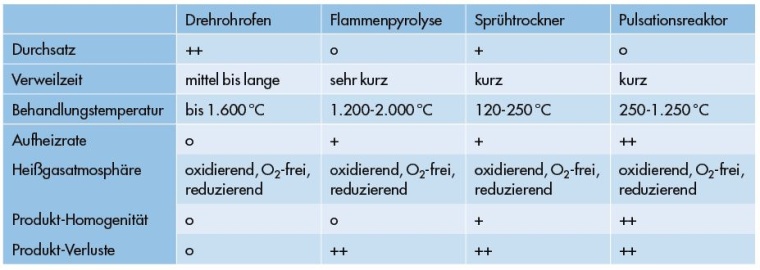
CITplus - Die Weimarer Firma IBU-tec setzt Pulsationsreaktoren ein, um Pulverwerkstoffe mit besonderen Eigenschaften herzustellen.
Der Pulsationsreaktor hat sich insbesondere zur Herstellung von keramischen und nanoskaligen Pulvern, wie auch zur Herstellung von hochaktiven Katalysatoren bewährt. Dabei können einfache Oxide wie Zinkoxid, aber auch Partikel wie Zirkoniumoxid mit Dotierungselementen oder Mischoxide wie Spinell produziert werden.
Funktionsweise und Aufbau
Prinzipiell handelt es sich bei einem Pulsationsreaktor um einen periodisch-instationär arbeitenden Rohrreaktor, in dem gasgetragene Stoffe thermisch behandelt werden können. Pulsationsreaktoren der ersten und zweiten Generation unterscheiden sich dabei hinsichtlich des grundsätzlichen Aufbaus nicht.
Die Erzeugung des pulsierenden Heißgasstromes erfolgt bei Pulsationsreaktoren beider Generationen innerhalb eines Heißgaserzeugers durch die Verbrennung von Erdgas oder Wasserstoff mit Umgebungsluft. Das Heißgas strömt durch ein Resonanzrohr in das pulverförmiges, flüssiges oder gasförmiges Edukt aufgegeben werden kann. Die Behandlung erfolgt durch die Heißgasströmung innerhalb des Resonanzrohres und wird durch geeignete Abkühlung definiert beendet. Das fertige Produkt wird in einem abreinigbaren Filter abgeschieden aus dem mit Hilfe eines Schleusensystems das Produkt während des laufenden Prozesses entnommen und in Fässer oder Bigbags abgefüllt werden kann. Im gesamten Reaktor - inklusive Filter - herrscht ein leichter Unterdruck, wodurch ein Austreten von Produkt in die Umwelt vollständig ausgeschlossen werden kann.
Durch das Pulsieren der Heißgasströmung bildet sich im Resonanzrohr - dem Behandlungsraum für das Edukt - eine nahezu kolbenförmige Strömung mit einer über den Rohrdurchmesser nahezu konstanten Temperatur aus. Die kolbenförmige Strömung führt zu einer engen Verweilzeitverteilung, wodurch zusammen mit den geringen Temperaturgradienten im Behandlungsraum eine sehr homogene Behandlung des Eduktes sichergestellt wird. Neben den homogenen Behandlungsbedingungen bewirkt die pulsierende Heißgasströmung einen erhöhten konvektiven Wärme- und Stofftransport zu bzw. von den Partikeln. Dadurch werden hohe Aufheizraten bei pulverförmigen und flüssigen Edukten erreicht.
Ein wesentlicher Unterschied der Pulsationsreaktoren der ersten und zweiten Generation liegt in der Art und Weise wie das Heißgas erzeugt wird. Bei Pulsationsreaktoren der ersten Generation arbeitet der Heißgaserzeuger mit hohem Luftüberschuss (l ≥ 2), bei den Pulsationsreaktoren der zweiten Generation kann die Heißgasatmosphäre auch sauerstofffrei oder reduzierend erzeugt werden. Auch die Heißgastemperaturen können bei den Pulsationsreaktoren der zweiten Generation über einen größeren Bereich (250 °C - 1.250 °C) als bei den Pulsationsreaktoren der ersten Generation (400 °C - 1.000 °C) variiert werden. Die tatsächliche Behandlungstemperatur kann sich nach Zuführung des Eduktes jedoch deutlich von diesen Werten unterscheiden. So sind beispielsweise bei Eduktsuspensionen auf Wasserbasis niedrigere Werte für die Heißgastemperatur nach Materialaufgabe zu erwarten, bei Edukten mit exothermer Reaktion höhere. Die tatsächlich erforderlichen Behandlungstemperaturen müssen durch systematische Versuche mit Temperaturvariation ermittelt werden.
Neben der Behandlungstemperatur und der Art der Heißgasatmosphäre kann in den Pulsationsreaktoren der zweiten Generation auch die Pulsation, d. h. die räumlich oszillierende Heißgasströmung, ohne Änderung der Anlagengeometrie in Frequenz und Amplitude auf das zu behandelnde Material abgestimmt werden.
Vergleich des Pulsationsreaktors mit anderen Herstellungsverfahren
Drehrohrofen
Drehrohröfen sind industriell häufig genutzte Reaktoren zur thermischen Behandlung einer Vielzahl von Stoffen. Bei indirekt beheizten Drehrohröfen sind auch sauerstofffreie und reduzierende Heißgasatmosphären zur Materialbehandlung verwirklichbar.
Da der Feststoff im Drehrohrofen nicht gasgetragen ist, sind hohe Materialdurchsätze mit vergleichsweise geringem Aufwand zur Abscheidung des fertigen Produktes möglich. Die Verweilzeit des Feststoffes ist erheblich länger als im Pulsationsreaktor und kann durch Einbauten im Drehrohr beeinflusst werden. Da das Material als Schüttung durch den Drehrohrofen transportiert und behandelt wird, ergeben sich ein Temperaturprofil sowie eine breite Verweilzeitverteilung während der Behandlung, wodurch das Produkt wesentlich inhomogener wird als bei einer Behandlung im Pulsationsreaktor. Das vollständige Vermeiden eines Produktaustritts in die Umwelt ist bei Drehrohröfen schwierig zu realisieren. Zudem ist durch die zahlreichen Einbauten im Drehrohrofen eine vollständige Reinigung, wie es bei den Pulsationsreaktoren bei Produktwechseln üblich ist, nicht möglich.
Flammenreaktor
Flammenreaktoren werden hauptsächlich zur Herstellung von Oxiden verwendet, es können aber auch reduzierende Flammen zur Synthese nichtoxidischer oder metallischer Produkte eingesetzt werden. Die Produktqualität wird dabei von der Verweilzeitverteilung und dem Temperaturprofil der Flamme bestimmt. Somit beeinflusst die Flammenart maßgeblich die Produktqualität.
Im industriellen Maßstab werden hauptsächlich turbulente Diffusionsflammen eingesetzt, da diese einfach zu variieren und ein Flammenrückschlag im Betrieb ausgeschlossen ist. Allerdings besitzen Diffusionsflammen ein ausgeprägtes Temperaturprofil, wodurch es zu einer inhomogenen Behandlung der Produkte kommt.
Im Vergleich zum Pulsationsreaktor lassen sich in Flammenreaktoren höhere Behandlungstemperaturen erzielen, allerdings ist der Einsatz von brennbaren Edukten zwingend erforderlich. Im Gegensatz dazu können im Pulsationsreaktor sowohl brennbare Edukte, als auch nicht brennbare Edukte zum Einsatz kommen. Darüber hinaus kommt es durch die hohen Temperaturen in einzelnen Zonen der Flamme des Flammenreaktors zu einer wesentlich stärkeren Bildung von harten Aggregaten als im Pulsationsreaktor.
Sprühtrockner
Sprühtrockner sind die wohl am häufigsten eingesetzten verfahrenstechnischen Anlagen in denen Pulver aller Art hergestellt werden. Die heute industriell eingesetzten Konvektionssprühtrockner überführen Flüssigkeiten, Schlämme, Pasten und Breie in feinteilige Pulver mit Korngrößen zwischen ca. 2 µm und 400 µm. Die Behandlung der Edukte erfolgt im Allgemeinen zwischen 120 °C und 250 °C, was eine schonende Trocknung ermöglicht.
Durch das Versprühen der Edukte tritt bei Sprühtrocknern häufig eine relativ große Mischzone mit inhomogenen Temperatur- und Geschwindigkeitsprofilen auf. Durch die Pulsation im Pulsationsreaktor kann dieser Effekt reduziert werden, so dass die Materialbehandlung homogener ist. Der durch den Pulsationsreaktor abgedeckte Temperaturbereich ist deutlich höher, wodurch einerseits eine schonende Trocknung nur eingeschränkt möglich ist, dafür andererseits eine Zusammenfassung von Trocknung und Kalzinierung umsetzbar ist.
Fazit
Der Pulsationsreaktor ist ein seit über 10 Jahren industriell erprobtes Herstellungsverfahren für pulverförmige Rohstoffe. In diesem Zeitraum wurden ca. 5.000 t verschiedener pulverförmiger Materialien an Kunden in aller Welt ausgeliefert.
Die Besonderheiten der Pulsationsreaktor-Technologie liegen in der kurzen Verweilzeit, einer hohen Aufheizrate sowie dem hohen Wärme- und Stofftransport in bzw. aus den Partikeln. Eine homogene Temperaturverteilung und eine enge Verweilzeitverteilung garantieren eine gleichbleibend hohe Produktqualität. Dank der wählbaren Gasatmosphäre - oxidierend, sauerstofffrei oder reduzierend - und der auf das Material in Frequenz und Amplitude einstellbaren Pulsation können auch bei schwierigen Materialien herausragende Ergebnisse erzielt werden.
Während der 20 Jahre andauernden Entwicklung des Pulsationsreaktors bei IBU-tec stellte sich immer wieder heraus, dass im Pulsationsreaktor erzeugte Materialien besondere Eigenschaften aufweisen: Hohe spezifische Oberflächen, eine gesteigerte Reaktivität, sehr homogene Produkte und Partikel bis in den Nanometerbereich mit engen Größenverteilungen sind nur einige Beispiele für die Leistungsfähigkeit des Pulsationsreaktors. Typische Anwendungsfelder sind hierbei Katalysatormaterialien, Hochleistungskeramiken, transparenter UV Schutz, Farbpigmente, Katalysatorträgerkeramiken und Batteriewerkstoffe.
Firmeninfo
Die IBU-tec advanced materials AG ist ein international agierendes Unternehmen im Bereich der Verarbeitung/Veredelung von Pulvern und Granulaten. Das Weimarer Unternehmen bietet Forschungs- und Produktionskapazitäten für die Entwicklung und Herstellung von kundenspezifischen Materialien auf Basis seiner thermischen Anlagen an. Mit dem eigenentwickelten und patentierten Pulsationsreaktor verfügt IBU-tec über eine Technologieplattform, mit der nano- bis mikroskalige Pulver in herausragender Qualität und am Markt einzigartigen Eigenschaften produziert werden. Darüber hinaus stehen den Kunden zahlreiche Drehrohrofenanlagen für Entwicklungsaufgaben und Lohnproduktionen zur Verfügung. Bei einzelnen Versuchen aber auch kompletten Lohnfertigungen kann die laufende Produktion in den eigenen Laboratorien überwacht werden.