Prozessgrenzen zuverlässig ausloten und beherrschen
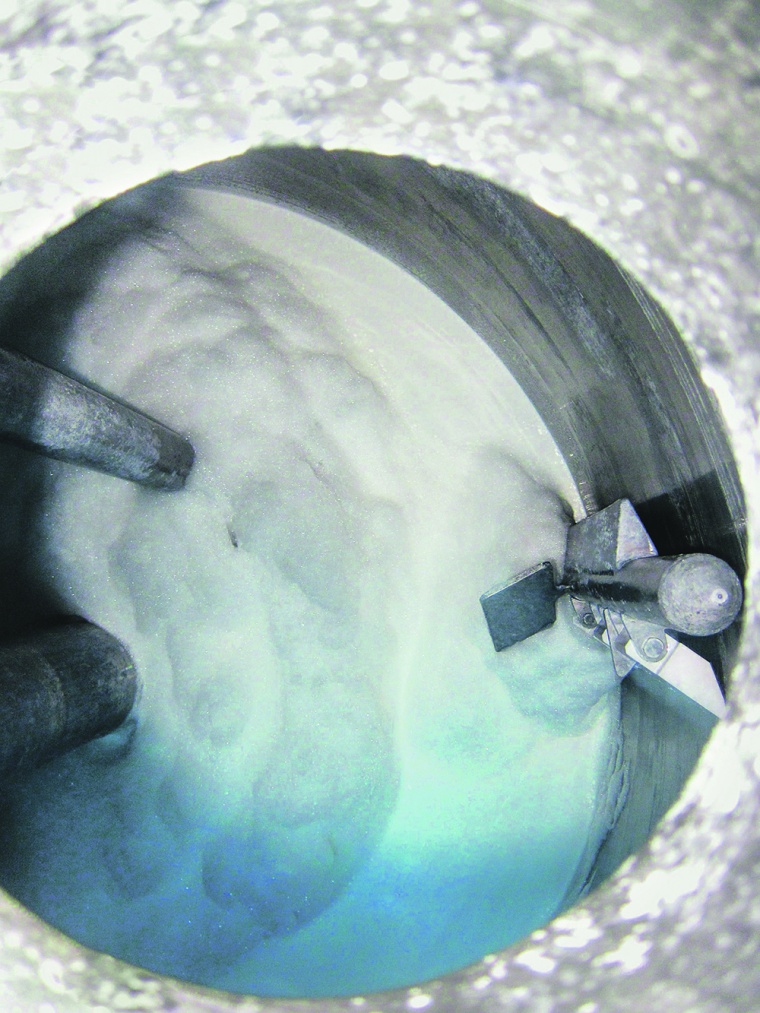
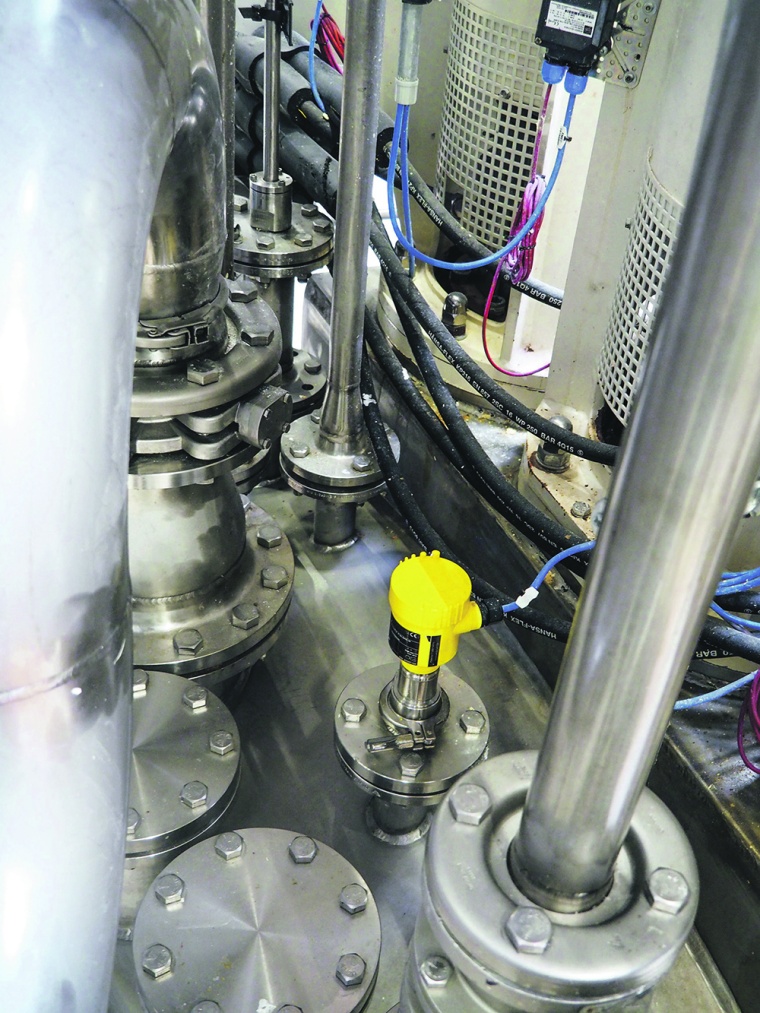
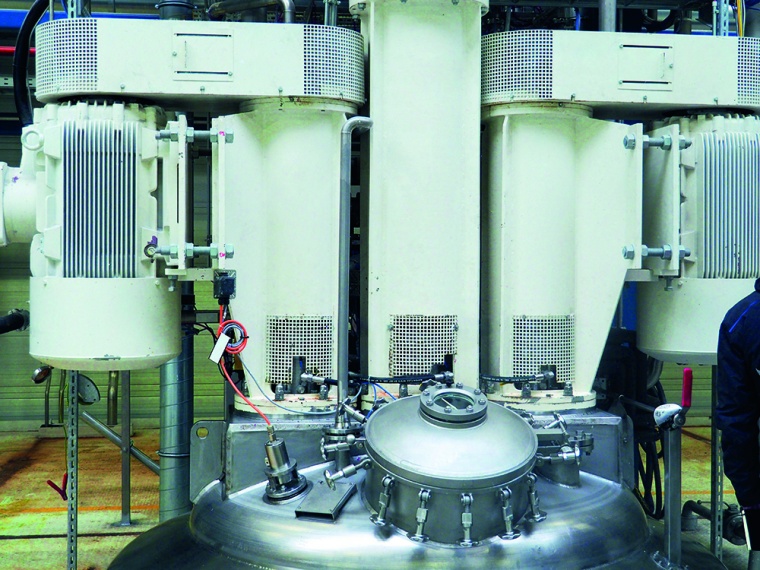
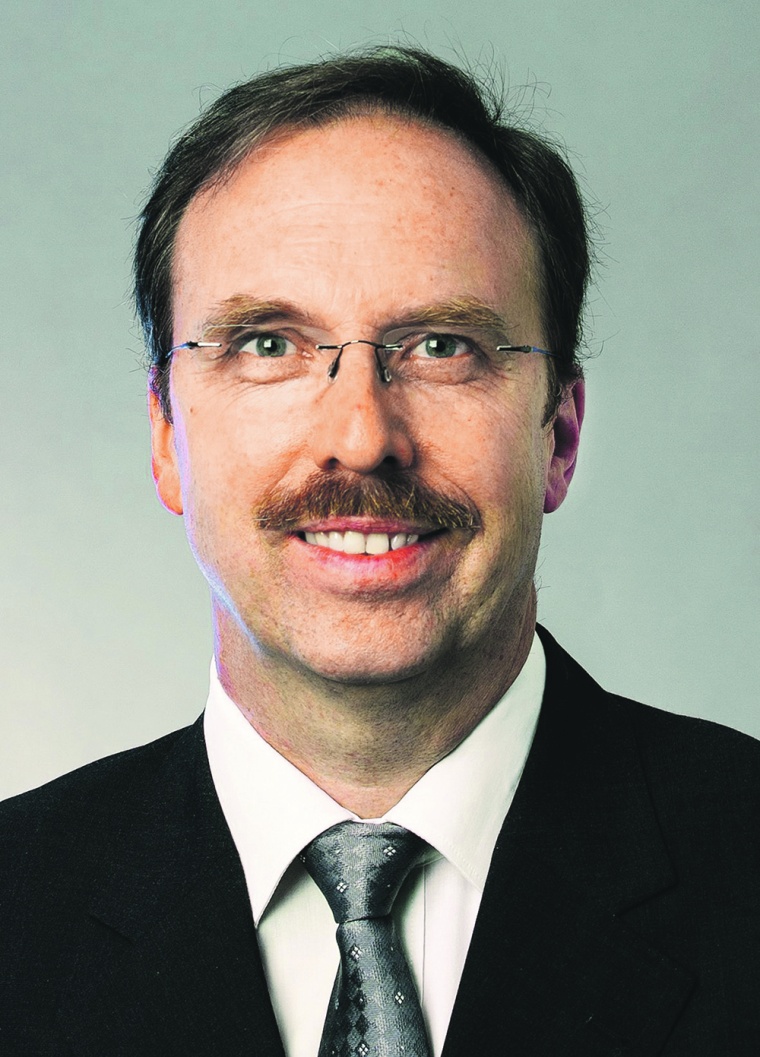
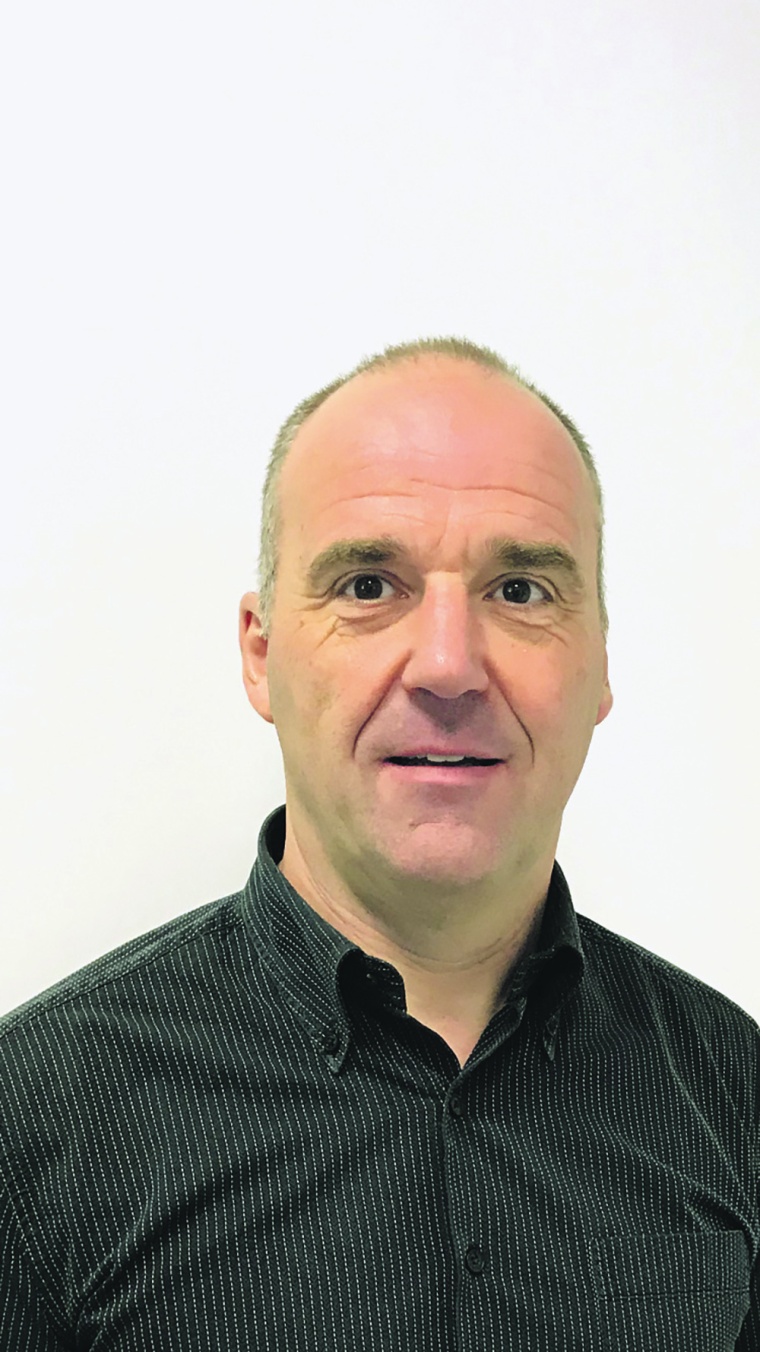
Immer wenn Textilien besondere Eigenschaften aufweisen, ist mit großer Wahrscheinlichkeit der Spezialchemikalienhersteller CHT involviert: Er liefert Verdickungsmittel für Textilfarben, damit diese beim Bedrucken der Stoffe nicht davonfließen. Einige Textilien bekommen ein flammenhemmendes Additiv, andere sind dank eines CHT-Produkts wasserdicht oder besitzen temperierende Eigenschaften.
Das Unternehmen ist mit seinen Produkten aber auch in der Teppichproduktion vertreten und entwickelt besondere Klebstoffe für Gummidichtungen in der Automobilindustrie. Mit anderen Worten: Der Produktvielfalt sind keine Grenzen gesetzt. Für den Schutz seiner Rührwerke, quasi das Herzstück der Produktion, setzt das Tübinger Unternehmen auf den Radarfüllstandsensor Vegapuls 64.
Hochviskose Produkte zuverlässig mischen
Am Dusslinger Standort der CHT Germany nahe Tübingen werden jährlich 50.000 t Spezialchemikalien für den B2B-Markt produziert. In einem Teilbereich der Produktion werden hochviskose Produkte auf mehreren Mischeranlagen – gewaltigen Behältern aus Edelstahl mit speziell designten Rührwerken – hergestellt. Drei Motoren mit bis zu 160 kW und 1.000 Umdrehungen pro Minute in jedem dieser Behälter sorgen dafür, dass der Kesselinhalt effektiv durchmischt wird. „Wir haben ein besonderes Know-how bei der Verarbeitung extremer Viskosität aufgebaut. Üblicherweise können mit Maschinen dieser Bauart lediglich 70.000 mPas erreicht werden. Durch ein spezielles Anlagendesign können wir bis zu viermal zähere Produkte darauf herstellen. Gleichzeitig – und das ist einmalig – eignet sich das Anlagendesign auch für niedrigviskose Produkte“, erklärt Günther Schätzle, Leiter Technik am Standort Dusslingen, die Besonderheit seiner Produktion. Während der Verarbeitung müssen sich die mehrstufigen Rührorgane immer unterhalb der Flüssigkeit befinden: Angesichts der kraftvollen Motoren könnte es sonst zu Vibrationen und Resonanzschwingungen kommen, die letztendlich die Welle oder das gesamte Aggregat schädigen. Wie kann man jedoch bei den bis zu 8 m hohen und 2 m breiten Behältern immer sicher sein, dass die Rührorgane mit Flüssigkeit bedeckt sind? Schließlich wechseln nicht nur die Prozessbedingungen täglich, sondern auch die Produkteigenschaften, bspw. schwanken Dichte oder Viskosität erheblich. Häufig gleicht der Behälterinhalt mit seinem Schaum und den starken Turbulenzen einem brodelnden Hexenkessel.
Um zu verhindern, dass die Rührwerke im Durchgangsbetrieb liefen oder es zu Resonanzschwingungen kam, fuhr man früher extrem vorsichtig und kontrollierte den Füllstand immer wieder manuell. „Die Behälter waren auf diese Weise jedoch nicht optimal ausgelastet. Zudem haben wir inzwischen stärkere Motoren im Einsatz, so dass die Situation noch einmal brisanter ist“, beschreibt Schätzle die Ausgangssituation.
Aufgrund seiner Sendefrequenz von 80 GHz
zeichnet sich der Vegapuls 64 durch eine extrem hohe Fokussierung aus.
Die erste Lösung bestand darin, Wägezellen unter den Mischbehältern zu installieren. Aber dies ist aus verschiedenen Gründen nicht ideal, denn die Produkte haben unterschiedliche Dichten und der Behälter besitzt einen Kühl-/ Heizmantel. Manchmal ist dieser nur mit Dampf gefüllt, wiegt also kaum etwas. Wenn jedoch Kühlwasser verwendet wird, kommen ganz schnell zusätzliche 400 kg auf die Waage. Eine weitere Problematik: Früher befanden sich die Behälter auf einer Ebene und um sie herum wurde eine Ex-Zone gelegt. Mittlerweile sind die Behälter in einem anderen Gebäude untergebracht und reichen über mehrere Stockwerke. Beim Einsatz von Wägezellen muss der Behälter von den Wänden mechanisch entkoppelt sein. In diesem Fall würde sich die Ex-Zone über mehrere Stockwerke ausweiten. Damit müsste dann das gesamte Gebäude in ATEX ausgelegt werden, was zu enormen Mehrkosten führen würde.
Für Günther Schätzle war diese Situation nicht zufriedenstellend. „Wir haben etwa 6.000 Produkte, die wir aus 3.000 bis 4.000 Rohstoffen für 9.000 Kunden zusammenstellen. Fast jedes Produkt ist maßgeschneidert. Um unsere Kunden pünktlich und vor allem mit einer durchgängig hohen Qualität zu beliefern, müssen wir die Produktion sehr effizient betreiben und jeden Schritt nachvollziehbar gestalten. Deshalb haben wir eine Prozesssteuerungslösung aus der Fertigungs- in die Chemieindustrie transformiert und dabei die besonderen Anforderungen der Chemie berücksichtigt.“ Dank des Prozessleitsystems Aprol von B&R wissen Schätzle und seine Kollegen heute von jedem Monitor in der Produktion aus, welcher Prozessschritt gerade getätigt wird und ob er problemfrei läuft.
Nicht verwunderlich also, dass Schätzle zum Schutz der Rührwerke eine effektive Lösung suchte und einen etwas anderen Weg fand. Es sollte eine Füllstandmessung integriert werden, deren Messergebnisse sich direkt auf die Antriebsleistungen der Rührwerksmotoren auswirkte. „Wir brauchen die Füllstandmessung also nicht im Sinne einer Bestandsmessung oder zum Dosieren, denn das geschieht bei uns über eine Negativverwiegung der Rohstoffe. Wir brauchen sie zur Sicherung unserer Anlagentechnik“, bekräftigt er.
Wir verwenden die gemessene Signalstärke als Indikator dafür,
ungewünschte Schaumbildung zu reduzieren.
Fokussiert im Rührwerk
Die Umsetzung in die Praxis war jedoch nicht ganz so einfach, was in erster Linie an der besonderen Einbausituation im Behälter lag. Darin befinden sich nicht nur drei unterschiedliche Rührwerke und ein umlaufendes Schaberelement, die alle als Störgeometrien die Messung behindern, sondern auch turbulente Oberflächen, wechselnde Temperaturen, schnell wechselnde Dichten und Viskosität, Dampf, Staub, Anhaftungen, etc. – Bedingungen also, die zuverlässige Messungen des Füllstandes deutlich erschweren.
Die Lösung: Das berührungslos messende Radarfüllstandmessgerät Vegapuls 64, das sich aufgrund seiner Sendefrequenz von 80 GHz durch eine extrem hohe Fokussierung und große Dynamik auszeichnet. Dadurch misst es sehr zuverlässig und trotzt den sich ständig ändernden Prozessbedingungen: „Wir füllen zum Beispiel Rohstoffe ein, die stark schäumen. Es kommt zu Ablagerungen, die Rührwerke und die Mischer sorgen für gewaltige Turbulenzen – das allein ist schon schwierig für eine präzise Füllstanderfassung. Und bei uns wechseln ja auch noch die Prozessbedingungen ständig“, erklärt Schätzle.
Bewertung der Messsicherheit
Da die Füllstandmessung für die Sicherheit der Anlagenkomponenten so wesentlich ist, wünschte sich Schätzle zudem eine Beurteilung der Qualität des Messsignals, also eine Angabe der Messsicherheit in Prozent. Diese Werte stehen bei den Radarsensoren als HART-Variable zur Verfügung. Daher erhält das Team im Betrieb auf den Monitoren zwei Angaben: Zum einen wird der Füllstand des Behälters angezeigt. Dieser Wert wird dann direkt für die Steuerung der Drehzahl der Rührwerke verwendet. Zum anderen erhalten die Mitarbeiter eine Prozentangabe, die ein Grad für die Beurteilung der Messsicherheit ist. Bei übermäßiger Schaum- und Staubbildung oder ungewöhnlichen Ablagerungen sinkt die Prozentangabe und das Team kann Gegenmaßnahmen, etwa eine Reinigung oder die Zugabe eines Entschäumers, einleiten. Alle Messwerte werden im Leitsystem Aprol zur Prozessteuerung eingelesen. Niedrige Messsicherheiten führen ebenfalls zu automatischen Abschaltungen oder Anpassungen der Maschinenbetriebsparameter, begleitet von Alarmen für das Betriebspersonal. So ist es nicht mehr zwingend notwendig, die Anlagen ständig im Auge zu behalten. Sie melden sich bei Problemen mit dem Füllstand von alleine.
„Mit den Sensoren von Vega ist es uns erstmals gelungen, den Füllstand bei allen Betriebszuständen zu ermitteln. Wir können im Prozess viel dichter an die Prozessgrenzen fahren und am Ende den Füllgrad in den Apparaten erhöhen, was zum wirtschaftlicheren Betrieb der Produktion führt“, fasst Schätzle den Einsatz der Sensoren zusammen.
Mittlerweile misst der Vegapuls 64 nicht nur sicher den Füllstand, sondern er wird auch zur Erkennung der Schaumbildung herangezogen. Wenn z. B. schäumende Stoffe eingefüllt werden, wird das Nutzsignal des Füllguts auf die gleiche Größe wie das Störsignal des Rührflügels gedämpft. Schätzle dazu: „Wir wollen die gemessene Signalstärke als Indikator verwenden, um ungewünschte Schaumbildung in der Rezepturoptimierung zu reduzieren. Dazu binden wir die Geräte im Sinne der Namur Open Architecture über einen LPWAN-Kanal über Aprol in unsere Process Data Aquisition Datenbank ein.“