Pharmaindustrie: RABS und Isolatoren erhöhen Produktivität
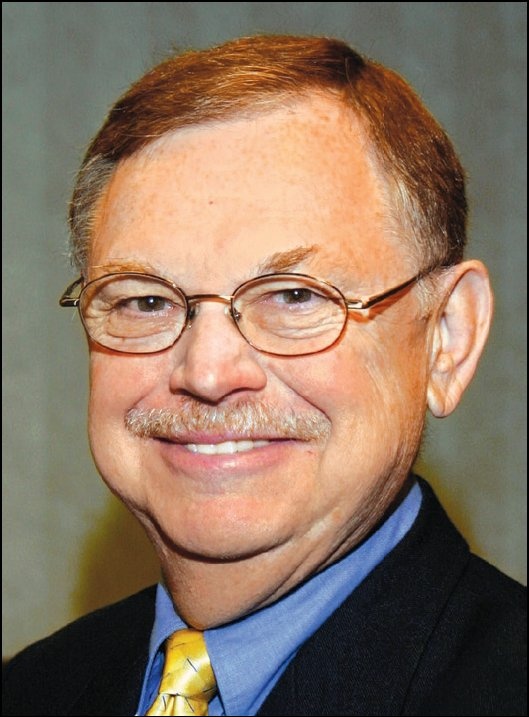
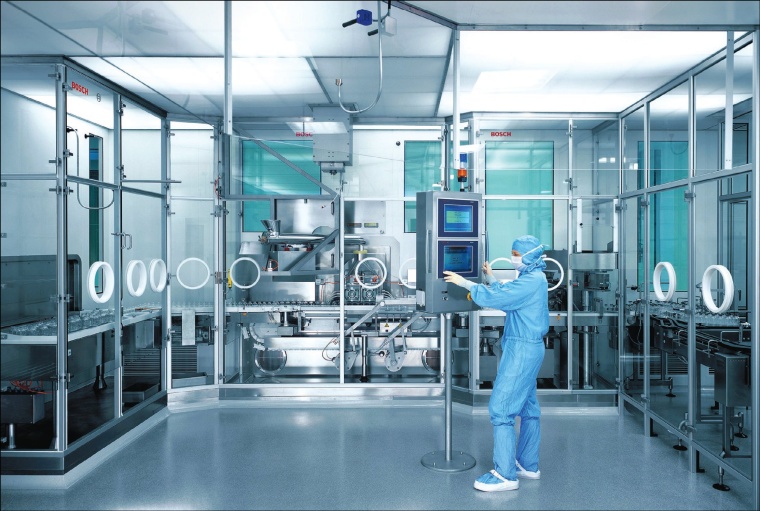
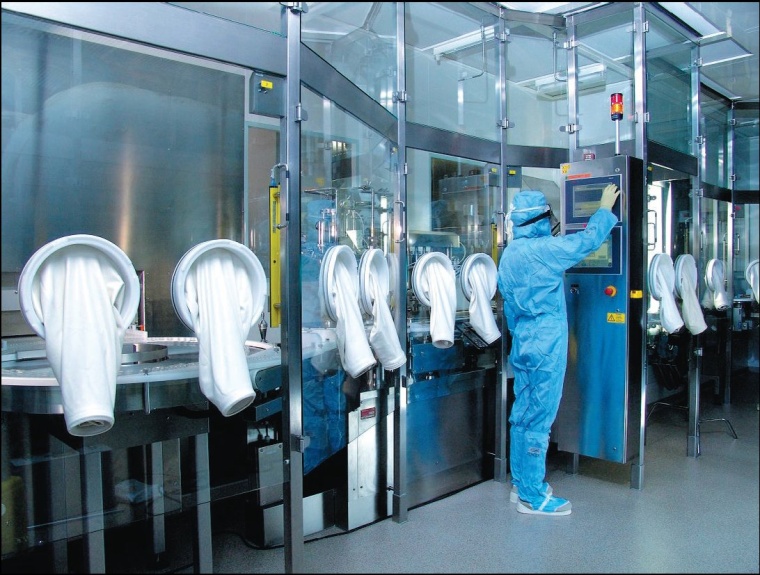
Pharmaindustrie: RABS und Isolatoren erhöhen Produktivität
In der Pharmaindustrie werden zunehmend hochwertige Pharmazeutika mit geringerem Produktionsvolumen hergestellt – Massenfertigungssysteme, die Millionen von Dosierungen ausstoßen, sind rückläufig. Damit stellt sich bei den Abfüll- und Verpackungsprozessen die Frage, ob die bislang dafür eingesetzten, großen ISO 5-Reinraumbetriebe unter diesen veränderten Bedingungen kosteneffektiv sein können. Oder ob es künftig besser ist, kompaktere und flexiblere Fertigungslinien einzusetzen, die reinraumtechnisch gesehen mit Restricted Access Barriers Systems (RABS ) und Isolatoren ausgestattet sind. CHEManager befragte dazu Jack Lysfjord, Vice President of Consulting bei Valicare, einem Dienstleistungsunternehmen im Bereich Qualifizierung und Validierung mit Standorten in Frankfurt/Main sowie in Philadephia und Minneapolis/USA . Das Unternehmen gehört zur Bosch-Gruppe.
CHEManager: Herr Lysfjord, könnten Sie bitte die RABSTechnologie und Isolatoren kurz skizzieren?
Jack Lysfjord: Im Großen und Ganzen ist die Barrier-Technologie darauf ausgerichtet, die Verwendung von Reinräumen bei bestimmten pharmazeutischen Abfüll- und Verpackungsprozessen, also Ampullen, Zylinderampullen und vorgefüllte Spritzen, überflüssig zu machen. Das Ziel von Isolatoren und RABS ist es, diese Produkte von Menschen fernzuhalten, so dass Pharmazeutika nicht mit wachstumsfähigen Organismen oder Partikel in Kontakt kommen.
Darüber hinaus schützen diese Systeme auch das Bedienpersonal beim Umgang mit hochwirksamen Präparaten. Isolatoren sind abgeschlossene, unter positivem Druck stehende Einheiten mit Feinstaubfilterung (HEPA-Filtern), die den ISO Klasse-5-Innenbereich mit einem unidirektionalen Luftstrom versorgen. Im Umluftbetrieb wird die Luft über abgedichtete Rohrleitungen zur Verteileranlage zurückgeführt. Die Biodekontamination erfolgt durch einen automatisierten Prozess unter Verwendung von gasförmigem Wasserstoffperoxid. Zugriff zum Isolator erfolgt nur über integrierte Handschuhe und sterile Transfersysteme; da die Isolatoren abgedichtet sind, eignen sie sich für die Aufstellung in einem ISO Klasse-8-Bereich.
RABS enthalten ebenfalls einen ISO Klasse-5-Bereich mit verschiedenen Abstufungen der Barriere zum Umgebungsraum (generell ISO Klasse 7 oder besser). Biodekontamination erfolgt in einem RABS manuell. Die Türen lassen sich öffnen, was jedoch nur ausnahmsweise geschieht; danach ist eine angemessene Reinigung des Systems sowie die entsprechende „Line Clearance“ notwendig.
CHEManager: Was sind die Hauptunterschiede zwischen RABS und Isolatoren?
Jack Lysfjord: Es gibt eine Reihe grundlegender Unterschiede zwischen den beiden Techniken. Verglichen mit Isolatoren ermöglichen RABS schnellere Start- und Umrüstzeiten. Trotz bestimmter Beschränkungen bieten sie verbesserte Betriebsflexibilität und verringern Kosten für Validierung und Revalidierung. Das Lüftungskonzept eines RABS ist ähnlich aufgebaut wie bei LFHs (Laminar Flow Hoods): Sie werden über Gebläse und HEPA Filter mit reiner Luft versorgt. Die Luft strömt aus der Barriere in den Umgebungsraum.
Die Anforderungen für die Luftaufbereitung bei Isolatoren sind komplizierter, da es sich um ein Umluftsystem mit zusätzlichen Lüftern und Rückluftkanälen handelt. Zudem muss die Luftaufbereitungseinheit leckdicht sein, um einen positiven Druck aufrechtzuerhalten. Es gibt ebenfalls Unterschiede bei Biodekontaminations- und Reinigungssystemen. Bei Isolatoren geschieht die Biodekontamination durch automatisierte Injektoren von gasförmigem Wasserstoffperoxid.
RABS jedoch verfügen über keinen automatisierten Biodekontaminationszyklus und die Reinigung erfolgt manuell durch Absprühen und Wischen. Die Validierung der manuellen RABS-Reinigung ist somit schwieriger als bei dem automatisierten Zyklus eines Isolatorsystems. Ein Umgebungsmonitoring ist erforderlich, um sicherzustellen, dass beide Systeme über einen ISO Klasse-5-Bereich verfügen.
Bei Isolatorsystemen ist eine solche Überwachung nur durch integrierte Sampling Ports oder sterilen Transfer von Monitoringsystemen möglich. Die Erfordernisse für das Umgebungsmonitoring sind daher beim Entwurf eines Isolatorsystems entscheidend. Bei RABS sind diese Verfahren ebenfalls möglich, jedoch besteht hier auch die Option, portable Monitoringsysteme durch die in Tischhöhe befindlichen Öffnungen einzufügen.
CHEManager: Welche Rolle spielen RABS bzw. Isolatoren bei den aktuellen Trends im Pharmasektor?
Jack Lysfjord: In der pharmazeutischen Industrie gibt es eine Reihe von Trends, die RABS und Isolatoren generell zu entscheidenden Komponenten für erfolgreiche Verpackungs- und Verarbeitungssysteme machen. Biotechnologie ist ein entscheidender Faktor bei den sich verändernden Verarbeitungstechniken von Pharmaunternehmen. Lebendimpfstoffe, große Moleküle und Medikamente auf Proteinbasis gewinnen an Bedeutung und erfordern hochsterile Bedingungen.
Toxische, zytotoxische und andere hochwirksame Präparate – ein typisches Beispiel sind immunsuppressive Krebsmedikamente – erfordern ebenfalls strikte Barrier-Technologie zum Schutz des Bedienpersonals. Generell besteht eine Tendenz in Richtung hochwertiger Pharmazeutika mit geringerem Produktionsvolumen. Die Herstellung mit Massenfertigungssystemen, die Millionen von Dosierungen ausstoßen, ist rückläufig. Langfristig muss die Frage nach der Kosteneffizienz für den Bau großer ISO 5 Reinraumbetriebe gestellt werden.
Kleinere Systeme, die den rechtlichen Rahmenbedingungen entsprechen und auf kleineren Produktausstoß umrüstbar sind, werden zunehmend attraktiver. Kompaktere, anpassungsfähigere Fertigungslinien ermöglichen flexible Konfigurationen und versetzen Hersteller in die Lage, schnell auf neue Markttrends reagieren zu können. RABS und Isolatoren sind ideal für kleinere Produktionseinheiten und flexible Systeme mit geringerer Standfläche. Verglichen mit einer voll entwickelten Reinraumeinheit bieten Barrier-Systeme beträchtliche Kostenersparnisse für Pharmaunternehmen.
Darüber hinaus liegen bei einem Isolatorsystem die Kosten für Arbeitskleidung erheblich niedriger, ganz abgesehen von Einsparungen bei Personal- und Wartungskosten. Isolatorsysteme bieten darüber hinaus verringerte Investitions-, Kapital und Betriebskosten im Vergleich zu herkömmlichen Reinräumen und RABS-Systemen.
CHEManager: Welche gesetzlichen Vorschriften gilt es bei RABS und Isolatoren zu beachten?
Jack Lysfjord: Das entscheidende rechtliche Kriterium bei Barrier- Systemen betrifft die sog. Open-door-Intervention bei RABS. Solche Eingriffe schaffen unerwünschte Variablen für den Betrieb der Einheit und können die aseptische Umgebung beeinträchtigen; sie sollten daher vermieden oder auf ein Mindestmaß beschränkt werden. Falls solche Eingriffe jedoch unvermeidlich sind, müssen entsprechende Maßnahmen zur Sicherung der aseptischen Umgebung ergriffen werden.
Opendoor- Interventionen erregen zwangsläufig die Aufmerksamkeit der Behörden, so dass Verfahrensregeln besonders streng gehandhabt werden müssen. Falls ein solcher Eingriff erforderlich wird, reduziert ein außerhalb des RABS installiertes vertikales, unidirektionales ISO-5 Luftstromsystem das Risiko einer Verletzung der ISO-5- Bedingungen und sichert zudem die aseptische Unversehrtheit des Systems. Jeder Eingriff, der das Öffnen einer Tür des RABS notwendig macht, ist ein schwerwiegender Vorgang und als solcher zu dokumentieren. Verriegelte RABS-Türen erleichtern Bedienung und Dokumentation. Nach einer Open-door- Intervention sind je nach Art des Eingriffs entsprechende Line Clearance sowie Desinfektionsmaßnahmen durchzuführen.
CHEManager: Welche Probleme können bei Einführung von Isolatoren und RABS auftreten?
Jack. Lysfjord: Der „Systemaspekt“ von RABS und Isolatoren wird oft vergessen. Für eine erfolgreiche Einführung dieser Technologien muss das Bedienungspersonal sich auf eine weit gefasste, ganzheitliche Sichtweise des Systems einstellen und dadurch gewährleisten, dass es in das Arbeitsumfeld integriert wird und die erforderliche regelmäßige Wartung und Aufsichtsführung sichergestellt ist. Hierzu zählt auch angemessenes Design der Räumlichkeiten, einschließlich Klimatechnik und Lüftungssysteme.
Die korrekte Entsorgung von Abfällen aus der Biodekontamination, sowohl im Gebäude selbst als auch mit Bezug auf allgemeine Umweltschutzrichtlinien, ist ebenfalls ein entscheidendes Kriterium. Auch sanitäre Einrichtungen und die Energieversorgung müssen berücksichtigt werden. Die Aufsichtspflicht der Geschäftsleitung muss wahrgenommen werden. Korrektes Bekleidungsprocedere, angemessene Schulung in aktuellen Produktionsverfahren, Standard- Arbeitsanweisungen für Eingriffe in das System sowie Dokumentation und Protokollierung müssen eingerichtet, strengstens ausgeführt und dauerhaft angewandt werden. Kontinuierliche Systemüberwachung ist ebenfalls Pflicht.
Ein RABS oder Isolatorsystem sollte nicht lediglich als eigenständiger Teil eines umfassenderen Produktionsprozesses verstanden werden, sondern als voll integriert mit allen anderen Aspekten des Betriebs. Natürlich ist es ein entscheidender Vorteil, wenn die Anlage selbst eine gute Integration aufweist und alle modularen Elemente von einem einzelnen Erstausrüster (OEM) stammen und unter derselben Steuerung arbeiten. Eine ganzheitliche Sicht, die alle diese äußeren Aspekte berücksichtigt, gewährleistet die erfolgreiche Einführung eines RABS oder Isolatorsystems.