Optimierung von Reinräumen

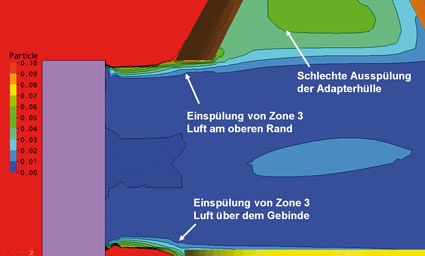
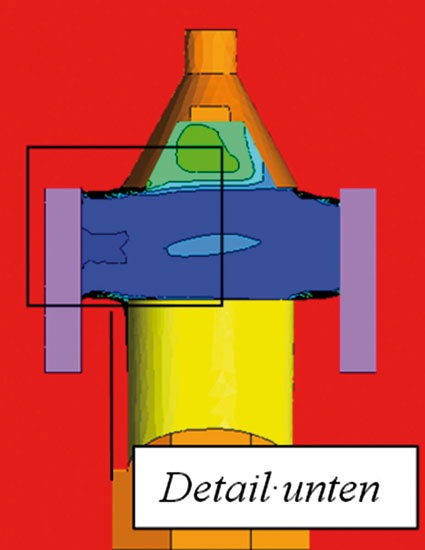

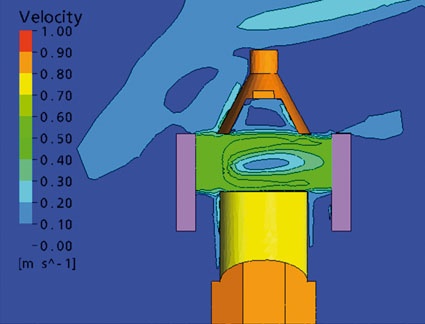
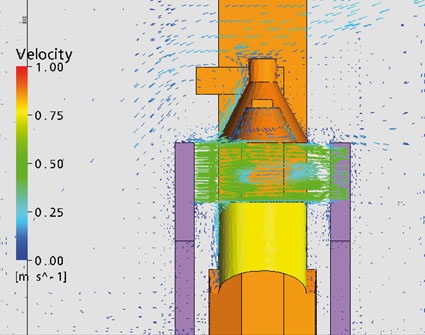
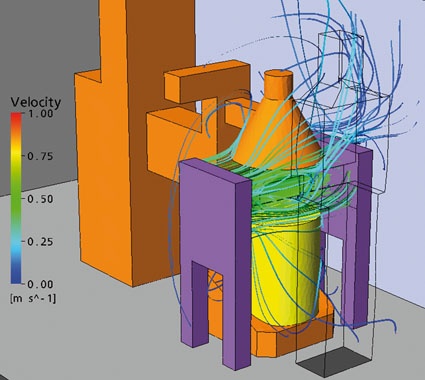
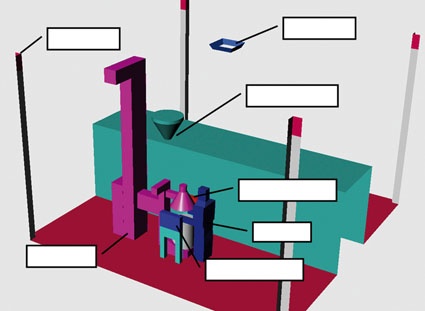
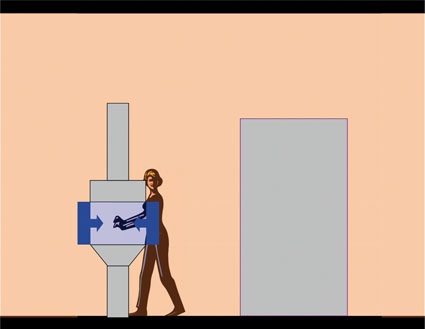
Die Anforderungen an die Reinhaltung und den Produkteschutz steigen zunehmend, ebenso wie der Druck zur Kostensenkung. Im Rahmen der Internationalen Ventilation-Konferenz, die vom 18. bis 21. Oktober 2009 in Zürich statt fand, stellten Forscher, Entwickler und Anwender neue Technologien, Produkte und Trends vor und diskutierten über moderne Lösungsansätze. Als Beispiel wird im Folgenden gezeigt, wie mit Hilfe von Strömungssimulationen nicht nur die Investitionskosten, sondern auch die Betriebskosten einer Blisterverpackungsmaschine markant gesenkt werden konnten.
Immer mehr Produkte bedingen Fabrikations- und Verpackungsstätten, die den diversen Reinraumanforderungen genügen. In der Regel werden deswegen ganze Räume unter Reinraumbedingungen betrieben. Der technische Aufwand hierfür schlägt sich entsprechend in sehr hohen Investitions- und Unterhaltskosten nieder. Die Suche nach kostengünstigen Alternativen, bei denen nur die relevanten Bereiche unter Reinraumbedingungen betrieben werden, führt in der Evaluation und Planung über eine genaue Analyse und Simulation der Luftströme in diesen sensiblen Bereichen. Hier greifen die Techniken von AFC Air Flow Consulting, ein Engineering-Unternehmen mit Sitz in Zürich, das sich auf die Analyse und Simulation strömungstechnischer Probleme spezialisiert hat.
Fallbeispiel: Neue Medikamenten-Verpackungslinie
Im Rahmen der Modernisierung des Produktionsstandortes plante ein Pharmahersteller in der Schweiz die Installation neuer Blisterverpackungsmaschinen. Die Bedarfsanalysen zeigten die Notwendigkeit von vier neuen Einheiten. Die vorhandene Bausubstanz sollte optimal genutzt werden. Das Projekt war Teil eines globalen Konzeptes, in dem Synergieeffekte möglichst optimal genutzt werden sollen. Weiter war zu beachten, dass bei der Beladung der Linien mit dem Ausgangsmaterial (Tabletten) aus Fässern oder Dosen, d. h. im Primärbereich der Produkteschutz der Zone 2 gewährleistet ist, während im Sekundärbereich keine speziellen Reinraumbedingungen zu beachten waren.
Zwei Varianten standen zur Diskussion:
- Der gesamte Primärbereich der Verpackungslinie und der Produktbeladung erfüllt den Produktschutz der Zone 2: Partikel < 100'000/m3; Temperatur 22 ±6 °C.
- Nur in den Bereichen innerhalb der Verpackungslinie und der Produktbeladung, wo das Produkt offen ist, ist Reinluft der Zone 2 zu gewährleisten.
Die Installations- und Betriebskosten bzw. der Energiebedarf wurden für beide Varianten berechnet (Tabelle 1). Damit die beutend günstigere Variante 2 ohne erhebliches Planungsrisiko realisiert werden konnte, entschloss man sich, das Konzept mit Hilfe von Simulationen zu überprüften. Der Pharmahersteller gelangte an AFC Air Flow Consulting mit dem Auftrag:
- Bewertung der untersuchten Konzepte und Varianten auf die Wirksamkeit zum Schutz der Produkte
- Bewertung verschiedener Optimierungsmassnahmen wie Design- und Betriebsparameter (Zu- und Abluftpositionen, Luftführung, Grösse, Luftmengen)
- Minimierung der benötigten Luftmenge
- Minimierung des Risikos von Fehlentwicklungen, Über- oder Unterdimensionierung
- Nachweis, dass die Variante 2 die geforderten Spezifikationen erfüllen kann.
Optimierung und Bewertung mit Hilfe von Strömungssimulationen
Für die Durchführung der Strömungssimulationen muss zuerst ein detailliertes dreidimensionales Modell der gesamten Anlage sowie der umgebenden Räume erstellt werden.
In den nächsten Schritten werden mit verschiedenen möglichen Szenarien der Luftströmung (seitliche Zu- und Abluft; Zuluft via Trichter oder separater Laminar Flow Einlass) berechnet, wobei auch die Randbedingungen variiert werden. Die Ergebnisse werden in anschaulichen, dreidimensionalen Abbildungen dargestellt, wie z. B. Stromliniendarstellung, Vektorbilder, repräsentative Schnitte. Als Beispiel aus der Vielzahl von Ergebnissen werden im Folgenden jene der Luftströmung und der Luftqualität rund um die Beladestation vorgestellt. Die Abbildung 3a zeigt die Luftströmung, die seitlich der Abfüllstation eingeblasen wird und so im eigentlichen Abfüllraum für optimale Luftqualität sorgt und das Eindringen der Umgebungsluft verhindert. Die Luftgeschwindigkeiten sind in Farben dargestellt, wobei blau 0 bis 0.3 m/s, grün ca. 0.5 m/s und rot > 0.8 m/s bedeutet. In Abbildung. 3b ist die Luftströmung in Form von Vektoren dargestellt. Abbildung 3c stellt das Strömungsfeld dar.
Eine zentrale Aussage ist die Anzahl der Partikel und ihre Verteilung im Raum. Die Strömungssimulation zeigt, dass die Luftqualität zwischen den beiden seitlichen Zuluftöffnungen und der trichterförmigen Abluftöffnung, d. h. im eigentlichen Abfüllort, nur 0 bis 10 % der Partikelkonzentration der Zone 2 Luft aufweisen. Die Zahl der Partikel in der Umgebungsluft ist als 100 % angenommen (Abb. 4a). Die Detailaufnahme (Abb. 4c) zeigt, dass diese Lösung noch nicht optimal ist und verschiedene Schwachstellen aufweist, wie schlechte Ausspülung in der Adapterhaube oder Einspülung von Luft aus der Zone 3.
In weiteren Optimierungsschritten wurden diese Schwachstellen behoben. Die seitlichen Lufteinlässe wurden vergrößert, mit dem Resultat, dass nun keine Einmischung von Luft aus der Zone 3 möglich ist.
Überprüfung der Anlage
Nach Abschluss der CFD Optimierung wurde die Konstruktion der Zu- und Ablufteinheiten nach Variante 2 umgesetzt. Nach Fertigstellung der Anlage wurden die Luftströmungen mit künstlichem Rauch überprüft. Diese Tests bestätigten die Simulationsergebnisse. Der Pharmahersteller ließ die Anlage durch eine Zertifizierungsfirma abnehmen. Die spezifizierten Sollwerte wurden bestens erreicht bzw. die zulässige Partikelzahl deutlich unterschritten. Aufgrund der guten Resultate wurde die Anlage als „Zertifizierte Lösung" erfolgreich abgenommen.
Markante Einsparungen
dank Simulationen
Aufgrund der Strömungssimulationen und Berechnungen konnte die Anlage optimiert und markant Installations- und Betriebskosten gesenkt werden: Der gezielte Produktschutz innerhalb der Verpackungslinie und der Produktbeladung (Variante 2) ist wesentlich günstiger als Variante 1. Die Investitionskosten der Anlage sind rund viermal geringer und die Betriebskosten konnten halbiert werden. Der Energiebedarf ist zudem 15-mal kleiner als bei Variante 1. Die Kosten für die Simulationen betrugen rund CHF 20.000. Aufgrund dieser Investition konnten allein bei der Installation der Anlage CHF 140.000.- pro Linie eingespart werden.
Die Kostenreduktionen betragen im vorliegenden Beispiel:
- Reduktion der Installationskosten um 70 %
- Reduktion der Betriebskosten um 50 %
- Reduktion der Energiekosten um 90 %.
Zudem konnten die Resultate innerhalb des Pharmakonzerns weltweit verwendet werden und werden zu weiteren Einsparungen beitragen.
Schlussfolgerung
Dieses Beispiel zeigt eindrücklich, dass mit Strömungssimulationen die strengen Anforderungen von Reinhaltung und Produktschutz nicht nur optimiert, sondern auch die Kosten erheblich gesenkt werden können.
Simulationen sind ein ausgezeichnetes Mittel, um die Massnahmen zu optimieren und auf Ihre Wirksamkeit hin zu überprüfen. Sie erhöhen deutlich die Planungssicherheit und führen zu markanten Energie- und Kosteneinsparungen.