Mächtiges Potenzial für die Prozessindustrie
Der umfassende digitale Zwilling für die chemische Industrie verbindet die digitale und die reale Welt und ermöglicht es, fundierte datenbasierte Entscheidungen zu treffen
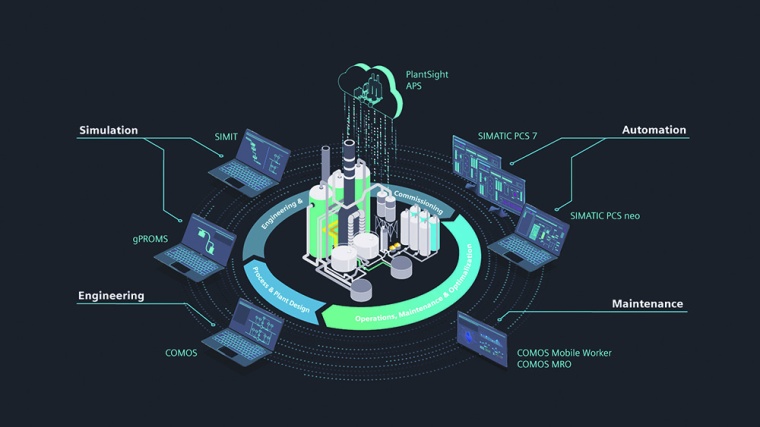
Die dynamischen Märkte von heute konfrontieren die Chemieindustrie mit Kostendruck, unterbrochenen Lieferketten, der Forderung nach schnellerer Markteinführung, der Realisierung von Mehrzweckanlagen oder der Notwendigkeit, den CO2-Fußabdruck zu reduzieren und zu dokumentieren. Gleichzeitig müssen alle Anwendungen in einer verfahrenstechnischen Anlage den neuesten Sicherheitsanforderungen und Vorschriften entsprechen. Um sich diesen Herausforderungen erfolgreich zu stellen, sind Digitalisierung, Daten und Software der größte Hebel – vor allem in Form des digitalen Zwillings.
Dieser Ansatz verbindet die digitale und die reale Welt und ermöglicht es, über den gesamten Lebenszyklus von Anlagen, Prozessen und Produktion sowie über alle Funktionen und Ebenen hinweg fundierte datenbasierte Entscheidungen zu treffen. Die Idee dahinter existiert seit einiger Zeit, aber mit den rasant wachsenden Möglichkeiten der Digitalisierung und vor allem in Kombination mit künstlicher Intelligenz birgt der digitale Zwilling ein mächtiges Potenzial für die gesamte Prozessindustrie.
Digitaler Zwilling aus einem Fluss
Der digitale Zwilling ist gleichermaßen für Greenfield- und Brownfield-Anwendungen geeignet. Entscheidend ist, dass je nach Phase eines Anlagenlebenszyklus die richtige und vor allem interoperable Software zum Einsatz kommt – von Prozessdesign über Anlagen-Engineering, Inbetriebnahme, Schulung, Betrieb und Instandhaltung. Für Greenfield-Anlagen beginnt der Designprozess mit Simulationen über Prozessmodellierungssoftware wie gProms von Siemens, um optimale Prozessdesigns für eine Anlage zu ermitteln. gProms erfasst tiefes Prozesswissen in mathematischen Modellen, die die Physik und Chemie der Prozessabläufe beschreiben. Diese Daten werden dann verwendet, um bspw. Prozessflussdiagramme (PFD) zu erstellen, die dann im weiteren Planungsverlauf zu detaillierten Rohrleitungs- und Instrumentendiagrammen (P&IDs) weiterentwickelt werden, die die Prozesse und die Ausrüstung einer Anlage detailliert beschreiben. P&IDs stellen Elemente wie Behälter, Rohre und Ventile dar und zeigen, wie Prozesse mithilfe von Automatisierungselementen wie Sensoren und Aktoren gesteuert werden.
Für die verschiedenen Disziplinen des Anlagenbaus, etwa Verfahrenstechnik, Elektrotechnik, Systemtechnik, Verrohrung und Automatisierung, hilft ein Engineering-Tool wie Comos, den digitalen Zwilling zu erstellen. Anschließend muss die Hard- und Software des Prozessleitsystems (DCS) eingerichtet und konfiguriert werden. Der Plant Automation Accelerator von Siemens bietet hierfür einen integrierten Engineering-Ansatz. Nach dem DCS-Engineering beginnt die kritische Phase der Abnahmeprüfung und Inbetriebnahme. Mit der Software Simit lässt sich das DCS-Verhalten für die virtuelle Inbetriebnahme simulieren, während sich die reale Anlage noch im Bau befindet. Durch die Wiederverwendung der Daten aus dem Prozessleitsystem, Simit, Comos und gProms kann das komplette Anlagenverhalten vor der Inbetriebnahme simuliert werden. Liegt zudem ein 3D-Modell einer Anlage vor, ermöglicht Comos Walkinside eine frühzeitige Schulung des Bedienpersonals per virtueller Realität. Dies reduziert den Inbetriebnahmeaufwand, minimiert Fehler, senkt die Projektkosten und beschleunigt die Inbetriebnahme.
Digitaler Zwilling für Bestandsanlagen
Im Fall von Bestandsanlagen profitieren Betreiber von einem digitalen Zwilling in der Betriebsphase. Die meisten Daten von Altanlagen werden in voneinander unabhängigen Anwendungen verschiedener Anbieter in Form von Engineering-Systemen, Prozessleitsystemen, Manufacturing-Execution- oder Asset-Management-Systemen gespeichert und verwaltet. Zudem ist ein großer Teil der technischen Anlagendokumentation und -daten oft nur in Papierform vorhanden. Eine solche fragmentierte und heterogene Systemlandschaft führt zu Datensilos mit geringer Datenqualität und geringer Datenkonsistenz, was datenbasierte Entscheidungen erschwert.
Die Software PlantSight bietet hierfür ein cloudbasiertes Portal, das unter Einbindung der Operations Intelligence Software XHQ Daten aus verschiedenen Quellen konsolidiert und mit Echtzeit-Anlageninformationen verknüpft. So wird sichergestellt, dass Daten aus allen Systemen übersichtlich und effizient visualisiert werden. Im Anschluss kann ein digitaler Zwilling von Prozessen und Produktion einer Brownfield-Anlage erstellt werden.
Entscheidend für den Aufbau und durchgehende Instandhaltung eines digitalen Zwillings ist letztlich eine Standardisierung von Daten für eine nahtlose Interoperabilität verschiedener Systeme. Viele Anlagen setzen auf separate Systeme für Engineering, Automatisierung und Simulation, was den Datenaustausch erschwert. Die Kombination von Anwendungen wie Comos, gProms, Simit und dem DCS-System hingegen sorgt für konsistente Datenaktualisierungen und optimiert die Produktivität und Leistung einer Anlage. Mit dem Prozessleitsystem Simatic PCS neo hat Siemens mit dem Module Type Package (MTP) einen Standard zur Beschreibung der Eigenschaften von Anlagenmodulen eingeführt. Dies sorgt für einen konsistenten Informationsfluss, weniger Fehler, schnelleres Engineering und einen flexiblen Anlagenbetrieb.
„Der digitale Zwilling ermöglicht es, über alle Funktionen und Ebenen hinweg fundierte datenbasierte Entscheidungen zu treffen.“
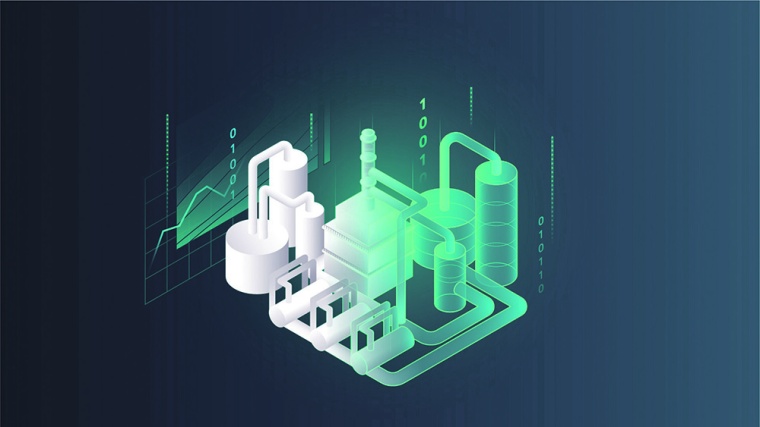
Beispiel aus der Spezialchemie
Siemens hat eine Digital-Twin-Anwendung zur Optimierung von Batch-Produktionsprozessen speziell in der Farben- und Lackindustrie erstellt. Der digitale Zwilling umfasst hierfür die Bereiche digitales Prozessdesign und Anlagenbau, digitale Rezeptur- und Prozessentwicklung und -simulation sowie den digitalen Prozess- und Anlagenbetrieb. Das Template für dieses Projekt hebt verschiedene Merkmale und Funktionalitäten der Digital-Twin-Implementierung für die Batch-Produktion hervor. Dazu zählen die Rezeptverwaltung, die eine effiziente Anpassung und Skalierung von Produkten ermöglicht, und die Prozesssimulationen, die das virtuelle Testen des gesamten Produktionsprozesses erlauben. Die batch-basierte Automatisierung folgt der S-88-Philosophie für die chargenorientierte Fahrweise (Batch Control) und gewährleistet eine flexible Produktion. Der digitale Zwilling überwacht kontinuierlich den Produktionsprozess, indem er Daten von verschiedenen Sensoren und Geräten sammelt. Diese Echtzeitüberwachung ermöglicht es dem Bedienpersonal, kritische Prozessparameter genau zu beobachten, Abweichungen zu erkennen und sofortige Korrekturmaßnahmen zu ergreifen, um eine gleichbleibende Produktqualität zu gewährleisten. Die MES-Funktionalität stellt darüber hinaus sicher, dass wichtige Prozess- und Produktionsinformationen in Echtzeit verfügbar sind. Schließlich wird durch die Integration mit ERP-Systemen ein reibungsloser Datenaustausch zwischen der Produktion und den Geschäftssystemen sichergestellt.
Diese Eigenschaften führen zu einer gesteigerten Effizienz und mehr Nachhaltigkeit, da der Produktionsprozess optimiert und der Energieverbrauch gesenkt wird. Obwohl dieses Konzept des digitalen Zwillings ursprünglich für wasserbasierte Farben entwickelt wurde, kann es auch auf andere Spezialchemikalien übertragen werden. Das unterstreicht noch einmal, welches Potenzial diese Technologie hat, um die Chemiebranche zu revolutionieren.
„Ein großer Teil der technischen Anlagendokumentation und -daten ist oft nur in Papierform vorhanden.“
Wie starten?
Der Aufbau eines digitalen Zwillings kann eine komplexe Aufgabe sein. Chemieunternehmen sehen sich in der Regel mit zwei Szenarien konfrontiert:
- Keine definierte Digital-Twin-Strategie: Für diesen Fall bietet Siemens eine Schritt-für-Schritt-Beratung, um den Digitalisierungsprozess zu skizzieren, einschließlich einer Fünf-Jahres-Roadmap mit Projekten, technischen Spezifikationen und Investitionsplänen. Diese Roadmap steht letztlich im Einklang mit der Strategie des Unternehmens und den bestehenden IT- und OT-Systemen. Ziel ist es, die beste Technologie mit minimaler Unterbrechung für Betrieb und Personal zu integrieren.
- Digital-Twin-Strategie in der Umsetzung: Nach ersten Erfolgen müssen Unternehmen die Dynamik beibehalten und die nächsten Schritte priorisieren. Siemens bietet modulare Lösungen, die auf den digitalen Reifegrad und die Strategie des Unternehmens zugeschnitten sind. Der digitale Zwilling ist demnach eine sich ständig weiterentwickelnde Einheit. Die modularen Dienstleistungen von Siemens können spezifische technische Bereiche wie Cybersecurity oder breitere Themen wie Datenmanagement abdecken.
Ausblick
Die digitale Transformation verändert die Chemieindustrie bereits heute enorm. Insbesondere die steigenden Energiekosten und der Druck auf Unternehmen, CO2-neutral zu produzieren, sind wesentliche Treiber dieses Wandels. Digitale-Zwilling-Anwendungen werden Unternehmen helfen, ihre Energiekosten deutlich zu senken und den Überblick über die CO2-Emissionen in der Produktion zu behalten. Viele Aufgaben werden von künstlicher Intelligenz übernommen und von der realen Anlage in die virtuelle Umgebung verlagert werden: Testen alternativer Anlagen- und Maschinenkonfigurationen, die Vorhersage von Wartungsintervallen oder die Unterstützung produktionsbezogener Entscheidungen.
Mit der Nutzung und dem Angebot von immer mehr digitalen Geschäftsmodellen werden Wertschöpfungsketten unternehmensübergreifend viel enger miteinander verknüpft sein. Langfristig ist der digitale Zwilling die Grundlage für die globale Zusammenarbeit in strategischen Partnerschaften und Ökosystemen; er wird die Barrieren zwischen verschiedenen Domänen weiter einreißen.
Autor: Bart Moors, General Manager Process Industries Software, Siemens AG
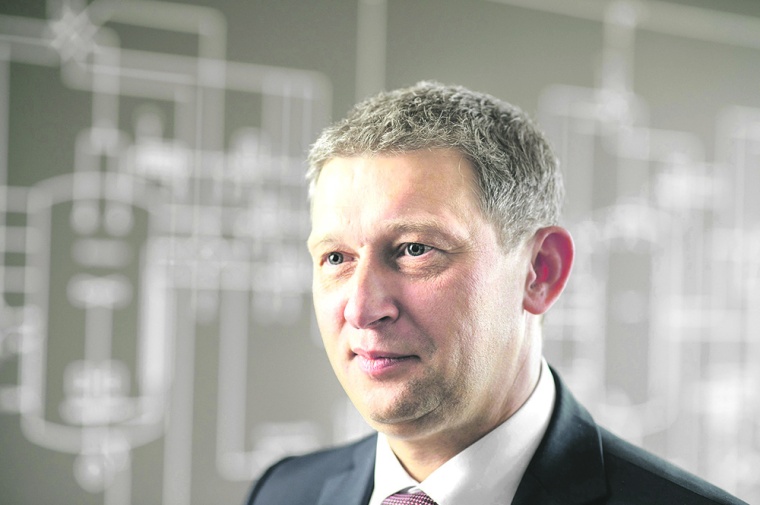
„Mit digitalen Geschäftsmodellen werden Wertschöpfungsketten unternehmensübergreifend miteinander verknüpft.“