KSB: Pumpen senken Energiekosten
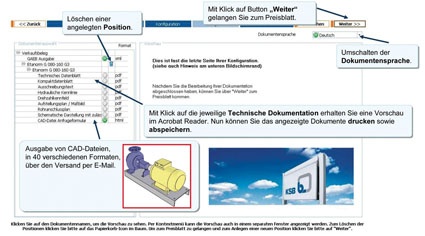
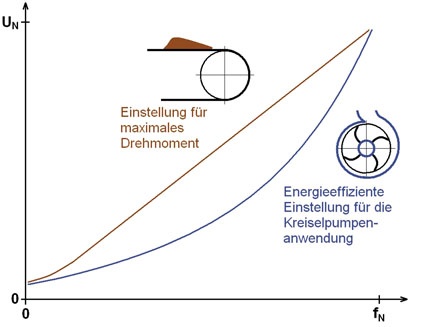
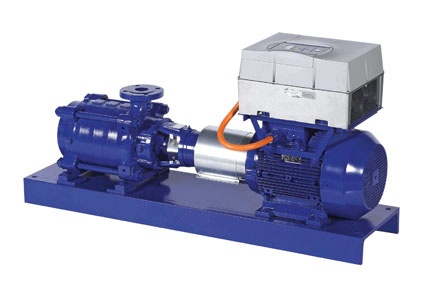
Vor dem Hintergrund steigender Energiepreise und der zwingenden Notwendigkeit einer Reduzierung des CO2-Ausstoßes gewinnt die Betrachtung des Stromverbrauches von Pumpensystemen an Bedeutung. Die Aktivitäten der Deutschen Energieagentur (dena) und des VDMA tragen erste Früchte: Der Fokus zahlreicher Anwender liegt heute auf der Senkung der Energiekosten.
Die dena hat ein Einsparpotenzial bei Pumpensystemen in Deutschland von 14 Milliarden kWh pro Jahr errechnet. Daraus ergibt sich für die Betreiber eine jährliche Kosteneinsparung von 1,12 Milliarden Euro und eine Reduzierung des CO2-Ausstoßes um 7,7 Millionen Tonnen. Eine europaweite Studie geht davon aus, dass durch besser ausgelegte Anlagen eine Einsparung von rund zehn Prozent der eingesetzten Energie möglich wäre. Der Einsatz von Pumpen sowie Motoren mit höherem Wirkungsgrad schlägt mit rund drei Prozent zu Buche.
Es gibt jedoch keine für alle Anwendungen gleichermaßen passende Lösung, um das wirtschaftliche Potenzial einer Anlage auszuschöpfen. Grundsätzlich gibt es vier verschiedene technische Möglichkeiten, um den Energiebedarf von Pumpensystemen zu mindern. Pumpenhersteller können durch die Bereitstellung von Auslegungssystemen, Anpassung der Laufraddurchmesser, dem Einsatz von drehzahlgeregelten Aggregaten und Sparmotoren zur Senkung des Stromverbrauchs beitragen.
Die hydraulische Optimierung einer geplanten Anlage beginnt mit der richtigen Auslegung der Pumpe, um einen häufig auftretenden Fehler - das Überdimensionieren - zu vermeiden. Hierbei sind Pumpenauslegungsprogramme von großer Bedeutung. Der Anwender erhält mit ihnen Zugriff auf Experten- Know-how. Er kann damit ein Pumpensystem unter kaufmännischen sowie technischen Parametern auslegen und auswählen. Spezielle EDV-Tools aus der Praxis helfen ihm, auch Details zu beachten. Der Planer kann beispielsweise mit einem Baustein sein Rohrleitungsnetzwerk kalkulieren. Kriterien wie Preis und Wirkungsgrad werden genauso berücksichtigt wie Energiekosten.
Laufraddurchmesser auf den Betriebspunkt auslegen
Eine Pumpe mit einem auf den Betriebspunkt angepassten Laufrad kann im Gegensatz zu einer Pumpe, die aus kommerziellen oder fertigungstechnischen Gründen mit festgelegtem, abgestuften Laufraddurchmesser eingesetzt wird, eine Energieersparnis von mehreren tausend Euro erzielen. An einem realen Beispiel aus der Verfahrenstechnik lässt sich dieses Einsparpotential belegen: Eine Chemienormpumpe fördert Ammoniakwasser mit einer Konzentration von 25 Prozent in einem hydraulisch offenen Kreislauf. Im Normalfall wird eine Fördermenge von 245 Kubikmetern in der Stunde auf einer Förderhöhe von 135 Metern benötigt. Mit einem vollen Laufrad von 324 mm hat die Pumpe eine Wellenleistungsaufnahme von 113,4 kW. Da der maximale benötigte Volumenstrom bei 324 Kubikmetern in der Stunde liegt und die Leistungsaufnahme in diesem Fall 127,9 kW beträgt, ist die Pumpe mit einem 132 kW Motor ausgerüstet.
Bei einem Motorwirkungsgrad von 96,2 Prozent hat der Effizienzklasse-1-Motor bei der Normalfördermenge von 245 Kubikmetern eine Stromaufnahme von 118,1 kW. Legt man 4.000 Betriebsstunden pro Jahr und einen Strompreis von 10 Cent pro Kilowattstunde zugrunde, fallen 47.147 Euro an Stromkosten an. Reduziert man den Laufraddurchmesser um 6 mm auf den exakten Betriebspunkt, liegt die vom Motor zu erbringende Leistung im Normalförderfall nur noch bei 113,1 kW. Aus der Anzahl an Betriebsstunden und den Stromkosten ergibt sich eine Minderung von 19.000 kWh und somit eine Kosteneinsparung von 1.900 Euro pro Jahr.
Leistung dem Bedarf anpassen
Das mit Abstand größte Einsparpotenzial bietet die Drehzahlregelung der Pumpen. Was bei anderen Anwendungen selbstverständlich ist, nämlich die aufgewendete Leistung dem tatsächlichen Bedarf anzupassen, ist in vielen Bereichen der Industrie noch immer kein Standard. In der Praxis stellt sich oft nach genauer Untersuchung des Betriebsverhaltens einer Pumpe heraus, dass sie nicht im optimalen, energiesparenden Betriebspunkt läuft.
Ursache sind häufig Abweichungen vom Auslegungswert durch Überdimensionierung der Anlage oder die normalen prozessbedingten, temporären Schwankungen des realen Strömungswiderstandes einer Anlage. Wird die Fördermenge nicht dem Bedarf durch eine geeignete Regelung angepasst, wird wertvolle Energie vernichtet. Bei geschlossenen Kreisläufen kann man je nach anfallendem Lastprofil bis zu 65 Prozent Energie einsparen. Durch Veränderung der Drehzahl kann die Förderhöhe der Pumpe an den Bedarf der Anlage genau angepasst werden. Die Industrie bietet eine Vielzahl von technischen Möglichkeiten, um über die Drehzahlregelung den Energieverbrauch zu beeinflussen. Toleranzen und Sicherheitszuschläge bei der Dimensionierung der Pumpe können somit entfallen.
Applikationsgerechte Lösungen
Standardumrichter sind universell einsetzbare Geräte mit diversen Einstellmöglichkeiten. Sie sind für Anwendungen nutzbar, bei denen Drehstrommotoren als Antrieb genutzt werden. Es bedarf genauer Kenntnisse über das hydraulische Verhalten von Kreiselpumpen, um solche Geräte auf die Eigenschaften einer Pumpe abzustimmen.
Pumpenhersteller bieten daher spezifische Lösungen mit fertig montierten und betriebsbereiten Drehzahlregelungen an. Bei diesen sind die Parameter und die Begrifflichkeiten im Einstellungsmenü auf diverse Pumpenan¬wendungen abgestimmt. Daher beschränkt sich die Inbetriebnahme auf die Eingabe weniger anwendungsspezifischer Parameter, wie etwa die Eingabe der Reglergeschwindigkeit. Zusätzliche Funktionen ermöglichen einen sparsamen Betrieb und verringern Verschleiß und Ausfallzeiten von Pumpe und Anlage.
Moderne Technik auch für Altanlagen
Beim KSB-System PumpDrive sorgt eine Druckregelung mit förderstromabhängiger Sollwertnachführung für zusätzliche Energieeinsparung bei Teillast. Dieses motormontierte System, bei denen der Frequenzumrichter an jeden beliebigen Elektromotor angebaut werden kann, bietet gegenüber einem fertigen Integralmotor den Vorteil der Nachrüstbarkeit von vorhandenen Anlagen.
Dabei spielen weder der Hersteller des Motors noch seine Effizienzklasse eine Rolle. Dank seiner Schnittstellen lässt sich dieses Gerät in ein Anlagenleitsystem integrieren. Über Busleitungen können außerdem bis zu sechs PumpDrive-Aggregate nach dem Master-Slave-Prinzip ohne zusätzliche Hardware parallel arbeiten. Als Leitmaschine dient eine Pumpe, die den anderen Pumpen den notwendigen Arbeitspunkt vorgibt, den sie zum Erreichen des gemeinsamen Sollwertes benötigen. Die Führungsrolle ist nicht fest einer Pumpe zugeordnet, sodass bei einem Spannungsausfall des Masters eine Slave-Pumpe die Führung übernimmt.
EU forciert Einsatz von Sparmotoren
Der Einsatz von Sparmotoren hat in den letzten Jahren zugenommen und wird von der Europäischen Union stark forciert. Die Gesetzgebung geht hier ähnliche einseitige Wege wie bei den Energiesparlampen. Durch einen höheren Kupfer- und Eisenanteil wird ein geringerer magnetischer Widerstand und dadurch eine größere Effizienz erzeugt. Die Herstellungskosten für einen solchen Motor sind jedoch auf Grund des höheren Rohstoffanteils deutlich höher als bei konventionellen Antrieben. Durch die Verwendung eines EFF1-Motors lässt sich der Energieverbrauch im Durchschnitt um 3,5 Prozent auf den Gesamtwirkungsgrad verbessern. Der Einsatz von Sparmotoren macht aber nur dann wirklich Sinn, wenn man die anderen Sparpotenziale ausgeschöpft hat. Einer Pumpe, die weit ab von ihrem Betriebsoptimum fördert, verhilft auch kein Sparmotor zu einer vernünftigen Energiebilanz. Um den größtmöglichen Einsparungseffekt zu erzeugen, muss man deshalb alle Energieeinsparpotenziale nutzen.