Druckmessung mit der Feder
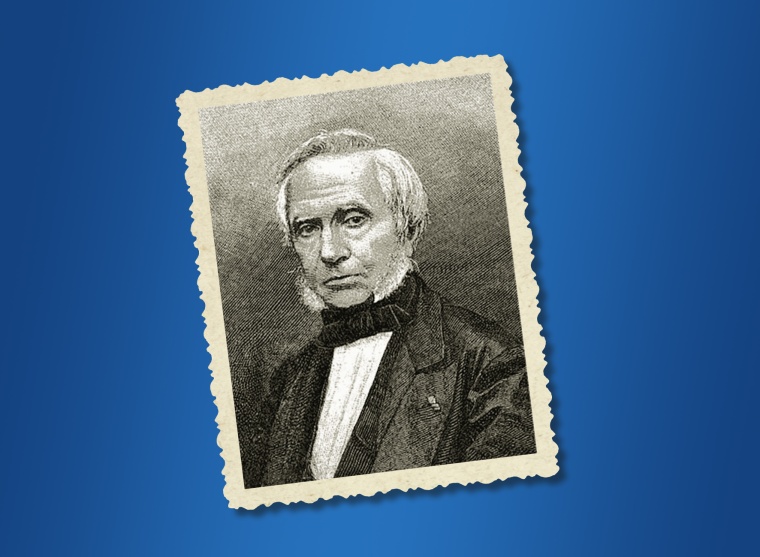
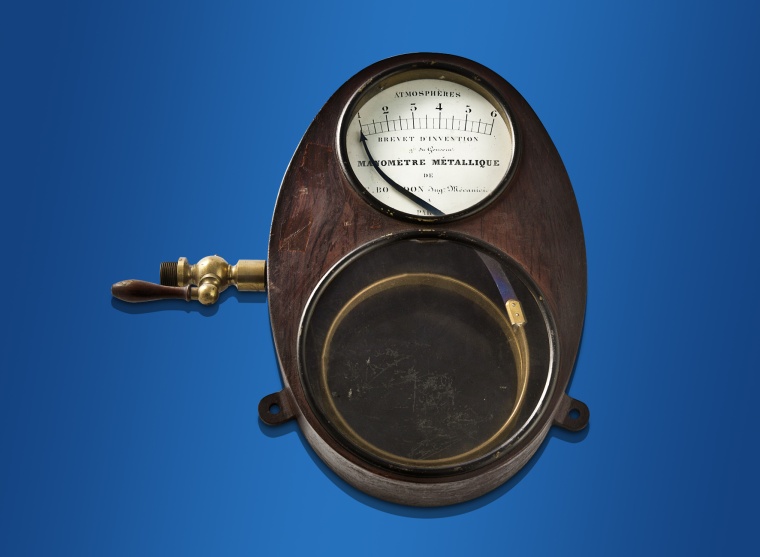
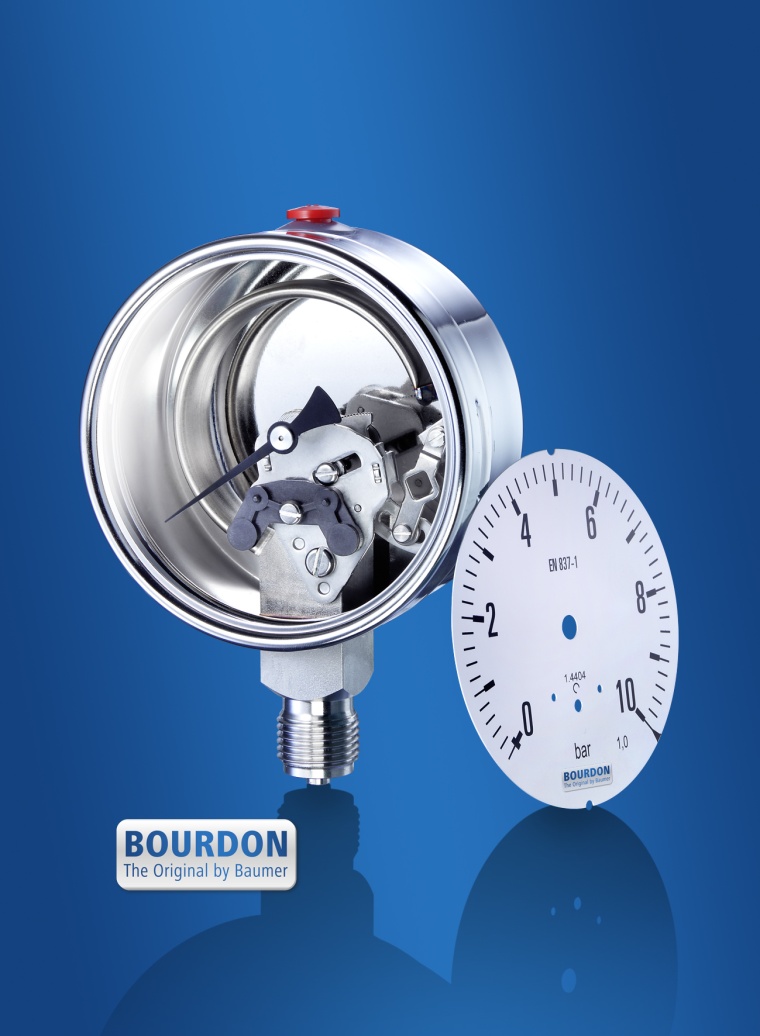
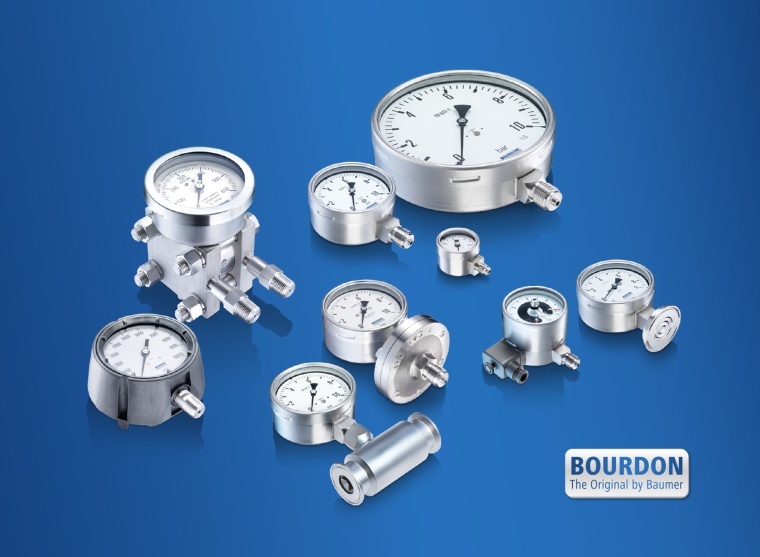
CITplus: Auch im 21. Jahrhundert ist die von Eugène Bourdon im Jahre 1849 zum Patent angemeldete Bourdonfeder die häufigste Methode zur mechanischen Druckmessung.
Baumer Bourdon Haenni ist heute innerhalb der Baumer Gruppe das Kompetenz-Zentrum für mechanische Messinstrumente, wo der Pioniergeist von Eugène Bourdon allgegenwärtig ist. Die Bourdonfeder in den Produkten von Baumer hat dank ihrer vielen Vorteile auch nach mehr als 160 Jahren noch nichts von ihrer Popularität eingebüßt: Beim Bau einer Dampfmaschine fiel Bourdon auf, dass das spiralförmig gewundene Rohr, das zum Verdichten des Dampfes dient, bei der Herstellung flachgedrückt wurde. Um dies zu korrigieren, wurde das Rohr an einem Ende verschlossen und am anderen Ende unter Druck gesetzt. Als Folge daraus begann die Spirale, sich aufzubiegen, während das Rohr danach strebte, seinen runden Querschnitt wiederzuerlangen. Beeindruckt von dieser Beobachtung, führte Bourdon sogleich einige Versuche durch und erfand letztlich einen Druckmesser auf der Basis der Wegänderung des Endes einer gekrümmten Rohrfeder mit elliptischem Querschnitt.
Durch diese Einfachheit sind diese Rohrfeder-Manometer einfach zu handhaben und instandzuhalten. Außerdem sind sie für einen breiten Druckbereich geeignet und bieten ein hohes Maß an Genauigkeit (bis 0,1 % vom Endwert). „Da sie keine externe Stromquelle benötigen, sind sie nicht anfällig für Spannungsschwankungen oder Stromausfälle", erklärt Sascha Engel, Leiter Marketing & Vertrieb Process Instrumentation bei Baumer.
Bewährtes Prinzip wird ergänzt durch moderne Methoden
Baumer setzt bei seinen mechanischen Druckmessern weiterhin auf dieses bewährte Bourdon-Prinzip, ergänzt dies am Produktionsstandort in Vendome (Frankreich) jedoch mit modernsten Produktionsmethoden, die in den anspruchsvollen Anwendungen in der Öl- und Gasindustrie entscheidende Vorteile bieten.
An der Biegemaschine werden aus langen Edelstahlrohren Rohrfedern hergestellt, die je nach Nenngröße des Messgerätes und abhängig vom Messbereich unterschiedliche Abmessungen haben. Die Rohrfedern erhalten die typische C-Form und einen abgeflachten Querschnitt. Die Rohrfedern werden an einem Ende mit dem Anschlussstutzen des Messgerätes und am anderen Ende mit dem Federendstück verschweißt. Die verschweißten Messsysteme werden auf Dichtigkeit geprüft und druckgealtert um Spannungen im Material zu beseitigen. Anschließend werden sie auf einer automatisierten Laserschweißanlage mit dem Manometergehäuse verschweißt.
Das Zeigerwerk wird montiert und das Manometer wird entsprechend Messbereich und Genauigkeitsklasse justiert und geprüft. Dies geschieht nach einem patentierten, halbautomatischen Verfahren, dass Justagefehler nahezu ausschließt. Das Manometer wird fertigmontiert, verschlossen und versandfertig verpackt. Auf Wunsch kann für jedes Manometer ein Kalibrierzertifikat erstellt werden. Dies geschieht auf einem computerbasierten System mit optischer Abtastung der Zeigerposition. Die Zertifikate werden archiviert und können jederzeit dem Messgerät zugeordnet werden.