Digitale Lösungen mit Nachhaltigkeit und Innovation
In der Prozessindustrie hat der digitale Wandel längst begonnen – und wird in Zukunft sogar noch mehr an Fahrt aufnehmen.
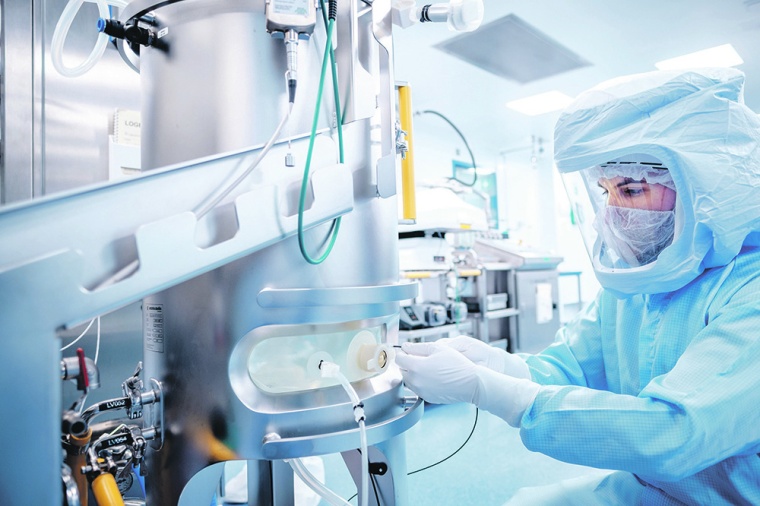
Als der CHEManager vor 30 Jahren zum ersten Mal erschien und gleichzeitig ich meinen Berufsweg bei Siemens begann, waren das „Industrial Internet of Things“ und „Industrie 4.0“ noch lange kein Thema, doch das hat sich in den vergangenen 10 Jahren komplett geändert: In der Prozessindustrie hat der digitale Wandel längst begonnen – und wird in Zukunft sogar noch mehr an Fahrt aufnehmen.
Welches Potenzial in den neuen, digitalen Möglichkeiten steckt, haben die Verantwortlichen in der Chemie- und Pharmaindustrie schnell erkannt: Heute werden Prozesse simuliert, optimiert, schnell skaliert. Vor zwei Jahren wartete die ganze Welt darauf, dass es der Pharmaindustrie gelingen würde, einen Impfstoff gegen das SARS-CoV-2-Virus zu entwickeln – und vor allem schnell in großen Mengen zu produzieren. Und das ist gelungen: Das Mainzer Biotechnologieunternehmen BioNTech hat mit Hilfe von Siemens in Rekordzeit eine bestehende Anlage in Marburg für die Produktion des Covid-19-Impfstoffs umgebaut. Statt einer Projektlaufzeit von etwa einem Jahr dauerte dieses Projekt nur fünf Monate, und wesentliche Bestandteile des neuen Manufacturing Execution Systems (MES) in Verbindung mit dem Prozessleitsystem SimaticC PCS 7 wurden in nur zweieinhalb Monaten umgesetzt. Ohne neue Ideen, einer agilen Zusammenarbeit und den Möglichkeiten, die uns die Digitalisierung an die Hand gegeben hat, wäre das undenkbar gewesen.
Lieferketten, Energiepreise, Klimawandel – hier kann Digitalisierung etwas bewegen
Die großen globalen Herausforderungen, aber auch die Covid-19-Pandemie haben die Nachfrage nach Gütern und ebenso die globalen Lieferketten nachhaltig verändert. Vor allem die steigenden Energiekosten bestimmen die Schlagzeilen, genauso wie die Suche nach alternativen Quellen für knappe Rohstoffe. Dem muss sich die Prozessindustrie stellen. Um den Herausforderungen des Klimawandels zu begegnen, braucht es in allen Bereichen des Lebens ein Umdenken – inklusive der Prozessindustrie. Und wenn wir schon beim Thema Wandel sind: Schon heute haben es Unternehmen immer schwerer, die richtigen Fachkräfte zu finden, um die komplexen Anlagen zu entwickeln, zu bauen und zu betreiben. Der demografische Wandel wird sich weiter verstärken – auch dafür brauchen wir neue Antworten.
Um diese Herausforderungen zu bewältigen, bieten Digitalisierung und Automatisierung die nötigen Hebel. Sie helfen, Anlagen nicht nur flexibler, effizienter und produktiver zu machen, sondern auch intelligenter. Schon heute kommen dabei digitale Assistenten zum Einsatz, die dem Betriebspersonal anhand modernster Technologien wie Augmented Reality die Digitalisierung sowie der Arbeit im Feld ermöglichen: Sie können damit einfach individuelle Prüf- und Checklisten für Produktion, Wartung und Instandhaltung erstellen, auf die elektronische Dokumentation der Anlagen zugreifen und werden durch intelligente Geräte durch die Abläufe geführt. Das macht die Digitalisierung für die Teams an den Anlagen greifbar.
„Eine Pharmaanlage statt in einem Jahr in fünf Monaten umrüsten? Ohne Digitalisierung undenkbar.“
Automatisierung und Digitalisierung für mehr Nachhaltigkeit
Auch beim Thema Nachhaltigkeit helfen Automatisierung und Digitalisierung, Ressourcen effizient zu nutzen und Emissionen zu reduzieren. Wir haben es uns bei Siemens als einem der führenden Partner der Prozessindustrie zum Anliegen gemacht, mit einer eigenen Nachhaltigkeitsstrategie voranzugehen und Konzepte und Lösungen aufzuzeigen. Wir haben uns verpflichtet, den CO2-Ausstoß in unseren Lieferketten deutlich zu reduzieren und bis 2050 auf Null zu verringern, in unseren eigenen Produktionen wollen wir sogar schon 2030 CO2-neutral sein. Und das geht: Wir haben seit 2015 unsere CO2-Emissionen schon mehr als halbiert – und zwar mit den gleichen Mitteln, mit denen wir alle unsere Kunden und Anwender unterstützen können: innovative Produkte, Lösungen und Technologien, die eine schier unerschöpfliche Ressource nutzen. Prozess- und Anlagendaten enthalten wertvolle Informationen, mit denen sich der Ressourcenverbrauch optimieren, CO2-Ausstoß reduzieren und ganze Wertschöpfungsketten nachhaltiger gestalten lassen. Genauso, wie wir technologisch vorangehen, möchten wir als Partner unseren Kunden neue Wege der Wertschöpfung aufzeigen. Damit wir hier ganz nah an der Praxis sind, setzen wir unsere Technik in unseren eigenen Werken ein und gewinnen damit Auszeichnungen wie aktuell das Siemens Manufacturing in Karlsruhe als „Factory of the year“. Gemeinsam können wir in der Prozessindustrie den Weg hin zur Dekarbonisierung effizient und nachhaltig gestalten. Und damit nicht genug: Technologien wie Cloud- und Edge-Computing oder die Anwendung von künstlicher Intelligenz, sie alle beruhen auf der Verfügbarkeit von Daten. Es ist also höchste Zeit, diesen Schatz zu heben.
IIoT und durchgängige Lösungen bis in die Cloud werden bald Alltag sein
Gerade im Bereich Prozessoptimierung, Modernisierung bestehender Anlagen oder Flexibilisierung von Anlagen und Kapazitäten gibt es einen enormen Bedarf nach innovativen Softwarelösungen – und daher wird es schon bald Alltag sein, über IIoT und durchgängige Lösungen in der Cloud zu sprechen: Daten werden ganz selbstverständlich vom Sensor in die Cloud gestreamt, Anlagen standardmäßig am digitalen Zwilling entwickelt und optimiert. Die Integration von Daten und Modellen zwischen IT und OT wird ebenfalls weitergehen, die digitalen Zwillinge von Produkt, Produktion und Performance zunehmend verschmelzen. Dies erfordert eine durchgängige Vernetzung aller Komponenten.
Intelligente Lösungen in der Anlage und in der Cloud arbeiten dabei Hand in Hand: Cloudbasierte Applikationen werden große Datenmengen aufbereiten, mit künstlicher Intelligenz analysieren und die gewonnenen Erkenntnisse dann anderen Applikationen zur Verfügung stellen. Genau genommen ist das noch nicht einmal ein Zukunftsszenario: Schon längst gibt es Technologien, die die klassische Automatisierungspyramide um vernetzte, modulare und autonome Funktionen ergänzen. Moderne Software-Lösungen für die IT/OT-Integration können sowohl On-Premises, in der Cloud, als Hybrid- oder Industrial-Edge-Lösung implementiert werden. Der nächste Evolutionsschritt kommt mit Industrial 5G: Es wird helfen, Produktionsanlagen und Intralogistik einfacher und flexibler zu vernetzen sowie autonomer und effizienter zu machen. Und Anwender können damit anspruchsvolle Industrie-4.0-Applikationen schneller, performanter und flexibler umsetzen.
„Lieferketten, Energiepreise, Rohstoffe, Klimawandel – hier können wir mit Digitalisierung wirklich etwas bewegen.“
Die Zusammenarbeit in Ökosystemen führt zu ganz neuen Konzepten
Es ist wichtig, dass die digitalen Lösungen in der Lage sind, sich anzupassen – sei es, um eine andere Nische zu besetzen oder um mit neuen Applikationen und Anwendungen zusammenzuarbeiten. Der Schlüssel dazu sind evolvierbare und modulare Architekturen wie Platform as a Service (PaaS) oder Docker-basierte Lösungen. Eine enge Zusammenarbeit mit Entwicklern und Anwendern (Co-Creation) ist dabei unabdingbar, um Prozess- und Kundenwissen zusammen – und mit künstlicher Intelligenz in die Software einzubringen.
So haben Siemens und der Cloud-Security-Experte Zscaler gemeinsam eine Lösung für den sicheren Zugriff vom Arbeitsplatz im Büro oder mobil auf OT-Systeme und -Anwendungen im Produktionsnetzwerk vorgestellt. Das Besondere: Die Lösung kombiniert das OT-Konzept „Defense-in-Depth“ mit einer Zero-Trust-Architektur. Dieses Beispiel zeigt, wie die Zusammenarbeit in Ökosystemen zu ganz neuen Konzepten führen kann – und ist ein Grund mehr, sich auf die kommenden Entwicklungen zu freuen: Wir erleben gerade mit, wie sich die Zusammenarbeit in und zwischen Unternehmen verändert – gemeinsame Entwicklungen statt Lasten- und Pflichtenhefte, agile Teams mit unterschiedlichen Kompetenzen, und dazu die richtigen Werkzeuge. Diese Kombination aus digitalen Lösungen, innovativen Technologien und Kreativität, das macht die Zukunft der Digitalisierung in der Prozessindustrie so spannend.
Wir können stolz darauf sein,was die Industrie alles erreicht hat
Wenn ich an die Anfänge der Digitalisierung in der Prozessindustrie zurückdenke, standen dort Themen, die sich im Vergleich zu den großen Visionen von sich selbst organisierenden, vernetzten Fabriken im Internet der Dinge recht bescheiden anhörten. Aber der nahtlose Datenaustausch zwischen Anlagenplanung bzw. -engineering und Automatisierung war ein wichtiger Meilenstein und die Voraussetzung für weitere Innovationen: Nur mit einer einheitlichen und durchgängigen Datenbasis lassen sich Prozesse transparent machen und damit letzten Endes optimieren. Das Integrated Engineering wurde schnell um Integrated Operations, also die Vernetzung von Planungs- und Betriebsdaten erweitert. Und dann ging es Schlag auf Schlag. Gerade weil die Prozessindustrie lange Investitionszyklen hat, können wir wirklich stolz darauf sein, was die Industrie schon alles erreicht hat. Beispiel Anlagensimulation: Für viele Unternehmen war die Simulation mit Werkzeugen der Einstieg in die Digitalisierung. Damit konnte man Automatisierungsfunktionen testen und so Fehler frühzeitig entdecken und beseitigen. Aus dem integrierten Engineering und der Simulation entstand der digitale Zwilling, der heute ein fester Bestandteil vieler Digitalisierungsprojekte ist und einen digitalen Workflow und eine transparente Produktion ermöglicht.
Der nächste Schritt bestand darin, die Systeme weiter zu öffnen und dabei von den Fortschritten bei Standards und Schnittstellen zu profitieren. „Und auch da sind wir schon sehr weit gekommen. Die Namur Open Architecture (NOA) in Verbindung mit Dexpi (Data Exchange in the Process Industry) als geeignetes Datenformat schafft die Voraussetzungen für die nötige Durchgängigkeit und problemlosen Datenaustausch. Die Entwicklung von standardisierten, herstellerunabhängigen Schnittstellen für die effiziente Konfiguration, Kommunikation und Integration modularer Anlagen, wie sie mit dem Module Type Package (MTP) Konzept definiert ist, ermöglicht es, Prozessmodule oder Teilanlagen informationstechnisch so zu beschreiben, dass sie leicht in eine übergreifende Automatisierungslösung integriert werden können. Eine solche Lösung ist unser webbasiertes Prozessleitsystem: Modullieferanten können automatisierte Package Units quasi auf Knopfdruck in Simatic PCS neo importieren, visualisieren und orchestrieren – ein wichtiger Schritt auf dem Weg zum Digital Enterprise, damit Plug-and-Produce in der Prozessindustrie Wirklichkeit wird.
Autor:
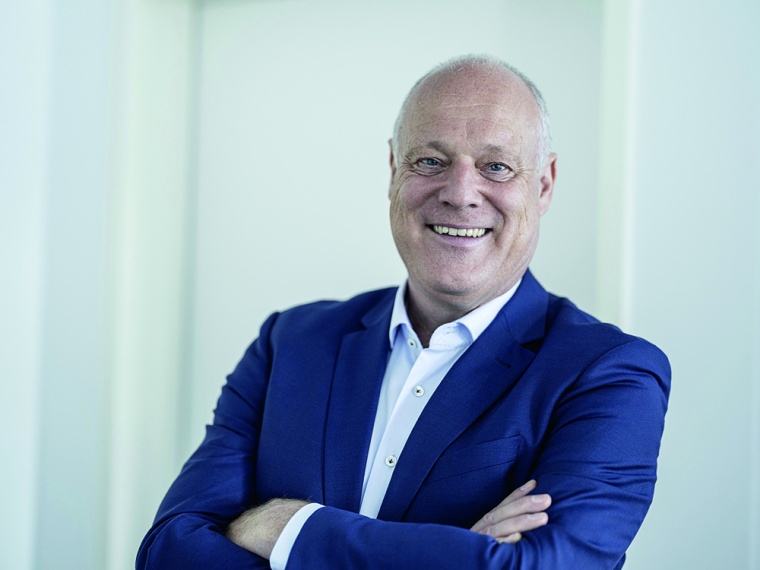
„Technologien wie Cloud- und Edge-Computing oder die Anwendung von künstlicher Intelligenz, sie alle beruhen auf der Verfügbarkeit von Daten. Es ist also höchste Zeit, diesen Schatz zu heben.“