Die Prozessindustrie im Wandel
In der modernen chemischen und pharmazeutischen Industrie sind Anpassungsfähigkeit, Resilienz und Nachhaltigkeit Schlüsselworte für eine erfolgreiche Produktion. Unternehmen entwickeln Initiativen, um wirtschaftlichen Schwankungen, Unterbrechungen in der Lieferkette und strengen gesetzlichen Anforderungen gerecht zu werden.
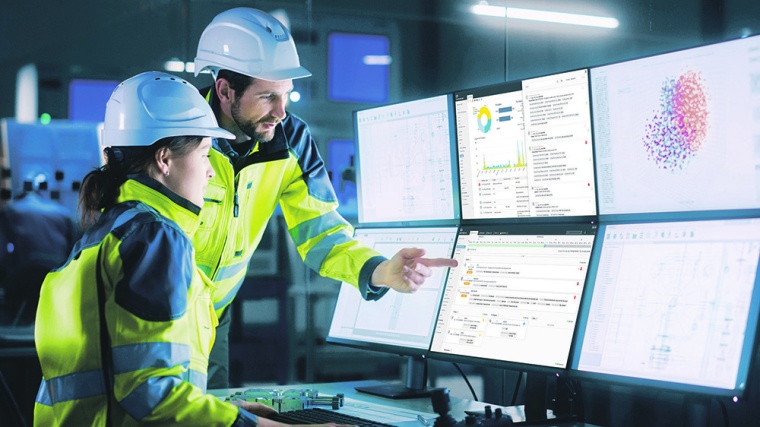
Das Ziel ist es, Nachhaltigkeit in den Kern der Geschäftsprozesse zu integrieren, ohne die Betriebskontinuität zu beeinträchtigen. Die Produktion soll sowohl effizient als auch umweltfreundlich gesteuert werden. Dabei ist ein hohes Maß an Flexibilität in den Betriebsabläufen und Transparenz in der Kommunikation entscheidend für den Erfolg. Nur so kann auf Veränderungen schnell reagiert werden.
Insbesondere energieintensive Sektoren in der Industrie stehen vor der Herausforderung, ihren CO2-Fußabdruck zu reduzieren. Man muss sich zunehmend von fossilen Brennstoffen verabschieden und den Energieverbrauch insgesamt reduzieren. In naher Zukunft müssen zahlreiche Unternehmen in der EU jährlich über ihre Fortschritte in Sachen Nachhaltigkeit berichten und bis 2050 sicherstellen, dass ihre Treibhausgasemissionen vollständig kompensiert werden. Dies bringt umfassende Veränderungen für die Betriebsanlagen mit sich und wirft häufig Fragen mit Blick auf die Umsetzung auf.
Für eine erfolgreiche digitale und ökologische Transformation ist es wichtig, dass Unternehmen eine kontinuierliche Optimierung anstreben – und das langfristig und strategisch. Dabei sind Ingenieurteams, Schichtleitende und Produktionsmitarbeitende gefordert, ein nachhaltiges Produktionsumfeld zu etablieren und zu stärken. Ingenieure müssen den Einsatz von Dampf, Strom, Kältemitteln, Druckluft, Heizgas und Wasser sorgfältig planen und synchronisieren. Die Anpassung von Chargenprozessen ist ein weiterer wichtiger Aspekt, um Synergieeffekte zu nutzen und Ressourcen effizient einzusetzen. Mit den richtigen Maßnahmen können Unternehmen nicht nur ihre ökologische Bilanz verbessern, sondern auch die Effizienz im Betrieb vorantreiben. Programme für Continuous Improvement (kontinuierliche Verbesserung), das die Mitarbeitenden in den Mittelpunkt stellt, bieten große Chancen, um Optimierungen im Betrieb erfolgreich zu verankern.
Continuous Improvement
Continuous Improvement (CI) ist ein langfristiger Ansatz zur Steigerung der Effizienz und Effektivität in Unternehmen, der sich über die letzten drei Jahrzehnte stetig weiterentwickelt hat. CI-Initiativen basieren auf einer Vielzahl von Maßnahmen, die darauf abzielen, Prozesse zu optimieren und Ressourcen effizienter zu nutzen. Ein klassisches Beispiel hierfür ist die Vermeidung und sofortige Behebung von Leckagen, die nicht nur Kosten sparen, sondern auch die Umwelt schützen.
Ein weiterer wichtiger Aspekt des CI ist die Vermeidung von Lastspitzen beim Anfahren von Anlagen, was durch die Synchronisation von Chargenprozessen erreicht werden kann. Der Einsatz von Bewegungsmeldern zur Steuerung von Beleuchtung und Heizung ist ein Beispiel für eine einfache, aber wirkungsvolle Maßnahme zur Energieeinsparung.
Prozessingenieure, Operational Excellence Manager oder Tagesschichtleitende benötigen kontextbezogene Informationen aus der Schichtdokumentation, um Probleme zu verstehen und zu lösen. So ist es wichtig, dass die Kommunikation im Schichtbetrieb nicht nur top-down, sondern auch bottom-up erfolgen kann – also in einem bidirektionalen Ansatz. Durch die Dokumentation von Daten können Ingenieure den Energieverbrauch erfassen und visualisieren. Mit Hintergrundinformationen aus den täglichen Schichtnotizen werden mögliche Ursachen und Herausforderungen ersichtlich, die oft einfach behoben werden können.
Mithilfe von einem digitalen Plant Process Management (PPM) können notwendige Informationen über Hierarchien und Abteilungen hinweg zirkulieren und interaktiv ausgetauscht werden. Um eine nachhaltigere Produktion zu erreichen, kann für jeden Bereich visualisiert werden, inwieweit Maßnahmen zur Reduzierung von Treibhausgasen beitragen. Ein digitales System, das Daten aus dem Produktionsprozess, wie z.B. Energiespitzen, mit kuratierten Informationen aus der Schichtkommunikation kombiniert, hilft den Schichtteams, sich schnell einen Überblick zu verschaffen und damit Zwischenfällen vorzubeugen bzw. diese schnell zu beheben.
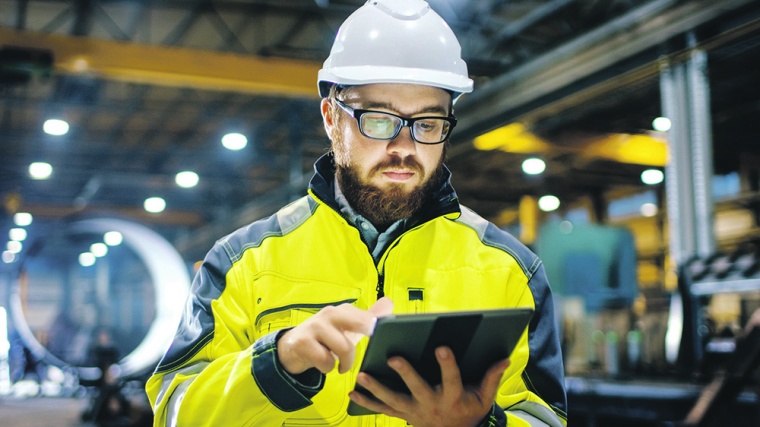
Synchronisierung
In einer Batch-Anlage, die auf die Herstellung chemischer Zwischenprodukte spezialisiert ist, stellen zeitlich variable Prozesse eine wesentliche Herausforderung dar. Diese Prozesse laufen parallel und müssen aufeinander abgestimmt werden. Verändern sich in einem Prozess diverse Parameter, kann dies Auswirkungen auf den kompletten Anlagenbetrieb mit sich ziehen. Das Hauptziel beim PPM ist es, die Wärmeenergie möglichst effizient zu nutzen, insbesondere da Prozesse wie Verdampfen, Kochen oder Destillieren einen hohen Energieaufwand erfordern. Im Schichtbetrieb ist es zudem wichtig, die Verfügbarkeit des Personals und den Schichtwechsel zu berücksichtigen. Die Prozessschritte müssen so abgestimmt werden, dass sie nahtlos von den Schichtteams übernommen werden können, um Energieverluste und Spitzenbelastungen zu vermeiden.
Schichtteams müssen stets über alle kritischen Aspekte informiert sein, um Energiepeaks zu verhindern. Da jede Schicht jedoch weniger als ein Drittel der Zeit der Woche arbeitet, ist es unmöglich, den gesamten Prozess alleine zu überwachen. Daher ist es entscheidend, dass umfassendes Wissen effizient an die nachfolgenden Schichten übergeben wird. Traditionelle Methoden wie Excel-Tabellen und Office-Dokumente sind unzureichend, da sie weder eine effektive Verknüpfung wichtiger Prozessinformationen noch tiefgehende Datenanalysen ermöglichen.
Digitale Lösungen haben in einigen Chemie- und Pharmaunternehmen zu einer Produktionssteigerung von bis zu 10 % geführt. Durch den Einsatz von Prozessdaten und digital gesteuerten Dashboards können Energieverbrauch und die Entwicklung der Gesamtanlageneffektivität (OEE) überwacht und eine Verringerung des Treibhausgasausstoßes erreicht werden. Diese Technologien ermöglichen eine präzisere Steuerung und Überwachung der Produktionsprozesse, was zu einer nachhaltigeren und effizienteren Betriebsführung führt.
Autor: Andreas Eschbach, CEO, Eschbach GmbH, Bad Säckingen
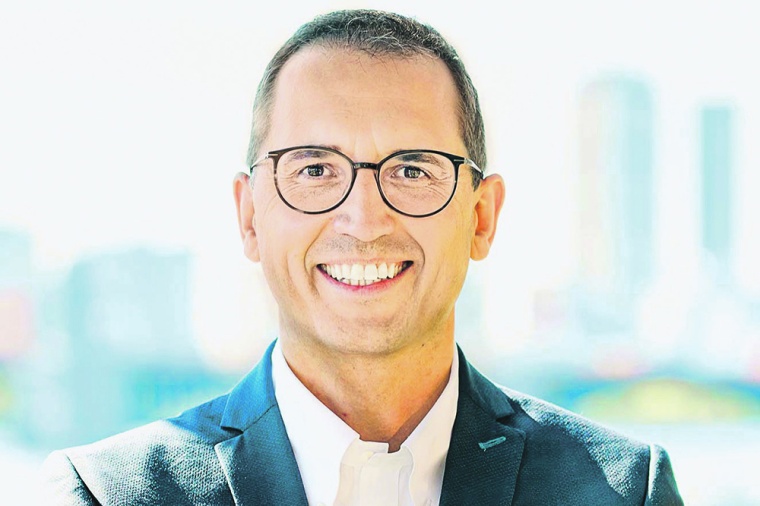
„Continuous Improvement ist ein langfristiger Ansatz zur Steigerung der Effizienz und Effektivität in Unternehmen.“
----------------------------
Zur Person
Andreas Eschbach ist CEO des Softwareunternehmens Eschbach mit Hauptsitz in Bad Säckingen, Süddeutschland, und einer US-Niederlassung in Boston, Massachusetts. Der Diplominformatiker und Computer-Validierungsbeauftragte erwarb ein Leadership-Diplom vom St. Gallen Management Institute (SGMI), bevor er 2005 sein eigenes Unternehmen gründete, das sich auf die Optimierung von Plant Process Management (PPM) in der Prozessindustrie fokussiert.