Chemieindustrie im Energiesparmodus: Verborgene Potenziale heben
Hohe Energiepreise belasten die Wettbewerbsfähigkeit und das Thema Energiemanagement ist aus der Unternehmenssteuerung der Chemieindustrie nicht mehr wegzudenken.
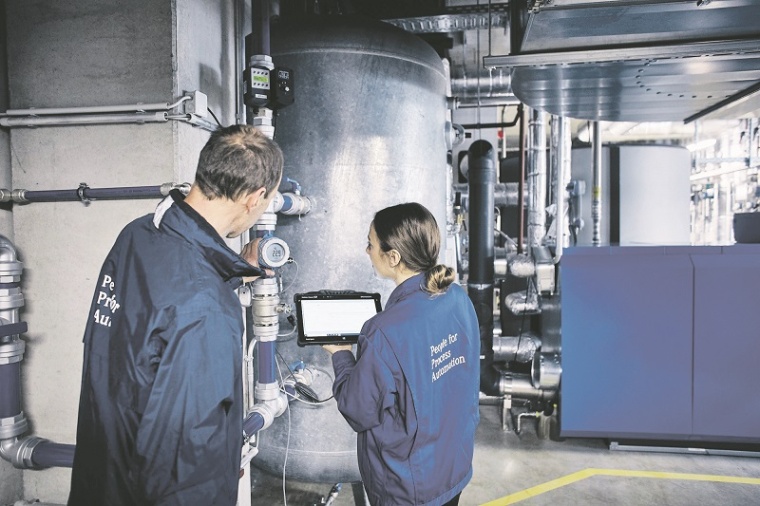
Hilfskreisläufe – wie bspw. der Dampfverbrauch, die Überwachung des Druckluftverbrauchs, Heizprozesse oder Kühlungen – sind essenziell für den reibungslosen Betrieb, werden jedoch häufig bei Energiebetrachtungen übersehen. Dabei bieten gerade diese unterstützenden Systeme erhebliche Möglichkeiten zur Energie- und Kosteneinsparung. Angesichts des ambitionierten Ziels der Treibhausgasneutralität bis 2045 ist ein ganzheitlicher Ansatz gefragt. Unternehmen müssen daher nicht nur ihre Hauptprozesse, sondern auch die Effizienz ihrer Hilfskreisläufe optimieren, ohne dabei Sicherheit, Qualität, Zuverlässigkeit und Betriebszeit zu beeinträchtigen.
Energieeinsparungen von bis zu 15 %
Daher ist es von großer Bedeutung, Möglichkeiten zur Verbrauchsreduzierung in den Hilfskreisläufen zu identifizieren und umzusetzen. Für eine präzise Erfassung und Analyse des Energieverbrauchs braucht es moderne und zuverlässige Messtechnik, die den Verbrauch um bis zu 15 % ermöglichen kann. Dies erfordert die Festlegung der richtigen Energieleistungsindikatoren (EnPIs) und entsprechende Anpassungen der Prozessabläufe. Solche Reduzierungen hängen von Messgeräten ab, die den Energiefluss, den Energieverbrauch und die Prozessdaten nach ISO 50001 und ISO 50006 objektiv messen und diese gemäß den definierten EnPIs darstellen können. Im Folgenden werden drei konkrete Beispiele beschrieben, die zeigen, wo die Chemieindustrie durch gezielte Maßnahmen Energie einsparen kann.
Optimierung der Kesseleffizienz
In der chemischen Industrie sind Kessel unverzichtbar, da sie als zentrales Element der Energieversorgung fungieren. Sie liefern die notwendige Wärme für chemische Reaktionen, Trennprozesse und viele weitere Anwendungen. Der Wirkungsgrad eines Kessels ist von großer Bedeutung, da er die Effizienz der Energieumsetzung bestimmt. Der Grad der Effizienz hängt von zahlreichen Faktoren wie Energieverluste, Wärmeübertragung, Korrosion und Dampfverbrauch ab, was das System sehr komplex macht. Eine genaue Überwachung der Kessel ist daher unverzichtbar.
Ungesättigter oder feuchter Dampf führt nicht nur zu erheblichem Energieverlust, sondern auch zu hohen Betriebskosten. Um dies zu verhindern, ist eine kontinuierliche und sorgfältige Überwachung notwendig. Insbesondere die Kontrolle des Trockenheitsanteils des Dampfs ist wichtig, da der Einsatz von trockenem statt nassem Dampf die Effizienz einer Anlage erheblich verbessern kann. Ein Trockenheitsanteil von nur 90 % bedeutet bereits einen Energieverlust von 10 %. Durch den Einsatz moderner Messtechnik, wie dem multivariablen Wirbelzähler-Durchflussmessgerät Proline Prowirl F200 kann der Trockenheitsgrad des Dampfes genau überwacht werden. Dies ermöglicht es, Energieverluste zu minimieren und die Effizienz des Kessels zu maximieren. Die Rückgewinnung und Wiederverwendung von Energie führt zu einem höheren Wirkungsgrad und einem geringeren Brennstoffverbrauch. Dadurch können Unternehmen ihre Betriebskosten nachhaltig senken und die Effizienz der gesamten Anlage deutlich steigern.
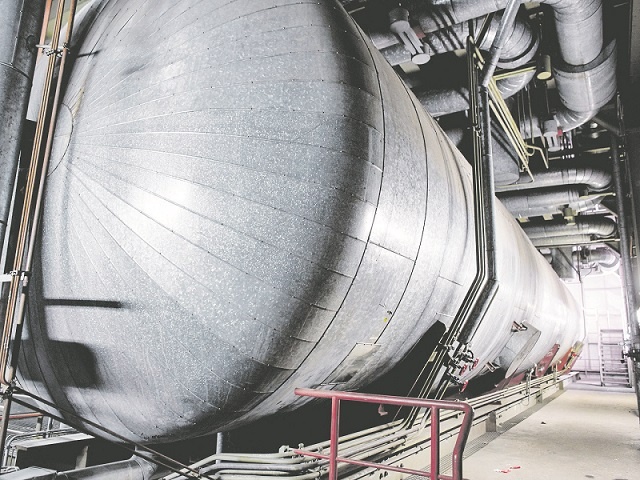
Effizienzsteigerung in Druckluftsystemen
Auch die Druckluftsysteme bieten große Einsparpotenziale. Schließlich werden bis zu 10 % des gesamten Stromverbrauchs für die Drucklufterzeugung genutzt, wobei 95 % dieser Energie als Abwärme verloren gehen. Zudem „verschwindet“ ein Teil der erzeugten Druckluft durch Leckagen im Versorgungsnetz, was zu erheblichen finanziellen Verlusten führt. Diese werden oft unterschätzt oder als unvermeidbar betrachtet. Zur Maximierung der Effizienz von Druckluftsystemen sind verschiedene Maßnahmen erforderlich. Leckagen zu minimieren und die Überwachung von Filtern zur Druckreduzierung sind dabei zentrale Aspekte. Messgeräte wie der T-Mass I 500 tragen zusätzlich zur Sicherheit der Druckluftkompressoren bei und helfen, Energieverluste zu vermeiden. Die Effizienz eines Luftkompressorsystems kann durch die Ansaugung der Luft an der kältesten Stelle, die Nutzung der Kompressorabwärme, die Reduzierung des Betriebsdrucks und das Abschalten der Kompressoren im Leerlauf während Stillstandzeiten verbessert werden. Eine kontinuierliche Überwachung der Kompressoreffizienz sowie Informationen über Wartungsintervalle sind ebenfalls von Bedeutung, um die Effizienz zu maximieren und Energieverluste zu minimieren.
Versorgungseffizienz bei Heiz- und Kühlsystemen
Die zunehmende Komplexität neuer Gebäude, strengere Gesetze und Vorschriften sowie veränderte Anforderungen an Heizung und Kühlung stellen Unternehmen vor große Herausforderungen. Angesichts der Vielzahl branchenspezifischer Heizverfahren und Heiztechnologien sind maßgeschneiderte Ansätze und präzise Messwerte erforderlich, um deren Leistung zu bewerten und den Output zu optimieren. Insbesondere bei Feuerungsanlagen treten häufig hohe Energieverluste auf, die durch ineffiziente Verbrennung, falsche Bedienung oder unzureichende Wartung verursacht werden. Die Messung der Energieeffizienz ist der effektivste Weg, um diese Verluste zu vermeiden und den Energieverbrauch um bis zu 55 % zu senken. Durch die Überwachung des Brennstoffverbrauchs, der Verbrennungsluft, der Abgastemperatur und der Übertragungsrate der thermischen Energie lassen sich erhebliche Verbesserungen erzielen. Dies ermöglicht die Identifizierung und Quantifizierung von Energieverlusten, wie sie bspw. beim Leerlauf- und Teillastbetrieb des Brenners auftreten, sowie die Bewertung und Optimierung des Wirkungsgrads und des Verbrauchs des Kessels. Zudem trägt es zur Minimierung von Wartungskosten und Stillstandzeiten bei und erlaubt die Quantifizierung von Verbesserungsmaßnahmen wie der Vorwärmung der Verbrennungsluft.
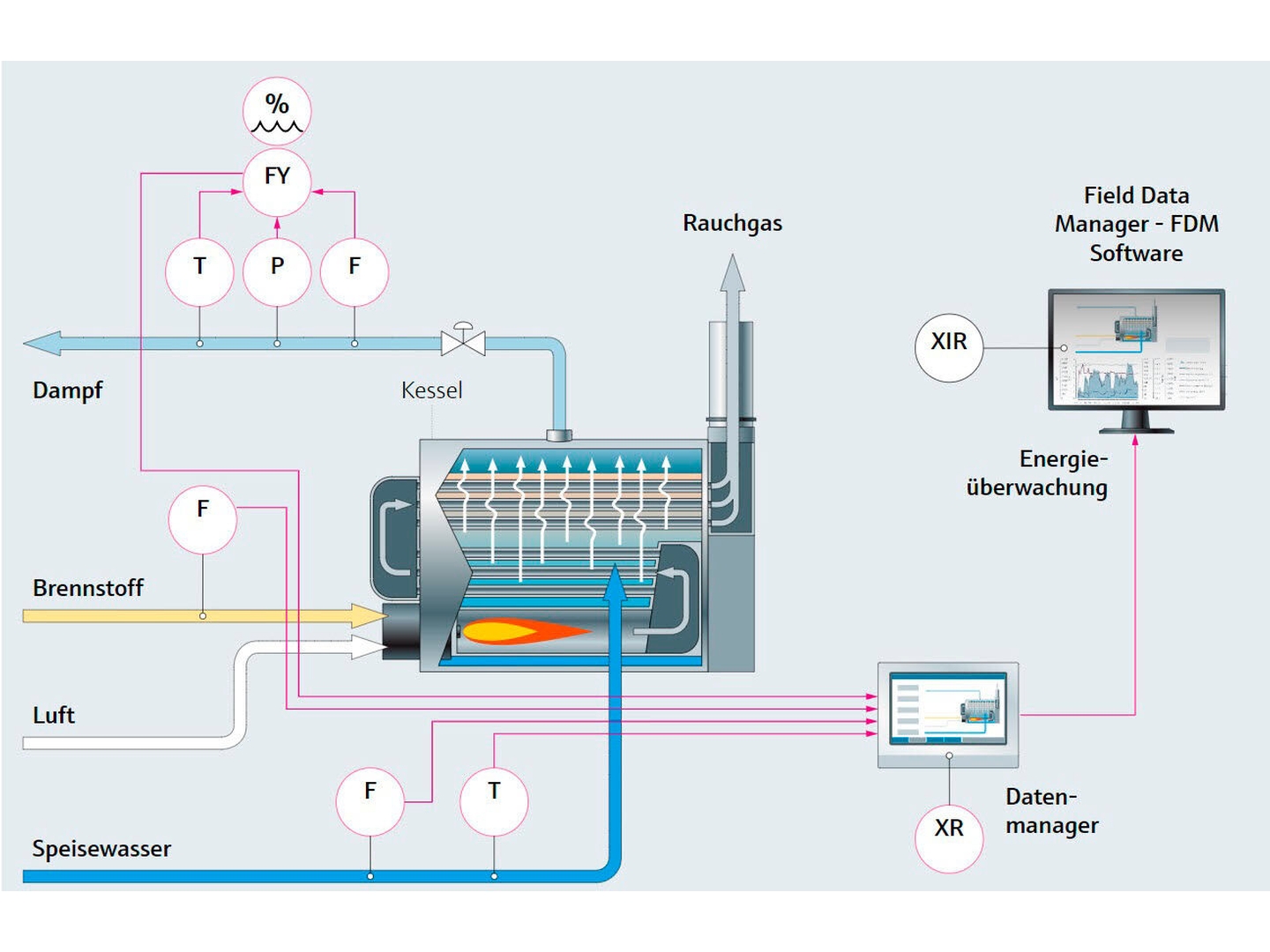
Überwachung des Gesamtwirkungsgrad im Kesselhaus durch Berechnung und Registrierung der Kesseleffizienz (FY = Dampfdurchfluss; XR = Berechnung und Registrierung der Kesseleffizienz; XIR = Energieüberwachung) © Endress+Hauser
Energieineffizienz frühzeitig erkennen mit Heartbeat Technology
Damit Energieverluste und sonstige Anomalien im Anlagenbetrieb frühzeitig entdeckt werden, hat Endress+Hauser das Heartbeat -Technology-Diagnosekonzept entwickelt, das umfangreiche Geräte- und Prozesseinblicke bietet, um die Anlagenperformance zu erhöhen sowie Betriebs- und Wartungskosten zu senken. Die Technologie ist in zahlreiche unserer Messgeräte integriert und besteht aus den drei Funktionen Diagnostics, Verification und Monitoring. Die Geräte prüfen sich selbst mit einem hohen Diagnoseabdeckungsgrad, melden ihren Zustand und geben klare Handlungsempfehlungen bei Fehlern. Die Verifikation der Geräte kann jederzeit ohne Prozessunterbrechung durchgeführt werden und ist ISO 9001-konform. Im Anschluss analysiert Heartbeat Monitoring dann die Sensorsignale und übersetzt sie in verständliche Informationen zum Gerät und Prozess. So können Anlagenbetreiber schnell handeln, bevor es zu großen Energieverlusten und damit verbundenen Kosten kommt.
Energiemanagement braucht Messtechnik
Mangelndes Verständnis und fehlende Transparenz darüber, wo Energie verbraucht wird, führen zu Ressourcenverlusten, Produktivitätseinbußen und unnötigem Energieverbrauch. Endress+Hauser bietet als zuverlässiger Partner deshalb innovative Lösungen und Technologien, die es Unternehmen ermöglichen, ihren Energieverbrauch signifikant zu senken und ihre Betriebskosten nachhaltig zu reduzieren. Mit unserer Expertise und den hochwertigen Messgeräten können Unternehmen nicht nur ihre Effizienz steigern, sondern auch einen wichtigen Beitrag zur Erreichung ihrer Klimaziele leisten.
Autor: Andreas Leppert, Industry Manager Chemical & Oil, Endress+Hauser Deutschland, Weil am Rhein
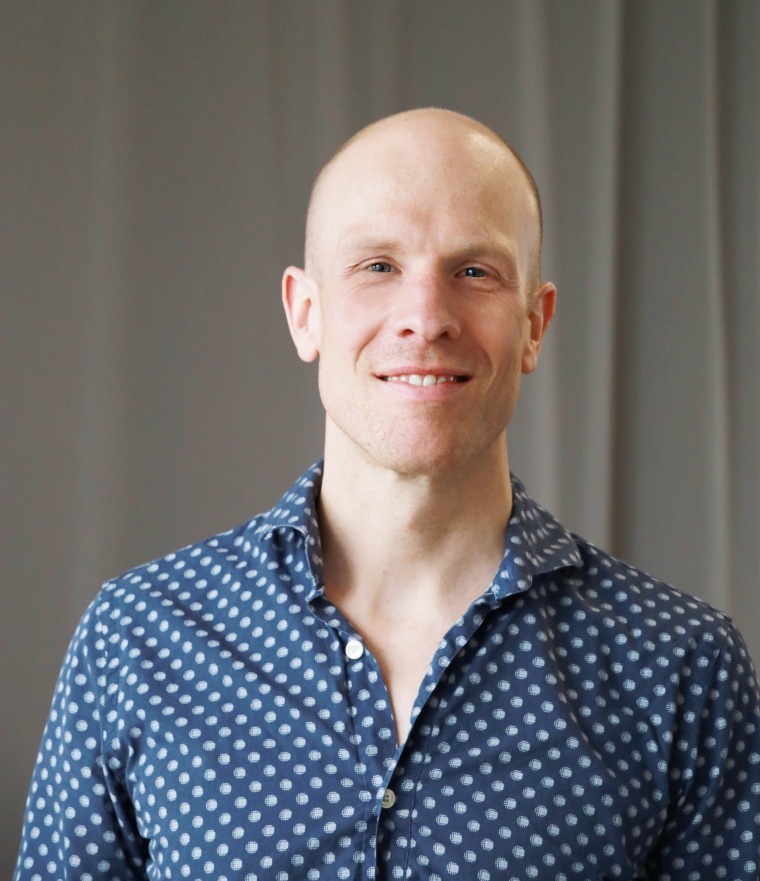
„Angesichts der Vielzahl branchenspezifischer Heizverfahren sind maßgeschneiderte Ansätze erforderlich.“