Asset Monitoring für Teilanlagen
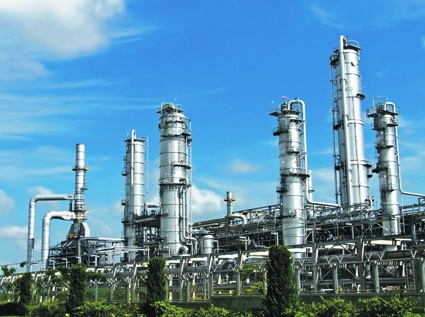
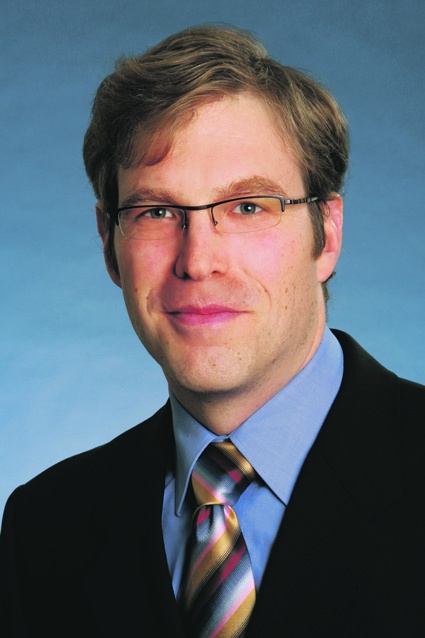
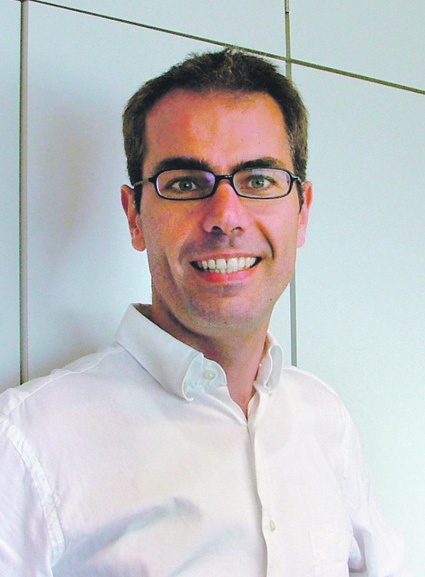
Vor dem Hintergrund einer zunehmend heterogenen Systemlandschaft sowie des ständig steigenden Automatisierungsgrades von Anlagen gewinnen innovative Assistenzsysteme und Plant Asset Management (PAM) Lösungen immer mehr an Bedeutung. Dabei kommt der Überwachung und Diagnose von Apparaten, Geräten und Automatisierungstechnik eine Schlüsselrolle zu.
Eine zentrale Zielsetzung von modernem PAM liegt in der Steigerung der Anlagenverfügbarkeit und der Anlagennutzung durch Zustandsüberwachung von Feldgeräten und Anlagenkomponenten (Asset Monitoring). Um frühzeitig Hinweise über schleichende Verschlechterungsprozesse zu gewinnen, kommt der echtzeitfähigen Bewertung der Asset-Gesundheit eine Schlüsselrolle zu, denn erst auf Basis gesicherter Erkenntnisse ist eine Prognose und schließlich eine Ableitung geeigneter Maßnahmen möglich, etwa im Sinne der vorausschauenden Wartung, aber auch der Produktions- bzw. Stillstandsplanung. Zuverlässige Asset-Statusinformationen bilden daher die Grundlage für vielfältige, für den Geschäftserfolg wesentliche Unternehmensentscheidungen.
Um über die Ebene der intelligenten Feldgeräte hinaus aussagekräftige Asset-Statusinformationen auch von „nicht intelligenten" Anlagenteilen und Teilanlagen verfahrenstechnischer Betriebe erhalten zu können, wurde in Zusammenarbeit von Bayer Technology Services und Fraunhofer IOSB ein Software-Werkzeug entwickelt, das ohne erhebliche Engineering- und Modellierungsaufwände sowie auf Basis der bestehenden Feldinstrumentierung zum Einsatz kommen kann.
Einordnung in die Systemlandschaft
Auf der Geräteebene existieren in vielen Fällen bereits Asset-Statusinformationen - intelligente Feldgeräte sind in vielen Betrieben etabliert. Häufig haben die Anwender allerdings keine Möglichkeit, die Informationen in vollem Umfang zu nutzen. Um auf die entscheidenden Aspekte zu fokussieren, müssen die Daten sinnvoll in einen Verdichtungsprozess eingebracht werden. Nur so lässt sich das anlagennahe Asset Management nachhaltig verbessern. Ebenso werden auf der Ebene der komplexeren Maschinen und Apparate, wie etwa Pumpen oder Wärmetauscher, Condition Monitoring Systeme angeboten. Aber auch hier ist die aufgabengerechte Verdichtung der Statusinformationen für den Anwender zwingend erforderlich.
Anders sieht die Situation bei der Überwachung und Diagnose bereits einfacher Apparatecluster, insbesondere aber ganzer Teilanlagen aus. Zwar stehen hier zur Prozessführung standardmäßig eine Vielzahl von Informationen, wie Mess- und Stellgrößen, zur Verfügung. Eine automatisierte Verdichtung sowie deren Abgleich mit dem aktuellen Betriebszustand fand aber bislang nicht statt. Um diese Lücke zu schließen, hat BTS in Kooperation mit dem Fraunhofer-IOSB das Entwicklungsprojekt PUMon (Process Unit Monitoring) initiiert, um ein System zur Überwachung von prozesstechnisch zusammenhängenden Anlagenteilen (Process Units) zu entwickeln.
PUMon soll sich ohne besondere Engineering- und Modellierungsaufwände auf Basis der bestehenden Feldinstrumentierung für die Asset Überwachung von Betrieben mit zunächst kontinuierlicher Fahrweise nutzen lassen. Bis heute wurde eine Reihe wichtiger Belastungstests mit Aufgabenstellungen unterschiedlicher Komplexität durchgeführt. Das Ergebnis: Dem Anwender steht heute ein zuverlässiges und einfach zu bedienendes Überwachungswerkzeug zur Verfügung, welches die Asset-Statusinformationen pro Process Unit verdichtet und aggregiert in Form einer Ampel darstellt. Anwendungsschwerpunkte sind alle nicht standardmäßig mit einer Eigendiagnose ausgerüsteten Anlagenkomponenten, wie etwa Kessel und Rohrleitungen, Wärmetauscher oder Destillationskolonnen. Zudem hat sich gezeigt, dass der Process Unit Monitor auch gewinnbringend zur Überwachung von störungsanfälligen Assetkombinationen eingesetzt werden kann, für die bereits Einzelüberwachungslösungen existieren.
Damit können bestimmte Typen von Anlagenproblemen abgedeckt werden, die bisher nicht erfasst wurden, und auch kausale Wirkzusammenhänge in den Verschlechterungsprozessen aufgedeckt werden, beispielsweise wenn sich Anlagenprobleme innerhalb einer Teilanlage von Asset zu Asset fortpflanzen.
Process Unit Monitoring enthält, richtig verstanden, bereits einige Elemente klassischer Prozessführung (Performance Monitoring) - allerdings nicht im Sinne einer Prozessführung nach Key Performance Indikatoren, um einen optimaleren Fahrzustand zu finden, sondern im Sinne einer gezielten Überwachung von bestimmten Teilprozessen. Damit können Informationen über nachlassende Asset Performance abgeleitet werden, die nicht unmittelbar auf eine Beeinträchtigung der Assetgesundheit zurückzuführen sind - etwa durch Verlassen der zuvor definierten Referenzfahrweise der Anlage.
Konzeption
Der mathematische Kernalgorithmus für das Überwachen von Anlagenteilen wurde bereits erfolgreich im Rahmen eines Diagnosekonzepts für feldbusbasierte Automatisierungsanlagen eingesetzt. Der Grundintention des Softwaretools folgend, werden die Prozessparameter einer Process Unit nicht isoliert betrachtet. Vielmehr korreliert das System alle Parametersätze miteinander und erfasst auf diese Weise das charakteristische Zusammenspiel der einzelnen Komponenten der zu überwachenden funktionalen Einheit. Es erlernt und überprüft dabei deren Abhängigkeiten und leitet daraus summarische Statusaussagen ab, etwa im Sinne eines Ampelschemas, bei dem zwischen Gutzustand („grün"), sich abzeichnendem Handlungsbedarf („gelb") und Fehlfunktion („rot") unterschieden wird.
Dank der besonderen Eigenschaften des verwendeten neuronalen Netzes kann der Anwender die Überwachungsmodelle eigenhändig - sozusagen per Knopfdruck - erzeugen. Dazu wählt sich der Prozessexperte die notwendigen Prozessinformationen in Form von Lern- oder Referenzdatensätzen aus. Dieser datengetriebene Ansatz unterscheidet sich grundlegend von der Vorgehensweise bei analytisch modellbasierten Methoden. Diese erfordern eine aufwändige Modellierung und viel Erfahrung der Entwickler. Hinzu kommt: Ändert sich der Prozess, zum Beispiel weil bauliche oder prozessoptimierende Maßnahmen durchgeführt wurden, muss auch das analytische Modell entsprechend angepasst werden. Zusätzliche Modellierungsaufwände sind die Folge. Dagegen bedarf es bei dem hier vorgestellten datengetriebenen Ansatz lediglich einer neuerlichen Anpassung des Modells durch den Anwender.
Vorgehen bei der Anwendung
Das konkrete Vorgehen im Zusammenhang mit der Anwendung des Überwachungstools, ausgehend lässt sich in neun Schritten beschreiben:
- Installieren der Software auf einem leistungsfähigen handelsüblichen PC: Die Software läuft auf allen gängigen 64bit-Betriebssystemen.
- Anbindung der Software an den Prozess: Der Process Unit Monitor verfügt übe OPC- und SQL-Schnittstellen. Im Fall der OPC-Schnittstelle werden historische Daten über OPC-HDA und Echtzeitdaten über OPC-DA akquiriert. Nach außen werden die Statusinformationen zusätzlich pro Process Unit mittels des internen OPC-DA Servers zu Verfügung gestellt.
- Auswahl der zu überwachenden Anlagenteile bzw. Teilanlagen (Process Units): Dies können besonders kritische oder für den Prozess besonders bedeutende Anlagenteile sein. Beispiele sind die Überwachung einer Destillationskolonne, einer Wärmetauscher-Pumpe Kombination, eines Schneckenextruders oder eines Kessels samt angeschlossener Peripherie wie Rohrleitungen und Instrumentierung.
- Festlegung der zu überwachenden Prozessparameter: Überwacht werden prozesstechnisch zusammengehörige Anlagenteile bzw. Teilanlagen. Die zur Überwachung notwendige Sensorik/Aktorik legt der Prozessexperte fest. Er bestimmt, welche Drücke, Temperaturen, Durchflüsse, etc. in die Überwachung einbezogen werden. Relevant sind alle Ist-, Soll- und Stellwerte der betrachteten funktionalen Überwachungseinheit. Die Software unterstützt die Konfiguration, indem Prozessvariable einfach an und abgewählt werden können.
- Platzierung der Ampeln zur Visualisierung des Process Unit Status auf Bedienbildern von PIMS oder PLS: Für jede Process Unit wird eine Ampel (OK; Erhöhte Aufmerksamkeit; Fehler) auf dem zugehörigen Bedienbild visualisiert. Später können mögliche Abweichungen auf diese Weise in Echtzeit von den Anlagenfahrern registriert werden.
- Selektion der Lern- bzw. Referenzdatensätze: Der Prozessexperte selektiert Prozessphasen, in denen die Anlage den Anforderungen entsprechend gefahren wurde. Indem pro Modell mehrere Produkte bzw. Lastzustände trainiert werden können, reduziert sich der Aufwand für die Modellerstellung und Überwachung.
- Trainieren des Modells: Das Modell einer Process Unit wird auf Knopfdruck in der Regel innerhalb einer Minute erstellt und kann im Anschluss sofort für die Überwachung verwendet werden.
- Start der Überwachung: Die Process Unit wird auf Basis der zuvor festgelegten Referenz (Lerndaten) mit dem in Schritt 7 erstellten Modell überwacht. Abweichungen in den Prozessvariablen bzw. in deren Korrelationen werden übersichtlich in Form einer Top-Ten Darstellung präsentiert. Für jede Prozessvariable wird der prozentuale Anteil am Gesamtfehler der Process Unit dargestellt.
- Statusüberwachung durch die Anlagenfahrer: Die Ampeln werden von den Anlagenfahrern überwacht. Bei „Gelb" oder „Rot" ist der Prozessexperte zwecks Detailanalyse zu informieren.
Die Schritte 6 bis9 sind erforderlichenfalls zu wiederholen und sollten idealerweise als Teil einer gelebten PAM-Strategie in den betrieblichen Alltag integriert werden - der Aufwand hierfür ist überschaubar. Für die Aktualisierung eines Modells braucht es in der Regel nur wenige Minuten.
Fazit
Der beschriebene Process Unit Monitor stellt ein prozessunabhängig adaptierbares und universell anwendbares Monitoringsystem zur Überwachung von Anlagenteilen bzw. Teilanlagen dar. Er basiert auf einem selbstlernenden neuronalen Algorithmus, der ohne erhebliche Engineering- und Modellierungsaufwände sowie auf Basis der bestehenden Feldinstrumentierung zum Einsatz kommen kann.
Anwendungsschwerpunkte sind nicht standardmäßig mit einer Eigendiagnose ausgerüstete Anlagenkomponenten, wie etwa Kessel und Rohrleitungen, Wärmetauscher oder Destillationskolonnen. Zudem kann das Überwachungswerkzeug zur Ergänzung bestehender Condition Monitoring Systeme sowie zur Diagnose bestimmter störungsanfälliger Assetkombinationen eingesetzt werden - beispielsweise um kausal bedingte Wirkungszusammenhänge von Verschlechterungsprozessen aufzudecken und zu eliminieren.
Die Leistungsfähigkeit des PUMon Konzeptes wurde in einer umfangreichen Testphase in Betrieben von Bayer MaterialScience gezeigt. Dem Anwender steht demnach ein marktreifes Überwachungstool zur Verfügung, das sich auf einfache Art und Weise zur Steigerung der Gesamtanlageneffektivität (OEE) einsetzen lässt.