Vorteile von kundenspezifisch entwickelten Folienlösungen gegenüber Edelstahlsystemen im Containmentbereich
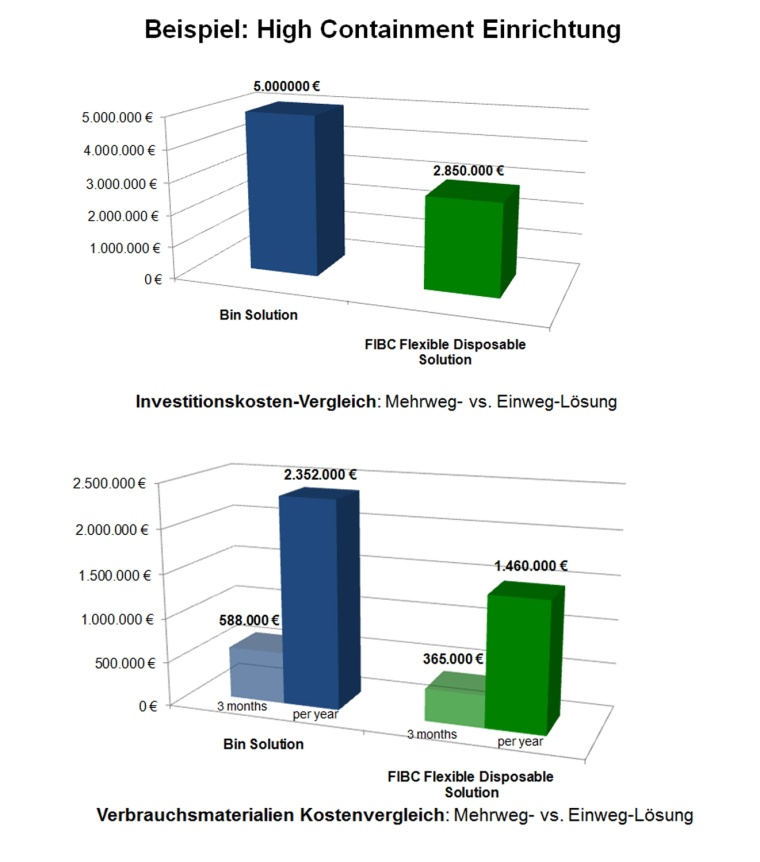
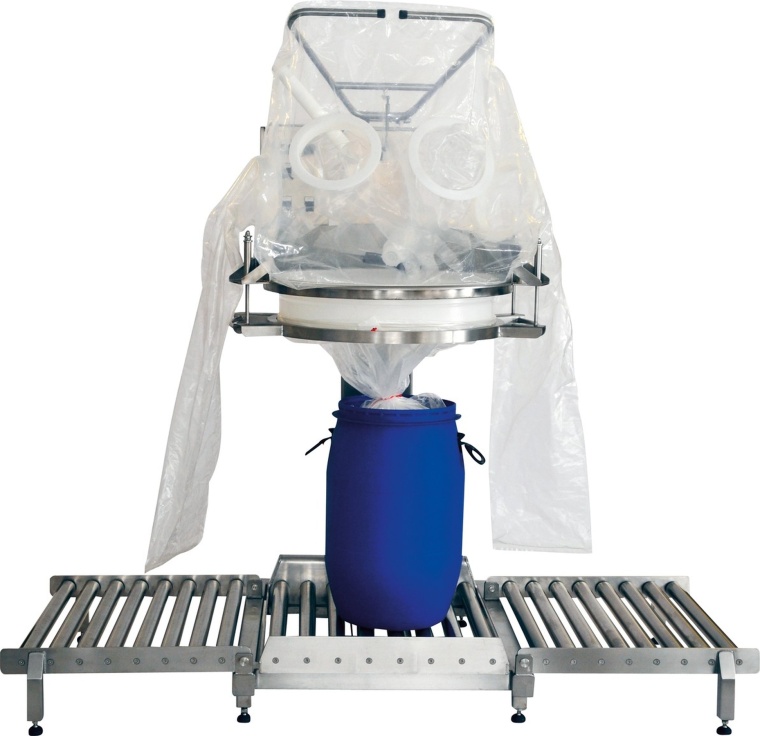
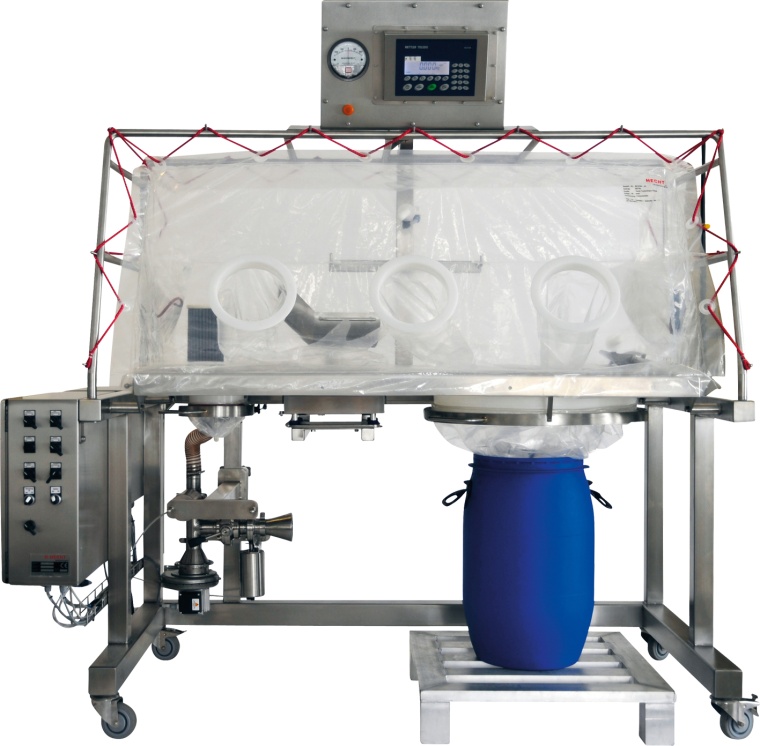
In der chemischen und wirkstoffherstellenden Industrie werden die eingesetzten Stoffe immer aktiver und damit auch gefährlicher. Zum Schutz der Mitarbeiter und/oder des Produktes werden zur Verarbeitung der Stoffe RABS oder Isolatoren eingesetzt. Dieser Beitrag stellt die Vorteile einer flexiblen Lösung im Vergleich zu einem konventionellen Isolator dar.
Bei vielen pharmazeutischen Wirkstoffen (API) sind Grenzwerte von OEB 5 (Occupational Exposure Band) einzuhalten, um das Personal effektiv vor den Folgeschäden zu schützen. Das bedeutet, dass eine Umgebungskontamination von maximal < 1 µg/m3 nicht zu überschreiten ist. Zur Verdeutlichung: Vervielfältigt man das Raumvolumen auf die Größe des Empire State Buildings, darf sich im gesamten Gebäude maximal die Stoffmenge von 0,04 Teelöffeln befinden, um dieses Level einzuhalten. Das untermauert, wie streng diese Grenzwerte sind. Somit bleibt oft nur die Möglichkeit die Stoffe in einem Isolator zu handeln. Die meisten Isolatoren waren bis vor kurzem starre Systeme aus Edelstahl, deren Investitions - und Anschaffungskosten sehr hoch und die Handhabung wenig flexibel waren. Auch die Reinigung von Prozessen und Anlagenteilen stellt eine zunehmende Herausforderung für die Qualitätssicherung, speziell in Vielzweckanlagen, dar. Hecht Technologie bietet Lösungen an, die sowohl die Vorteile von Isolatoren, wie z. B. die absolute Geschlossenheit des Systems, ausnützen, auf der anderen Seite die Schwächen dieser starren Systeme überwunden haben. Dabei gleicht kein System den anderen, jede Lösung wird speziell auf die Bedürfnisse der Kunden zugeschnitten. Eine sorgfältige Planung und Definition der Anforderungen ist also ein absolutes Muss beim Engineering dieser Systeme.
Haben hochpolierte Edelstähle noch Zukunft?
Bislang glänzt es noch sehr in den Wirkstoff- und Pharmabetrieben. Jedoch dringen immer mehr so genannte „Single Use Systems" - Einwegsysteme in diesen Bereich vor. Edelstahlisolatoren werden durch Einwegfolie ersetzt. Beutel ersetzen Fässer oder sogar Container. Die Biotechindustrie macht es vor. Vor 10 Jahren wurden fast ausschließlich Edelstahlapparate in der pharmazeutischen Biotechnologie eingesetzt. Die Realität sieht anders aus, es werden überwiegend flexible Foliensysteme eingesetzt. Grund für diesen Trend: Enorme Kosteneinsparung und Flexibilität in der Produktion. Eine Reduzierung um bis zu 40 % der Herstellungskosten konnte durch den Einsatz von Single Use Technologies bereits erreicht werden. In den USA arbeitet man bereits an Disposable Facilities (=vollständige Einweg-Herstellprozesse) zur Senkung der Herstell- und Reinigungskosten. Weitere Vorteile sind, dass es keine Produktrückstände gibt und eine Kreuz-Kontaminationen nicht mehr möglich ist. Dies gewährt höchste Sicherheit für Anwender und herzustellende Produkte.
Bei welchen Stoffen finden die Systeme ihren Einsatz
Der Vorteil der Einwegtechnologien kommt bei häufigen Produktwechsel und der dadurch verbunden Reinigung sowie der Handhabung hochaktiver oder hochgefährlicher Substanzen zu tragen. Gerade bei diesen Produkten ist eine Rückstandslose Reinigung von größter Wichtigkeit. Als hochaktive oder hochgefährliche Substanzen werden Zytostatika, kanzerogene, mutagene, teratogene Stoffe sowie Hormone und Antibiotika bezeichnet. All diese Stoffe fordern einen aktiven Bedienerschutz sowie ein hohes Maß an Reinheit.
Welche Einwegtechnologien stehen heute zur Verfügung
Speziell im Bereich des Feststoff-Transfers zur Befüllung sowie zur Entleerung der Prozesse gibt es bereits Einwegtechnologien die eingesetzt werden. Betrachtet man den Herstellprozess in einem Pharma- oder Wirkstoffbetrieb findet der erste Kontakt mit der Substanz im Wareneingang statt. Dort werden die Produkte bemustert und Proben zur Analyse und Kontrolle entnommen. Um diesen Arbeitsschritt auszuführen stehen zum Beispiel Einwegisolatoren zur Verfügung, aber auch in der Verwiegung zur Vorbereitung der Produktion, auch in der Forschung und Entwicklung werden die System bereits eigesetzt.
Einwegprobenahmesystem EPS zur Bemusterung
Zur Bemusterung im Wareneingang findet man häufig in der pharmazeutischen- oder Wirkstoffherstellung Laminar Flow Einheiten(Abk.: LF). Diese LF-Einheiten bieten im Bereich der Bemusterung Schutz des Produktes während der Bemusterung durch HEPA gefilterte Luft. Diese LF-Einheiten schützen jedoch den Bediener nur bedingt. Durch das arbeiten am offenen Gebinde kommt der Bediener auch mit dem Produkt in Kontakt. Gerade bei hochaktiven oder gefährlichen Substanzen muss dies vermieden werden. Das EPS schließt diese Lücke.
Die zu bemusternden Gebinde werden über eine Folientechnologie, an den in das EPS integrierten Einwegisolator, angeschlossen.
Die Bemusterung findet innerhalb des Isolators statt. Der Bediener ist zu jeder Zeit vor dem Produkt geschützt. Durch die geschlossene Proben-Entnahme wird weder der Raum, noch andere Gebinde kontaminiert. Die Reinigung sowie Dekontamination des Raumes und Bedieners wird reduziert und beschleunigt. Der Einwegisolator wird nach der Bemusterung entsorgt. Eine Aufwändige Reinigung wie z. B. bei Edelstahlisolatoren entfällt.
Einweg-Wäge-Isolator EWI zur Einwaage
Nach der Bemusterung und Freigabe wird der Einsatzstoff vor der Produktion auf die geforderte Masse eingewogen. Dies geschieht in einem Wägebereich. Auch hier muss der Schutz stets gewährleistet werden. Die Gebinde werden ähnlich wie beim Probenahmesystem über ein Foliensystem an den Isolator angedockt. Eine zusätzliche Hubvorrichtung für das Gebinde erleichtert die Entnahme des Produktes im Folienisolator. Neu ist die aktiv - passiv Wägetechnik. Durch diese innovative Technologie können erstmals Produkte in einem Isolator gewogen werden, ohne dass sich die Wägeplattform im Isolator befindet. Hecht Technologie hat eine Technik entwickelt, bei der die Wägeplattform außerhalb des Isolators befestigt und durch eine spezielle Durchführung im Isolator mit einer Schale verbunden ist. Genauigkeiten von ± 1 g können hiermit erreicht werden. Eine spezielle Membrantechnologie an der Isolatorduchführung kompensiert mögliche Druckunterschiede im Isolator. Die Beeinflussung der Waage ist ausgeschlossen. Sollten geringere Toleranzen benötigt werden, besteht die Möglichkeit eine Waage in den Isolator einzuschleusen. Durch die undurchlässige Folie und den Betrieb im Unterdruck, ist die Sicherheit der Anwender stets gewährleistet. Ein integrierter Einweg-Hepa-Filter unterstützt das System zusätzlich.
Folientechnologie in der Herstellung
Durch die Kooperation von Hosokawa Alpine und Hecht Technologie wurde sogar der weltweite erste Herstellprozess als Einwegsystem entwickelt. Das Mikronisieren eines Wirkstoffes durch eine Einwegluftstrahlmühle. Abgesichert wird dieser Prozess durch einen Einwegisolator. Eingesetzt wird diese Technologie zuerst in der Forschung und Entwicklung, bei der häufige Produktwechsel an der Tagesordnung stehen. Gerade in der F&E sind in der frühen Produktentwicklung keine verlässlichen Toxitäts-Daten vorhanden. Ein optimaler Mitarbeiterschutz muss trotz allem immer gewährleistet sein. Die in den Isolator integrierte Einweg-Luftstrahlmühle handelt all diese Anforderungen.
Anbieter
Hecht Technologie GmbH
Meist gelesen
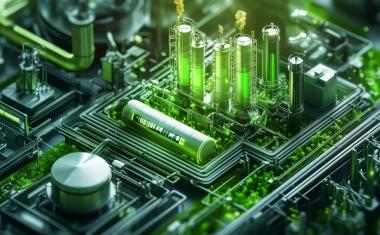
Die Zukunft der Chemieindustrie
Die Chemieindustrie in Deutschland und Europa steht vor erheblichen Problemen. Die hohen Energiekosten und die Nachfrageschwäche setzen viele Unternehmen unter Druck und belasten ihre Wettbewerbsfähigkeit.
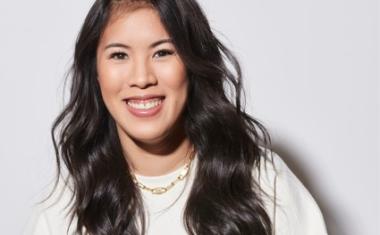
Wissenschaftliche Fakten kreativ verpackt und emotional präsentiert
Interview mit der Chemikerin, Wissenschaftsjournalistin, Fernsehmoderatorin, YouTuberin und Autorin Mai Thi Nguyen-Kim zur Rolle von Wissenschaft in unserer Gesellschaft.
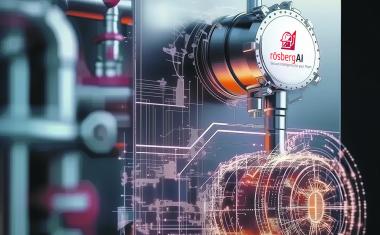
KI im Engineering
Rösberg Engineering hat ein KI-Projekt aufgesetzt; bei dem eine Datenbasis, Infrastruktur und verschiedene Lösungen für KI-gestütztes Engineering entstehen
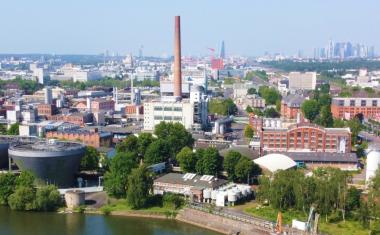
WeylChem Fine Chemicals: Globaler CDMO mit Produktionskapazitäten auf drei Kontinenten
Ein neuer Akteur betritt die Bühne der Feinchemie: WeylChem Fine Chemicals (WCFC), eine global aufgestellte Organisation für die kundenspezifische Entwicklung und Herstellung von Spezialchemikalien (CDMO).
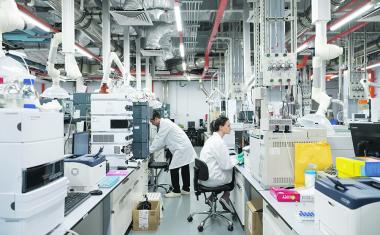
Cyberresilienz – vom Faktor Mensch bis zu Audits
Die europäische Richtlinie zur Sicherheit von Netz- und Informationssystemen (NIS 2) dient der Angleichung des IT-Sicherheitsniveaus in allen EU-Staaten