Produktwechselzeiten verkürzen
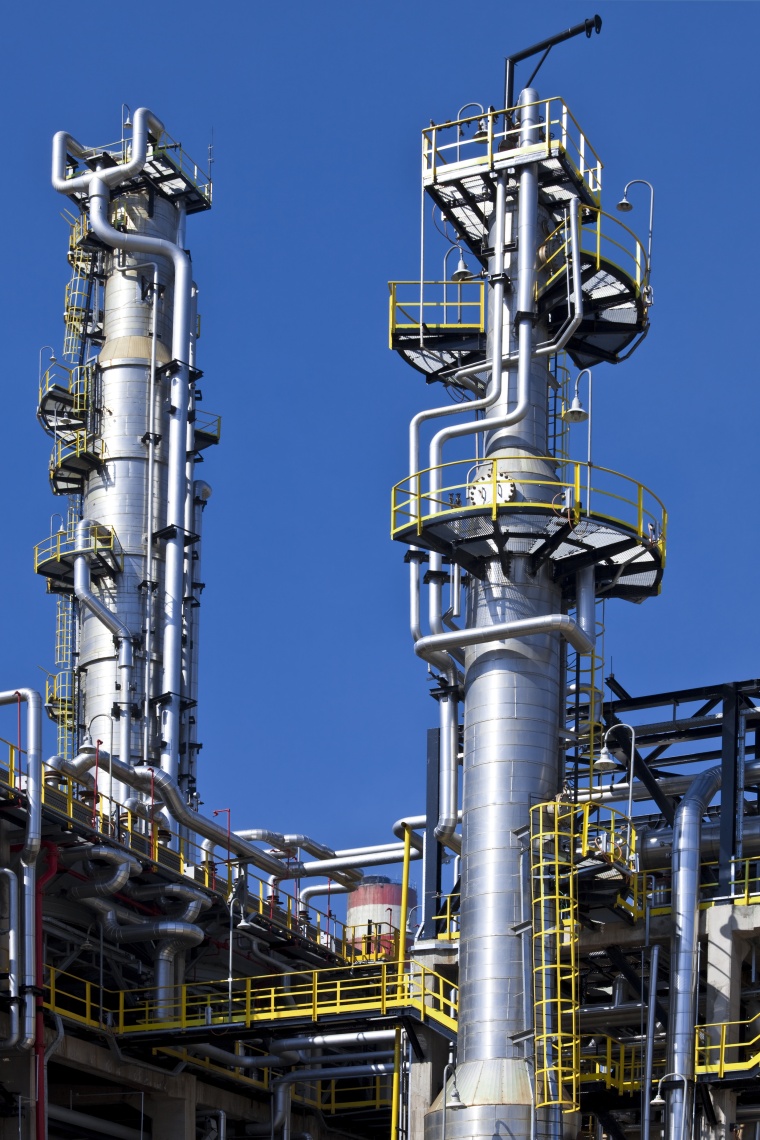
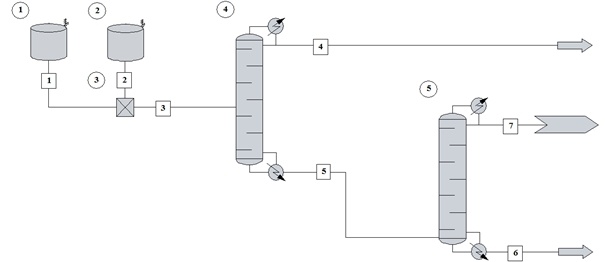
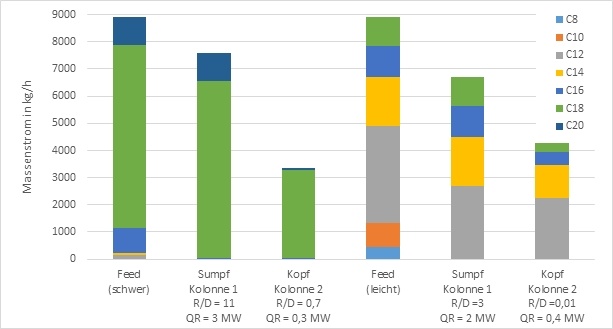
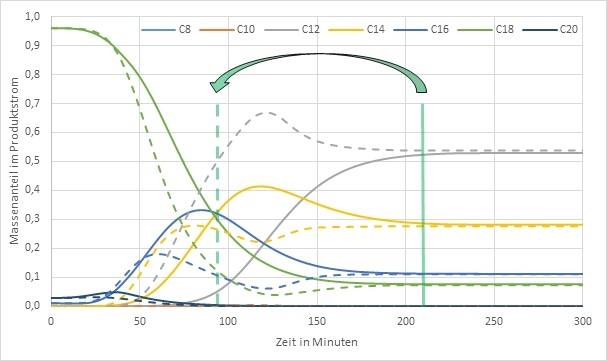
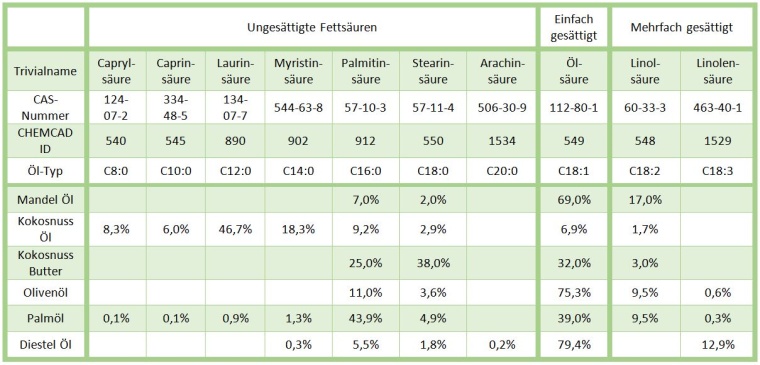
Mit Hilfe des Prozesssimulators Chemcad können die durch Produktwechselzeit bedingten Produktionsausfälle minimiert werden.
Verschiedene Produkte mit nur einer Produktionsanlage herzustellen ist nicht erst seit dem wachsenden Fokus auf Rohstoffwandel und Energiewende für Anlagenbetreiber attraktiv. Die flexible Produktion ist ein wichtiger Bestandteil zur Umsetzung dieser Megatrends. Während sich an den Anlagenlebenszyklen von 20 bis 40 Jahren nichts geändert hat, verkürzen sich die Produktlebenszyklen. Zudem ändern sich Art, Qualität, Preis und Verfügbarkeit der zur Produktion benötigten Ressourcen in der globalisierten Welt immer schneller. Es ist also von wirtschaftlichem Vorteil wenn die Produktion flexibel auf solche Änderungen reagieren kann, gegebenenfalls auch mit veränderten oder mit neuen Produkten.
Die rigorose computergestützte Simulation der Produktionsprozesse hilft, verschiedene Rohstoff-Produkt-Szenarien in kurzer Zeit zu analysieren und zu bewerten. Hierbei werden thermodynamische und apparative Beschränkungen konsequent berücksichtigt. Ohne die Simulation wären zahlreiche kosten- und zeitaufwändige Versuche an den Produktionsanlagen notwendig um die neuen Szenarien zu verifizieren. Während dieser Versuche können die Anlagen in der Regel nicht zur Produktion genutzt werden.
Sind die verschiedenen, im Idealfall optimierten, einzelnen Betriebsparameter einer Produktionsanlage für die einzelnen Szenarien bekannt, so kommt es nur noch während der Umstellung von einer Produkt-Rohstoff-Kombination zu einer anderen zu Produktionsausfällen. Der Prozesssimulator Chemcad kann dabei helfen, die produktwechselzeitbedingten Produktionsausfälle zu minimieren.
Fallbeispiel Oleochemie
Die oleochemische Industrie hat es als Verwerter von Naturprodukten und Recyclestoffen traditionell mit schwankenden Zusammensetzungen in den Ausgangstoffen ihrer Prozesse zu tun. Um für nachgeschaltete Prozesse weitgehend gleichbleibende Feed-Bedingungen zu schaffen, kann eine Destillationsanlage vorgeschaltet werden, in der die starken Schwankungen in der Zusammensetzung der Rohstoff-Öle auf ein vorgegebenes Maß reduziert werden.
Eine solche Destillationsanlage ist Gegenstand dieser Fallstudie. Tabelle 1 zeigt die Zusammensetzung verschiedener Rohstoff-Öle. Man erkennt, dass selbst die reinen Rohstoff-Öle ein breites Spektrum an chemischen Zusammensetzungen bieten. Bei der Verwendung von Ölgemischen und der Verwertung von recycelten Ölen kommt es zu weiteren Kombinationsmöglichkeiten.
Dennoch kann mit zwei nacheinander geschalteten Destillationskolonnen das Spektrum der einzelnen Fettsäuren gut eingegrenzt werden. Dabei werden in der ersten Destillation die unerwünschten Leichtsieder abgetrennt und in der zweiten Destillation die unerwünschten Schwersieder. In Abbildung 1 ist das Fließbild einer solchen zweistufigen Destillationsanlage dargestellt. Betrachtet werden hier beispielhaft ein schweres und ein leichtes Rohstoff-Öl, für welche durch Destillation je ein Produkt-Öl Spektrum erreicht werden soll.
Optimale Betriebszustände
Fixiert man die Kolonnendrücke, so verbleiben je Kolonne zwei freie Variablen. In diesem Beispiel wurden das Rücklaufverhältnis (R/D) und die Verdampferleistung (QR) als Designvariablen gewählt. Als optimaler Betriebszustand wird hier der Betriebspunkt bezeichnet in dem der Produktstrom maximal ist. Die Utilitykosten werden also gegenüber den Feedkosten vernachlässigt. Zur Optimierung wird der in Chemcad implementierte „Process Optimizer“ eingesetzt. Die Ergebnisse der Optimierungsrechnungen sind in Abbildung 2 dargestellt. Im Falle des schweren Rohstoff-Öls werden 38 % der Feedmasse bzw. 48 % der C18-Fettsäure in das Produkt übernommen, im Falle des leichten Rohstoff-Öls sind es 48 % bzw. 63 % der C12-Fettsäure.
Rohstoff-Produkt-Wechsel
Um den Wechsel vom leichten zum schweren Produkt zu simulieren, müssen die Speicherterme berücksichtigt werden. Das Volumen der Rohrleitungen kann gegenüber den Volumina der einzelnen Kolonnenböden und der Wärmetauscher (Kopfkondensator und Verdampfer) vernachlässigt werden. Mit dieser Annahme lässt sich das bisher stationär betrachtete Flowsheet ohne Veränderungen in ein dynamisches Flowsheet umwandeln. Um das Speicherverhalten der Kolonnen korrekt wiederzugeben sind aber noch zusätzliche Annahmen und Angaben notwendig. Für Kopfkondensator und Kolonnensumpf mit Verdampfer kann durch eine stabile Füllstandsregelung von konstanten Volumina ausgegangen werden. Der Durchmesser der Kolonnen kann basierend auf einer Flutpunktberechnung mit dem in Chemcad integrierten Sizing Tool berechnet werden. Um den variablen Flüssigkeitsfüllstand auf den einzelnen Kolonnenböden zu berechnen, sind zusätzliche geometrische Angaben notwendig, wobei auch hier das Chemcad Sizing Tool bei der Ermittlung hilft.
Die Umstellung der Betriebsparameter erfolgt mit Rampen über einen Zeitraum von 30 Minuten, um keine zu sprunghaften Änderungen der Größen hervorzurufen und dem Operator die Möglichkeit zum Eingreifen zu lassen. Erlaubt man den Start der Rampen bereits zum Zeitpunkt des beginnenden Feedwechsels, so beläuft sich die Zeit bis zum Erreichen der Produktspezifikation auf 213 Minuten.
Dynamische Optimierung
Der CHEMCAD „Process Optimizer“ kann auch zur Optimierung dynamischer Prozesse verwendet werden. Optimierungsziel hier ist es, die Zeit bis zum Erreichen der Produktspezifikation zu minimieren. Als Entscheidungsgrößen werden die Zielwerte der Rampen gewählt. Die Betriebsparameter sollen also entsprechend den oben beschriebenen Strategien nur einmal verändert werden. Doch selbst mit dieser Einschränkung lässt sich die Produktwechselzeit um mehr als die Hälfte auf 93 Minuten reduzieren wie in Abbildung 3 gezeigt wird.
Bei dem gefundenen Szenario der minimalen Produktwechselzeit handelt es sich nicht im mathematischen Sinne um ein Optimum. Häufig ist es jedoch nicht entscheidend das globale Minimum der Zielfunktion zu finden. Für den Betrieb zahlt sich die Optimierungsrechnung bereits aus, wenn die Produktwechselzeit reduziert wird.
Globales Optimum und Process Simulation Cup
Führt man die Optimierung mit zusätzlichen Punkten der Designvariablen durch, so kann die Produktwechselzeit weiter reduziert werden, das Optimierungsproblem wird aber komplexer. Mit dem OTS Modus (Operator Training System) kann auch ganz auf Rampen verzichtet werden und stattdessen können die Regelventile für Rücklauf und Dampfzufuhr zeitlich frei verstellt werden.
Wie weit lässt sich die Produktwechselzeit noch reduzieren und wie groß ist das Potential, wenn mehr als ein Sprung der Designvariablen erlaubt wird? Diese Fragen werden im Process Simulation Cup 2015 beantwortet. Ziel ist es für den gegebenen Prozess das globale Minimum der Produktwechselzeit zu finden (siehe Infokasten).
Erfolgreiche Umsetzung in der Praxis
Die Produktwechselzeit und das Potential zu ihrer Reduzierung sind für jede Anlage und jedes Rohstoff-Produkt-Szenario unterschiedlich. Außerdem muss abgewogen werden, wie detailliert das dynamische Prozessmodell sein muss, beispielsweise in Bezug auf geometrische Daten.
Für die beschriebene Umsetzung bietet InfraServ Knapsack in Zusammenarbeit mit Chemstations entsprechende Dienstleistungen an. So wurden beispielsweise für einen Kunden aus der Oleochemie die Produktwechselzeiten für 12 Rohstoff-Produkt-Szenarien reduziert und über die zusätzlich gewonnene Produktionszeit noch der Rohstoff- und Energieeinsatz veringert.
Fazit
Chemcad bringt in einem Paket alle benötigten Werkzeuge für die stationäre und die dynamische Simulation sowie für die Optimierung von Prozessen mit. Durch die vollständige Integration der Tools zur Prozessoptimierung (Process Optimizer), zur Apparatedimensionierung (Sizing Tool) und zur dynamischen Simulation (CC-Dynamics) können schnell und einfach Szenarien durchgerechnet und Verbesserungsvorschläge erarbeitet werden. Anlagenbesitzer und Betreiber können in allen Phasen Unterstützung und Beratung bei InfraServ GmbH & Co. Knapsack KG einholen. So wurde bereits zahlreichen Kunden geholfen die Betriebskosten in der Produktion deutlich zu reduzieren.