Firefighting prägt den Alltag, Teil 1
Seit gut einer Dekade hat die Globalisierung alle Bereiche der Prozessindustrie erreicht. Wertschöpfungsketten verschieben sich in immer kürzeren Abständen.
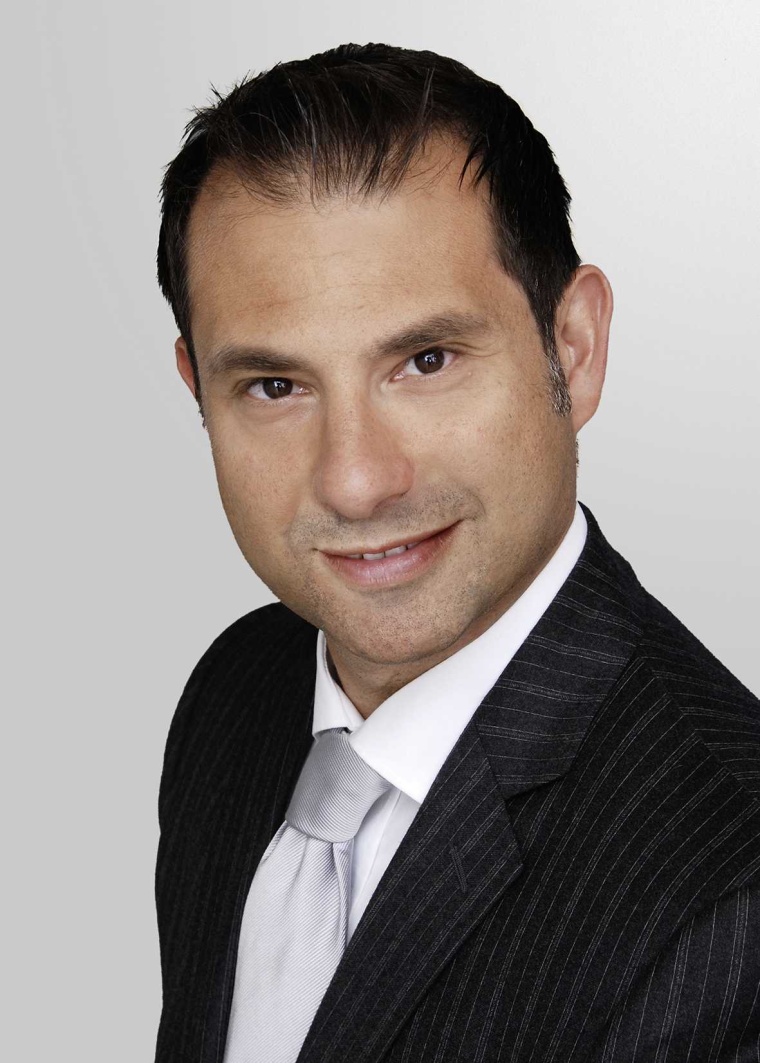
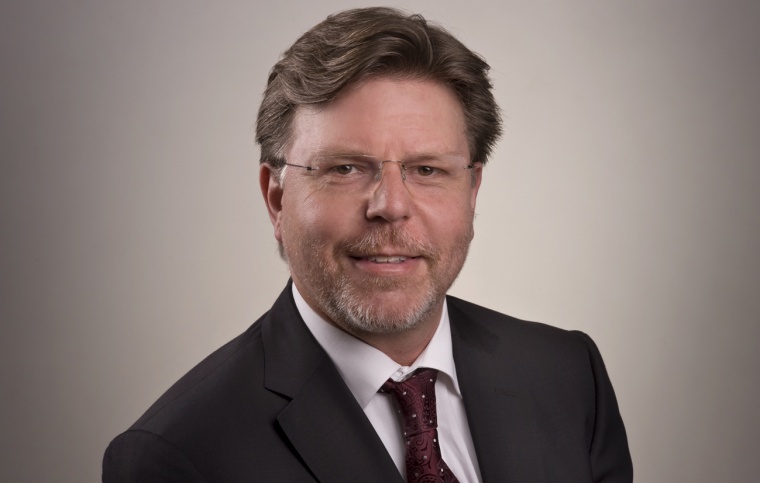
Innovative Ansätze und Produktideen müssen in kürzer werdenden Zeitabständen umgesetzt werden. Steigendes Arbeitsvolumen muss mit tendenziell abnehmenden Ressourcen bewerkstelligt werden. Mit dem Ergebnis, dass sich in der Belegschaft das Gefühl festsetzt, nur noch von einer Katastrophenverhinderung zur anderen zu hetzen. Firefighting ist nicht mehr die Ausnahme sondern die Regel.
In der Prozessindustrie hat sich in den vergangenen Jahren ein Phänomen manifestiert: Das Geschäft scheint unvorhersehbarer zu werden – vor allem die mittel und kurzfristigen Ressourcenanforderungen verändern sich ständig und manchmal auch mehrmals am Tag. Auf dem Shopfloor wird jede Herausforderung angenommen und mit dem Einsatz vereinter Kräfte werden die Kundenanforderungen fast immer erfüllt. Trotz der weiter wachsenden Arbeitsbelastung stellt sich eine Mischung aus einem wohligen Gefühl des Unverzichtbaren bei vielen Individuen ein. „Ohne mich wäre das nicht mehr gegangen“ und andererseits einer permanenten Überlastung. Es hat etwas von Brände löschen mit dem Heldengefühl, welches unter Feuerwehrleuten bei schwierigen Einsätzen entsteht. Daher haben wir den Begriff „Firefighting“ für dieses Phänomen gewählt, welches 80 % der Unternehmen in der Prozessindustrie betrifft. Es hat sich bereits in vielen Kulturen der Prozessindustrie verankert und kann zum einen ein neues Wir-Gefühl schaffen oder aber bei entstehender Überbelastung auch Konflikte zwischen den beteiligten Organisationseinheiten hervorrufen.
Teamgedanke in Gefahr
Besonders in den Fällen wo „Firefighting“ in Form von kontinuierlichen Eingriffen in die Produktionsfeinplanung dazu führt, dass die vorhandene Grundkapazität über zusätzliche Rüstwechsel reduziert wird und in denen der Instandhaltung die benötigten Freiräume für die Grundwartung nicht mehr zur Verfügung gestellt werden und sich das Störaufkommen an den Anlagen dadurch weiter aufbaut, gerät der Teamgedanke in Gefahr. Dann ziehen sich die Beteiligten in der Konsequenz häufig in ihre „Silos“ zurück. Bei aller emotionalen Glorifizierung bzw. die damit verbundene Hassliebe zu dieser Situation müssen wir uns die Frage stellen, ob dies der richtige Weg für die Unternehmen ist. Wie sieht es nüchtern betrachtet mit der Effizienz und der Effektivität aus? Das Gefühl sagt uns, es kann nicht effizient sein und die durch sinkende Produktivität damit einhergehende, negative Kostenentwicklung ist oft ein deutlicher Beweis dafür.
Mehr Arbeit mit weniger Ressourcen bewältigen
Zunächst sollten wir beleuchten, woher dieses Phänomen kommt, was es nährt und wie es sich entwickelt. Seit gut einer Dekade hat die Globalisierung alle Bereiche der Prozessindustrie erreicht. Wertschöpfungsketten verschieben sich in immer kürzeren Abständen. Dieser beschleunigte Wandel führt zu immer höheren Anforderungen an die Flexibilität. Innovative Ansätze und Produktideen müssen in kürzer werdenden Zeitabständen umgesetzt werden. Eine Situation, die zunächst mehr Ressourcen auf den Plan rufen müsste. Durch Kostensenkungsprogramme ist die Situation in den meisten Unternehmen eine andere. Das steigende Arbeitsvolumen muss mit tendenziell abnehmenden Ressourcen bewerkstelligt werden.
Gerade in den vergangenen Jahren hat das Thema Kosten die Prozessindustrie erfasst. Selbst die lange Zeit als Bastion gegen die schnellen Märkte stehende Pharmaindustrie, insbesondere die Originator Hersteller sind hiermit zunehmend konfrontiert. Es wurden viele Mitarbeiter abgebaut, da dies der schnellste Weg ist Kosten einzusparen und die Industrie sich in den Jahrzehnten zuvor über viele Bereiche sehr fett aufgestellt hat. Die Notwendigkeit wird in der Pharmaindustrie getrieben durch auslaufenden Patentschutz und die häufig schwächelnde F&E Pipeline sowie veränderte Marktsituationen. Viele neue Medikamente sind keine klassischen Blockbuster mehr, da die Regularien zur Zulassung in vielen Märkten mittlerweile so stark angezogen sind, dass ein weiteres Konkurrenzprodukt für diese Therapeutika ein zu hohes Risiko beinhaltet, hierfür die Zulassung nicht zu erhalten. Strategisch werden vermehrt therapeutische Lücken besetzt, welche dann zwar relativ konkurrenzarm aber dafür mit deutlich geringeren Margen auskommen müssen. Die Kosten für die Entwicklung und für die diversifizierten Marktzulassungen sind die gleichen. Darüber hinaus treiben die Regularien der Zulassungsbehörden und Gesundheitsämter den Aufwand an nicht wertschöpfenden Tätigkeiten jährlich an. Diese Entwicklung kann nur durch eine gesteigerte Produktivität abgefedert werden.
Die Folge der Entwicklung in der Pharmaindustrie sind hohe Volatilitäten in der API- und Pharmaproduktion. In der Fein- und Basischemie ist dieser Trend vergleichbar. Zum einen sind deren Prozesse mit denen der Pharmaindustrie verwoben und sie werden hiervon direkt mit betroffen, zum anderen führt hier der beschleunigte Wandel zu Produktverlagerungen und zu einer vom Abnahmemarkt getriebenen Mikrosteuerung. Das Arbeitsvolumen an indirekten Tätigkeiten wird u. a. durch den Dokumentationsaufwand durch Reach und den Umwelt- und Energiebehörden stark erhöht.
In diesem Spannungsfeld von geforderter Flexibilität in den operativen Prozessen und einem anwachsenden Arbeitsvolumen in den indirekten Prozessen, das geforderte Pensum mit schlank aufgestellten Ressourcen bewerkstelligen zu müssen bewegt sich die Prozessindustrie zunehmend. Umso wichtiger wird die optimale, holistische Steuerung der gesamten Wertschöpfungskette entlang der Supply Chain. Optimal definierte und am Best Practice ausgerichtete Steuerungsparamter in Kombination mit einer realistischen und auf Tagesbasis nachgehaltenen Tagesplanung sind der Schlüssel für stabile Produktionspläne und eine hohe Liefertreue. Eine dadurch ansteigende Gesamtanlageneffektivität (englisch Overall Equipment Effectiveness – OEE) hilft in erster Linie vorhandene Kapazitätsengpässe zu reduzieren und dringend benötigte Freiräume für Instandhaltungsmaßnahmen zu schaffen, damit das Störaufkommen nachhaltig verbessert werden und die Kapazität weiter ausgeweitet werden kann. Der schöne Nebeneffekt der daraus entsteht drückt sich direkt in einer weiteren Stabilisierung der Feinplanung, einer Steigerung der Liefertreue, einer möglichen Reduktion an Lagerbeständen und einer Reduktion der Kosten aus.
Das Herz der Prozessindustrie schlägt in der Produktion
In der Produktion findet i.d.R. der Hauptanteil der Wertschöpfung statt. Hier ist am ehesten zu beobachten, wenn die globalen übergreifenden Prozesse nicht harmonisiert sind. Zur Optimierung und Kostensenkung hat die Prozessindustrie bereits sehr viel getan, um die aus dem Toyota Produktionssystem seit den 90er Jahren bekannten Lean Methoden mit 5S, Just in Time, Kaizen und Gemba, flächendeckend zu installieren. Der OEE zur Steuerung der Gesamtanlagenproduktivität wurde eingeführt. Der kontinuierliche Verbesserungsprozess ist zur Routine geworden.
Eine Studie zum Thema Operational Excellence in der Prozessindustrie, die das Beratungsunternehmen Polarixpartner zwischen April und Juni 2015 durchgeführt hat, zeigt klar, dass in den meisten Unternehmen die klassischen Instrumente wie ein Planungs- und Kennzahlensystem installiert sind. Und dennoch ist der Alltag durch hohe Volatilität und „Firefighting“ geprägt. Dies wird vor allem deutlich durch die eindeutige Aussage: „ ja wir tun das alles…“. Nur weshalb prägt dann trotzdem bei 80 % der befragten Unternehmen das „Firefighting“ immer noch den Alltag. Die Meister und Teilbereichsmeister müssen hier ständig gegenhalten und die Ressourcen steuern. Für Sie ist jedes weitere Tool eine zusätzliche Belastung, wenn es keine praxisgerechten Ergebnisse liefert.
Häufig krankt es an validen Prozessstandards und einer Vorausschaufähigkeit, um mit diesen Instrumenten gezielt steuern zu können. Zeitstandards für die Prozesse sind nur in 31 % der befragten Unternehmen vorhanden und in einigen Fällen sind diese nicht auf Basis durchgeführter Anlagenveränderungen aktualisiert, um eine aussagefähige und stabile Ressourcenplanung aufzusetzen und zur Steuerung geeignete Kennzahlen durch Soll/Ist-Abgleiche zu generieren.
Rollen und Verantwortlichkeiten sind nur in 17 % der befragten Unternehmen hinreichend definiert und werden vollständig gelebt. Ohne klar zugeordnete und gelebte Rollen und Verantwortlichkeiten sind Entscheidungswege zu lang und ineffizient. Dies lähmt die Organisation. Eine zielgerichtete Entwicklung hin zu einer lernenden sowie leistungsorientierten Organisation ist kaum möglich. Überdies sind Redundanzen ein wesentlicher Kostentreiber und häufige Ursache für zunehmende Identifikationsmängel bis hin zur organisatorischen Orientierungslosigkeit.
Ca. 80 % der befragten Unternehmen sollten über eine strukturierte Implementierung von Operational Excellence als ganzheitliches System nachdenken und ihr Managementsystem durch geschlossene Regelkreise auf Best in Class Fähigkeit trimmen. Vor allem die Unternehmen, die bereits den LEAN Baukasten installiert haben und ein regelmäßiges Reporting sowie eine Problemlösungskultur besitzen, haben die nächste Hürde der Vernetzung der Bereiche zu meistern. Auch wenn tägliche Problemlösungsrunden bereits initiiert sind hängt vieles davon ab, wie konsequent die Problemlösungs-Regelkreise geschlossen werden. Sind die definierten und beschlossenen Problemlösungsaktivitäten nur auf ein Symptom ausgerichtet oder zielen diese auf die Wurzel des vorhandenen Problems?
Ein durchgängiges Planungssystem der Supply Chain und somit der Wertströme mit implementierten Kostenoptimierungskreisläufen ist die Thematik der Stunde. Hier sollten die Unternehmen schnell handeln, um im Wettlauf der globalen Märkte zu bestehen und somit den zukünftigen Unternehmenserfolg abzusichern. Die Marktstrategie kann nur so auf die Anforderungen der individuellen Prozesse heruntergebrochen werden und als flexible Größe an die Kundenbedürfnisse gekoppelt veränderlich und dennoch homogen gelebt werden.
Overall Supply Chain Effectiveness
Overall Supply Chain Effectiveness (OSE) ist eine von Polarixpartner entwickelte Kennzahl und Vorgehensweise, die das durchgängige und holistische Planungssystem herstellt, ein Kostenoptimum der Wertströme definiert sowie Mess- und Steuerbarkeit am Kostenoptimum erreicht. Hierbei wird der Reifegrad der Supply Chain auf Produktebene definiert. Eine interne Integration (Reifegrad 2) über die Bereiche Einkauf und Beschaffung, Produktion mit Qualitätskontrolle, Logistik und Vertrieb und die Instandhaltungsbereiche, um die Verfügbarkeit der Assets sicher zu stellen ist die Mindestvoraussetzung für eine funktionierende Supply Chain..
Der OSE definiert sich über die gesamte Wertschöpfungskette und stellt nach TCO (Total Cost of Ownership) Gesichtspunkten das Kostenoptimum als Soll Wert dar. Die Sollwerte werden durch ein Optimierungs-Solver unter vorgegeben Randbedingungen wie Stillstände, Servicelevel, Kampagnengrößen errechnet. Gegen diesen Sollwert, werden die Ist-Materialströme gemessen und bei Abweichungen strukturiert gegengesteuert. Es entsteht eine mess-und steuerbare Supply Chain. Dies erhöht die Forecast- und Planungsstabilität erheblich und ist der wirkungsvollste Hebel dem Phänomen „Firefighting“ zu begegnen und die Effizienz und Effektivität aller Assets – letztendlich der gesamten Value Chain maßgeblich zu steigern.
Anbieter
PolarixpartnerGraf-Siegfried-Str 32
54439 Saarburg
Meist gelesen
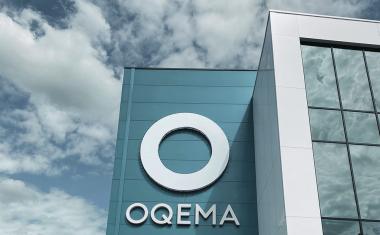
„Wir stellen uns für die Zukunft auf“
Zurück im Familienbesitz rüstet sich Oqema, um die sich bietenden Chancen in der Chemiedistribution zu ergreifen.
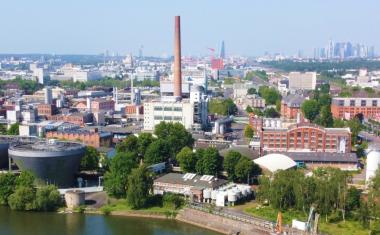
WeylChem Fine Chemicals: Globaler CDMO mit Produktionskapazitäten auf drei Kontinenten
Ein neuer Akteur betritt die Bühne der Feinchemie: WeylChem Fine Chemicals (WCFC), eine global aufgestellte Organisation für die kundenspezifische Entwicklung und Herstellung von Spezialchemikalien (CDMO).
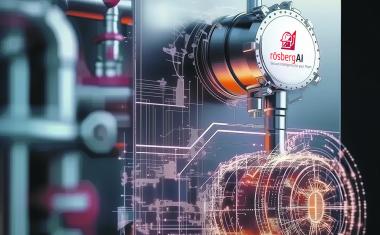
KI im Engineering
Rösberg Engineering hat ein KI-Projekt aufgesetzt; bei dem eine Datenbasis, Infrastruktur und verschiedene Lösungen für KI-gestütztes Engineering entstehen
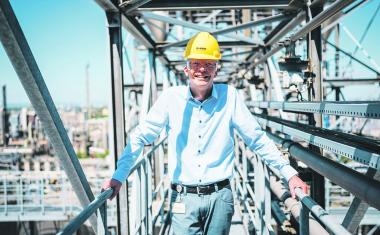
Die Zukunft der Textilindustrie
Textilrecycling: Konzepte und Technologien zur Wiederverwertung von Altkleidern
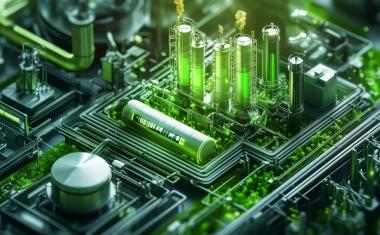
Die Zukunft der Chemieindustrie
Die Chemieindustrie in Deutschland und Europa steht vor erheblichen Problemen. Die hohen Energiekosten und die Nachfrageschwäche setzen viele Unternehmen unter Druck und belasten ihre Wettbewerbsfähigkeit.