Ein Reaktorsystem für alle scale-up-Stufen
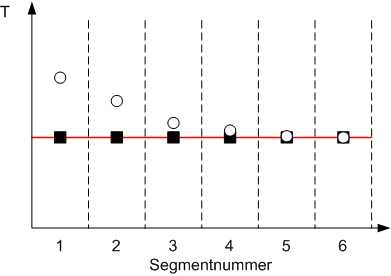
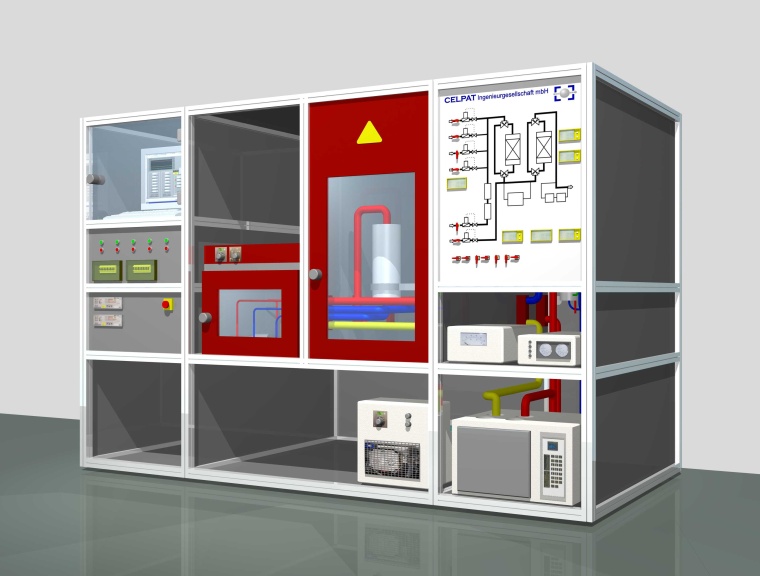
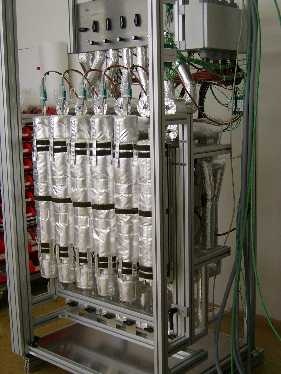

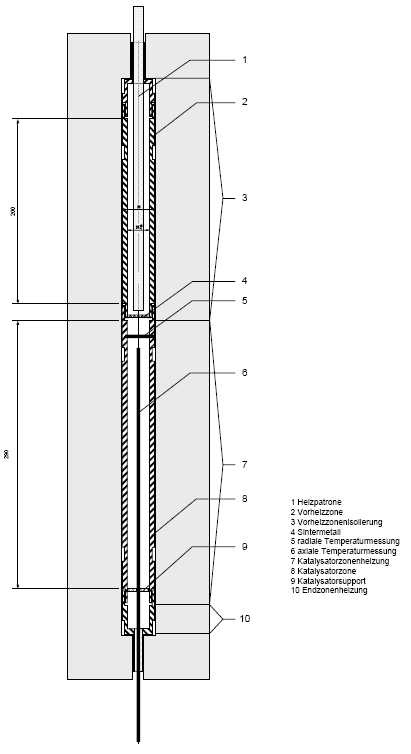
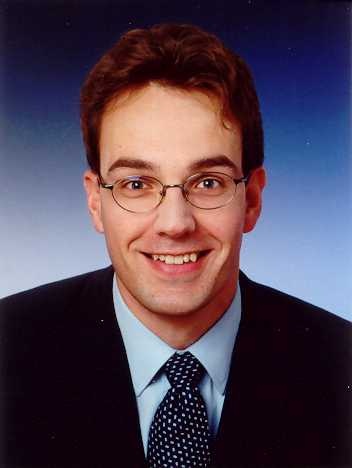
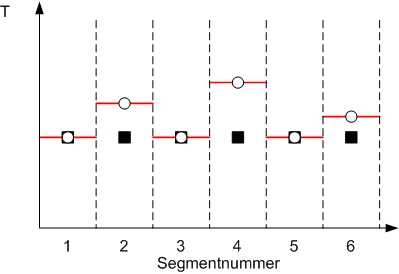
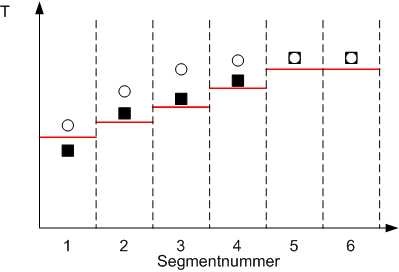
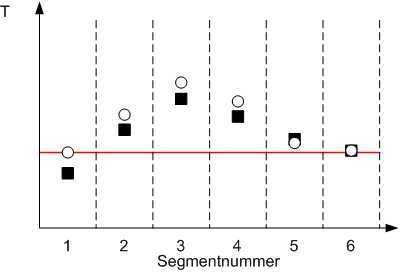
Die technische Katalyse ist die Schlüsseltechnologie der chemischen Industrie. Sie hat heute eine enorme volkswirtschaftliche Bedeutung, wird doch der weitaus größte Anteil (man rechnet ca. 80 bis 90 Prozent) aller chemischen Produkte der Mineralöl verarbeitenden, der chemischen, der pharmazeutischen und der Umweltschutz-Industrie mittels katalytischer Prozesse hergestellt. Die Karlsruher Firma Celpat hat jetzt ein zeit- und ressourcenschonendes Reaktorsystem auf der Basis von mehreren Segmentreaktoren entwickelt, in dem von den chemischen Grundlagen des Katalysators bis zu den Parametern für den Industrieeinsatz alles in einer flexiblen Reaktoranlage ermittelt wird.
Die Fachwelt ist sich einig, ohne Katalyse wären auch die vor uns liegenden Herausforderungen wie verminderter und optimierter Verbrauch der fossilen Ressourcen mit einer Reduktion der umweltbelastenden Schadstoffe sowie eine nachhaltige Herstellung von - Humankapital fördernden - chemischen Produkten und Energie nicht lösbar. In der Natur ist die Katalyse ein weiterverbreitetes Phänomen. Ohne sie gäbe es wohl kaum diese Art von Leben auf unserem Planeten. Aber technisch, sozusagen im Reagenzglas, solche Reaktionen nachzuvollziehen, das war nicht ganz so einfach. Dabei lohnt es sich, einen näheren Blick auf das interessante Phänomen Katalyse zu werfen. In den Jahren der Katalyse-Urväter (Berzelius, Döbereiner) Anfang des 19. Jahrhunderts hatte man beobachtet, dass Wasserstoffgas und Sauerstoffgas, die im Normalfall sehr reaktionsträge sind, sich in ‚Anwesenheit' von Platin unter Wärmeentwicklung zu Wasser verbinden. Katalysatoren beschleunigen also die Bildung von Reaktionsprodukten durch eine Senkung spezieller Energiebarrieren, ohne selbst bei der Reaktion maßgeblich zu erscheinen oder verbraucht zu werden.
Aber sie beschleunigen die Reaktionen nicht nur, sie ‚lenken' sie u.U. auch in eine bestimmte Richtung. So lassen sich als modernes Anwendungsbeispiel aus einem Gemisch von Kohlenmonoxid und Wasserstoff drei Produktwege einschlagen: mittels eines Nickelkatalysators wird Methan hergestellt, mit einem Katalysator bestehend aus Kupfer, Zinkoxid und Aluminiumoxid Methanol und mit einem Eisen- oder Cobalt-Katalysator dagegen Benzin produziert. Wasserstoff und Sauerstoff kommen heute auch in der Brennstoffzellentechnik zum Einsatz um saubere elektrische Energie mit hohem Wirkungsgrad zu erzeugen. Dafür ist aber noch einiges an - auch katalytischer - Entwicklungsarbeit zu leisten.
Katalyseforschung erlebt zweiten Frühling
Viele chemische Reaktionen, von denen man annahm, dass sie technisch nicht durchzuführen seien, sind mittlerweile durch katalytische Unterstützung möglich geworden. Wobei beim Katalyse-Prozess noch lange kein Ende der Entwicklungs- und Optimierungsmöglichkeiten in Sicht ist, im Gegenteil. Die Verbesserung der Effizienz eines Katalysators zeigt sich sofort in entsprechenden Kosten- und Ressourceneinsparungen. Deshalb werden die Katalysatoren für einen bestimmten Prozess einer umfangreichen Optimierung bereits in der Labor- und Technikum-Phase unterzogen, bevor die Anlage dann per scale-up in Produktionsgröße gebaut wird. Dazu werden die katalytischen Eigenschaften Aktivität (die Beschleunigung der Reaktion), Selektivität (die selektive, reaktionslenkende Beschleunigung eines bestimmten Reaktionsweges) und Standzeit (die Lebensdauer) bei unterschiedlichsten Katalysatormaterialien bzw. -formen und in variablen Temperatur- und Druckumgebungen oder Reaktortypen bestimmt. Der Reaktor ist der Teil der Anlage, in dem die chemischen Prozesse ablaufen. Da sich diese Eigenschaften im Allgemeinen gegenseitig beeinflussen, sind zusätzlich Erfahrung und Intuition gefragt, um das Optimum zu finden.
Während die Vergangenheit eher zeitaufwendige, empirische Testmethoden der Katalysatorforschung sah (auf der Suche nach dem optimalen Katalysator zur Ammoniakherstellung soll z.B. A. Mittasch 3000 verschiedene Materialien mit etwa 20000 Testmessungen in zehnjähriger Forschungsarbeit untersucht haben), werden heute vermehrt auch wissenschaftliche Methoden, basierend auf dem besseren Verständnis der chemischen und physikalischen Grundlagen, zusätzlich genutzt. Zusammen mit den sogenannten Hochdurchsatzverfahren (HTE = High-Through-put-Experimentation), bei denen mehrere Katalysatoren gleichzeitig in parallelen Reaktoren getestet werden, bewirkt das eine große Reduzierung von Zeit und Experimenteanzahl in der Größenordnung von weit mehr als Faktor 10.
Geschäftsidee: flexibel einsetzbare Katalyse-Reaktoren
Celpat, eine Technologieausgründung vom Institut für Chemische Verfahrenstechnik der Universität Karlsruhe (ist heute Teil des Karlsruher Instituts für Technolgie (KIT)) und jetzt in der dortigen Technologiefabrik beheimatet), hat sich als Dienstleister genau auf diese modernen Verfahren rund um das Thema Katalyse spezialisiert. Das junge Unternehmen fertigt kundenspezifische Werkzeuge und apparative Lösungen für eine effektive Katalysatorforschung. Geschäftsführer Matthias Pieper: „Auf diese Geschäftsidee kamen wir bei den Katalysatorforschungen und Industrieaufträgen am Institut, bei denen immer die chemischen Reaktionen im Vordergrund standen. Der Apparatebau war ein notwendiges Übel und meist wurden die Geräte zugekauft. Mit einem Landesprogramm für Innovatoren und räumlicher Unterstützung vom Institut wurden uns dann die ersten Schritte in die Selbstständigkeit erleichtert, so dass auch die begonnene Promotion erstmal in den Hintergrund trat." Pieper weiter: „Unsere Kernkompetenzen liegen heute bei Entwurf und Fertigung von kompletten und vollautomatischen Versuchsanlagen im Miniplant-Maßstab für einen weiten Anwendungsbereich in der Katalysatorforschung (Katalysatorscreening, Prozess- und Kinetikstudien). Aber auch Um- und Nachrüstungen bestehender Anlagen oder beratende Unterstützung bei Planung und Konzeption gehören zu unserem Angebot."
Für ein spezielles Endprodukt eines Anwenders im Bereich Katalysatorherstellung erhielt Celpat aktuell den Auftrag zur Entwicklung eines Reaktors für Festkörperkatalysatoren (Splitt, Formkörper, Monolithe und Schäume) im Mengenbereich von ca. 5 - 200 g Katalysatormasse. Die Vorgabe war, dass der Reaktor so flexibel einzusetzen ist, dass zum einen in der parallelen Untersuchung von kleinen Katalysatormengen von 5 - 10 g in sechs bis acht gleichwertigen ‚Reaktorteilen' die intrinsisch kinetischen Parameter der chemischen Reaktion bestimmt werden können. In diesem ‚Screening'-Betrieb im Parallelmodus erfolgt also zur Optimierung der Katalysator-Zusammensetzung und -herstellung die qualitative Beurteilung der katalytischen Eigenschaften der Testmaterialien. Mit einer durch die Parallelschaltung wesentlich reduzierten Anzahl an Versuchsreihen.
Einfache Umstellung vom Screening- auf Kinetik-Betrieb
Zum anderen sollte der gleiche Reaktor die genaue kinetische Vermessung eines Katalysators mit bis zu 200 g im sogenannten Kinetik-Betrieb mit Abschnitts- oder Segmentreaktoren ermöglichen. Im Gegensatz zum hohen Probendurchsatz im Screening-Betrieb werden im Kinetik-Betrieb mit einem geringen Probendurchsatz detaillierte Informationen zum Reaktionsablauf und über die zu erwartenden katalytischen Leistungsdaten im kommerziellen Bereich erfasst. Dabei wird die Effektivität des Katalysators in einer Reaktorumgebung untersucht, die in Bezug auf Geometrie, Heizung/Kühlung und Strömungsverhalten bereits weitgehend den industriellen Reaktoren entspricht, die Katalysatormengen und -formen sind identisch mit der industriellen Anwendung.
Ein solcher flexibel einzusetzender Reaktor deckt somit in einem System die gesamte Bandbreite der typischen scale-up-Stufen bei der Entwicklung und der Bestimmung der Leistungsdaten eines Katalysators ab. Während bisher für die Ermittlung der Parameter meist unterschiedliche Reaktoren eingesetzt werden, die im Design auf die jeweiligen Anforderungen angepasst sind.
In der technischen Realisierung sind für den Screening-Betrieb 6 - 8 Reaktoren mit jeweils eigenständigen Heizungen, Temperaturmess- und Probeentnahmestellen vorgesehen, die über eine gemeinsame Dosierung parallel mit dem Ausgangsstoff (Edukt) beschickt werden. Im Kinetik-Betrieb bilden die 6 - 8 seriell angeordneten Reaktoren einen sogenannten Zapfstellenreaktor mit Messstellen für Temperatur und Gaskonzentration nach jedem Teilsegment. Dabei kann einfach und schnell von den parallel geschalteten Segmentreaktoren in deren Serienschaltung gewechselt werden.
Damit das gesamte System flexibel zu handhaben ist, erhält jedes Reaktorsegment eine eigene Vorheiz-/Kühlzone. Matthias Pieper erläutert: „Die Beheizung des restlichen Segmentteils erfolgt über mehrere Heizzonen, z. B. neben der Vorheizstrecke über die Hauptheiz- und Abheizstrecke. Diese lassen sich unabhängig voneinander betreiben, sodass man also auch pro Reaktorsegment verschiedene Temperaturen fahren kann." Die Temperaturen können dann alternativ an drei Punkten gemessen werden: Nach der Vorheizzone erfolgt die Messung mittels eines verschiebbaren Thermoelements für die Gaseintrittstemperatur in die Katalysatorschüttung. Zweitens ermöglicht ein in der Schüttung axial bewegbares Thermoelement die Aufzeichnung eines Temperaturprofils über die gesamte Schüttung. Und drittens ist die Temperaturermittlung am Schüttungsende realisierbar, was den Vorteil hat, dass in der Schüttung kein Mittelrohr installiert ist, das die Strömung im Reaktorsegment beeinflusst.
Jedes Reaktorsegment mit eigener Heizung
Durch diese flexiblen Temperatureinstellungen jedes Reaktorsegmentes kann das Gesamtsystem sowohl als Reaktor mit konstanter als auch mit segmentweise variierender Wandtemperatur eingesetzt werden (zur Abbildung kommerzieller Reaktoren mit Ein-Zonen- bzw. Mehr-Zonen-Heizung). Damit lassen sich generell verschiedenste Temperaturprofile über das Gesamtsystem erreichen. „Mit unserer Lösung kann man auch ein spezielles Temperaturprofil vorgeben, um den Einfluss variierender Temperaturen z.B. auf den Reaktionsablauf bei verschiedenen Umsätzen zu erforschen", so Pieper. Hierbei könne dann die reale Gaszusammensetzung untersucht werden, die nach einem Teil des Gesamtsystems vorhanden ist (Teilumsatz). Das erübrige den Einsatz bzw. Zukauf von Modellgasmischungen. Zudem, so Pieper, gäbe es Zwischenprodukte, die nicht im Handel erhältlich sind und die deshalb im eigenen Reaktor hergestellt werden müssten.
Unterstützt wird die Flexibilität der Forschungsanlage durch eine entsprechend flexible und streckenweise automatisierte Prozessleittechnik. Denn sowohl Hardware wie Software sind so angelegt, dass sie die größtmögliche Freiheit der Experimente als auch die Erweiterung der Anlage erlaubt. Über eine einfach zu erlernende Makrosprache werden z.B. verschiedene Automatisierungsebenen definiert, wie die Einhaltung von Grenzwerten und deren automatische Variabilität oder die automatische Probenentnahme über Nacht, die dann am nächsten Tag ausgewertet werden können.
Matthias Pieper ist sich sicher: „Durch die hohen Zeit- und Ressourceneinsparungen gehört solchen flexiblen Segment-Reaktorsystemen, in denen von den chemischen Reaktionen bis zu den verfahrenstechnischen Kennzahlen für den kommerziellen Einsatz alle Forschungen in einer Anlage durchgeführt werden können, die Zukunft."
Der Autor Eduard Rüsing ist freier Fachjournalist in Karlsruhe
Technische Eckdaten des Abschnitt-Reaktors:
Anzahl: 6 - 8 Abschnitte (Segmentreaktoren), jeweils einzeln beheizt mit separater Einlaufzone
Temperatur: 200-600°C
Druck: bis 1,49 bar absolut
Reaktordurchmesser: 15-25 mm (fest)
Reaktorlänge: ca. 40 cm pro Teilstück, 20 cm für Katalysator
Reaktorvolumen: gesamt ca. 600 cm3, 420 cm3 für Katalysator (bei 25 mm Reaktor) Teilstück ca. 100 cm3, 70 cm3 für Katalysator (bei 25 mm Reaktor)
Edukte: gas/dampfförmige Kohlenwasserstoffe, Luft, Inertgase
Temperaturmessung: nach Vorheizzone (radial verschiebbar)
nach Katalysatorschüttung (fest)
in der Katalysatorschüttung in Thermoelementrohr (axial verschiebbar)