Bioprozesse simulieren und optimieren
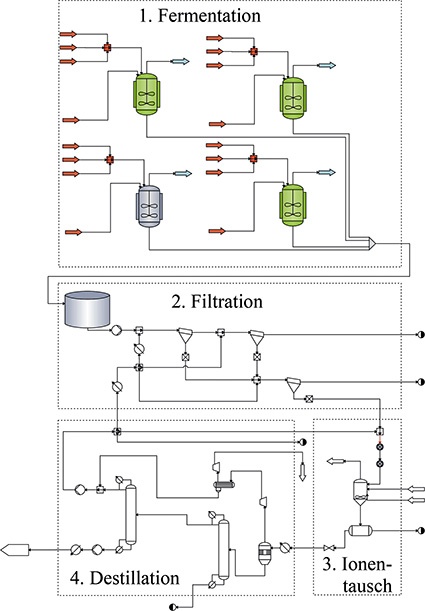
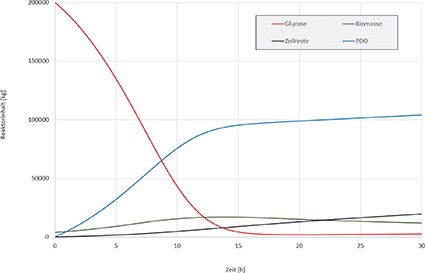
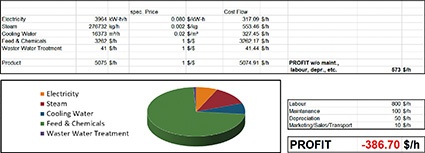
Biotechnologische Prozesse können in Chemcad vollständig abgebildet werden, begonnen bei Upstream Prozessen zur Aufbereitung der Edukte über die kontinuierlich oder batchweise betriebenen Bioreaktoren bis hin zu kontinuierlichen und diskontinuierlichen Downstream Prozessen für die Produktreinigung.
Der Einsatz von Mikroorganismen zur Erzeugung von Grund- und Spezialprodukten der chemischen Industrie gewinnt zunehmend an Bedeutung. Damit werden auch die projektierten und die realisierten Anlagen immer größer und haben mittlerweile die Dimensionen konventioneller chemischer World-Scale Anlagen erreicht. Dies wird deutlich am Beispiel der im Titelbild gezeigten Bioethanol Anlage. Neben den im Vordergrund des Bildes sichtbaren Bioreaktoren werden in biotechnologischen Produktionsanlagen weitgehend verfahrenstechnische Standardausrüstungen, wie Destillationskolonnen, Wärmetauscher, Lagertanke, Pumpen usw. eingesetzt. Die Verwendung von Fließbildsimulatoren zur Prozessgestaltung, zur Dimensionierung der Ausrüstung, zur Prozessoptimierung und zur Simulation des dynamischen Anlagenverhaltens ist bei chemischen und energietechnischen Prozessen üblich.
Besonderheiten biotechnischer Prozesse
Biotechnische Prozesse haben aber zwei Besonderheiten, die eine vollständige Abbildung im Fließbildsimulator zu einer Herausforderung machen:
Die Massenbilanz um den Bioreaktor kann häufig nicht geschlossen werden, da die Details über die intrazellulären Vorgänge in den Mikroorganismen nicht ausreichen bekannt und/oder zu komplex sind, um sie modelltechnisch darzustellen.
Viele Bioreaktoren werden diskontinuierlich im Fed-Batch Modus betrieben während die Downstream Prozesse, zumindest bei großen Anlagen, üblicherweise kontinuierlich gefahren werden.
Daher werden Ansätze benötigt, um mit nicht geschlossenen Massenbilanzen und mit kombinierten Batch-Konti-Prozessen umzugehen. In diesem Beitrag werden solche Ansätze am Beispiel eines Prozesses zur Erzeugung von 1,3-Propandiol (PDO) aus Zuckerrohrsaft aufgezeigt. PDO ist eine Grundchemikalie, die zur Erzeugung von Kunststoffen verwendet werden kann. Ein solcher Prozess wurde von DuPont entwickelt und der entsprechende Kunststoff wird unter dem Namen Sorona vermarktet.
Prozessübersicht
Der PDO Prozess kann in vier Abschnitte unterteilt werden:
- Fermentation
- Filtration
- Ionentausch
- Destillation
In den Fed-Batch Fermentern wird die Glucose aus dem Zuckerrohrsaft von spezialisierten Escherichia coli Bakterien (E.coli) zu PDO umgesetzt. Die Glucose wird von den Bakterien zudem zum Biomasseaufbau und zur Erhaltung verwendet.
In der mehrstufigen Querstromfiltrationsanlage werden Biomasse, Zellreste und große Proteine abgetrennt. Die modellierte Anlage besteht aus zwei Mikrofiltrationsstufen und einer Ultrafiltration.
Der Ionentauscher dient dazu, verbleibende Proteine und die während der Fermentation entstandenen Salze abzutrennen. Zur Regeneration der verwendeten chromatographischen Säulen werden Natronlauge und Schwefelsäure eingesetzt. Dabei wird das System als zyklisch stationär arbeitend angenommen.
Ziel des Downstream Prozesses ist es das PDO mit einer Reinheit von 99,9 Massenprozent zu erzeugen. Dazu wird im Destillationsabschnitt zunächst in einem Flash-Verdampfer ein Teil des in großem Überschuss vorliegenden Wassers entfernt. In einer ersten Destillationskolonne werden PDO und Wasser über den Kopfkondensator von verbleibenden Schwersiedern wie z. B. Resten von Glucose getrennt. Die zweite Destillationskolonne dient der Einstellung der gewünschten Produktreinheit.
Teile des abgetrennten Wassers werden zur Filtration und zum Ionentauscher zurückgeführt. Das vollständige Prozessfließbild ist in Abb. 1 dargestellt.
Fermentation
Die Fermentation von Glucose zu PDO wird in vier Bioreaktoren mit einem Betriebsvolumen von je 400 m3 durchgeführt. Die Zykluszeit beträgt 30 Stunden und das Reinigen und Füllen eines Reaktors dauert 10 Stunden. Damit ist alle 10 Stunden ein Batch vollendet und der jeweilige Reaktorinhalt wird in den Zwischentank überführt.
Die in den Bioreaktoren eingesetzten E.coli Bakterien sind auf die Erzeugung von PDO aus Glucose spezialisiert. Nach dem in den stöchiometrischen Gleichungen 1 bis 4 dargestellten Reaktionsnetzwerk benötigen die Bakterien neben Glucose (Substrat /S) Stickstoff (bereitgestellt über wässrige Ammoniaklösung /N) und Acetat (A), um Biomasse (X) aufzubauen. Acetat fällt wiederum bei der Erzeugung von PDO als Nebenprodukt an, siehe Gleichung 2. In Gleichung 3 ist der Substratverbrauch zur Erhaltung der lebenden Biomasse dargestellt während, Gleichung 4 den Verfall der Biomasse zu toter Biomasse bzw. Zellresten (DX) beschreibt.
S + 4.5 O2 + N + 2 A ➝ 5 X + 6.5 H2O + 5 CO2
5 S + 4 O2 ➝ 6 PDO + A + 4 H2O + 10 CO2
S + 6 O2 ➝ 6 H2O + 6 CO2
X ➝ DX
Die Geschwindigkeiten der Reaktionen (1) und (2) werden mit einem um Edukt Limitierungen erweiterten Monod Ansatz entsprechend den Gleichungen 5 und 6 beschreiben.
Die Reaktionen 3 und 4 werden als Reaktionen erster Ordnung bezüglich der Biomassekonzentration X modelliert. Die molstöchiometrischen Koeffizienten stehen in Zusammenhang mit der elementaren Zusammensetzung der Biomasse. Der hier gewählte Ansatz der C1 Modellierung ergibt die Definition von
X := C1H2O1/2N1/5. Dieses Ergebnis steht in guter Übereinstimmung mit Elementaranalysen für E.coli Stämme. Die stöchiometrischen Koeffizienten wurden so gewählt, dass die in Tabelle 1 zusammengefassten Ertragskoeffizienten Y zu den veröffentlichten Daten dieses speziellen Prozesses passen.
Ertragskoeffizient Molspezifisch [mol/mol] Massenspezifisch [kg/kg]
YX/S 5 0,69
YX/A 2,5 1,04
YX/N 5 7,35
YX/O 1,1 0,87
YPDO/S 1,2 0,51
YPDO/O 1,5 3,56
YA/S (PDO Produktion) 0,2 0,07
Tab. 1: Ertragskoeffizienten des in den Gleichungen 1 bis 4 dargestellten Reaktionsnetzwerks
Während der Fed-Batch Fermentation werden dem Bioreaktor kontinuierlich Luft (O-Lieferant), Zuckerrohrsaft (S-Lieferant), Ammoniaklösung (N-Lieferant) und Essigsäure (A-Lieferant) zugeführt. In Abb. 2 ist der sich über die Zeit verändernde Reaktorinhalt für einen Batch-Zyklus aufgetragen.
Filtration
Aus dem Zwischentank wird kontinuierlich ein fixer Massenstrom abgezogen und der Filtration zugeführt. Die Querstromfiltrationsanlagen werden mittels Filterkurven modelliert, aus denen sich ergibt wie hoch der benötigte transmembrane Druck (TMP) bezogen auf den gegebenen Flux durch die Membran (TMF) ist. Damit kann die benötigte Pumpleistung ermittelt werden.
Der Bedarf an elektrischer Pumpenergie kann also mit der Vorwärmtemperatur und der Menge an zurückgeführtem Wasser beeinflusst werden. Die erreichten Abscheidegrade resultieren aus den Membranparametern und den Partikelgrößenverteilungen der beiden Feststoffe X und DX.
Ionentauscher
Das von Feststoffen befreite Gemisch wird den Säulen des Ionentauschers zugeführt. Hier werden gelöste Salze und verbleibende Proteine abgetrennt. Modelliert wird in diesem Fall allerdings nur die Umsalzung und Entfernung der während der Fermentationen gebildeten Salze des Ammoniaks und der Essigsäure. Die für die Regeneration der Säulen benötigten Mengen an Natronlauge und Schwefelsäure werden aus einfachen stöchiometrischen Beziehungen berechnet.
Destillation
Nach der Entfernung der Salze und Proteine im Ionentauscher muss das PDO noch von verbleibenden Schwersiedern befreit und aufkonzentriert werden. Modelliert wird an dieser Stelle nur der Schwersieder Glucose, wobei im realen Prozess noch von weiteren schwersiedenden Komponenten auszugehen ist. In einem ersten Flashverdampfer wird ein Teil des Wassers durch Drucksenkung und Wärmezufuhr zusammen mit den gelösten Gasen Stickstoff, Sauerstoff und CO2 vom Flüssigstrom getrennt. Da dies bei Unterdruck geschieht muss der Abdampf des Verdampfers verdichtet werden. Danach wird Wasser auskondensiert bevor die Inertgase in einer weiteren Verdichtungsstufe auf Umgebungsdruck gebracht werden.
In der ersten Destillationskolonne wird das flüssige Gemisch verdampft und die Leichtsieder Wasser und PDO werden im Kopfkondensator kondensiert. Dieses Kopfprodukt wird der zweiten Destillationskolonne zugeführt in der Wasser als Leichtsieder vom Sumpfprodukt PDO getrennt wird.
Produktionskosten und Wirtschaftlichkeitsrechnung
Die Simulationsergebnisse werden über die in Chemcad integrierte Data Map Funktionalität an eine Excel Tabelle übertragen. Mit spezifischen Preisen für Zuckerrohrsaft, elektrische Energie, Dampf, Kühlwasser und andere Verbrauchsmaterialien können die Betriebskosten (OPEX) detailliert berechnet werden. Zusammen mit dem aktuellen Marktpreis für PDO und den anfallenden fixen Kosten kann dann der aktuelle Profit der Anlage ermittelt werden. Unter Verwendung der vorgegebenen Werte für die 19 Designvariablen des Prozesses ergibt sich ein Verlust von -386,70 $/h, siehe Abb. 3.
Die Produktionsanlage arbeitet also nicht wirtschaftlich. Die Erhöhung des Profites durch Veränderung der Designvariablen ist Gegenstand des 4. Process Simulation Cups (siehe Infokasten). Mit dem aktuell besten Lösungsvorschlag der Teilnehmer wird ein Profit von 204 $/h erreicht (Stand April 2018). Der Profit konnte also um ca. 590 $/h erhöht werden! Dabei wurden bisher lediglich Designvariablen aus dem Bereich der Destillation verwendet.
Fazit
Biotechnologische Prozesse können in Chemcad vollständig abgebildet werden, begonnen bei Upstream Prozessen zur Aufbereitung der Edukte über die kontinuierlich oder batchweise betriebenen Bioreaktoren bis hin zu kontinuierlichen und diskontinuierlichen Downstream Prozessen für die Produktreinigung.
Vorteilhaft in Chemcad sind dabei der einfache Wechsel zwischen dem stationären und dem dynamischen Simulationsmodus, die intuitive Einbindung von Excel Tabellen sowohl als Grundoperation im Fließbild als auch zur Auswertung der Simulationsergebnisse und der flexible, robuste und einfach zu bedienende generische Rührkesselreaktor, der hier als Fed-Bach Bioreaktor verwendet wurde.
Der Einfluss der verschiedenen Betriebsparameter auf die Verbräuche der Anlage und auf Produktmenge und Qualität kann schnell mittels Parameterstudien erfasst werden. Die detaillierte Auswertung von Key Performance Parametern wie bspw. dem Profit der Anlage in Excel Tabellen kann dann bspw. zur Optimierung der Wirtschaftlichkeit des Prozesses verwendet werden.
Anbieter
Chemstations Europe GmbHUnter den Linden 21
10117 Berlin
Meist gelesen
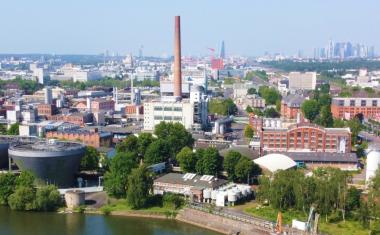
WeylChem Fine Chemicals: Globaler CDMO mit Produktionskapazitäten auf drei Kontinenten
Ein neuer Akteur betritt die Bühne der Feinchemie: WeylChem Fine Chemicals (WCFC), eine global aufgestellte Organisation für die kundenspezifische Entwicklung und Herstellung von Spezialchemikalien (CDMO).
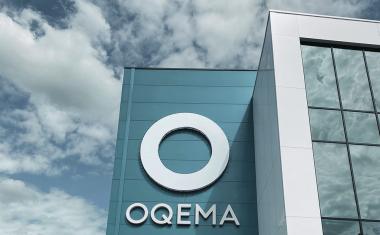
„Wir stellen uns für die Zukunft auf“
Zurück im Familienbesitz rüstet sich Oqema, um die sich bietenden Chancen in der Chemiedistribution zu ergreifen.
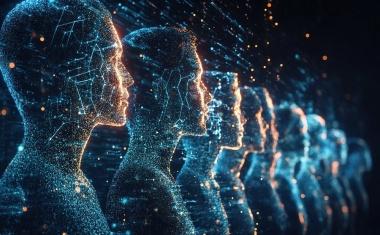
CHEMonitor 01-2025 – Künstliche Intelligenz und Demografie
Das aktuelle Trendbarometer CHEMonitor beleuchtet das Zusammenwirken des demografischen Wandels und den Einfluss der künstlichen Intelligenz (KI) auf die Chemie- und Pharmaindustrie.
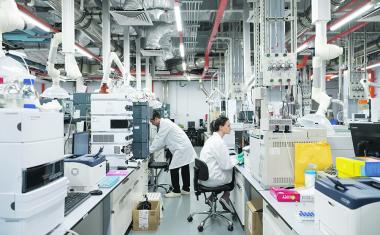
Cyberresilienz – vom Faktor Mensch bis zu Audits
Die europäische Richtlinie zur Sicherheit von Netz- und Informationssystemen (NIS 2) dient der Angleichung des IT-Sicherheitsniveaus in allen EU-Staaten
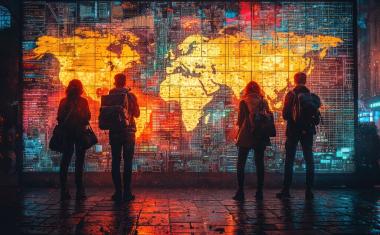
Optimismus nicht nur als moralische Pflicht
Roman Gaida, CSO von Bürkert, erläutert, wie mittelständische Unternehmen wachsende Herausforderungen durch disruptive Veränderungen und Wirtschafts-Protektionismus meistern können