Auch die Chemie kann Gas geben
Managementansätze, wie sie zum Beispiel in der Automobilindustrie Standard sind, werden als holistisches System vorgestellt. Wie lassen sich Veränderungen gezielt umsetzen? Wie entsteht eine Leistungskultur?
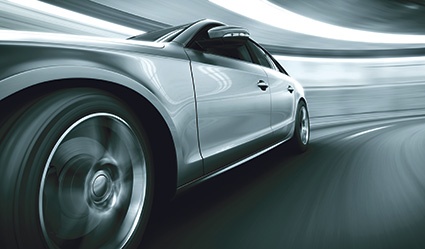
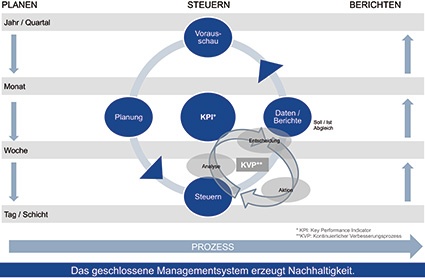
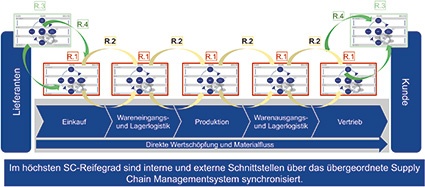
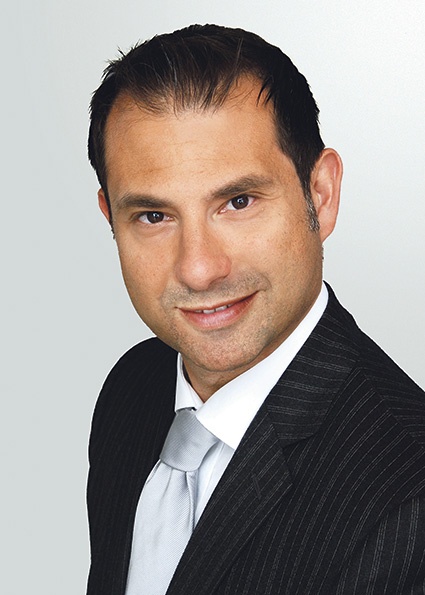
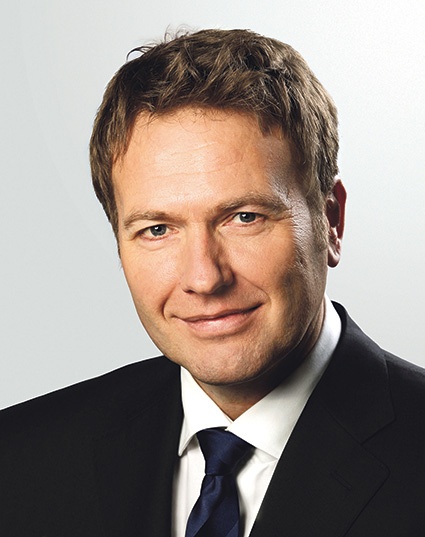
Angefangen von der Produktentstehung über den gesamten Produktlebenszyklus lassen sich diese Ansätze auf alle Branchen übertragen – auch auf die Prozessindustrie. Das Ergebnis ist eine wettbewerbsfähige Supply Chain.
Die Wertschöpfung in der Prozessindustrie erschließt sich bei einem Blick in die Produktionsbereiche zunächst nicht so eindeutig. Während in der Automobilindustrie Fließbänder laufen und sich das Produkt mit jedem Schritt zu einem fertigen Automobil oder zu einem Zulieferteil entwickelt, ist der visuelle Eindruck in der Pharma- und Chemie-Industrie ein anderer, von Verpackungslinien einmal abgesehen. Was hier Teile und Automobile sind, sind dort Produkt- und Teilprodukt-Massenströme, bzw. Tabletten und Liquida.
Doch trotz vieler grundsätzlicher Unterschiede in der Prozessgestaltung, der Wertschöpfung sowie der Entwicklungsanforderungen und -zeitleisten, sind elementare Ansätze zur Prozessgestaltung und deren Steuerungsmechanismen gut übertragbar, um notwendige Veränderungen zu meistern.
Individualisierung verändert Supply-Chain-Management
Führende Unternehmen der pharmazeutischen- und chemischen Industrie weltweit sehen sich mit einer neuen Realität konfrontiert. Während in früheren Zeiten Wertschöpfung auf intellektuellen Eigenschaften und Marktexklusivität beruhte und Produktqualität als wesentliches Kriterium galt, ist die neue Realität durch ein sich stark veränderndes Marktumfeld in Richtung kundenspezifischerer, individuellerer Produkte und sinkender R&D-Produktivität gekennzeichnet. In der Folge rückt das Thema Kosten und damit verbunden ein stetig wachsender Kostendruck in den Vordergrund. Gerade Pharma-Firmen und größtenteils auch Chemie-Unternehmen treten somit in eine Epoche ein, in der sich andere Industrien, wie die Automobilindustrie, seit Dekaden befinden. Das bedeutet aber auch, dass diese Unternehmen von anderen Industrien lernen und basierend darauf Operational Excellence und Produktionseffizienz als Grundstein jeder Operations-Strategie manifestieren müssen, wie es in der Automobilindustrie schon längst Standard ist.
In der Automobilindustrie nehmen Planungshorizonte ab, was u. a. dadurch getrieben wird, dass Modellpaletten immer breiter werden (häufig um die 30 Varianten pro OEM) und dabei unzählige Konfigurationsmöglichkeiten wählbar sind. Um dem scharfen Wettbewerb Stand zu halten, werden Lagerkosten und Lagerzeiten auf ein Minimum reduziert. In der Folge müssen vor allem die direkt an den OEM liefernden Tier-One-Lieferanten in kürzer werdenden Abständen Teile und Komponenten an den Produktionsstandorten bereitstellen. Im Falle von unzureichenden Prozessfähigkeiten bzw. Fehlern in der Planungs- und Logistikkette wird hier auch die Belieferung mittels Helikopter als letztes Mittel eingesetzt, damit die Bänder beim OEM nicht stillstehen – kostentechnisch ein Desaster.
Zusammenfassend lässt sich festhalten, dass in der gesamten Industrielandschaft aufgrund des sich beschleunigenden Wandels und der zunehmend globalen Vernetzung die Anforderungen an Produktions- und Supply-Chain-Management gepaart mit steigenden Flexibilitätsanforderungen an die Unternehmen deutlich verändern werden. Für die Unternehmen bedeutet das, ihre Strategien in kürzeren Abständen anzupassen und ihre Dynamik mit starkem Durchgriff auf alle Prozessebenen deutlich zu erhöhen.
Die Automobilindustrie hat es geschafft, sich sehr früh diesem Wandel anzupassen und ist heute die Industrie mit dem höchsten prozessualen Reifegrad. Für die Pharma- und Chemie-Industrie gilt: Erfolgreicher wird letztendlich derjenige sein, der die notwendigen Veränderungen in seiner Organisation als erster konsequent umsetzt, sprich: selbstlernende Strukturen im Sinne von Leistungsorientierung und einem Kostenbewusstsein angedeihen lässt. Dies bedeutet: Weg von statischen Herstellprozessen und einer „das haben wir schon immer so gemacht“-Mentalität hin zu einer dynamischen und sich kontinuierlich verbessernden Organisation.
Industrieübergreifender Best Practice
Wirkliche Veränderung kann nur in einem sich proaktiv regulierendem System erfolgreich umgesetzt und gelebt werden. Hierfür braucht es zunächst Konstanten wie z. B. klare Rollen und Verantwortlichkeiten in den Kernprozessen. In regelmäßigen Abständen werden diese Prozesse durch die Verantwortlichen einer Soll-Ist-Bewertung unterzogen. Bei Abweichungen werden die Gründe eruiert und strukturiert Maßnahmen zur Verbesserung eingeleitet. Dieser Mechanismus erfolgt über die gesamte Prozesslandschaft des Unternehmens, von der Strategieentwicklung über die Umsetzung auf allen Prozessebenen bis hin zur Steuerung der operativen und administrativen Prozesse. Das Prinzip dieser Managementprozesse ist denkbar einfach und basiert auf den folgenden Systemelementen: Vorausschauen, Planen, Steuern und Berichten – als Grundstruktur eines Managementsystems. Elementar wichtig dabei ist, dass die Prozesse klar definiert, Planungen harmonisiert und zur Steuerung geeignete, die Unternehmensstrategie wiederspiegelnde Kennzahlen definiert werden. Erst die Nutzung dieser Systemelemente in geschlossenen Regelkreisen auf allen zeitlichen und hierarchischen Ebenen befähigt das Unternehmen, seine Strategie nachhaltig und effizient umzusetzen.
Die Einführung solcher Managementsysteme – und die damit verbundene konsequente Nutzung geschlossener Steuerungs- und Kommunikationsregelkreise – erzielt mehrfach nachgewiesen Kosteneinsparungen von 10 - 30%.
Das Managementsystem ist die Grundlage, in Organisationen nachhaltig eine Leistungskultur zu etablieren. Die Disziplin und der stete Wille zur Veränderung wird durch messbare Ergebnisse manifestiert. Der Aufwand, ein solches System im eingeschwungenen Zustand zu betreiben, ist vergleichsweise gering, da über die entstehende Transparenz und die implementierten Steuerungsmechanismen im Sinne kontinuierlicher Verbesserungsprozesse Redundanzen und Verlustzeiten vermieden werden. Der Aufwand, ein solches System nachhaltig zu implementieren, ist mitunter nicht unerheblich und erzeugt Widerstände – gerade in Unternehmen mit langjährig eingefahrenen Strukturen. Notwendige kulturelle Umbrüche müssen frühzeitig und über den gesamten Prozess der Implementierung begleitet werden.
Pharma- und Chemie-Industrie muss Gas geben
Der wesentliche Vorteil, Managementsysteme zu nutzen – vom monetären Aspekt einmal abgesehen – ist die messbare Steuerung der Kundenzufriedenheit. Es entstehen definierte Strukturen, die Vorausschaubarkeit und Planbarkeit in einer Welt ermöglichen, die bislang augenscheinlich als wenig oder gar nicht planbar erschien.
Klassische Elemente zur Prozessverbesserung, z. B. aus dem Lean und Six Sigma-Werkzeugkasten, erzeugen für sich genommen, d. h. ohne Bestanteil der o. g. Managementstruktur zu sein, häufig mehr Verwirrung als echten Nutzen, weil eine systematische Vernetzung fehlt. Somit bleibt die gewünschte Wirkung häufig aus und der Aufwand wird nicht mit dem Return auf dieses Investment belohnt. Das Managementsystem ist der Treiber und Garant für strukturierte Veränderungen. Die Anwendung klassischer Change-Management-Methoden allein kann dies nicht bewirken. Auf der anderen Seite ist für die Einführung eines Managementsystems eine gezielte Change-Unterstützung durch Experten sehr hilfreich und in vielen Organisationen auch notwendig, um Mitarbeiter und oftmals auch das Management von ihrem gewohnten Verhalten hin zu einer transparenten Leistungskultur zu bewegen.
Produktentstehungsprozess und Supply Chain
Hier kann die gesamte fertigende Industrie von der Automobilindustrie lernen. Kaum eine Branche, außer der Smartphone- & Tabletindustrie, unterliegt derart vielen Veränderungen. Modellzyklen von unter vier Jahren, Technologie-Innovationen und -Revolutionen wie die digitale Vernetzung halten Einzug, um als Komposition in hochinnovativen Produkten einem harten Wettbewerb in globalen Märkten zu bestehen. Die Kosten würden ohne strukturiertes Kosten- und Supply-Chain-Management längst nicht mehr beherrschbar sein. Die Automobilindustrie hat hier einen vergleichsweise hohen Reifegrad der Supply Chain erreicht, der je nach Ausmaß der Zusammenarbeit, von der gelegentlichen Auftragsabwicklung bis hin zur synchronisierten Zusammenarbeit, bereits in den frühen Phasen der Produktentstehung etabliert ist.
Während in der Automobil- und Zulieferindustrie, von der Produktidee bis zum Start der Serienproduktion (SOP), Entwicklungszyklen von 2 - 4 Jahren liegen, sind z.B. in der forschenden Pharma-Industrie 10 Jahre und mehr ein übliches Zeitfenster. Die präklinischen und klinischen Studien der Phase 1 bis 3 sind hierbei regulationsgetrieben als Prozess ausdifferenziert und qualitätsseitig exzellent gesteuert. Die frühen Phasen der Produktentstehung, also die ersten 3-5 Jahre sind hingegen in der Regel wenig prozessorientiert und organisatorisch oftmals in verschiedenen Bereichen mit zumeist schlecht funktionierenden Schnittstellen aufgestellt. Gerade hier kann ein frühzeitiges Einbinden aller Bereiche und eine definierte Steuerung der Entwicklungsprogramme Zeit und Kosten einsparen. Das stärkt die Wettbewerbsfähigkeit in doppeltem Maße: time to market könnte von 10 auf 7-8 Jahre verkürzt und die Kosten um 20-30% gesenkt werden.
Der zentrale Unterschied zwischen der Prozess- und der Automobilindustrie liegt in den unterschiedlichen Eigenschaften der Prozesse: In der Automobilindustrie sind die Entwicklung auf Basis bestehender Technologien und die Montage über alle Phasen des Produktlebenszyklus gut plan- und beherrschbar. In der Prozessindustrie ist dies anders. Die Prozesszeiten können schwanken, da viele häufig nicht oder nur unzureichend beeinflussbare Faktoren die Cycle time beeinflussen. Dies macht sich insbesondere beim Transfer von Produkten aus dem Entwicklungsstatus in die Serien-Technologie (upscaling) bemerkbar. Gerade deswegen ist eine klar definierte und gut steuerbare Prozesslandschaft in dieser Industrie umso wichtiger. Auf Basis von Erfahrungswerten lassen sich für die meisten Prozesse relativ genaue Vorhersagen treffen.
Fazit
In Zeiten des beschleunigten Wandels müssen auch grundlegende Strukturen beschleunigt umgesetzt werden. Eine sich an Gegebenheiten anpassende Struktur wie das Managementsystem ist die ideale Basis zukünftige Veränderungen zu treiben und deren Wirkung als messbares Resultat auf allen Ebenen sicherzustellen. Ein Managementsystem schafft Nachhaltigkeit.
Anbieter
PolarixpartnerGraf-Siegfried-Str 32
54439 Saarburg
Meist gelesen
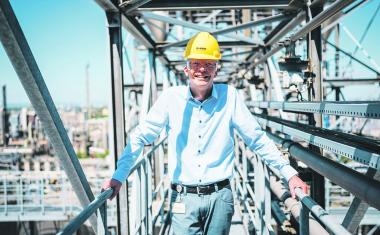
Die Zukunft der Textilindustrie
Textilrecycling: Konzepte und Technologien zur Wiederverwertung von Altkleidern
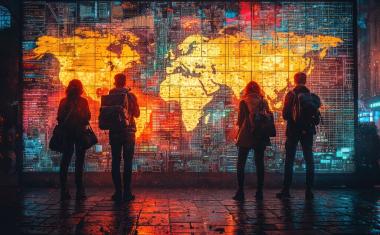
Optimismus nicht nur als moralische Pflicht
Roman Gaida, CSO von Bürkert, erläutert, wie mittelständische Unternehmen wachsende Herausforderungen durch disruptive Veränderungen und Wirtschafts-Protektionismus meistern können
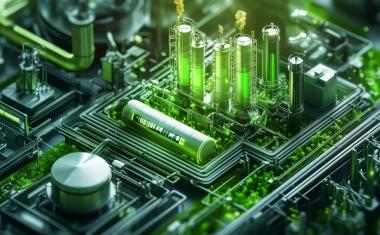
Die Zukunft der Chemieindustrie
Die Chemieindustrie in Deutschland und Europa steht vor erheblichen Problemen. Die hohen Energiekosten und die Nachfrageschwäche setzen viele Unternehmen unter Druck und belasten ihre Wettbewerbsfähigkeit.
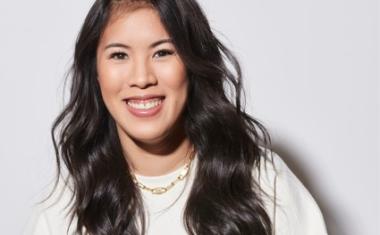
Wissenschaftliche Fakten kreativ verpackt und emotional präsentiert
Interview mit der Chemikerin, Wissenschaftsjournalistin, Fernsehmoderatorin, YouTuberin und Autorin Mai Thi Nguyen-Kim zur Rolle von Wissenschaft in unserer Gesellschaft.
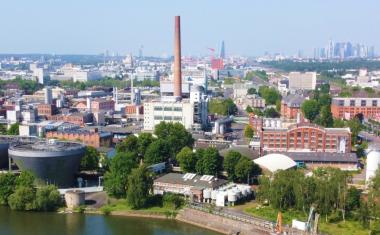
WeylChem Fine Chemicals: Globaler CDMO mit Produktionskapazitäten auf drei Kontinenten
Ein neuer Akteur betritt die Bühne der Feinchemie: WeylChem Fine Chemicals (WCFC), eine global aufgestellte Organisation für die kundenspezifische Entwicklung und Herstellung von Spezialchemikalien (CDMO).