Weniger ist mehr
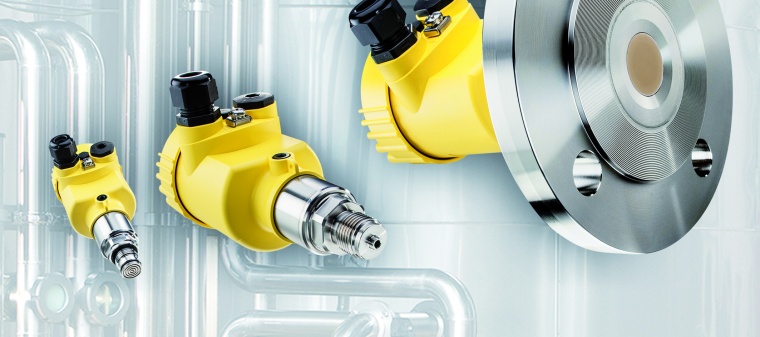
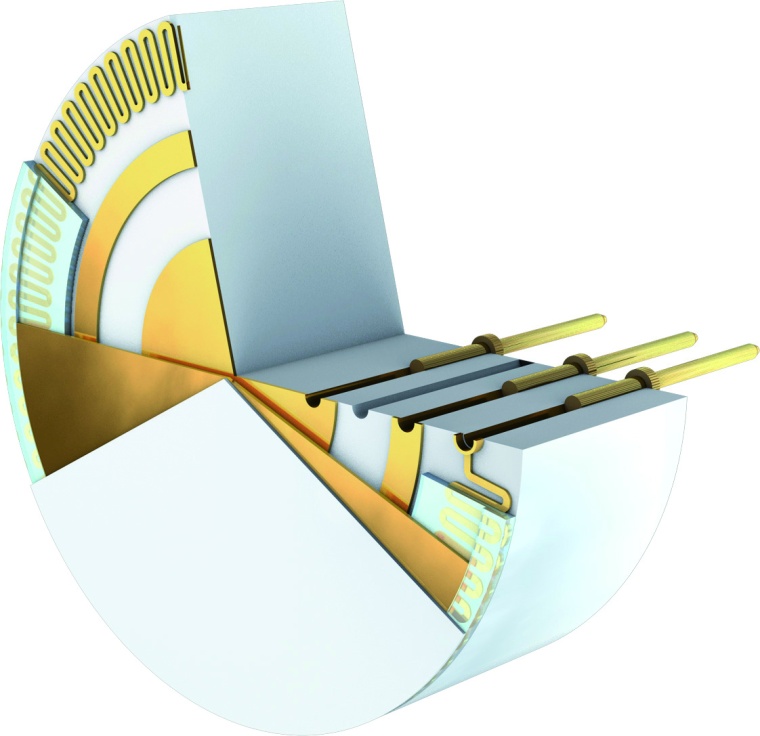
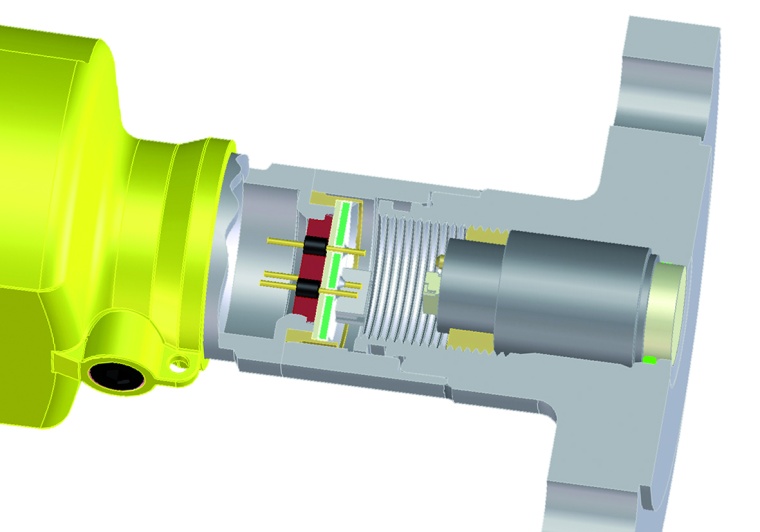
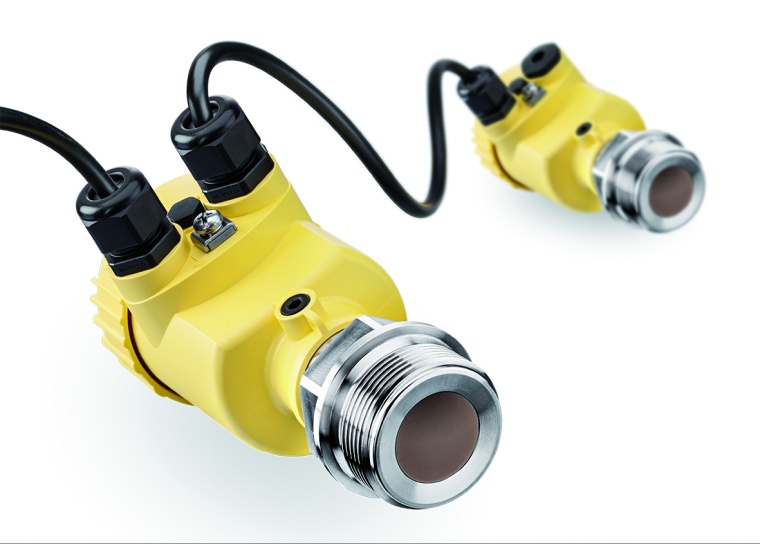
Mit drei Prozessdruckmessumformern deckt Vega das Anwendungsspektrum ab: Mit einem Alrounder, einem für hohe Drücke und einem für hohe Temperaturen und aggressive Medien.
Mit der Vegabar Serie 80, die konsequent nach SIL entwickelt wurde, hat Vega das Druckportfolio auf den neuesten Stand der Technik gebracht. Ab sofort haben die Schwarzwälder nur noch drei Prozessdruckmessumformer im Programm, die das komplette Anwendungsspektrum abdecken können: Der Allrounder Vegabar 82 mit keramischer Messzelle löst
60 -70 % aller Anwendungen. Bei hohen Drücken beweist der Vegabar 83 mit metallischer Messzelle, was er kann. Der Vegabar 81 mit klassischem Druckmittler ist das Gerät der Wahl bei hohen Temperaturen und aggressiven Medien.
Die Geräteplattform plics, die seit Jahren viele Fans hat, bietet für alle Messverfahren von Vega, ob Druck oder Füllstand, ein durchgängiges Gehäuse-, Elektronik- und Bedienkonzept über den gesamten Lebenszyklus eines Messgerätes - von der Auswahl und Bestellung über die Montage und Inbetriebnahme bis hin zu Wartung und Service.
Sogenannte Familien-DTMs erleichtern dem Anwender die Arbeit. Benötigte man früher für die Geräteintegration jedes einzelnen Messgerätes einen speziellen Treiber, gibt es in Zukunft für eine Gerätelinie lediglich noch einen DTM.
Volles Vertrauen in die Keramik
Bei beiden Arten von Druckmesszellen, ob metallisch oder keramisch, kann das Unternehmen große Fortschritte vermelden. Die größeren Technologiesprünge machten jedoch die Aushängeschilder von Vega, die keramischen Messzellen Certec. Nur wenige Anbieter haben keramisch-kapazitive Zellen im Portfolio, noch weniger besitzen das Know-how diese selbst zu produzieren. 80 % der verkauften Geräte arbeiten mit keramischen Druckmesszellen. Bei einem Großteil der Anwendungen lassen sich prinzipiell beide Technologien einsetzen. Doch Vega ist fest davon überzeugt, dass die Keramik in vielen Fällen die bessere, weil robustere und langlebigere Technologie ist.
Gewusst wie
Die Schwarzwälder schwören auf ihre keramischen Messzellen, aber diese haben auch einige weitläufig bekannte Schwachstellen, wie z. B. ihre Temperaturschock- und Feuchteempfindlichkeit. Bis jetzt. Denn mit der Temperaturschockkompensation ist dem Hersteller eine technologische Meisterleistung gelungen, die bereits zum Patent angemeldet ist.
Nach starken Temperatursprüngen kann es bei keramischen Messzellen minutenlang dauern, bis der Sensor wieder zuverlässige Messwerte liefert. Oftmals wussten die Anwender überhaupt nicht, dass der Sensor einen Temperaturschock hat und dadurch falsche Werte überträgt. Bei den keramischen Messzellen von Vega können die Kunden heute absolut sicher sein, dass diese den richtigen Messwert liefern, weil nun selbst sehr schnelle Temperaturänderungen der Druckmessung nichts mehr anhaben können.
Das Geheimnis hinter der Temperaturschockkompensation: Ein zweiter, zusätzlicher Temperatursensor auf der Rückseite der Certec-Messzelle, den der Komplettanbieter für Druck in einem technisch überaus anspruchsvollen Prozess in der Glasnaht direkt hinter der Keramikmembran aufbringt. Durch seine exponierte Position kann dieser minimale Temperaturänderungen detektieren. Über einen speziellen Algorithmus lässt sich der Temperaturschock vollständig kompensieren.
Der zweite Sensor direkt am Prozess ermöglicht auch eine Temperaturmessung von hoher Güte mit einer Genauigkeit von ±2 K. Ein Temperatursignal konnten bereits die Vorgänger liefern. Dieses eignete sich aber durch die Langsamkeit des Sensors nur für Lagertanks mit relativ stabiler Temperatur. Mit der neuen Generation von Sensoren können Anwender oftmals auf einen separaten Temperatursensor verzichten und somit bares Geld sparen.
Die typische Feuchtigkeitsempfindlichkeit der Keramik konnte das Unternehmen ebenfalls erheblich senken, indem bei der neuen Generation die gesamte Oberfläche des Mess- und Referenzkondensators mit einer hauchdünnen Glasschicht überzogen wird.
Innovative Keramik
Ein weiteres herausragendes Merkmal der Keramik von Vega ist die hohe Überlastfestigkeit von bis zu Faktor 200 - mehr als das Doppelte,
was andere Keramiken können. Auch beim Temperaturbereich wurde ein Fortschritt erzielt. War früher bei 120 °C Schluss, so kann die Certec-Messzelle nun Temperaturen von bis zu 130 °C widerstehen.
Die neue Generation keramischer Messzellen besticht auch durch einen sehr kleinen Messbereich von bis zu 25 mbar (vorher
100 mbar). Und das ohne elektronischen Turndown - bis dato einzigartig. Nach oben ist der Messbereich ebenfalls gewachsen, von bisher 60 auf 100 bar, was die Einsatzmöglichkeiten des Standardgerätes Vegabar 82 deutlich erweitert.
Trotzt mühelos abrasiven Medien
Die Certec-Messzelle ist die einzige keramische Messzelle auf dem Markt, die einen frontbündigen Einbau ermöglicht, weil die radiale Dichtung zurückversetzt liegt und gegen das Medium geschützt ist. Diesen Vorteil kann diese insbesondere in abrasiven und korrosiven Medien bei Anwendungen in der Chemie, Petrochemie oder Papier- und Zellstoffindustrie ausspielen. Die Papierindustrie hat dies längst erkannt, weltweit sind dort in den Produktionsanlagen mehr als 20.000 Messstellen installiert. Auch Anbackungen sind kein Thema mehr, da sich der Sensor im Füllgutstrom ganz einfach selbst reinigt.
Sicherheit ist oberstes Gebot
In einigen chemischen Prozessen kommen extrem toxische Stoffe zum Einsatz. Design und Funktionssicherheit müssen hier besondere Bedingungen erfüllen. Ein redundantes Dichtungskonzept und die Auswahl hochbeständiger Werkstoffe geben den Anwendern die notwendige Sicherheit. Würde das hochgiftige Medium durch die Messzellendichtung in den Anschlussraum gelangen, wären Mensch und Umwelt gefährdet. Die sogenannte „Second Line of Defense" trennt Messzelle und Elektronikraum zusätzlich durch eine gasdichte Glasdurchführung. So ist bei der Messung von Prozessen mit stark toxischen Medien, wie z. B. Phosgen, erhöhte Sicherheit gewährleistet. Sowohl der Vegabar 82 als auch der Vegabar 83 sind optional mit dieser Sicherheitsfunktion erhältlich. Die beiden vollverschweißten Sensormodule mit „Second Line of Defense" können erstmals in Kombination mit der klimakompensierten Elektronik für Relativdruckmessungen eingesetzt werden.
Bisher mussten die Kunden auf gekapselte Absolutdrucksensoren zurückgreifen. Durch einen sehr kleinen Prozessanschluss, gelingt es den Schwarzwäldern, eine sehr hohe Messgenauigkeit zu realisieren.
Elektronischer Differenzdruck
Ein innovatives Software- und Hardwarekonzept erlaubt es, alle Geräte der Vegabar Serie 80 zu einem elektronischen Differenzdrucksystem zu kombinieren. Dazu muss der Kunde z. B. nur sein Standardgerät Vegabar 82 mit einem zweiten Sensor in der Elektronikausführung Slave kombinieren. Die Vorteile: einfache Auswahl, identische Bedienung und vereinfachte Lagerhaltung.
Zudem gibt es beim elektronischen Differenzdruck keine ölgefüllten Kapillarleitungen, die isoliert werden müssen, um Umgebungseinflüsse wie Temperaturschwankungen oder starke Vibrationen auszuschließen. Nicht zuletzt gehören ölgefüllte Druckmittler nicht unbedingt zu den preisgünstigsten Lösungen. Für den Anwender dürfte sich in vielen Fällen der Einsatz eines elektronischen Differenzdrucksystems durchaus lohnen.
Mehr braucht man nicht
Vega hat die Vegabar-Druckgerätefamilie auf wenige Varianten reduziert und erleichtert damit dem Anwender die Auswahl. Ab sofort lassen sich alle denkbaren Applikationen mit drei Prozessdruckmessumformern lösen: Bei Standardanwendungen ist der Allrounder Vegabar 82 erste Wahl. Bei hohen Temperaturen und hohen Anforderungen an die chemische Beständigkeit kann der Vegabar 81 glänzen. Sind hohe Drücke gefragt, führt kein Weg am Vegabar 83 vorbei. Die keramischen Messzellen, selbstverständlich aus eigener Entwicklung und Fertigung, lassen andere Druckmessumformer bei Feuchtigkeits- und Temperaturschockempfindlichkeit weit hinter sich.