Validierung in vier Schritten
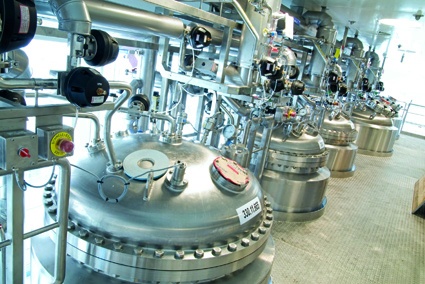
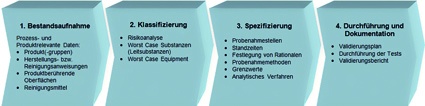
Neben dem validen Prozessverfahren konzentriert sich die Validierung bei pharmazeutischen Anlagen auf die nachweislich erfolgreich durchgeführte Reinigung. Obwohl die Behördenanforderungen an ein gereinigtes Gesamtsystem tendenziell steigen, gibt es immer noch Wege, den Validierungsaufwand effizient zu gestalten.
Was für das bloße Auge als sauber gelten mag, reicht im Pharmasektor kaum. Hier ist die erfolgreiche Reinigung erst dann geglückt, wenn analytisch nichts mehr nachgewiesen werden kann, bzw. der Reinigungsrückstand unterhalb eines geforderten Akzeptanzbereiches liegt. Bereits Rückstände im ppm-Bereich reichen aus, um ein Folgeprodukt zu verunreinigen bzw. zur Kreuzkontamination zu führen oder gar die Gesundheit von Patienten zu gefährden.
Was ist die Reinigungsvalidierung?
Mit der Reinigungsvalidierung soll gemäß nationaler als auch internationaler behördlicher Vorgaben und Richtlinien sichergestellt werden, dass ein dokumentierter Nachweis besteht, um ein geprüftes Reinigungsverfahren für Equipment zur Herstellung von pharmazeutischen Produkten zu gewährleisten. Als Voraussetzung für die Durchführung einer Reinigungsvalidierung müssen umfangreiche Kenntnisse über Produkt, Reinigungsmittel, Reinigungsverfahren, Anlagendesign, Probenahmestellen und -verfahren sowie analytische Nachweisverfahren zusammengetragen werden. Vor der Validierung ist in mehreren Optimierungsversuchen der ideale Reinigungsprozess zu ermitteln. Dieser ist mit der Reinigungsvalidierung zu bestätigen.
Die Validierung in vier Schritten
Die Reinigungsvalidierung erfolgt im Wesentlichen in vier Schritten (Abb. 1). Während der Bestandsaufnahme werden prozess- und produktrelevante Daten und Informationen gesammelt. Hierzu gehören z.B. Produkteigenschaften, Herstellungs- und Reinigungsanweisungen, Größe und Gestalt der produktberührenden Oberflächen des Equipments, sowie Reinigungsmittel und -verfahren. Wichtig ist auch die Produktionsreihenfolge: Ein hochaktives Vorgängerprodukt muss anders betrachtet werden als ein Wirkstoff mit wenig Aktivität.
Im zweiten Schritt werden diese Informationen klassifiziert. Neben den detaillierten Kenntnissen der Ausrüstung und des Produkts sind umfassende Informationen zu den Wirksamkeiten bzw. zur Toxizität der „Worst Case-Produkte" und dem „Worst Case-Equipment" einzuholen. Die kritischen Parameter eines Reinigungsverfahrens werden durch eine Risikoanalyse ermittelt. Diese soll den Einfluss von produkt-, anlagen- und prozessbezogenen Parametern auf das Reinigungsziel bewerten.
Im Spezifizierungsschritt werden die Probenahmestellen, Standzeiten, produktberührenden Oberflächen des Equipments, Rationalen, Probenahmemethoden festgelegt. Die Probenahme kann an ausgewählten Stellen definierter Größe mit Hilfe eines Tupfers direkt auf der produktberührten Oberfläche der Produktausrüstung durchgeführt werden. Falls dies nicht möglich ist, erfolgt die Probenahme der Anlage indirekt durch Spülen mit einem geeigneten Lösungsmittel.
Exkurs: Festlegen von Grenzwerten
Zur Überprüfung der Reinigungsvalidierung werden im Vorfeld Grenzwerte für Produkt- und Reinigungsmittelrückstände und den mikrobiologischen Status festgelegt. Dabei sind folgende Grenzwerte zu beachten:
- Eine Anlage muss nach der Reinigung immer „visually clean" sein. Dieses Kriterium wird stets in Kombination mit einem weiteren Kriterium verwendet. In der Literatur sind das 1/1000-Dosis-Kriterium, das 10-ppm-Kriterium sowie das toxikologische Kriterium für Rückstände aus dem Produktionsprozess zu finden. Dabei wird jeweils das „härteste" Kriterium angewandt.
- Für die Betrachtung von Reinigungsmittelrückständen werden ebenfalls das 10-ppm-Kriterium oder der Wert für den „Acceptable Daily Intake" und der daraus ermittelbaren maximal tolerierbaren Verschleppung eines definierten Reinigungsmittels in die Folgecharge herangezogen.
- Die Grenzwerte für die Mikrobiologie können auf Basis der eingesetzten Spülwasserqualität und den Spezifikationen der Reinraumumgebung (Keimzahl pro Fläche) festgelegt werden.
Mit geeigneten analytischen Nachweisverfahren (z.B. HPLC, GC usw.) müssen diese Grenzwerte - unter Berücksichtigung der Wiederfindungsrate für die Probenahme- und Testverfahren - innerhalb der festlegten Akzeptanz eingehalten werden.
Dokumentation
Schließlich ist die Reinigung zu dokumentieren. Hierbei wird ein Validierungsplan erstellt, welcher den Inhalt und die Durchführung der Validierung beschreibt. Die Tests sind analog der Vorgaben des Planes durchzuführen. Vor dem Start einer Reinigungsvalidierung muss das Equipment bereits qualifiziert und die zu reinigende Oberfläche bekannt sein. Aus den Rohdaten der Messungen auf Rückstände aus drei Validierungsläufen allein entsteht noch kein Validierungsbericht. Die Ergebnisse der Messungen sind mit den Grenzwerten zu vergleichen und zu bewerten. Abweichungen vom Validierungsplan sind darzulegen, zu begründen und zu bewerten. Die Dokumentation erfolgt im Validierungsbericht. Validierungsplan und -bericht müssen von den verantwortlichen Personen genehmigt werden.
Ansätze für weniger Validierungsaufwand
Zur Minimierung des Umfangs und Beschleunigung des Validierungsvorgangs kann ein „Groupingansatz" helfen: Equipment lässt sich in Gruppen zusammenfassen, wenn z.B. Behälter gleicher Bauweise, Design und Konstruktion vergleichbar, mit dem gleichen oder ähnlichen Reinigungsverfahren gereinigt werden. Verschmutzungen lassen sich über ein «Matrixing» zusammenfassen, wenn sie vergleichbare, chemisch-physikalische Eigenschaften aufweisen und somit die Reinigbarkeit gleich ist.
Sensible Systeme lupenrein testen
Eine grundsätzliche GMP-Anforderung ist, die Reinigungsprozesse qualitätsrelevanter Ausrüstungen und Anlagen zuverlässig und wirksam zu validieren. Wo in der Vergangenheit stets der Betreiber gefordert war, sind mittlerweile kompetente Dienstleister zur Stelle. Eine effizient gestaltete Validierung senkt dabei nicht nur die Kosten sondern auch den Zeitaufwand. Die Chemgineering Technology Designer unterstützen Unternehmen im gesamten Validierungsprozess. In enger Zusammenarbeit mit Produktions- und Betriebspersonal wird eine Strategie entwickelt. Dabei profitieren Kunden von den Erfahrungen aus zahlreichen Projekten und der umfassenden Kenntnis regulatorischer Anforderungen.