Schüttgut kennen und beherrschen
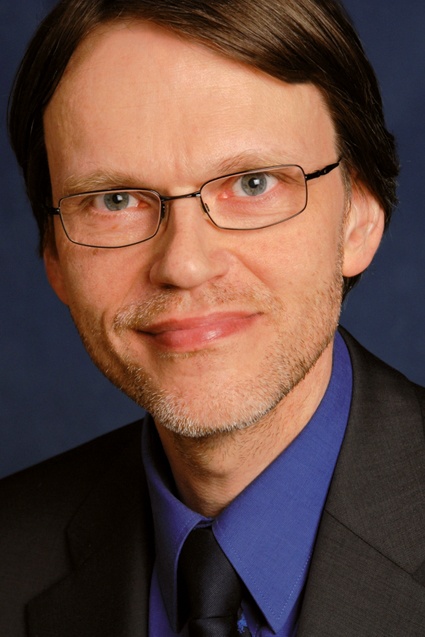
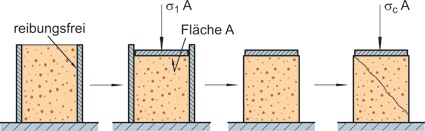
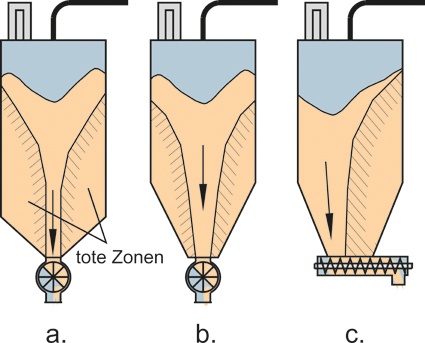
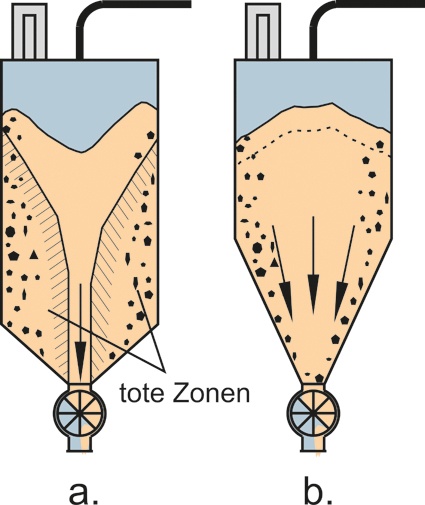
CITplus - Viele Produkte, auch Vor- und Zwischenprodukte, liegen in Form von Schüttgütern vor, angefangen vom Nanopulver bis hin zum Granulat. Für die industrielle Anwendung stehen hinsichtlich der Handhabung folgende Fragen im Vordergrund: Wie gut fließt das Schüttgut? Wie verhält sich das Schüttgut in spezifischen Anlagen wie z. B. Silos oder Zuführtrichtern? Mit diesen Themen beschäftigt sich die Schüttguttechnik, eine über fünfzig Jahre alte Wissenschaft, die leider nicht so bekannt ist, wie es geboten wäre - was an häufig auftretenden und in diesem Beitrag beschriebenen Problemen bei der Handhabung von Schüttgütern sichtbar wird.
Fließeigenschaften
Fluidisiert man ein Schüttgut wie in einer Wirbelschicht, nähert sich sein Verhalten dem einer Flüssigkeit. Kompaktiert man ein Schüttgut wie bei der Tablettierung, erhält man einen Festkörper. Gewöhnlich begegnet man Schüttgütern zwischen diesen Extremen, denn in den meisten Fällen unterliegt ein Schüttgut Spannungen von deutlich unter 100 kPa und wird auch nicht in einer Weise mit Gas durchströmt, dass es zur Fluidisierung kommt.
Ein Schüttgut zum Fließen zu bringen bedeutet, dass Partikel oder Partikelbereiche gegeneinander verschoben werden. Bei grobkörnigen, trockenen Produkten ist dies mit verhältnismäßig wenig Aufwand verbunden, da im Wesentlichen Coulomb‘sche Reibung überwunden werden muss. Bei zunehmend feinkörnigen oder feuchten Produkten nimmt dagegen der Einfluss der Haftkräfte (van-der-Waals-Kräfte, Flüssigkeitsbrücken bei feuchten Schüttgütern [1]) zu, so dass Fließen nur mit größerem Aufwand zu erreichen ist. Eine weitere wichtige Einflussgröße ist die Zeit: Lagert ein Schüttgut längere Zeit unter Druckspannungen in einem Behälter ohne zwischenzeitige Bewegung, können sich die Haftkräfte durch Mechanismen wie z. B. Sintern, Kristallisation oder plastische Verformung der Partikelkontakte drastisch vergrößern, so dass der Aufwand weiter steigt.
Damit wird deutlich, dass die „Fließfähigkeit" eines Schüttgutes nur unter Berücksichtigung des Aufwandes zu beschreiben ist, der notwendig ist, um ein zunächst ruhendes Schüttgut in Bewegung zu bringen. Der einachsige Druckversuch in Abbildung 1 beschreibt dies. Das zunächst lockere Schüttgut befindet sich in einem Hohlzylinder mit reibungsfreien Wänden und der Querschnittsfläche A. Nach Aufbringen einer vertikalen Verfestigungsspannung σ1 auf das locker eingefüllte Schüttgut kommt es zur Verfestigung und Verdichtung. Danach wird die Druckfestigkeit σc gemessen, indem der verfestigte Schüttgutzylinder einer zunehmenden vertikalen Druckspannung unterworfen wird, bis es zum Bruch (Fließen) kommt.
Aus dem Druckversuch ergibt sich die Definition der Fließfähigkeit ffc, die gleich dem Verhältnis von Verfestigungsspannung σ1 zu Schüttgutfestigkeit σc ist [1, 2]:
ffc = σ1/ σc(1)
Umso größer ffc ist, d. h. umso kleiner die Schüttgutfestigkeit im Verhältnis zur Verfestigungsspannung ist, desto leichter ist ein Schüttgut aus der Ruhe zum Fließen zu bringen. Die genannten Einflussgrößen wie Spannung, bei der ein Schüttgut lagert (z. B. am Boden eines BigBag), oder Lagerzeit lassen sich bei der Messung ebenso wie Temperatur oder Luftfeuchtigkeit berücksichtigen, so dass man eine auf physikalischen Größen basierende Aussage zur Fließfähigkeit erhält.
So einfach der einachsige Druckversuch aussieht, so schwierig ist er zu realisieren. Wird die auch im Ruhezustand auftretende Reibung zwischen Schüttgut und Wand des Hohlzylinders nicht durch eine aufwändige Schmierung verhindert, nimmt die aufgebrachte Verfestigungsspannung von oben nach unten stark ab, was eine zuverlässige Messung unmöglich macht. Daher bevorzugt man in der Schüttguttechnik sogenannte Schergeräte, mit denen definierte physikalische Größen zur Beschreibung des Schüttgutverhaltens gemessen werden. Schergeräte basieren auf den Arbeiten Jenikes [2], der die Grundlagen zur Charakterisierung von Schüttgütern und zur verfahrenstechnischen Siloauslegung schuf. Heute haben sich vor allem automatische Ringschergeräte zur Messung der Fließfähigkeit und anderer Fließeigenschaften etabliert [1, 3]. Schergeräte liefern neben der Schüttgutfestigkeit nach Abb. 1 auch Ergebnisse zur inneren Reibung, zur Schüttgutdichte und zur Wandreibung. Die Wandreibung beschreibt das Fließen des Schüttgutes entlang einer Feststoffoberfläche (z. B. Trichterwand, Schurre). Sie gibt Informationen zur notwendigen Steilheit von Wänden als auch zur Neigung zum Anbacken [1].
Im Gegensatz zu Schergeräten erscheinen phänomenologische Messmethoden zur Messung von Größen, die die Fließfähigkeit beschreiben sollen, als wenig hilfreich für eine ernsthafte Aussage. So sagt z. B. ein Böschungswinkel nichts dazu aus, ob sich ein Schüttgut bei der Lagerung verfestigt, oder ob es bei einer bestimmten Auslauf-
abmessung zum Stocken des Schüttgutflusses kommt. Das gleiche gilt für alle „Einfachmessmethoden", deren Resultate keine physikalisch definierten Größen sind [1] und die nur deshalb als einfach empfunden werden, weil aufgrund der komplexen Vorgänge keine theoretischen Grundlagen zu ihrer Beschreibung verfügbar sind.
Schüttgutgemäße Gestaltung von Anlagen
In Anlagen, die Schüttgüter verarbeiten, müssen diese gelagert, gefördert, zugeführt und dosiert werden. Die häufigsten Probleme, die dabei auftreten, sind Fließstörungen und Entmischung.
Fließstörungen sind in erster Linie das Ergebnis zu kleiner Querschnitte, so dass das Schüttgut z. B. über zu kleinen Auslauföffnungen Brücken bildet. Die maßgebliche Schüttguteigenschaft hierzu ist bei kohäsiven Schüttgütern die in Abb. 1 erläuterte Schüttgutfestigkeit, die es dem Schüttgut erlaubt, eine stabile Brücke zu bilden. Durch Messen der Fließeigenschaften ist es möglich, die Mindestquerschnitte für ein Schüttgut zu bestimmen und so eine Anlage so auszuführen, dass es nicht zu Brückenbildung kommt [1, 2].
Von enormer Tragweite für das Verhalten des Schüttgutes in einer Anlage ist die Gegenwart sogenannter toter Zonen (Abb. 2). Dies sind Bereiche, die in Ruhe verharren, während Schüttgut aus oder durch einen Behälter oder Trichter fließt. Man spricht in diesem Fall von Kernfluss.
Kernfluss tritt z. B. dann auf, wenn die Trichterwände nicht steil oder glatt genug sind (Abb. 2.a). Es bilden sich tote Zonen, und nur in einer Fließzone, die sich von der Auslauföffnung nach oben hin erstreckt, bewegt sich das Schüttgut nach unten. Tote Zonen bilden sich auch auf Vorsprüngen (Abb. 2.b) oder durch Austraggeräte, die nicht in der Lage sind, das Schüttgut über der gesamten Auslauföffnung abzuziehen. Abbildung 2.c zeigt einen Schneckenförderer unter einem Auslaufschlitz, der sich bereits am hinteren Ende mit Schüttgut füllt, so dass er im weiteren Verlauf kein Schüttgut mehr aufnehmen kann. Die gezeigten Beispiele gelten nicht nur für Silos, sondern für jegliche Behälter, in denen Schüttgut fließen soll.
Kernfluss ist die Ursache vieler unterschiedlicher Probleme. Das Schüttgut in den toten Zonen kann sehr lange im Silo verweilen, so dass seine Qualität abnimmt, oder es sich mit der Zeit so sehr verfestigt, dass die toten Zonen nach Entleerung der Fließzone stabil stehen bleiben (Schachtbildung)
Ein häufig auftretendes Problem ist die Entmischung. Beim Füllen eines Behälters muss man schon bei geringen Unterschieden in Partikelgröße, -form oder -dichte davon ausgehen, dass sich das Produkt über dem Siloquerschnitt entmischt. Im Beispiel von Abb. 3 findet man mehr Grobgut am Rand des Silos und mehr Feingut nahe der Siloachse. Dies ist ein typisches Ergebnis bei mittiger Einfüllöffnung und nicht zu feinem Schüttgut. Herrscht im Silo Kernfluss (Abb. 3.a), wird zunächst das Produkt aus der Mitte (z. B. Feingut) ausfließen, während das Produkt vom Rand (z. B. Grobgut) erst später folgt. Dadurch entsteht am Auslauf ein Schüttgutstrom mit zeitlich veränderlicher Zusammensetzung - auch wenn das Schüttgut beim Füllen bestmöglich gemischt war.
Anhand der beschriebenen Probleme wird deutlich, dass Kernfluss nachteilig ist. Die Alternative zu Kernfluss ist Massenfluss. Bei Massenfluss ist sämtliches Schüttgut während des Schüttgutabzugs in Bewegung (Abb. 3.b). Um Massenfluss zu erreichen, müssen die Trichterwände steil genug sein, um tote Zonen zu verhindern. Die notwendige Neigung lässt sich aus den gemessenen Fließeigenschaften, insbesondere der Wandreibung, bestimmen [1, 2]. Außerdem müssen die übrigen in Abbildung 2 gezeigten Ursachen für Kernfluss vermieden werden, was eine Frage der konstruktiven Ausführung ist. Bei Schneckenförderern vermeidet man tote Zonen, wenn die Schnecke steigende Förderkapazität in Förderrichtung hat, z. B. durch eine allmähliche Zunahme der Steigung, für andere Austraggeräte gibt es entsprechende Lösungen [1].
Bei Massenfluss verlässt das Schüttgut das Silo etwa in der gleichen Reihenfolge, in der es eingefüllt wurde. Die Verweilzeitverteilung ist eng. Schachtbildung kann nicht auftreten, da es keine toten Zonen gibt. Die beim Füllen entstandene Entmischung wird reduziert, da die entmischten Bereiche im Trichter wieder vereinigt werden.
Fazit
Das Verhalten eines Schüttgutes wird mit Größen beschrieben, die physikalisch definiert und mit Schergeräten messbar sind. Diese Größen lassen sich nutzen, um Produkte hinsichtlich ihrer Fließfähigkeit zu beurteilen oder Anlagenkomponenten auszulegen. Problemen wie Fließstörungen oder Entmischung wird entgegengewirkt, wenn Trichter etc. an die Fließeigenschaften des Schüttgutes angepasst werden. In vielen Fällen ist Massenfluss der Schlüssel für einen erfolgreichen Betrieb.
Literatur
[1] Schulze, D.: Pulver und Schüttgüter, 2. Auflage, Springer-Verlag (2009)
[2] Jenike, A.W.: Storage and Flow of Solids, Bull. No. 123, Utah Engng. Station, Univ. of Utah, Salt Lake City (1964)
[3] Schulze, D.: Ringversuch mit Ringschergeräten, Schüttgut 16 (2010) 3, S. 146-153