Richtungsweisende Logistiktrends
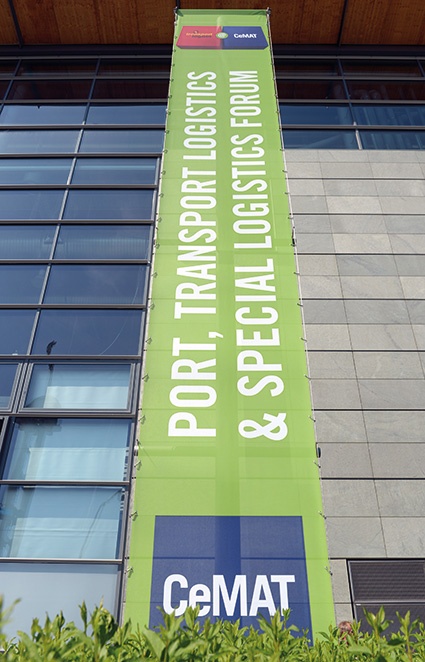
Einen hervorragenden Einblick in aktuelle Logistikthemen der Chemie- und Pharmabranche brachte das Anwenderforum Chemie- und Pharmalogistik während der CeMAT 2014 in Hannover. Das von CHEManager organisierte Forum griff in vier Themenblöcken die wichtigsten Technologiebereiche der Intralogistik-Messe auf. Durch den Tag führte Prof. Dr. Carsten Suntrop, CMC² und Dozent an der EUFH Rhein/Erft.
Lager- und Kommissioniertrends
Unter dem Titel „Adaptive Produktion unterstützt durch autonome Intralogistik" stellte Dr. Daniel Ewert vom Institut für Informationsmanagement im Maschinenbau der RWTH Aachen University die „Fabrik der Zukunft" vor. In dieser entwickelt sich der Produktionsprozess aus der Interaktion selbständig agierender Produktionseinheiten ohne jede zentrale Steuerung. Ein festgelegter unidirektionaler Produktstrom existiert nicht, denn autonome FTS sorgen für eine flexible Intralogistik.
In der Kommissionierung ist trotz des allgemeinen Automatisierungstrends der Anteil an manuellen Tätigkeiten noch immer hoch, was in manchen Fällen zu einer starken körperlichen Belastung der Mitarbeiter führen kann. Tobias Rammelmeier stellte in seinem Referat ein System zur fortlaufenden Ermittlung und Visualisierung der Mitarbeiterbelastung vor, das vom FML der TU München entwickelt worden ist.
Richtungsweisende Trends in der Pharmalogistik zeigte Manfred Preiß, Vice President, SSI Schäfer Peem auf. Die Pharmabranche sucht nach neuen Lösungen, da gesetzliche Auflagen, Qualitäts- und Hygienestandards steigen. Um die Produktsicherheit zu gewährleisten, spielen die Nachverfolgung von Chargen und Ablaufdaten aber auch die Lagerung nach Batch oder Charge eine wichtige Rolle. Preiß stellte u.a. neben vollautomatischen A-Frame Kommissioniersystemen auch ein neu entwickeltes Sortersystem vor.
Optimierung der Supply Chain
Wie sich in der Seehafenabwicklung die Transparenz von Transportketten der Chemielogistik erhöhen lässt, erklärte Holger Pontow, TU Darmstadt, in seinem Vortrag „Informationsflüsse der containerbasierten Seehafenabwicklung im Hinterland". Es zeigt sich in den bisherigen Untersuchungen, dass zahlreiche unterschiedliche IT-Systeme aber auch manuelle Abstimmungsroutinen im Prozess enthalten sind, die es zu harmonisieren gilt. Zudem kann der Informationsfluss einen hohen Einfluss auf Containerflüsse haben.
Einen innovativen Lösungsansatz zur Frage „Wie passe ich meine Supply Chain optimal den Anforderungen der modernen VUCA-Welt an?" (Link zum Video) gab der Vortrag von Hanns-Philipp Henckel, Head of Sales & Business Development der Camelot ITLab. VUCA steht hierbei für Volatilität, Unsicherheit, Komplexität und Ambiguität. Anhand von Praxisbeispielen zeigte Henckel, wie Unternehmen ihre Lieferketten anpassen können, um sie robuster gegen äußeren Einfluss zu machen, und wie die Supply Chain nicht nur schlanker sondern auch effizienter wird.
Siehe hierzu auch diese Artikel zu dem Thema: Artikel 1;Artikel 2!
RFID, Verkehrsfluss und Transportabwicklung
„RFID & Co - technische Grundlagen, Nutzenpotentiale und Herausforderungen" war der Vortrag von Ulli Münch, Gruppenleiter Technologien, Fraunhofer Supply Chain Services, betitelt. Münch gab einen Einblick in die unterschiedlichen Funktechnologien für eine bessere Verknüpfung von Informations- und Warenfluss in verschiedenen Einsatzbereichen. Er zeigte zudem die bestehenden Hürden und Problemstellungen beim Einsatz von Smart-Object Technologien auf.
Hohe Wartezeiten an den Werkstoren und negative Auswirkungen auf die Lieferzuverlässigkeit waren bei der BASF der Auslöser, über ein neues Einlass- und Abwicklungsverfahren nachzudenken. So kam es zur Umsetzung des Projekts „DRIVE" (Link zum Video) und damit zur Reduzierung der Durchlaufzeiten am Standort Ludwigshafen, wie Jürgen Müller, Information Services & Supply Chain Operations der BASF, im Vortrag „Das „DRIVE" Projekt und seine Pilotierung bei der BASF" erläuterte.
Hans Maier-Dech, Geschäftsführer von Star/trac, knüpfte in seinem Referat „Neue Technologien in übergreifenden Logistikketten: Hürden und Potenziale" an das „DRIVE"-Projekt (Link zum Video) an und ging auf praktikable Ansätze mit dem Ziel einer schnelleren Transportabwicklung in Chemieparks ein. Die Struktur der Chemielogistik spräche dabei unbedingt gegen Insellösungen. BASF und Chemion hätten sich deshalb bereits auf Grundsätze zum Einsatz der RFID und Transponder Technologie verständigt - auch zum Nutzen der Chemie-Verlader.
Im Vortrag „GATE"-Projekt: Chemion optimiert Lkw-Abfertigung" (Link zum Viedeo) zeigte Uwe Menzen, Geschäftsführer von Chemion Logistik, wie den steigenden Transportvolumina und damit steigenden Abfertigungszeiten zu Leibe gerückt werden muss. Mit dem Projekt-Partner Star/trac wurde „GATE" im Chempark Leverkusen eingeführt und Check-In und -Out durch die automatisierten Prozesse beschleunigt. In der branchenweiten Zusammenarbeit sieht Menzen Vorteile für alle Beteiligten, wie die Verbesserung von Qualität und Sicherheit aber auch durch Unternehmensübergreifende Transportabwicklung. Gemeinsam mit BASF wurde ein offener Branchenstandard geschaffen.
Siehe hierzu das Video: Verkehrsfluss und Transportabwicklung in Chemieparks!
Sichere Lagerung von Gefahrstoffen
Der vierte Themenblock befasste sich schließlich mit der Lagerung von Gefahrstoffen und hier im speziellen mit der TRGS 510, die der erfahrene Prof. Dr. Herbert Bender, Gefahrstoff Consulting Compliance, in seinem Vortrag „TRGS 510 - Neuausrichtung des Regelwerks" in einem Kurzumriss vorstellte. Erstmalig umfasse dieses Regelwerk Lagervorschriften für alle Gefahrstoffe in ortbeweglichen Behältern bei passiver Lagerung. Zusatzregelungen seien nur bei Ansteckungsgefährlichen Stoffen, Sprengstoffen, Organischen Peroxiden und Ammoniumnitrat zu beachten. Bender erläuterte die wichtigsten Punkte der Vorschrift und ihrer Anlagen und wies auf die Besonderheiten hin.
Als Frau aus der Praxis ging Christine Jäger, Umweltschutz/ Anlagensicherheit, Bode Chemie, im abschließenden Vortrag des Tages auf die „Umsetzung der Lagerregelungen in die Praxis" ein. Sie erläuterte die nötigen fünf Schritte der Umsetzung: Gefahrstoffe identifizieren, Gefahrstoffmengen und Lagerbereiche festlegen, erforderliche Schutzmaßnahmen ermitteln, Lager gestalten und betreiben. Wichtig seien vor allem ein systematisches Vorgehen und die Dokumentation der Entscheidungen in einer Gefährdungsbeurteilung.
Fortlaufende Belastungsermittlung in der Kommissionierung
Eine der zentralen Anforderungen an Kommissioniersysteme ist ein hohes Maß an Flexibilität. Die Kommissionierung ist daher trotz des allgemeinen Trends hin zur Automatisierung von einem hohen Anteil an manuellen Tätigkeiten, insbesondere manuellen Lastenhandhabungsvorgängen, geprägt.
Um in Kommissioniersystemen langfristig eine gesunde Mitarbeiterbelastung zu gewährleisten, sind die Ursachen für eine hohe Belastung zu ermitteln und geeignete Maßnahmen abzuleiten. Als Grundlage hierfür ist die kontinuierliche und objektive Aufnahme, Bewertung und Visualisierung der physischen Belastung erforderlich. Bestehende Verfahren zur Beurteilung der körperlichen Belastung, die z.B. bei Montagetätigkeiten angewandt werden, berücksichtigen jedoch nur teilweise die vielfältigen Einflussgrößen in Kommissioniersystemen, wie z.B. variierende Lastgewichte oder Körperhaltungen, oder verursachen einen hohen Aufwand bei der Durchführung.
Deshalb wurde am Lehrstuhl für Fördertechnik Materialfluss Logistik (fml) der Technischen Universität München ein System zur fortlaufenden Ermittlung und Visualisierung der Mitarbeiterbelastung entwickelt. Durch den Einsatz von Motion Capturing, Industriesensoren und der Pick-by-Vision Technologie sowie durch den Zugriff auf Daten des Warehouse Management Systems erfolgt die Belastungsermittlung dabei vollständig automatisiert. Durch den Einsatz des Systems stehen Entscheidungsträgern jederzeit und ohne zusätzlichen Aufwand für die Datenerhebung wichtige Informationen zur Verfügung, um zielgerichtet Maßnahmen zur Belastungsreduktion ableiten zu können.
Autor: Tobias Rammelmeier, Mitarbeiter am Lehrstuhl für Fördertechnik Materialfluss Logistik (fml) der TU München
TRGS 510 - Umsetzung der Lagerregelungen in der Praxis
Die Anforderungen an die Lagerung von Gefahrstoffen nach TRGS 510 „Lagerung von Gefahrstoffen in ortsbeweglichen Behältern" sind in der Praxis überschaubar. Voraussetzung ist lediglich ein systematisches Vorgehen und die Dokumentation der Entscheidungen in einer Gefährdungsbeurteilung.
Die Systematik ist folgende:
1.) Gefahrstoffe identifizieren
2.) Gefahrstoffmengen und Lagerbereiche festlegen
3.) erforderliche Schutzmaßnahmen ermitteln
4.) Lager gestalten
5.) Lager betreiben
zu 1.) Gefahrstoffe identifizieren
Gefahrgutkennzeichnung und Gefahrstoffkennzeichnung sind wichtigste Indizien, dass ein Gefahrstoff vorliegt. Maßgeblich sind die Angaben im Sicherheitsdatenblatt. Der Inverkehrbringer hat die sicherheitsrelevanten Daten zur Verfügung zu stellen, dies erfolgt im Allgemeinen durch das Sicherheitsdatenblatt. Er hat die sicherheitsrelevanten Daten auch dann zur Verfügung zu stellen, wenn kein Sicherheitsdatenblatt vorgeschrieben ist. Dies kann z.B. in einem Produktinformationsblatt in Anlehnung an das Sicherheitsdatenblatt erfolgen.
zu 2.) Gefahrstoffmengen und Lagerbereiche festlegen
Anhand der TRGS 510 ist zu ermitteln, ob die betrachteten Gefahrstoffe in den vorgesehenen Mengen außerhalb von Lagern gelagert werden dürfen oder ob Gefahrstofflager ggf. mit zusätzlichen und besonderen Schutzmaßnahmen erforderlich sind.
zu 3.) Erforderliche Schutzmaßnahmen ermitteln
Von den in der TRGS 510 vorgegebenen Schutzmaßnahmen kann abgewichen werden, wenn dies in einer Gefährdungsbeurteilung begründet und dokumentiert ist.
So ist es bspw. nicht erforderlich elektrostatisch ableitfähige Auffangwannen zu verwenden, wenn im konkreten Einzelfall elektrostatische Entladungen keine wirksame Zündquelle darstellen.
Auf Auffangwannen kann im konkreten Einzelfall verzichtet werden, wenn die Gefährdungsbeurteilung ergibt, dass hierdurch keine zusätzliche Gefährdung der Mitarbeiter entsteht.
Solche Entscheidungen sind in einer Gefährdungsbeurteilung zu dokumentieren und in angemessenem Umfang zu begründen.
Zu den Schutzmaßnahmen gehören auch Flucht- und Rettungswege, ggf. das Vorhandensein von Notduschen und Löscheinrichtungen.
zu 4.) Lager gestalten
Zweck des Lagers ist es, die Schutzfunktion der Verpackung zu erhalten und im Fall des ungewollten Produktaustritts die Gefährdung für Mitarbeiter zu begrenzen. Die Schutzfunktion der Verpackung wird durch die Auswahl einer geeigneten Verpackung und Ladeeinheit sowie durch die physikalischen Lagerbedingungen sichergestellt. Zur Begrenzung des Schadensausmaßes für Mitarbeiter ist eine übersichtliche Gestaltung und Ordnung des Lagers erforderlich, weiterhin Auffangräume sowie Flucht- und Rettungswege, ggf. auch Löscheinrichtungen.
zu 5.) Lager betreiben
Sicheres Betreiben bedeutet, die vorgegebenen Schutzmaßnahmen aufrecht zu erhalten. Das Lager ist mit Sicherheits- und Gesundheitsschutzkennzeichnung auszustatten und Mitarbeiter zu unterweisen. Insbesondere bei Einlagern ist zu beachten, dass das Lagergut in einer geeigneten einwandfreien, leicht zu identifizierenden Verpackung am vorher bestimmten Lagerplatz eingelagert wird. Der Einlagerungsplan ist fortzuschreiben.
Autor: Christine Jäger, Umweltschutz/Anlagensicherheit, Bode Chemie