Reinraumkleidung: typische Fehlerquellen
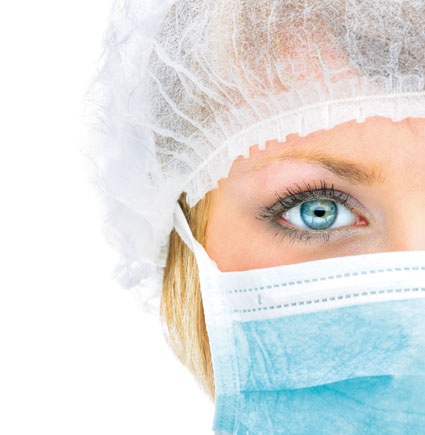
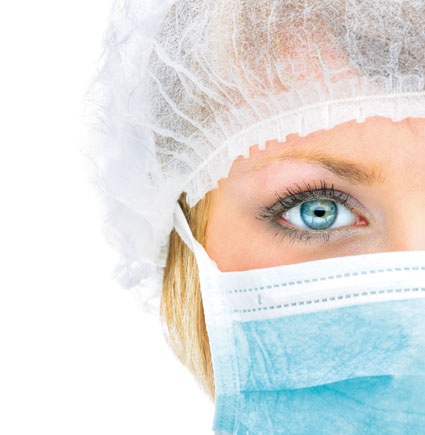
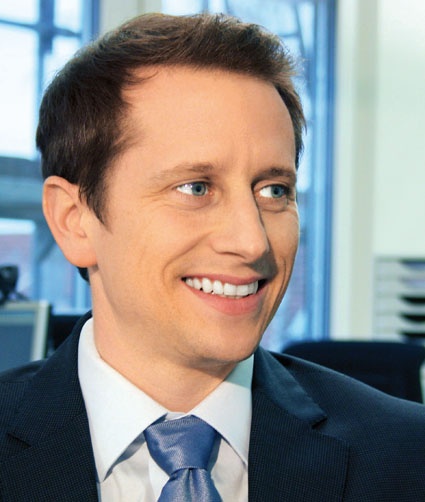

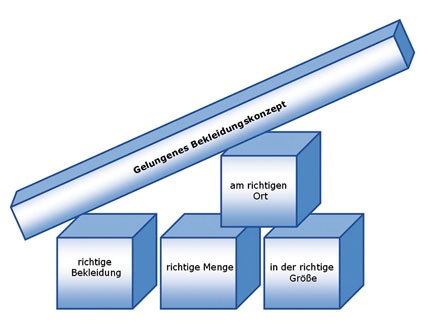
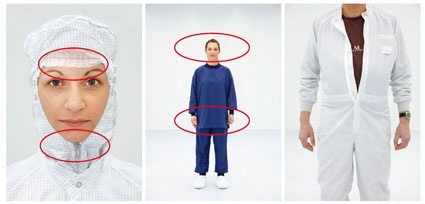
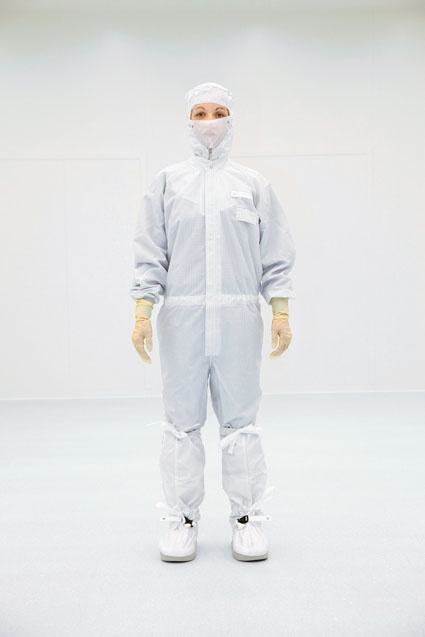
In zunehmendem Maße steigen die Reinheitsanforderungen an Produktionsumgebungen. Reinraumbekleidung spielt dabei eine wesentliche Rolle. Doch nur der richtige Einsatz gewährleistet einen effektiven Produktschutz. Von der Gestaltung des Bekleidungskonzepts bis hin zum richtigen Verhalten ergeben sich viele Fehlerquellen, die mittelbaren oder unmittelbaren Einfluss auf die Produktqualität haben.
Oft sind es kleine und einfache Punkte die darüber entscheiden ob ein Bekleidungssystem funktioniert - operativ und ökonomisch. Allgemein betrachtet sollte ein Bekleidungssystem folgendem Prinzip entsprechen: Die richtige Bekleidung, in der richtigen Menge, in der richtigen Größe, zur rechten Zeit am richtigen Ort.
Die Auswahl der richtigen Bekleidung
Die Auswahl der richtigen Bekleidung, d.h. welche Bekleidungsteile (bspw. Overall, Haube) zum Einsatz kommen sollen, orientiert sich immer am Produktionsprozess und den räumlichen Gegebenheiten. Die Berücksichtigung von speziellen Anforderungen wie beispielsweise ESD, flüssigkeitsabweisende Beschichtung, besondere Passform etc. erhöhen die Schutzfunktion des gewählten Bekleidungssystems. Zudem sollte ein Augenmerk auf den „Personenfluss" gelegt werden. Manche sinnvolle Bekleidungssysteme lassen sich aufgrund der räumlichen Gegebenheiten (insbesondere der Schleusengestaltung) nicht umsetzen. Hier müssen Kompromisse gefunden werden, welche den Produktanforderungen und Regularien entsprechen.
Die erforderliche Menge an Bekleidung
Die erforderliche Menge an Bekleidung (Ausstattungsmenge) orientiert sich an der Wechselhäufigkeit, an den Reinheits- und/oder Hygieneanforderungen sowie regulatorischen Anforderungen. Starke Verunreinigungen der Bekleidung sowie häufiger Produktwechsel können dazu führen, dass die geplante Anzahl von Wechseln nicht ausreicht. Folglich kommt es zu einem Engpass, welcher dazu führen kann, dass die Bekleidung nicht ausreichend häufig gewechselt wird. Die Filterfunktion des Gewebes ist gestört - die Bekleidung wird zur Kontaminationsquelle. Zu beachten ist bei der Mengenbestimmung auch, dass das Reinigungspersonal sowie gelegentliche Besucher (Wartungspersonal etc.) berücksichtigt werden.
Die korrekte Passform
Damit Reinraumbekleidung seiner Schutzfunktion gerecht wird, ist auf die korrekte Passform (bspw. nicht zu weit, nicht zu eng) zu achten. Um den firmenspezifischen Größenspiegel zu ermitteln, ist, unabhängig vom Versorgungssystem, eine Anprobe vorzunehmen. Dies gilt gleichermaßen für personenbezogene und Pool-Bekleidung. Dabei sind auch individuelle Anpassungen wie beispielsweise überlange Arme zu beachten. Modische Aspekte sind in den Hintergrund zu stellen. Genauso wie die absolute Veränderung des Personalbestands, verändert Fluktuation oftmals den Größenbedarf. Daher ist eine regelmäßige Überwachung des Größenspiegels zu empfehlen.
Der Ort des Einsatzes
Als Selbstverständlichkeit wird oft betrachtet, dass die Bekleidung rechtzeitig an dem jeweiligen Verwendungsort bereitgestellt ist. Doch bei Mehrschichtproduktionen bzw. Sonn- und Feiertagsarbeiten, ist eine entsprechende Logistik sorgfältig zu planen. Hier kann es ratsam sein, dass verschiedene Kennzeichnungen oder Bekleidungsfarben eingesetzt werden, um Produktionsbereiche voneinander zu unterscheiden. Sofern Mitarbeiter Reinräume wechseln, ohne die erforderlichen Umkleideschritte einzuhalten, wird dies leicht erkennbar (bspw. blauer Overall im Bereich für weiße Overalls). Ebenfalls kann unterbunden werden, dass dezidierte Bekleidung in nicht dafür vorgesehenen Bereichen eingesetzt wird („cross-contamination"). Bei der Lagerung der Bekleidung ist zu berücksichtigen, dass Kontaminationen während der Lagerzeit vermieden werden. Diese Lagerräume sollten sich in der Nähe der reinen Bereiche befinden und angemessen hinsichtlich Sauberkeit, Luftfeuchtigkeit und Temperatur gestaltet sein. Zu feuchte Lagerräume können beispielsweise dazu führen, dass die Bekleidung unnötig kontaminiert wird.
Der laufende Betrieb
Ist das Bekleidungssystem einmal etabliert, ergeben sich im laufenden Betrieb immer wieder Stolperfallen, die dazu führen können, dass die Produktqualität bzw. die Gutmenge negativ beeinflusst wird. Insbesondere bei der detailgetreuen Umsetzung ergeben sich Abweichungen. Ein zentraler Punkt ist die Verwendung reinraumgerechter Bekleidung. Dabei sollte nicht ausschließlich der Fokus auf die Oberbekleidung wie etwa Overalls gelegt werden, sondern auch auf die sonstigen Bekleidungsteile, welche potentiell in den Reinraum mitgenommen werden. Manchmal werden modische Accessoires wie Schals oder in den kälteren Monaten Rollkragenpullover oder Pullover mit hohem Halsabschluss getragen. Bekleidungsteile dieser Art können jedoch zu erheblichen Problemen in der Produktion führen, da Fasern brechen und somit die Umgebung unnötig kontaminieren. Sofern keine spezielle Unterbekleidung verwendet wird, ist auch zu bedenken, dass jede Umkleideprozedur große Mengen von Partikeln freisetzt und insbesondere in Umkleideräumen/Schleusen zu inakzeptablen Verunreinigungen führt. Diese werden dann von allen Mitarbeitern in die Produktion getragen. Eine einfache Möglichkeit die Partikelbelastung (nicht schwebend) in den Umkleidebereichen zu überprüfen, bietet Schwarz-/UV-Licht. „Reinraumgerechte Bekleidung" bedeutet jedoch auch, dass festgelegte Bekleidungswechsel eingehalten werden. Nur in einem aufbereiteten Zustand kann die Reinraumbekleidung ihre Filterfunktion richtig erfüllen. Wird die Bekleidung länger als festgelegt getragen, ist nicht mehr auszuschließen, dass die Filterfunktion für den jeweiligen Einsatzbereich noch ausreichend ist. In Produktionen höchster Reinheitsklassen kann dies bereits nach wenigen Stunden der Fall sein. Hier können partikuläre oder mikrobielle Verunreinigungen zu erheblichen Problemen in der Produktion führen.
Das Anlegen der Bekleidung
Die Reihenfolge, in der die Bekleidungsteile angelegt werden, ist ebenfalls entscheidend für die Kontaminationskontrolle. Im Privatbereich erfolgt das Ankleiden - bevor man das Haus verlässt in der Regel von „unten nach oben" - sprich zuerst die Schuhe und zum Schluss die Mütze oder Hut. Im Reinraum ist, aufgrund der besonderen Luftführung, genau die umgekehrte Reihenfolge einzuhalten. Sicherlich für viele eine Selbstverständlichkeit, jedoch ist in der Praxis gerade hier Fehlverhalten zu beobachten. Ein Mantel, welcher vor der Vlieshaube angezogen wird, kann durch herabfallende Haare und Kopfhautschuppen unmittelbar kontaminiert werden. Des Weiteren ist darauf zu achten, dass die Shirts der Unterbekleidung auch in den Hosenbund gesteckt werden. Andernfalls können Körperhaare und Hautschuppen ungehindert in den Produktionsraum gelangen. Auch die Armbündchen der Bekleidung stellen besonders kritische Stellen dar, da diese in der Regel aus einem sogenannten Gestrick bestehen und folglich ein verändertes Partikelrückhaltevermögen gegenüber dem Gewebe aufweisen. Aus diesem Grund sollten die Handschuhe stets über den Bündchen getragen werden. Manchmal wird aus Komfortgründen der Handschuh unter dem Armbündchen getragen, was beim planmäßigen Handschuhwechsel zu unnötigen Kontaminationen führt. Diese wenigen Beispiele zeigen, dass das korrekte Anlegen der Reinraumbekleidung regelmäßiger Schulungen bedarf. Die ISO 14644-5 (Anhang C) bietet gute Hinweise hierzu. Zusätzlich haben sich Fotos des korrekten „Outfits", welche in der Schleuse aufgehängt werden, als hilfreich erwiesen.
Kosmetika und Reinraum
Neben dem Bekleidungssystem an sich, ergeben sich in der Praxis immer Fragestellungen hinsichtlich der Verwendung von Kosmetika. Dabei gelten gerade diese Stoffe in reinen Umgebungen als besonders gefährlich. Das Abfallen von Kosmetika (bspw. Wimperntusche) und die Partikelabgabe können dazu führen, dass Produktverunreinigungen auftreten. Bei fettbasierten Kosmetika besteht zudem die Gefahr, dass Mikroorganismen Nährboden erhalten und sich drastisch vermehren können. Dass Kosmetika durchaus immer wieder im Reinraum verwendet werden, kann man oft an der Reinraumbekleidung erkennen: insbesondere im Kragenbereich entstehen irreversible Verfärbungen des Materials.
Rauchen und Reinraum
Jedes Unternehmen muss sich auch mit dem Thema „Rauchen und die Arbeit im Reinraum" auseinander setzen. Tatsächlich wird noch Stunden nach dem Rauchen der letzten Zigarette eine erhebliche Anzahl von zusätzlichen Partikeln ausgeatmet. Grundsätzlich empfiehlt es sich, bei Produktionen der höchsten Reinheitsklassen auf den Einsatz von Rauchern gänzlich zu verzichten. Bei Produktionen niedrigerer Reinheit sollten Regeln gefunden werden, die einen Produktschutz gewährleisten. In der Praxis haben sich dabei Zeitintervalle von 30 - 60 Minuten ergeben; d.h. der Zeitraum zwischen der letzten Zigarette und dem Eintritt in die reinen Räume.
Fazit
Sicherlich gibt es noch weitere Fehlerquellen, die den Einsatz von Reinraumbekleidung ungünstig beeinflussen können. Werden aber die aufgestellten Regeln von allen Personen, die den Reinraum betreten oder mit der Reinraumbekleidung Umgang haben, eingehalten, so ist das Wesentliche zur Sicherstellung der gewünschten reinen Produktionsumgebung erfolgt. Zusätzliche präventive Maßnahmen wie Schulungen, laufende Kontrollen und Korrekturen sind jedoch unerlässlich für eine langfristige, kontinuierliche Fertigung auf gleich hohem Niveau.