Optimierungspotenziale aufdecken
Aufgrund der Kapitalbindung spielt die kosteneffiziente Nutzung von Produktionsanlagen eine besondere Rolle, insbesondere in Ländern mit hohen Faktorkosten.
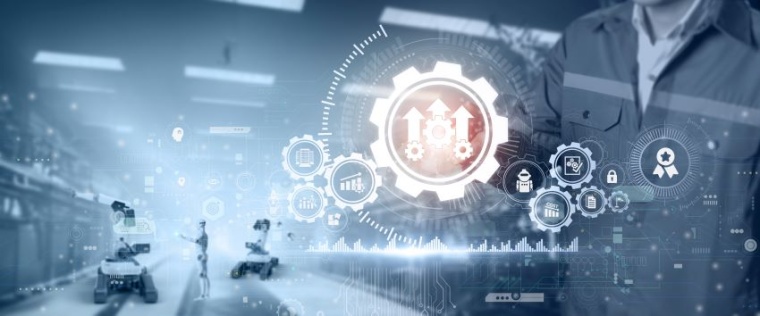
Striktes Kostenmanagement ist für viele Unternehmen seit Jahrzehnten gängige Praxis und Grundvoraussetzung, um im globalen Wettbewerb zu bestehen. Aufgrund der zunehmenden Automatisierung und der damit verbundenen Kapitalbindung spielt die kosteneffiziente Nutzung von Produktionsanlagen dabei eine besondere Rolle, insbesondere in Ländern mit hohen Faktorkosten für bspw. Personal oder Energie.
Bei der Leistungsmessung und Optimierung von Produktionsanlagen hat die Overall Equipment Effectiveness (OEE) als zentrale Kennzahl zur Effizienzbewertung weite Verbreitung gefunden. Die OEE-Methodologie weist jedoch eine Reihe von Schwachstellen auf, u. a. wird die monetäre Dimension des Anlagenbetriebs nur ansatzweise betrachtet. Um diese Schwachstelle zu beheben und zusätzliche Kostenpotenziale zu erschließen, bietet sich eine Kombination der vielfach vorhandenen OEE-Kennzahlen mit Kostendaten aus dem Controlling an. Die daraus resultierende anlagenbezogene Kernkostenanalyse ermöglicht es, monetär bewertete Optimierungshebel zu ermitteln, um sich dem wirtschaftlichen Optimum des Anlagenbetriebs möglichst weit anzunähern.

Die OEE-Kennzahl gibt an, wie effizient eine Produktionsanlage im Vergleich zu ihrem theoretischen Optimum arbeitet. Die Analyse des OEE-Wertes sollte im Kontext der jeweiligen Produktionsumgebung vorgenommen werden: Während in einzelnen Branchen Werte von über 85% erreicht werden, ist in komplexeren Produktionsumgebungen schon ein Wert von 60% ein sehr gutes Ergebnis. © Höveler Holzmann
Overall Equipment Effectiveness
Das OEE-Kennzahlensystem ist in den 1980er Jahren im Rahmen des Total Productive Maintenance-Ansatzes (TPM) entstanden. Ziel des Verfahrens ist die Messung der Produktivität einzelner Anlagen in einer Fabrik. Dazu werden die drei Parameter „Verfügbarkeit“, „Durchsatz“ und „Akzeptanz der erzeugten Produktion“ bewertet. Auf diese Weise fasst das Verfahren die Parameter „Zeit“, „Stückzahl“ und „Qualität“ in einer für das Produktionsteam nachvollziehbaren Art zusammen, wodurch insbesondere auch eine Einbeziehung der Mitarbeiter in die Anlagenoptimierung erreicht wird. Das Verfahren hat sich als dominierendes Verfahren zur Performance-Messung von Anlagen durchgesetzt.
Verfügbarkeit ist der erste Faktor der OEE und misst den Prozentsatz der geplanten Produktionszeit, die tatsächlich für die Produktion genutzt wird. Verfügbarkeitsbeschränkungen, sei es durch Störungen oder Wartezeiten, verringern die Verfügbarkeit und somit den OEE.
Der zweite Faktor der OEE ist die Leistung. Diese bezieht sich auf die Geschwindigkeit, mit der die Produkte hergestellt werden, wenn die Maschinen laufen und vergleicht die tatsächliche mit der theoretischen maximalen Produktionsrate. Einflussfaktoren sind u.a. Kurzstillstände und reduzierte Geschwindigkeit.
Der dritte Faktor bewertet die Qualität der produzierten Einheiten, indem der Anteil der Gutteile an der Gesamtproduktion gemessen wird. Dies umfasst die Analyse von Ausschuss und Nacharbeit, welche die Effektivität negativ beeinflussen, da Ressourcen verwendet werden, ohne qualitativ akzeptable Produkte zu liefern.
Die OEE-Kennzahl – OEE = Verfügbarkeit x Leistung x Qualität – spiegelt wider, wie effizient eine Produktionsanlage im Vergleich zu ihrem theoretischen Optimum arbeitet.
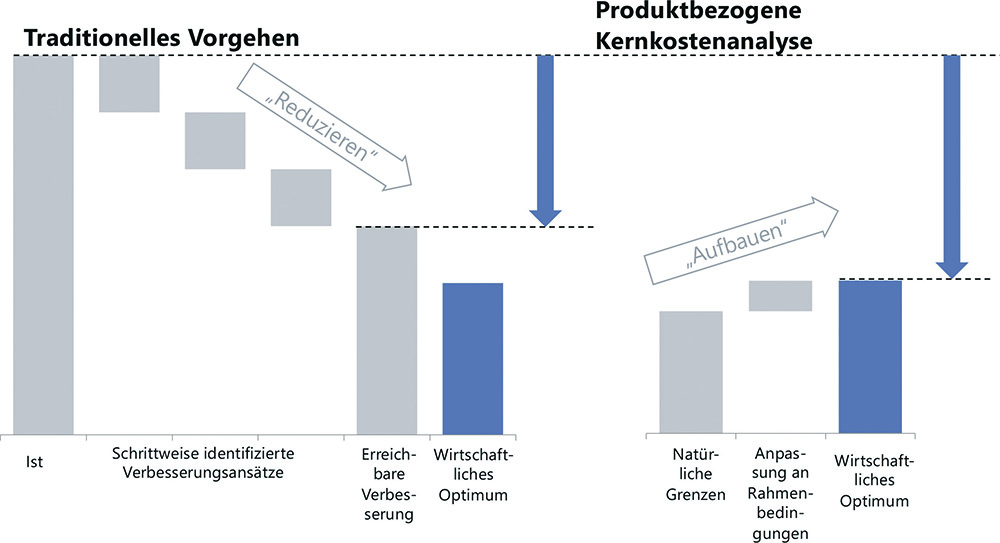
Grundkonzeption der produktbezogenen Kernkostenanalyse. © Höveler Holzmann
Kernkosten
Unter Kernkosten wird der „harte Kern“ der Kosten verstanden, die für den Geschäftserfolg absolut erforderlich sind. Ziel des Verfahrens ist, durch die Berücksichtigung natürlicher Grenzen noch über das vordergründig ausgereizte Kostenniveau hinaus weitere Potenziale zu ermitteln. Bei den Zielkosten handelt es sich um das Kostenniveau, das unter den gegebenen Rahmenbedingungen auch tatsächlich erreicht werden kann.
Der grundlegende Gedanke bei der Ermittlung von Kernkosten für Produktionsanlagen ist, dass es auch bei Produktionsanlagen eine physikalisch-technische Kostenuntergrenze gibt, bei deren Erreichung ein Unternehmen am absoluten Kostenoptimum produzieren würde. Die Kernkosten stellen einen theoretischen Wert dar, der in der Praxis bestenfalls annähernd erreicht wird. Anhand der Kernkosten der Anlage ist erkennbar, ob die aktuelle Kostenstruktur weit vom möglichen Optimum entfernt liegt oder ob bereits relativ nahe am theoretischen Optimum produziert wird. Dies hat einen wesentlichen Effekt auf die Priorisierung dieser Anlage im Rahmen von Kostensenkungsprogrammen.
„Um neue Kostenpotenziale zu erschließen, bietet sich eine Kombination der OEE-Kennzahlen mit Daten aus dem Controlling an.“
Im Gegensatz zur OEE basiert die anlagenbezogene Kernkostenanalyse nicht ausschließlich auf Zeitmessungen an der Anlage, sondern integriert zusätzlich die Kostenstrukturen in die Analyse. So werden Verluste nicht abstrakt in Prozent einer theoretischen Auslastung angegeben, sondern direkt monetär bewertet, um Kostenreduktionspotenziale zu identifizieren und die dazugehörigen Optimierungshebel aufzuzeigen.
Die Differenz zwischen aktuellen Kosten und Kernkosten werden auf sechs verschiedene Optimierungshebel aufgeteilt. Durch diese Analyse lassen sich die entscheidenden Ansatzpunkte zur Kostenoptimierung relativ schnell erkennen.
- Die Auslastung misst die Kosten der nicht genutzten Kapazitäten (im Wesentlichen die anteiligen Fixkosten).
- Der Produkt-Mix stellt die Kosten dar, welche für Produktvielfalt und nicht anlagenoptimale Produkte entstehen.
- Durchsatzkosten entstehen durch Geschwindigkeitsverluste und Kurzstillstände während einer Produktion.
- Kosten für Anlagenstillstände und für Störungsbeseitigungen fallen unter die Kategorie „Störungen“.
- Unter Qualität fallen alle Kosten von nicht einwandfreien Produkten.
- Normabweichungen beinhalten alle nicht im Standard enthaltenen Kosten (z.B. die Kosten einer zusätzlichen Person an der Anlage, über die Standardbesetzung hinaus).
Die auf die Optimierungshebel zu verteilenden Kosten bestehen aus den Fixkosten einer Anlage, wie Abschreibungen oder Werksumlagen, Energiekosten der erforderlichen Medien, Personalkosten der Produktionsmitarbeiter inkl. aller anteiligen Sozialbeiträge und Lohnzusatzleistungen, Sachkosten für Wartungen und Instandhaltungen einer Anlage und die dazugehörigen Personalkosten der Instandhaltungsmitarbeiter sowie die Kosten für Materialverluste bei Rüst- und Reinigungsvorgängen sowie für nicht verkaufsfähige Ware.
Durch die Betrachtung der Kernkosten kann zunächst festgestellt werden, wie groß die Differenz zwischen Ist- und Kernkosten ist. Sollten die Kernkosten im Bereich von über 70 % der Ist-Kosten liegen, sind dies bereits sehr gute Ergebnisse. Bei Werten von unter 20 – 30 % könnte hinterfragt werden, ob überhaupt ein wirtschaftlicher Betrieb der Anlage gegeben ist.
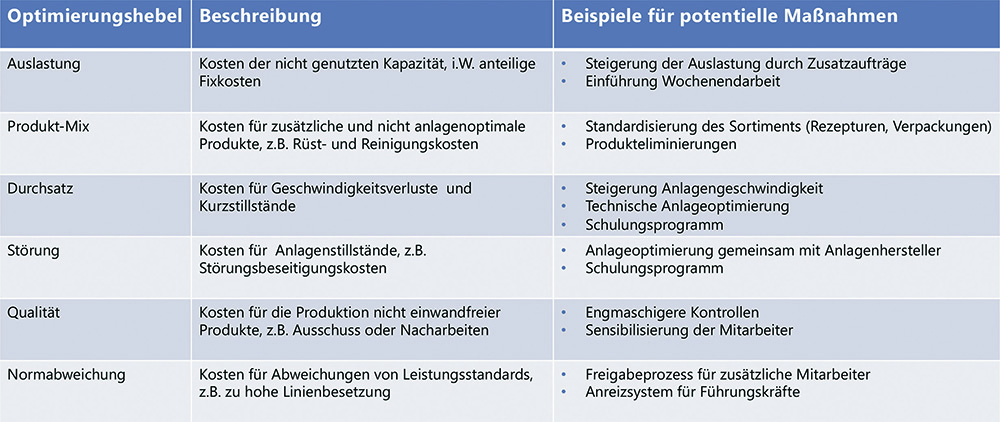
Optimierungshebel der Kernkostenanalyse. © Höveler Holzmann
Einsatzmöglichkeit
Die OEE-Methodologie hat sich in vielen Werken bewährt, um täglich oder wöchentlich die Anlageneffizienzen zu überprüfen. Dieses wird häufig gemeinschaftlich unter Einbezug von Werksleitung, Schichtführern und Anlagenbesetzung durchgeführt. Die anlagenbezogene Kernkostenanalyse soll dies nicht ersetzen, sondern stellt eine zusätzliche Auswertung dar, die idealerweise monatlich erstellt wird und speziell die Management-Ebene des Werkes unterstützt.
Im Ergebnis ermöglicht die anlagenbezogene Kernkostenanalyse, Anlagenverluste auf Optimierungshebel aufzugliedern und monetär zu bewerten. Dadurch wird die finanzielle Größenordnung einzelner Anlagenverluste deutlich, sodass die Ergebnisauswirkungen durch die Reduzierung dieser Verluste direkt abgelesen und entsprechende Optimierungsmaßnahmen abgeleitet werden können.
Autor: Matthias Lütke Entrup und Dennis Goetjes, Partner, Höveler Holzmann Consulting GmbH, Düsseldorf
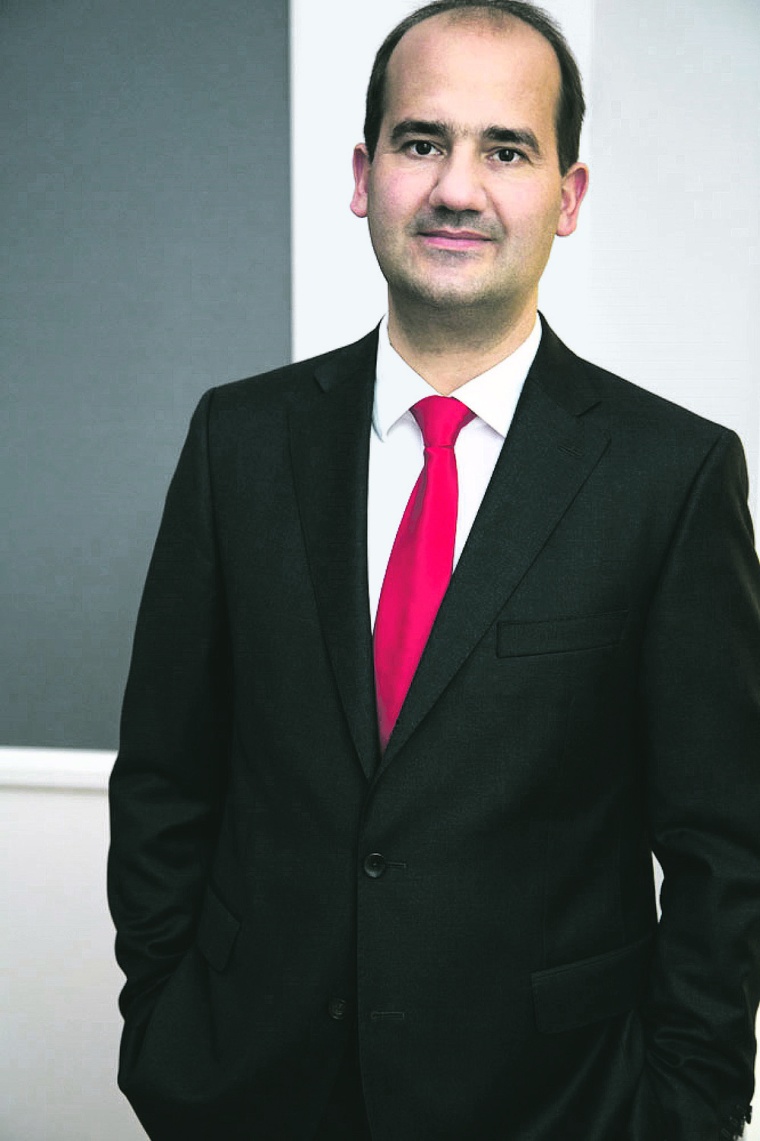
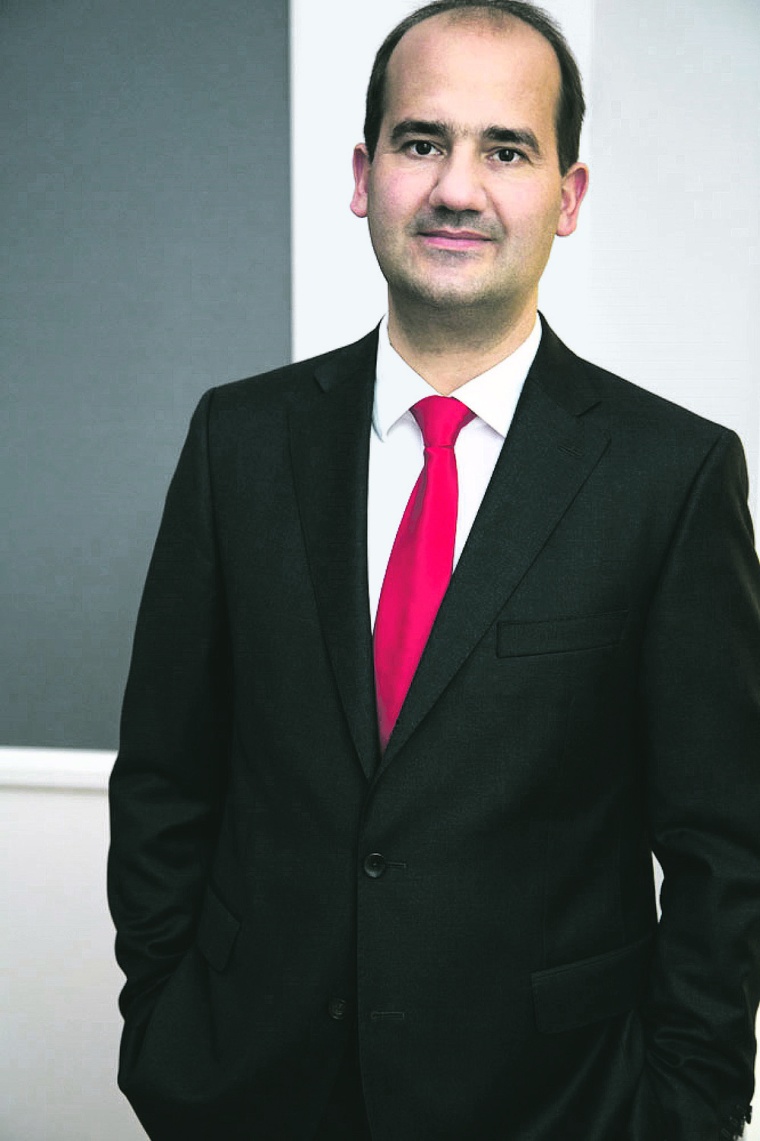
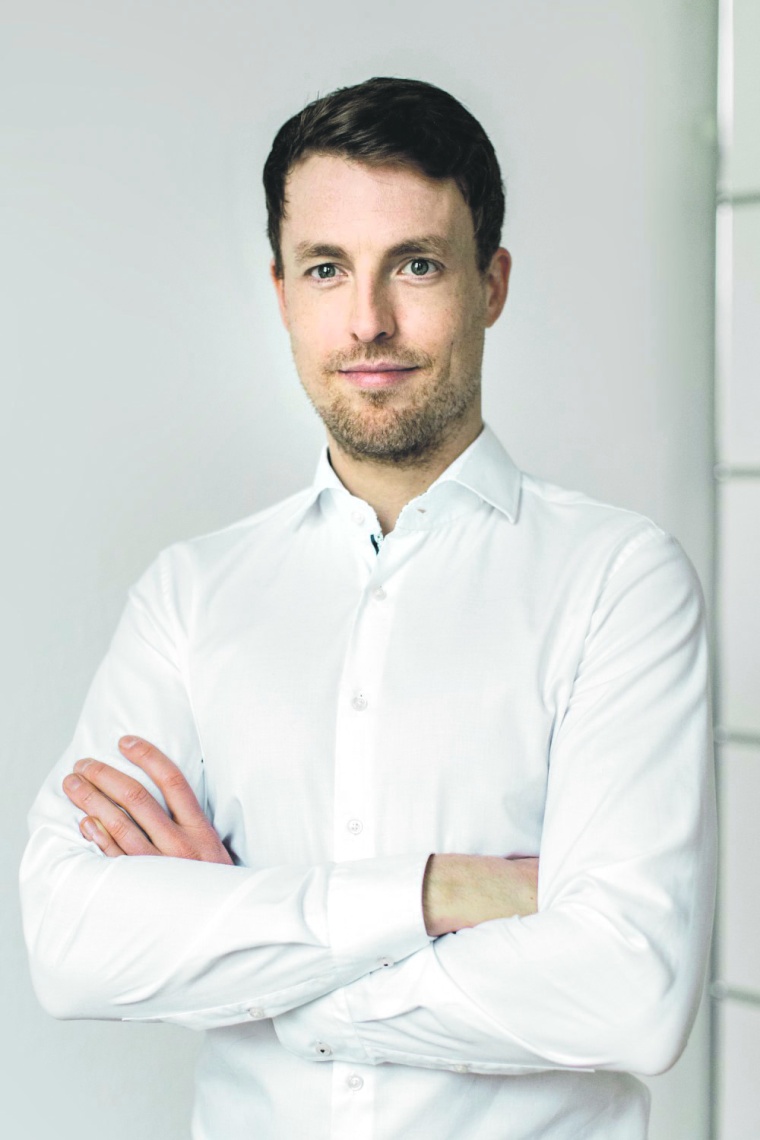