Luftwechsel mal 100
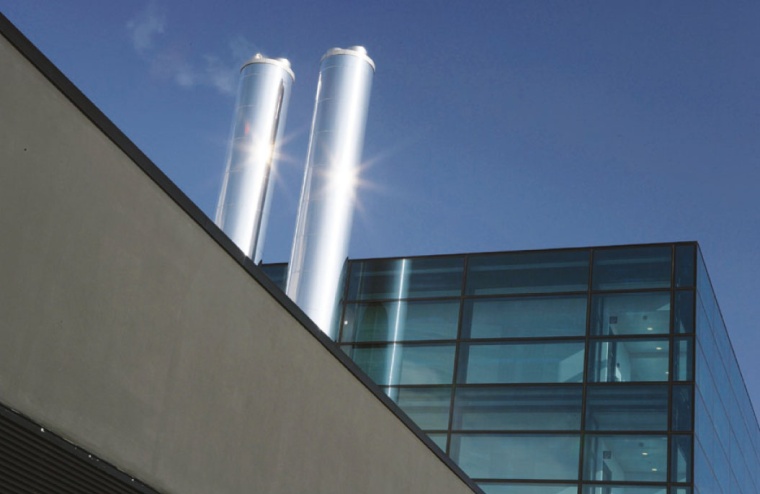
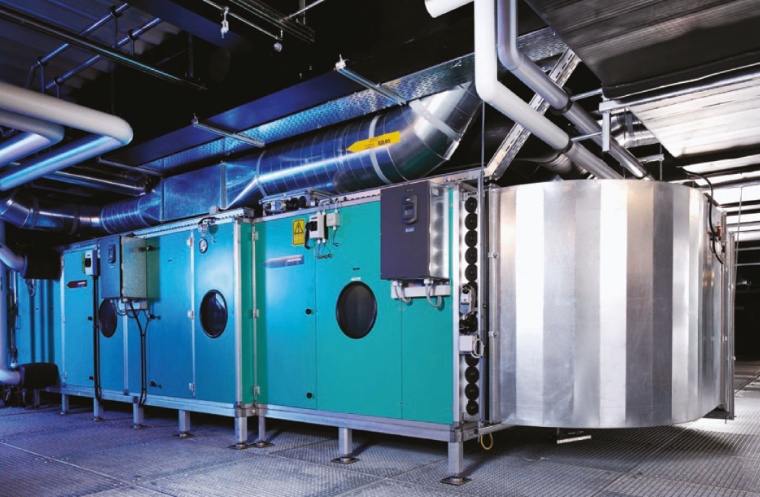
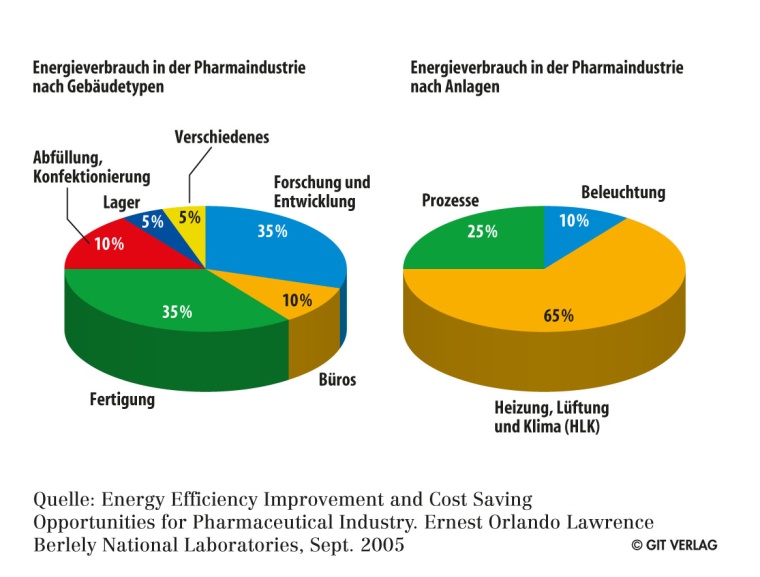
Luftwechsel mal 100 – Energieoptimierung in Life Science-Umgebungen. Nicht der Produktionsprozess, sondern die Heizungs-, Klima- und Lüftungstechnik schluckt in der pharmazeutischen Industrie den Löwenanteil an Energie.
Verbrauchs- und Kostentransparenz ist die Voraussetzung, um Optimierungsmaßnahmen planen und umsetzen zu können. Die Sicherheit von Personal und Produkten hat dabei oberste Priorität.
Mehr als 80 % der Energie in Pharmaunternehmen wird in Gebäuden mit kritischen Bereichen verbraucht, rund 65 % gehen dabei auf das Konto von der Heizungs-, Klima- und Lüftungstechnik.
Der Grund sind die hohen Luftwechselraten, die in den Gebäuden für den Personen- und Produktschutz erforderlich sind.
Zum Teil ist ein mehr als 100facher Luftwechsel nötig, um die Partikelkonzentration zu reduzieren, das heißt, pro Stunde wird die Luft in den sensiblen Bereichen 100 Mal komplett ausgetauscht.
Jeder Kubikmeter Luft muss entsprechend den Anforderungen temperiert und be- bzw. entfeuchtet werden und anschließend durch mehrere Filterstufen den Räumen zu- und abgeführt werden.
Nicht selten sind die Zu- und Abluftventilatoren die größten elektrischen Verbraucher im gesamten Gebäude. Da die Anlagen 24 Stunden am Tag und 365 Tage im Jahr in Betrieb sind, haben Optimierungen hier eine große Hebelwirkung.
Vor diesem Hintergrund hat Siemens seinen klassischen Vor- Ort-Service - Inspektion, Funktionskontrolle, Softwarepflege, Migration - durch den Service „Advantage Gebäudeperformance Optimierung", kurz GPO-Service, weiter ausgebaut. Das AOC „Advantage Operation Center" überwacht Kundenanlagen nicht nur, sondern optimiert diese in Zusammenarbeit mit dem technischen Personal des Kunden und hält sie auf dem neuesten Stand.
Ziel des GPO-Service ist es, die Effizienz der Anlagen zu halten bzw. zu steigern. Der AOC-Operator unterstützt aktiv den Kunden vor Ort und transferiert so Knowhow zum Kunden.
Keine Transparenz ohne Kontrolle
Die Basis für die Energieoptimierung ist eine detaillierte Übersicht der aktuellen Verbrauchssituation. Hierfür bietet Siemens das Energie Monitoring und Controlling (EMC) an, das sich komfortabel über das Internet bedienen lässt und eine in Ergänzung zu einem Gebäudeleitsystem ist.
Die Daten zur elektrischen und thermischen Energie werden automatisch eingelesen oder können manuell eingetragen werden.
Die automatische Auswertung und Aufbereitung der Daten ermöglicht eine verursacherbezogene Zuordnung der Kosten auf Kostenstellen, die automatische Berechnung der CO2-Emission sowie den Vergleich von unterschiedlichen Gebäuden und Nutzern.
Auf Basis dieser Informationen müssen die Benutzeranforderungen hinterfragt und ein Optimierungskonzept erarbeitet werden. Dieses kann folgende Bereiche umfassen:
- Anpassung der Luftwechselraten an unterschiedliche Betriebsarten
- variable Volumenströme gesteuert durch Kalender und Zeitschaltprogramme
- Überwachung der Reinraumbedingungen durch kontinuierliche Partikelmessung
- bedarfsabhängige der Kälteund Wärmeerzeugung mit durchgängiger Vernetzung von Erzeugung, Verteilung und Verbrauchern
- transparente Visualisierung, Alarmierung und Optimierung durch die Gebäude- Leittechnik.
Im Rahmen der Energie-Qualifizierung (EQ) wird der dokumentierte Nachweis erbracht, in wieweit die gesteckten Ziele erreicht werden. Diese Informationen sind insbesondere für den standortübergreifenden Vergleich von Gebäuden hilfreich.
Personen- und Produktsicherheit hat oberste Priorität
An oberster Stelle stehen bei der Energieoptimierung in der Pharmaindustrie die Produktund die Personensicherheit.
Alle geplanten Maßnahmen müssen diesen Grundsätzen genügen. Für die Planung erfordert dies:
- detaillierte Kenntnisse der Prozesse und qualitätsrelevanten Parameter
- ausführliche Bewertung des möglichen Einflusses jeglicher Optimierungen
- intensive Beurteilung aller Risiken und Maßnahmen zur Risikoreduktion
- Änderungsmanagement vor der Implementierung jeglicher Optimierungen
- Abwägung von dem Aufwand für Revalidierung und dem Einsparpotential
- Einhalten einschlägiger Sicherheitsnormen, beispielsweise für Laborabzüge.
Praxisbeispiele
Umgesetzte Projekte zeigen, dass erhebliche Optimierungen möglich und wirtschaftlich sind.
In einem namhaften Forschungszentrum in den USA beispielsweise benannte Siemens auf Basis des Energie- Audits die Kälteerzeugung als erfolgversprechenden Kandidaten für die Optimierung.
Die Pumpsequenzen wurden angepasst, Temperaturregelungen modernisiert, die Sequenzierung der Kältemaschinen verbessert und die Verwendung der Rückkühlwerke verändert. Das Ergebnis: Mit einer Investition von weniger als 390.000 US-$ wurde der jährliche Energieverbrauch um 1.646.268 kWh reduziert. Dies entsprach zu damaligen Preisen einer jährlichen Einsparung von 186.000 US-$.
Die jährlichen CO2-Emissionen gingen um jährlich 450 t zurück. In einem Laborgebäude in der Schweiz brachte die Umrüstung der Laborabzüge von konstantem auf variablen Volumenstrom sowie die Optimierung der Raumdruckregelung eine dauerhafte Halbierung der Luftmenge, die aufzubereiten war.
In einem toxikologischen Forschungszentrum in Deutschland wurden 36 Ventilatoren auf variable Drehzahlregelung umgerüstet und die gesamte Gebäudeautomation erneuert.
Zudem wurde die Beleuchtung modernisiert. Mit einer Investition von ca. 2,7 Mio. € konnte hier der jährliche Energieverbrauch um 7.757.000 kWh reduziert werden, was zu damaligen Preisen einer jährlichen Einsparung von 670.000 € und einer CO2-Reduktion von 5.300 t entsprach.
Kontakt:
Jens Feddern, Global Sector Head Life Sciences
Siemens Schweiz AG,
Building Technologies Group
Tel.: +41 585579383
Fax: +41 417235204
jens.feddern@siemens.com