Instandhaltungsplanungssystems: Optimale Anwendung
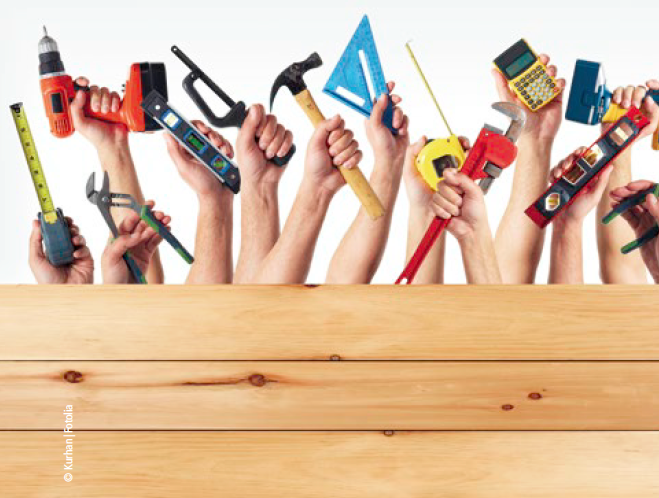
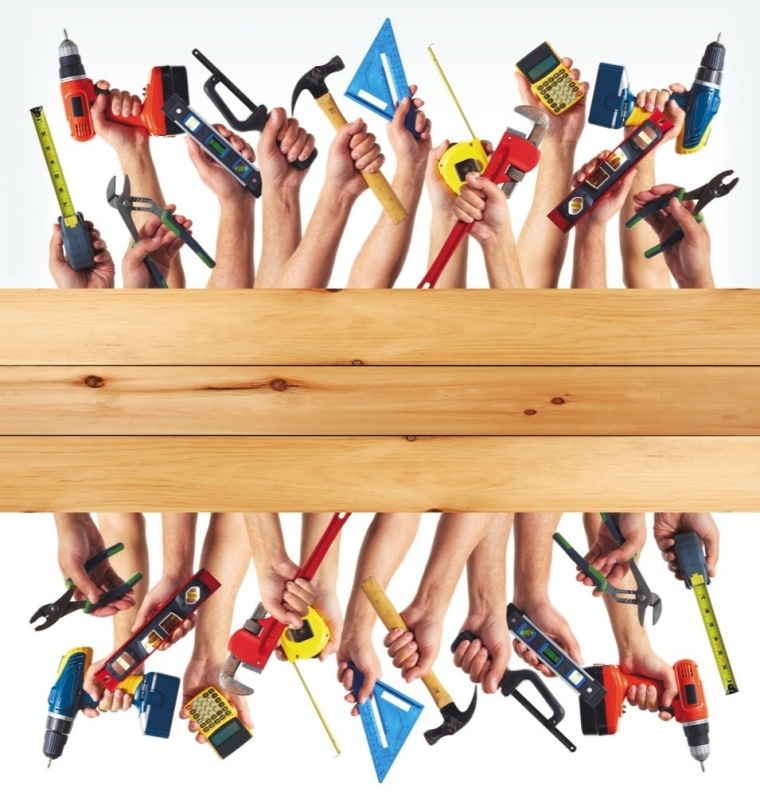
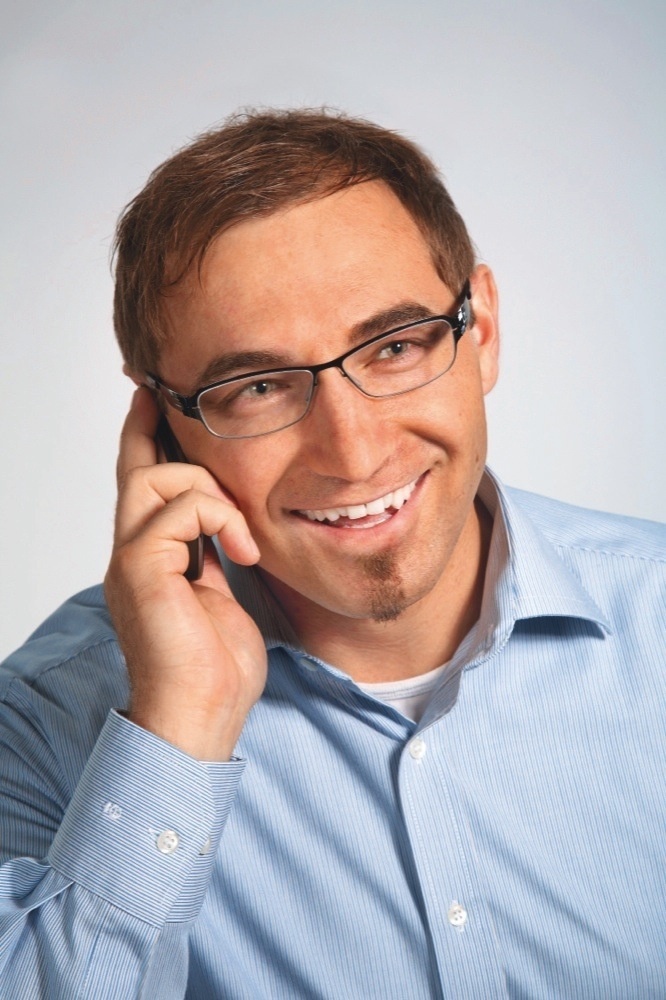
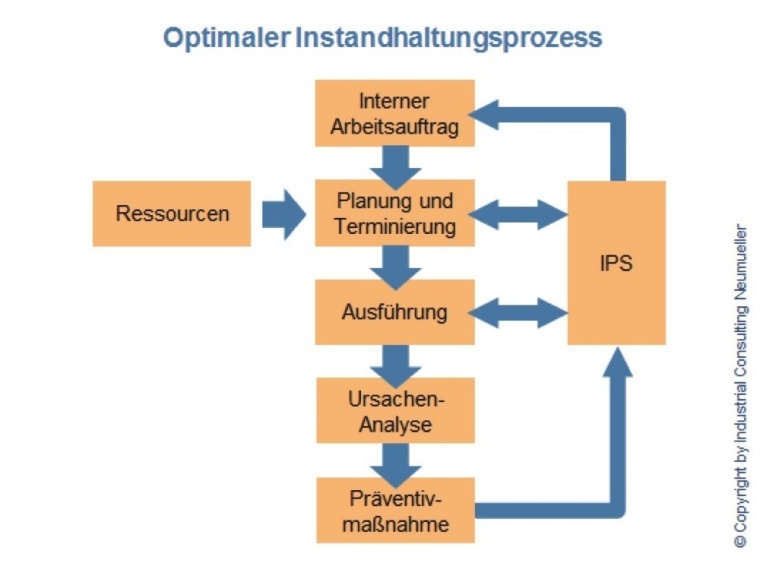
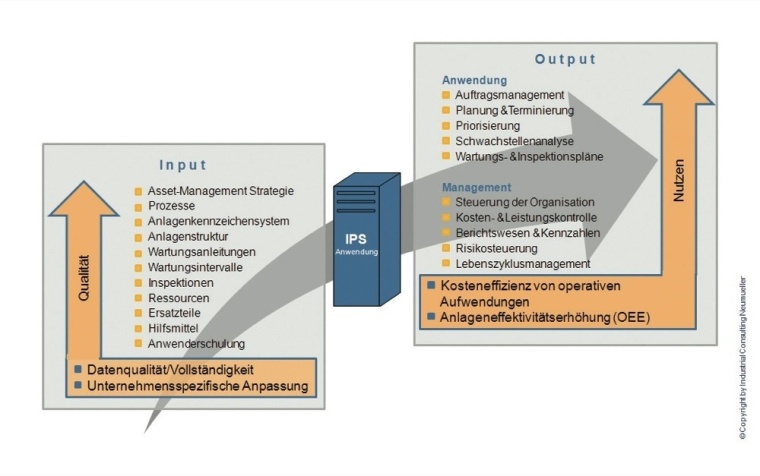
Die effektive Anwendung eines Instandhaltungsplanungssystems (IPS) hängt nicht nur von der Software ab! Die optimale Planung und Steuerung von Prozessen in Instandhaltungsorganisationen zur Optimierung von betrieblichen Aufwendungen und Verlustzeiten wird heute für Unternehmen immer wichtiger. Hohe Instandhaltungsaufwendungen und ungeplante Maschinenausfälle sowie damit verbundene Ausfallkosten müssen nicht sein.
Unternehmen können hier gegensteuern und Planung sowie arbeitsvorbereitende Prozesse systematisieren, um erhöhte Produktivität der Ressourceneinsätze von Personal und Material zu erreichen. Durch den Einsatz eines passenden Instandhaltungsplanungssystems, einer Planungssoftware zur Abbildung der (vorbeugenden) Instandhaltungsprozesse, ist dies für jedes Unternehmen realisierbar.
Am Markt stehen viele verschiedene Systeme zur Auswahl. Der Schlüssel für eine erfolgreiche Anwendung ist nicht nur die Systemauswahl und Datenintegration, sondern die Definition der unternehmensspezifischen Prozesse und Qualität der Daten, wie z. B. Auftragsmanagementprozess oder Inspektions- und Wartungsmaßnahmen. Industrial Consulting Neumueller unterstützt vorab bei der Prozessbereinigung sowie der Datenvorbereitung, betreut den Auswahlprozess sowie alle Phasen der Einführung bis hin zur Anwendung.
Begriffsabgrenzung
Es werden am Markt unterschiedliche Begriffe für unterschiedlich Ausprägungen der Systeme verwendet. Meistens spricht man von einem Instandhaltungsplanungssystem (IPS) oder auch englisch Computerized Maintenance Management System (CMMS) genannt Teilweise werden diese auch Enterprise Asset Management (EAM) genannt.
Letzteres wohl eher aus marketingtechnischen Gründen zur Abgrenzung von Mitbewerbern. Die Anforderungen an ein „Managementsystem" im Sinne des Asset Managements, kann nicht nur durch ein IT-Softwaresystem abgebildet werden, dabei bedarf es weitaus mehr. Ein „EAM" bzw. IPS ist jedoch ein wichtiger Bestandteil dessen.
IPS-Software am deutschen Markt
In Deutschland gibt es eine Vielzahl von Systeme diverser Hersteller am Markt, von denen aber lediglich circa 35 Systeme Auftragsmanagementprozesse nachbilden können und daher als qualifiziertes IPS für die präventive Instandhaltung einsetzbar sind. Sie unterscheiden sich allerdings in der Funktionalität und insbesondere in der Bedienbarkeit sowie der Maskendarstellung.
Des Weiteren bestehen bei den Systemangeboten verschiedene Lizenz- und Preismodelle. Grundsätzlich kann zwischen ERP-Modulen und autarkem Softwaresystem (Sekundärsystem) unterschieden werden. In den letzten Jahren wurde eine deutliche Zunahme der autarken Systeme beobachtet, die sich vor allem durch praxisnahe Features auszeichnen. Dabei ist die Integration in die bestehende ERP-Softwarelandschaft und Primärsysteme (z. B. Marktführer SAP R/3) oftmals durch Standardschnittstellen gegeben.
Besonders die grafische Planungsunterstützung und Schwachstellenanalyse ist bei ERP-geführten IPS-Modulen (z. B. SAP PM) gegenüber den autarken Systemen noch unterentwickelt. In der Praxis sind deshalb unterstützende Tools (z. B. makroprogrammierte Exceltools zur Schwachstellenanalyse) unerlässlich für eine hohe Produktivität, jedoch ebenso gut und einfach anwendbar.
Auswahlprozess einer geeigneten Software in einem pharmazeutischen Produktionswerk
In einem Workshop mit dem Kunden und den praxiserfahrenen Beratern von Industrial Consulting Neumueller wurden als erstes die Rahmenbedingungen festgelegt. Dazu gehörten die Festlegung von Zielen der Systemeinführung wie Kostenoptimierung und Strategieänderung (proaktiver statt reaktiver Instandhaltung), Budget, Implementierungszeitraum, benötigte Ressourcen sowie Bestimmung von operativen Rahmenbedingungen.
Dabei war eine Vielzahl von Definitionen zu berücksichtigen, eine kleine Auswahl davon ist:
- In welchem System wird die Materialwirtschaft abgebildet?
- Sollte eine Schichtbuchfunktionalität im IPS verankert sein?
- Welche Schnittstellen zu weiteren (Primär-) Systemen werden benötigt?
- Künftige Anwendungskosten des Systems?
- Welche Instandhaltungsmaßnahmen werden (künftig) erbracht?
- Welche weitere möglichen Funktionen müssen abgestimmt werden?
Als nächster Schritt wurde ein Lastenheft als Grundlage für eine Ausschreibung eines geeigneten Software-Lieferanten erstellt.
Die in Frage kommenden Systeme wurden anhand eines umfangreichen Bewertungskatalogs mit knapp 200 unterschiedlichen Kriterien analysiert. Anschließend erfolgten die Live-Vorstellungen der mit dem Kunden ausgewählten Favoriten und vor Ort Begehung bei Referenzkunden der Systemhersteller.
Je höher die Datenqualität bei der Einführung, desto größer ist der Anwendernutzen
Beim sogenannten Einführungsprozess werden alle Stammdaten erfasst und bereinigt. Dazu gehört die Bestimmung der Anlagenstruktur mit allen administrativen und technischen Ebenen. Hierbei kommt es besonders einem Maschinenund Anlagenpark zu einer durchgängigen Definition der Objektebenen an.
Industrial Consulting Neumueller empfiehlt in diesem Zuge alle Anlagenkomponenten einer Risiko- und Kritikalitätsbewertung zu unterziehen. Ableitend von den definierten operativen Instandhaltungsstrategien wurden die vorhandenen Wartungspläne angepasst und kombinierte Inspektions- und Wartungspläne erstellt um gleichzeitig eine vorbeugende und zustandsorientierte Instandhaltung einzuführen. Die Kritikalitätsbewertung gibt somit indirekt die Instandhaltungsintensität an technischen Komponenten an.
„Zum Beispiel bedarf die Zentralhydraulik an einem Extruder einer anderen Instandhaltungsintensität im Form einer frühzeitigen Ausfallerkennung als eine Hilfsaggregat an der Verpackungslinie." Die Definition des spezifischen Auftragsmanagementprozesses war hierfür ebenfalls notwendig. Für diese Prozessgestaltung wurde ein Workshop durchgeführt, an diesem ein relevanter Personenkreis aller hierarchischer Ebenen aus Produktion, Instandhaltung und Controlling und Einkauf teilnahm.
Frühzeitige Planungen entscheidend
Für eine erfolgreiche Einführung und Anwendung sind frühzeitige Planungen der Prozesse und entsprechende unternehmensspezifische Definitionen entscheidend. Werden, wie in vielen Fällen geschehen, keine spezifischen Prozesse definiert, das System „nur" in seiner Standardanwendung genutzt, entsteht oftmals eine negative Systemakzeptanz und die Erwartungen des Systemnutzens bleiben unerfüllt.
Der Grund hierfür liegt auf der Hand:
„Das Softwaresystem gibt durch die Standardanwendung meist Prozessschritte vor (was praktisch bedeutet, dass bestimmte Felder gefüllt werden müssen oder Status gesetzt werden) die einfach nicht zur Organisation passen.", so Ulrich Neumüller. Neben Berechtigungskonzepten müssen letztendlich auch Kennzahlen in Form eines Kennzahlen- und Reportingsystems definiert werden.
Besonders erfolgreich hat sich die Zuordnung von Verantwortlichkeiten zu Kennzahlen und die Definitionen von Soll-Ist-Abweichungen erwiesen. Wird der Systemoutput in Form von zielgerichteten Berichten nicht richtig genutzt, erweist sich das System als ein unwirtschaftliches „Datengrab". „Das erleben wir in der Praxis sehr häufig".
Auch hier sind Abstimmungen gefragt, besonders die beliebte Kennzahl OEE (zu deutsch: Gesamtanlageneffektivität) muss klar definiert werden um Transparenz zu erzeugen. Ein weiterer umfangreicher Part ist die Integration der Materialwirtschaft. Hier besteht in den meisten Fällen ein besonders großes Einsparpotential. Eine Lagerbestandsoptimierung im Zuge einer klaren integrierten Ersatzteil- und Fremdleitungsstrategie ist teilweise bis zu 40 % möglich.
„Vom Betroffenen zum Beteiligten"
Mehr als die Hälfte aller Veränderungsprojekte scheitern. Das wichtigste Instrument bei der Einführung eines IPS ist das Change Management: Das Veränderungsprojekt muss nach Change Management Kriterien durchgeführt werden. Bei einer Nichtbeachtung sind Resistenzen bei den Mitarbeitern vorprogrammiert. Deshalb: Frühzeitig die Mitarbeiter in die Veränderung einbeziehen und ein geeignetes Informationskonzept anwenden. Ganz im Sinne: „vom Betroffenen zum Beteiligten". So lässt sich vorbeugen, dass unnötige Ängste vor zu viel Transparenz und Kontrolle entstehen.
KONTAKT
Ulrich Neumüller
Industrial Consulting Neumueller, Schiltberg
Tel.: +49 8259 8979798
info@ic-neumueller.com