Heißgasentstaubung und NOx Reduzierung in der Zementindustrie
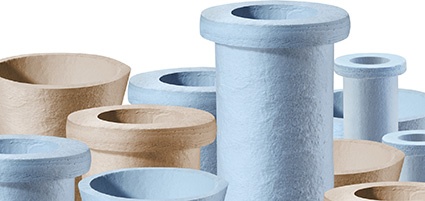
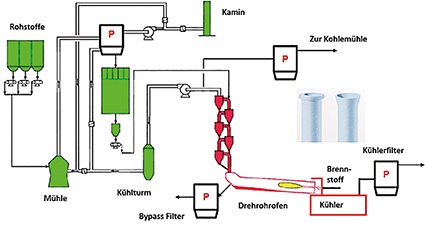

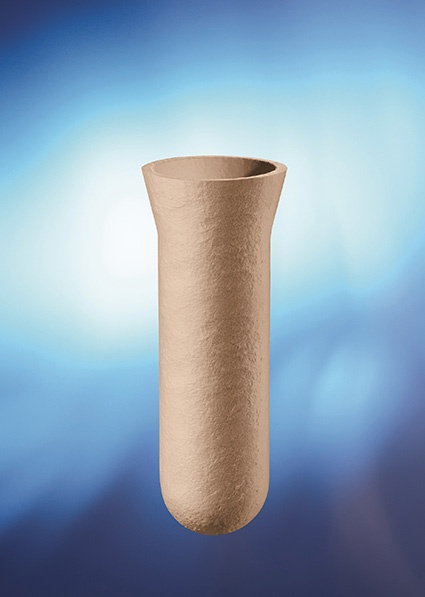
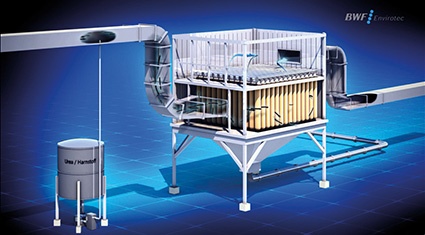
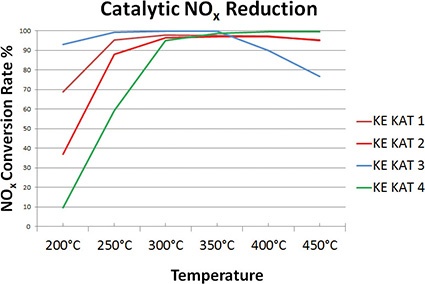
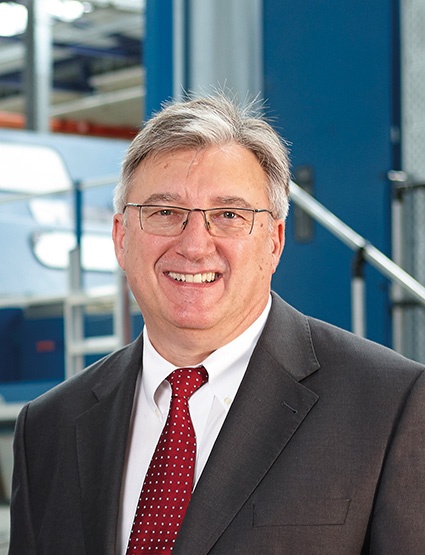
Zementhersteller werden weltweit ihre Aktivitäten zur Staubkontrolle verbessern müssen. Eine zukunftsweisende Lösung dafür könnte die Pyrotex KE-Technik sein.
In Zementwerken auf der ganzen Welt haben sich Zyklone, Elektrofilter und Gewebefilter einzeln oder in Kombination in der Staubbekämpfung durchgesetzt, wobei jedes System seine eigenen Vorteile bietet. Die bekannte und bewährte Technik der Elektrofilter ist in der Lage, Staubemissionsgrenzwerte von 5–10 mg/Nm3 einzuhalten. In der Zementindustrie können E-Filter bis zu einer Betriebstemperatur von ca. 450 °C eingesetzt werden. Allerdings werden das für die Ofenaustrittsgase benötigte Gas, und das Gas für die Klinkerkühlung nicht gekühlt. Bei Bypass-Filtern müssen die Gase in Abhängigkeit der Ofenaustrittstemperatur mit Luft oder Wasser gekühlt werden. Eines der überzeugendsten Argumente für die Installation eines E-Filters ist deren einfache Bedienung. Zudem ist der Wartungsaufwand vergleichsweise gering und kostengünstig, da hier weniger Komponenten verbaut sind, als dies bspw. bei Gewebefiltern der Fall ist. Andererseits ist der Platzbedarf bei einem Elektrofilter enorm und möchte man die Staubemissionen noch weiter reduzieren, so wird der Filter extrem groß und der Stromverbrauch steigt drastisch. So kann der Ausbau eines E-Filters, bspw. um neue Emissionsgrenzwerte einzuhalten, zu höheren Fix - und Betriebskosten führen. Zumeist können vorhandene E-Filter in bestehenden Anlagen aufgrund des verfügbaren Raums nicht ausgebaut werden. Zudem kann es sein, dass die vorgeschriebenen verminderte Emissionsziele gar nicht mehr erreicht werden können.
Filterumwandlung
Immer wieder zwingen Änderungen der Verordnungen und strengere Emissionsgrenzwerte die Branche, sich nach neuen Lösungen umzusehen. Verminderte Emissionen im Bereich von ca. 3–5 mg/Nm3 können auch über Gewebefilter erreicht werden, die einen geringeren Platzbedarf als E-Filter haben. So erstaunt es nicht, dass die Branche reagiert hat, indem bestehende E-Filter Anlagen entweder insgesamt oder teilweise in Gewebefilter umgebaut wurden. Diese Art der Filterumwandlung hat sich in der Zementindustrie durchgesetzt und angesichts der Vorgabe neuer Grenzwerte wird erwartet, dass in den kommenden Jahren weltweit weitere Anlagen nachgerüstet werden. Dennoch zahlt sich die Nachrüstung nur bei sachgemäßer Umsetzung aus. Einige der Probleme sind auf die substanziellen Unterschiede zwischen den beiden Systemen zurückzuführen. Zu diesen grundlegenden Unterschieden gehören die Strömungsrichtung der Rauchgase sowie die Betriebstemperatur.
Bei einem E-Filter müssen die Rauchgase die Niederschlagselektroden horizontal durchströmen. In einem Gewebefilter durchströmen die Rauchgase vertikal durch die Filterelemente. Dementsprechend muss der Luftstrom bei einem Gewebefilter vertikal verlaufen.
Ein E-Filter kann bei etwa 450 °C betrieben werden, wohingegen die Temperatur bei einem Gewebefilter von der Art der eingesetzten Filtermedien begrenzt wird. Die maximale Dauerbetriebstemperatur bei Gewebefiltern liegt bei 250–260 °C, sodass die Rauchgase gekühlt werden müssen. Das Filtermedium kann hierbei ein Gewebe aus Nadelfilz oder gewebter Glasfaser sein. Beide Gewebe können mit Polytetrafluorethylen (e-PTFE)-Membranmaterial ergänzt werden. Wegen der sehr geringen Porengröße der Membran von 1–2 µm, können die geringeren Emissionsraten von ca. 3–5 mg/Nm3 erreicht werden. Der Kristallit Schmelzpunkt von PTFE liegt bei 327 °C, sodass eine mögliche aktive Dauerbetriebstemperatur von 288 °C möglich scheint. Die praktischen Dauerbetriebstemperaturen der Filtration liegen jedoch im Bereich von höchstens 250–260 °C. Um also die Gewebefiltermedien zu schützen, muss wertvolle Wärmeenergie für das Kühlen der Rauchgase verschwendet werden. In vielen Fällen, in denen über Luft gekühlt wird, handelt es sich bei 30–50 % der durch den Gewebefilter geführten Luft um die Luft, die zum Herunterkühlen der Rauchgase auf die gewünschte Temperatur erforderlich wird.
Auch bei hohen Temperaturen beständig
Das Kühlen der Rauchgase kann vermieden werden, wenn das Filtermedium auch für höhere Temperaturen ausgelegt ist. In diesem Fall bieten sich die folgenden Möglichkeiten:
- Die Luftmenge kann reduziert werden, was Stromkosten am Gebläse Motor spart.
- Somit kann die Produktionskapazität gesteigert werden, ohne dass die Kapazität des Ventilators erhöht werden muss.
- Die sauberen Gase haben eine höhere Temperatur und müssen somit nicht für eine mögliche SCR-NOx-Reduktion erhitzt werden. Dies spart Kraftstoff und damit Kosten.
Die Wärmeenergie der sauberen Heißgase kann entweder als Wärmeenergie zum Trocknen von Rohstoffen oder von Kohle verwendet werden. Zudem können diese sauberen Heißgase auch zur Produktion von Strom eingesetzt werden.
Starre Filterelemente haben sich in der Glasherstellung schon seit langem etabliert. Sie sind in der Zementindustrie noch neu. BWF Envirotecs‘s Markenname für dieses Produkt ist Pyrotex KE. Damit lassen sich extrem geringe Staubemissionen von weniger als 1 mg/Nm3 erreichen. Diese Filterelemente bestehen aus Kalzium-Magnesium-Silikat-Fasern, die nicht kanzerogen und biolöslich sind. Diese Fasern sind für die Gesundheit unbedenklich.
Hohe Luftdurchlässigkeit, geringer Differenzdruck
Die für die Herstellung der Pyrotex KE-Filterelemente verwendeten Werkstoffe sind auch bei hohen Temperaturen beständig, und bleiben auch bei konstanten Betriebstemperaturen von bis zu 850 °C stabil. Werden diese Elemente in den Anlagen zur Staubkontrolle der Rauchgase aus dem Zementofen, einem Ofen-Bypass-Filter und der Staubkontrollanlage des Klinkerkühlers eingesetzt, müssen die Rauchgase nicht herabgekühlt werden. Thermische Heizenergie muss nicht verschwendet werden, ca. 1 Megajoul Wärmeenergie kann pro 10 t Klinker eingespart werden.
Im Vergleich zu anderen erhältlichen Filterelementen, weisen die Pyrotex KE-Filterelemente eine geringe Dichte auf, was ein vergleichsweise niedriges Gesamtgewicht ermöglicht. Aufgrund der geringen Dichte des Aufbaus, verhält sich die Luftdurchlässigkeit der Filterelemente des Offinger Herstellers ähnlich wie bei Glasfasern mit Membranmaterial. Mit der hohen Luftdurchlässigkeit geht ein geringer Differenzdruck einher.
Die erste erfolgreiche gewerbliche Installation der Pyrotex KE-Filterelemente in einem Klinkerkühler mit einer Betriebsleistung, welche die Auslegungsparameter bei weitem übertrifft und insbesondere mit einem hohen, günstigen Differenzdruck überzeugt, hat den Weg für die erfolgreiche Zukunft geebnet. Bei dieser Anwendung liegt der Reinigungsdruck bei etwa 2,0–2,5 bar, sodass sich ein Differenzdruck von 10–12 mbar über das gesamte Filter ergibt. Angesichts der hervorragenden Luftdurchlässigkeit benötigt diese Anlage lediglich einen kompletten Reinigungszyklus pro Tag. Somit darf mit einer erhöhten Lebensdauer der Pyrotex KE-Elemente gerechnet werden.
Die Pyrotex KE-Elemente sind mit Durchmessern von 60 und 150 mm erhältlich. Der obere Kragen kann als V- oder T-Kragen ausgeführt werden. Der V-Kragen hat sich in der Glasindustrie durchgesetzt, dennoch werden auch immer mehr T-Kragen angefragt. Damit wird der Austausch der regulären Filter deutlich einfacher. Die Elemente stehen in verschiedenen Längen zur Verfügung. Das längste Element ist in einem Stück ausgeführt und bietet eine Gesamtlänge von 4,5 m. Alle Elemente von mehr als 4,5 m sind modular ausgelegt und werden vor Ort miteinander verbunden. Die Elemente von 8 m Länge befinden sich in der Testphase und Elemente von 6 m Länge sind bereits für gewerbliche Anlagen lieferbar.
Zusätzlich zur überragenden Entstaubungsleistung von ≤1 mg/Nm3, können die Filterelemente mit einem Katalysatormaterial zur Reduzierung des NOx-Gehalts per Selektive Katalytische Reduktion (SCR) ausgestattet werden. Bei der klassischen NOx-Reduktion als Selektiver Nicht-Katalytischer Reduktion (SNCR) wird Harnstoff oder Ammoniak im Temperaturbereich zwischen 850–1.050 °C eingedüst. Auch bei der NOx-Reduktion mit Pyrotex KE muss Harnstoff oder Ammoniak eingedüst werden, aber aufgrund des Katalysators funktioniert das Ganze im niedrigeren Temperaturbereich von 200–450 °C.
BWF Envirotec bietet zur Zeit vier unterschiedliche Katalysatoren an, die in diesem Temperaturbereich arbeiten. Bei der Auswahl des Katalysators müssen die spezifischen Eigenschaften der Prozessgase überprüft und entsprechend berücksichtigt werden.
Geringste, derzeit realisierbare Staubemissionen
Die Pyrotex KE-Elemente sorgen als Einzellösung für die geringsten, derzeit realisierbaren, Staubemissionen von weniger als 1 mg/Nm3. In Kombination mit einem Katalysatormaterial können die Pyrotex KE-Elemente zudem andere gasförmige Emissionen und zwar insbesondere NOx herausfiltern. Durch die Möglichkeit des Einsatzes bei erhöhten Temperaturen lässt sich so auch die Reduktion von SOx mit Kalziumhydroxid (Ca(OH)2) optimieren. Die besten SOx-Reduktionsergebnisse mit Ca(OH)2 werden bei 350 °C erzielt, was oberhalb der Temperaturen liegt, denen Gewebefiltermedien standhalten.
Die Pyrotex KE-Elemente erfüllen diese Anforderung. Da nunmehr eine einzige Anlage zur Staubkontrolle den Staub sammelt und die gasförmigen Emissionen reduziert, sinken insgesamt die Investitions- und Betriebskosten für diese Art von Filter, der mit einem besonders wirtschaftlichen Wirkungsgrad aufwarten kann.
Jeder Prozess erfordert maßgeschneiderte Lösungen und zwar insbesondere dann, wenn letztlich eine NOx-Reduktion mit SCR-Katalysatorsystemen erreicht werden soll. Auch die Energieeinsparungen werden jeweils von Fall zu Fall einer eigenen Prüfung unterzogen. In manchen Fällen ist es schon von Vorteil, wenn bereits das Kühlen der Rauchgase entfällt. Wir haben gesehen, dass saubere Heißgase zur Trocknung von Werkstoffen verwendet werden. Wird die Pyrotex KE-Technik für die Filtration von heißem Zementklinker eingesetzt, so können diese sauberen Heißgase sogar als Verbrennungsluft für andere thermische Prozesse verwendet werden. Ein Anlagenbauer, der sich auf die Kraft-Wärmekopplung mit einem Zementwerk spezialisiert hat, führt an, dass der wirtschaftlichste Ansatz zur Stromerzeugung mit einer Ofengröße von ≥ 5.000 t/d Klinkerproduktion realisiert werden kann.
Es liegt auf der Hand, dass mit immer strengeren Emissionsanforderungen verschiedene neue Technologien und Lösungen auf den Markt kommen werden. Die Pyrotex KE-Technik könnte zu den zukunftsweisendsten Lösungen für die Zementindustrie gehören.