Bioethanol - Energiemanagement verringert Produktionkosten drastisch
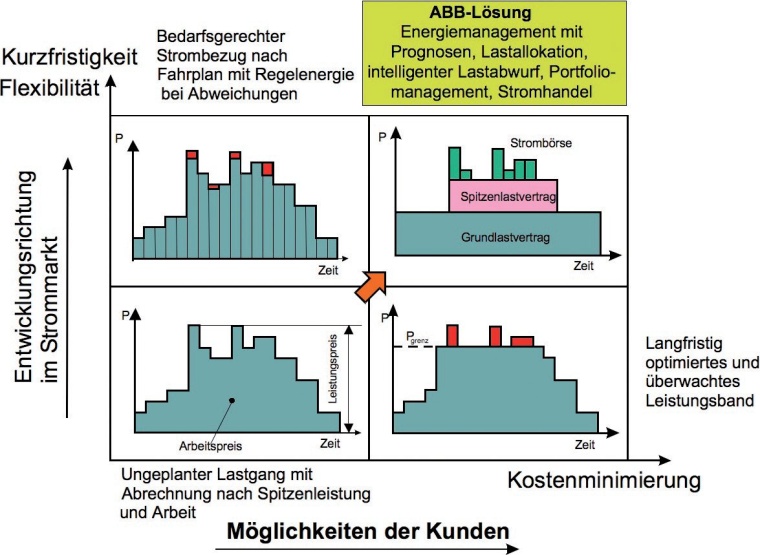
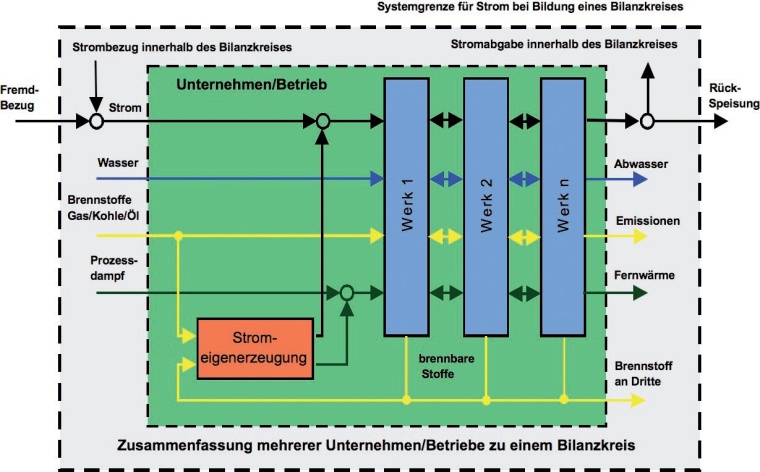
Bioethanol - Energiemanagement verringert Produktionkosten drastisch
Die Produktion von Bioethanol ist sehr energieintensiv und natürlich steht dieser Kraftstoff auch im Wettbewerb zu anderen Biokraftstoffen wie Biodiesel und Butanol. Das ABB Forschungszentrum in Ladenburg hat den Energieverbrauch in Biodieselanlagen eingehend untersucht und Lösungen zur Senkung des Energieverbrauchs bzw. der Energiekosten entwickelt. Sie erlauben eine Senkung des Energieverbrauchs um bis zu 10 % durch eine intelligente Steuerung und Optimierung der Produktionsanlage.
Die Europäische Union hat Biokraftstoffe als strategische Lösung für die zunehmende Energieproblematik erklärt und dazu eine Direktive herausgegeben. Bis 2010 sollen demnach 5,75 % der im Verkehrssektor verbrauchten Kraftstoffe biologischen Ursprungs sein. Die Produktion von Bioethanol wird daher in den nächsten Jahren und danach langfristig und nachhaltig zunehmen.
Seit Beginn dieses Jahres hat die Mineralölindustrie die Verpflichtung, eine feste Quote der jährlichen Kraftstoffproduktion durch Biokraftstoffe zu erfüllen. Vor dieser Regelung wurden Biokraftstoffe im Vergleich zu herkömmlichen Kraftstoffen durch Steuererleichterungen gefördert. Die verschiedenen Biokraftstoffe werden in Zukunft im starken Wettbewerb zueinander stehen und genau auf ihre Produktionskosten untersucht werden.
Der Energieverbrauch trägt hierzu einen signifikanten Teil bei. Durchschnittliche Anlagen mit einer Kapazität von 200.000 bis 300.000 t/a Bioethanol haben einen Energieverbrauch von ungefähr 8 – 10 MW. In den USA hat die jährliche Produktionskapazität im Jahr 2005 bereits 100 Mio. t überschritten. Da die Energiepreise in Nordamerika jedoch im Vergleich zu Europa recht niedrig sind, bestand hier noch nicht die Notwendigkeit den Energieverbrauch von Bioethanolanlagen zu verringern.
Um im Wettbewerb mit anderen regenerativen Energien, insbesondere mit anderen Biokraftstoffen wie Biodiesel und Butanol, langfristig bestehen zu können, muss die Produktion von Bioethanol effizient sein. Am ABB Forschungszentrum in Ladenburg wurde daher der Produktionsprozess (Abb. 1) eingehend analysiert. Ein genaues Verständnis wo und warum der größte Teil der Energie bei der Produktion verbraucht wird, ist unabdingbar (siehe Tab.). Sobald die großen Verbraucher in der Prozesskette identifiziert sind, können Technologien entwickelt werden, die den Verbrauch reduzieren und so die Effizienz erhöhen. Obwohl die meisten dieser noch recht neuen Methoden bis jetzt nicht in großem Umfang angewendet wurden, zeigen einige das Potential, den Energieverbrauch und die Produktionskosten drastisch zu verringern.
Prozess und Energieverbrauch
Bioethanol wird aus zuckeroder stärkebasierenden Anbaupflanzen gewonnen, wie beispielsweise Zuckerrohr, Mais oder Weizen. Um die Energieanforderungen einer Bioethanolanlage zu verstehen, werden die wichtigsten Prozessschritte betrachtet. Bei der so genannten Hydrolyse von stärkebasierenden Rohstoffen wird dem Getreide Wasser hinzugefügt, um eine Verzuckerung zu erreichen. Um die Temperatur auf circa 60°C zu erhöhen und so eine Verflüssigung zu erzielen, werden ungefähr 10 % des gesamten Energieverbrauchs benötigt. Danach werden Enzyme in der Fermentierung zu der Zuckermasse hinzugefügt, die fermentierte Maische wird destilliert, um den Alkoholgehalt zu erhöhen.
Da die Maische in der Destillationskolonne stark erhitzt werden muss, wird hier auch etwa ein Drittel der im Gesamtprozess eingesetzten Energie verbraucht. In der Destillation wird das Bioethanol am Kopf der Kolonne abgezogen, während die schwerere so genannte Vinasse sich am Boden der Kolonne sammelt. Die protein- und ballaststoffreiche Vinasse wird üblicherweise getrocknet und in Pellets (engl. DDGS, Dried Distillers Grains with Solubles) gepresst, die als Tierfutter verkauft werden können. Dieser Trocknungsprozess verbraucht jedoch große Wärmemengen und ist daher ebenfalls für nahezu ein Drittel des Energieverbrauchs verantwortlich.
Ansätze zur Reduzierung der Energiekosten
Um die Energiekosten zu reduzieren kann man zwei verschiedene Ansätze verfolgen: Ein neues, am Energieverbrauch orientiertes Prozessdesign oder ein intelligentes Energiemanagement (Abb. 2). Mit Änderungen am Design der Anlage lassen sich zwar höhere Energieeinsparungen erzielen, dafür ist jedoch ein Umbau der Anlage nötig. Mit den Lösungen von ABB zum Energiemanagement ist es möglich, eine Produktionsanlage intelligenter zu steuern.
Die Planung kann, basierend auf einer guten Vorhersage für Strom und Dampfverbrauch, beispielsweise mehrere Wochen im Voraus vorgenommen werden. Damit wird ein gleichmäßigerer Energieverbrauch erreicht. Lastvorhersagen können, bei richtiger Einstellung, automatisch aus der Produktionsplanung abgelesen werden. Eine optimierte Lastzuteilung (Abb. 3) kann ebenfalls zu Energieeinsparungen beitragen.
Wird in einer Anlage Energiemanagement intelligent betrieben, so kann der Verbrauch der existierenden Anlage um ungefähr 10 % reduziert werden. Die meisten Anlagen werden heutzutage nur nach betrieblichen Kriterien optimiert. Ziel der Maßnahmen zum effizienteren Energiemanagement ist es jedoch, den Betrieb des Energiesystems sowohl unter betrieblichen als auch unter finanziellen Gesichtspunkten zu optimieren. Oft wird beispielsweise in der Anlage nicht nur Strom verbraucht, sondern durch Prozesserweiterungen auch Strom produziert. In solchen Fällen kann der Verbrauch von eigen- und fremdproduziertem Strom an die Anforderungen angepasst werden. Berichtswesen und Energiekostennachverfolgung ermöglichen außerdem eine Echtzeit-Überwachung der Produktionskosten.
Wenn die Möglichkeit besteht beim Neubau einer Anlage oder innerhalb eines Retrofits den kompletten Produktionsprozess so zu designen, dass nicht der Durchsatz, sondern der Energieverbrauch optimiert wird, dann ergeben sich noch wesentlich höhere Einsparpotentiale durch die Optimierung der Massenund Wärmebilanzen. Forscher an der TU Wien haben zum Beispiel herausgefunden, dass die Erhöhung der Temperatur in der Destillationskolonne von 60°C auf ungefähr 90°C und in der anschließenden Gleichrichterkolonne auf ungefähr 130°C sinnvoll sein kann. Netzwerke von Wärmetauschern können die Abwärme aus der Gleichrichterkolonne zur Vorerhitzung der Destillationskolonne nutzen.
An der Carnegie Mellon University (CMU) in Pittsburgh, mit dem das ABB Forschungszentrum eine strategische Kooperation unterhält, wurde ein anderes, energieeffizientes Prozessdesign entwickelt. Bei diesem Aufbau werden Teile des Trocknungsprozesses zur Tierfuttergewinnung vor der Destillationskolonne platziert und damit der Energieverbrauch reduziert. Dampf- und Kühlwasserverbrauch können zusätzlich reduziert werden, indem eine Multieffekt-Destillationskolonne zum Einsatz kommt.
Eine Studie, die von Forschern der CMU an Ethanolanlagen in den USA vorgenommen wurde, zeigt Verbesserungspotentiale von mehr als 50 % an Strom, Wasser und Dampf auf, die durch die beschriebenen Ansätze erzielt werden können. Bioethanol, das in neuen, optimierten Anlagen hergestellt wird, wird in Zukunft wettbewerbsfähig werden. Die von ABB durchgeführte Analyse zeigt zudem, dass die Potentiale noch nicht ausgeschöpft sind.