Steam, Sugar And Salt
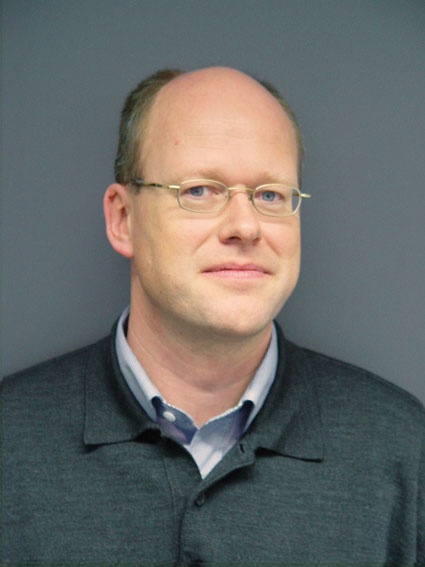
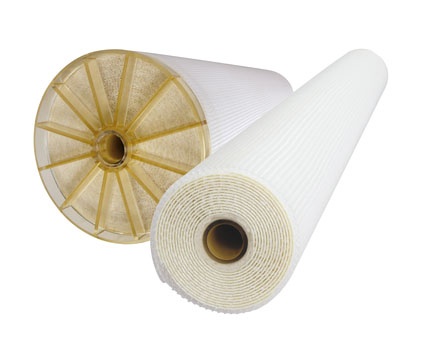
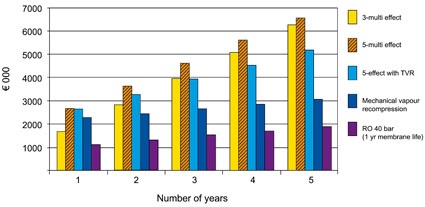
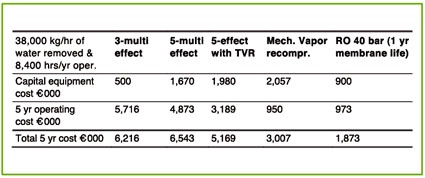
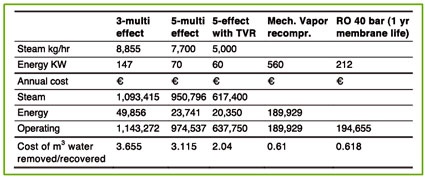
The EU food ingredients manufacturers face continuing pressure to improve base line profits against continuing increase in cost of operations due to energy, water, raw materials and environmental legislation. Climate control policies with increased utility cost and demand for reducing CO2 emissions require companies to re-examine their operations. Ingredient production steps frequently incorporate product recovery steps employing centrifugation, rotary vacuum filtration, evaporation, and spray drying demanding high energy inputs.
Many companies which employ evaporation as a standard de-watering step in the manufacture of products such as dairy food ingredients, sugars, sweeteners, beverages, organic acids, renewable source bio-fuels etc., can potentially reduce their carbon foot print with membrane technology. Product and process waste streams often contain small molecular weight components that can be concentrated, desalted, or, in some applications, fractionated with membrane filtration technology. Substantial capital and operating cost benefits together with selective separations can be derived by use of low energy consumption membrane technology - as a complete stand alone process step or in conjunction with evaporation enabling product recovery and water for reuse.
Two Ways
In comparison to a five-effect evaporator with thermal vapor recompression, reverse osmosis membrane technology can offer more than 75% reduction in operating cost. Mechanical vapor recompression evaporators offer the lowest operating cost - similar to membrane technology, but with a considerably higher capital investment. The dairy industry has utilized membrane filtration technology to derive high value products from whey, which was historically a cheese manufacturing waste product. Today the complete range of membrane filtration technologies covering microfiltration, ultrafiltration and nanofiltration are employed to clarify, concentrate, desalt or fractionate whey components. Reverse osmosis (RO) also offers the recovery of high quality water from the process for reuse.
Steam And Energy
Evaporation is a well-established process in the dairy, food and other manufacturing industries requiring an increase of solids content in aqueous streams by effecting water removal. Through development and improvements of evaporator equipment designs the required steam and energy input could be reduced. This resulted in lower operating costs. Local combined heat and power co-generation can considerably reduce the steam cost and argue for steam heated mechanical vapor recompression (MVR) evaporator. Low-cost energy may support the multi-effect evaporator with thermal vapor recompression (TVR). Conventional multi-effect, steam heated evaporators offer the lowest capital investment but present the highest operating cost due to the steam requirements and design efficiencies. Unfortunately, whilst increasing the evaporator operating efficiency, the additional process equipment requirements enlarge the hardware costs. The condensed vapor can provide suitable quality for direct reuse in the manufacturing process or it may require further treatment to remove any carryover components.
Membrane Systems
RO is a pressure (typical 20 to 40bar g) driven process that enables recovery of dissolved materials (proteins, peptides, sugars, salts, etc.) present in feed streams typically operating at 20~50°C. Filtered water can be suitable for secondary application reuse. Generally ~20 to 30% total solids are achieved dependent on the feed stream composition. The contribution of dissolved salts and sugars to osmotic pressure is the main limiting factor. Nanofiltration (NF) membrane technology offers the potential to recover protein, peptides, amino acids and partial rejection of some salts and sugars that can afford some selectivity of the final product profile. By reducing sugars and salts in the stream, improved product quality can be gained when spray dried. NF permeate would require polishing with RO to provide a quality suitable for a secondary reuse application. Membrane filtration as a stand alone process allows for 50 to 99% removal of the liquid phase. Further dewatering with evaporation can achieve the required higher solids concentration. Usually, the installation cost for membrane filtration equipment is substantially less than evaporation equipment due to the compact foot print. Membrane system design affords simple modular expansion.
Economics
The example is based on a stream containing ~6% total dissolved solids that is dewatered to obtain ~12% TDS. The membrane system is a fully automated plant. The operational cost includes energy and membrane replacement on an annual basis. Plant location and method of steam generation will dictate cost which can vary from as low as €10 to €25 for 1,000 kg of steam produced. The installation of a cost-covering system and the building to house the equipment, have been excluded. Membrane system foot print and installation costs will be relatively low in comparison to evaporation equipment.
Conclusion
The example demonstrates that evaporation equipment based on MVR offers an operational cost similar to RO technology, but requires twice the capital investment cost. A new installation would require a cost evaluation to establish the capital cost benefit of an RO and MVR combined installation. Existing installations with current evaporation systems based on multi-effect and including TVR could benefit from RO dewatering with return of investment in one to two years. Future requirements to reduce water and energy consumption or facilitate the expansion of the production need to look for alternative and combined dewatering technologies.
Company
Koch Membrane SystemsKackertstr. 10
52072 Aachen
Germany
most read
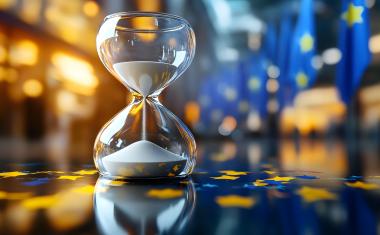
Standing Strong for Europe's Chemical Industry
Rising tariffs and regulatory changes challenge the European chemical industry, highlighting the need for resilient regional supply networks and strategic collaboration among CEFIC members.
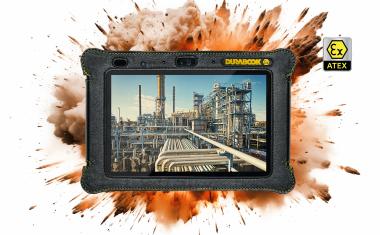
Rugged Tablets: How to Successfully Digitize Hazardous Areas
Digital processes in hazardous areas? Durabook's rugged tablets are ATEX-certified for industrial use.
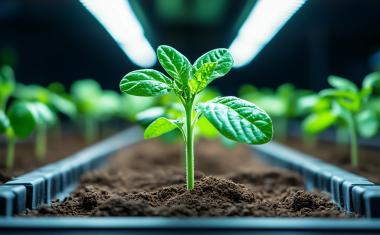
Phytoinitiator mRNAs as a Game Changer in Agriculture
Unlocking nature’s resilience: phytoinitiator mRNAs empower plants to thrive in deserts, saline soils, and harsh climates—no gene editing required.
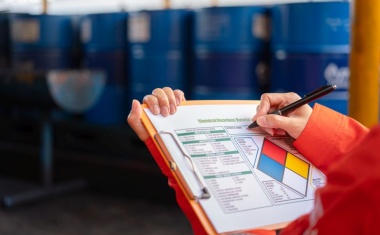
Substances of Concern
The EU Chemicals Strategy for Sustainability (CSS) highlights the shift to a hazard-centric approach in EU chemical regulation, emphasizing 'Substance of Concern' over risk-based measures.
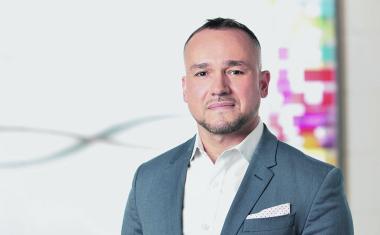
“Access to Talent is a Crucial Factor”
In an interview with CHEManager, Edgardo Hernandez, President of Lilly Manufacturing, explains the strategy behind the ambitious investment project.