Maximize the Potential of Spent Hydroprocessing Catalysts
A new approach is helping reduce waste, recover value, and deliver on sustainability goals.
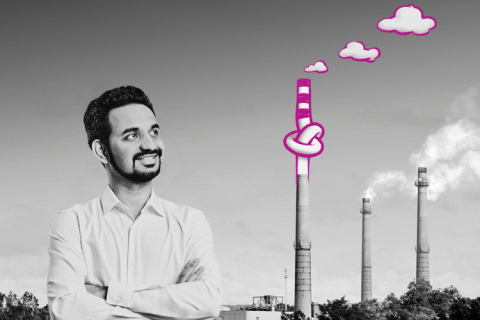
Hydroprocessing units, such as hydrotreaters and hydrocrackers, rely on high-performance catalysts to remove sulfur, nitrogen and other impurities from petroleum streams. But once the catalysts are deactivated, what’s next?
Historically, spent hydroprocessing catalysts were considered hazardous waste and commonly sent to landfill. Over time, metal reclamation became the standard – recovering valuable metals like molybdenum (Mo), cobalt (Co) and nickel (Ni) through energy-intensive processes. While an improvement, the approach still falls short of maximizing value and sustainability potential.
Today, a smarter alternative is gaining traction: reprocessing spent catalyst for reuse. Much like choosing to refurbish rather than scrap a used car, refiners can opt for solutions that recover more value, reduce waste and align with environmental and regulatory expectations.
Sustainability Gains
Hydroprocessing catalysts are rich in valuable metals critical to catalyst performance; when sourced through traditional mining, they come at high environmental and economic cost.
Refineries worldwide generate thousands of tons of spent hydroprocessing catalysts annually. They often contain significant residual metal content and active material that, while no longer optimal for fresh use, can be recovered or rejuvenated. Despite their potential, a large portion of these spent materials still end up being treated for metal reclamation or landfilled – a missed opportunity for sustainability.
By focusing on the reuse potential of hydroprocessing catalysts, companies can:
- Avoid the environmental costs associated with mining virgin metals
- Reduce hazardous waste generation; and
- Minimize CO₂ emissions.
A Multi-purpose Solution
Traditional end-of-life management for hydroprocessing catalysts often stops at metal recovery – stripping out valuable metals and discarding the rest. While salvaging some value, it leaves a significant portion of material underutilized and adds to landfill waste.
Through its catalyst acquisition program, Evonik transforms spent hydroprocessing catalysts into an asset by assessing their full reuse potential. Each container is sampled, sorted and screened to determine the best way forward. The tailored approach ensures refiners extract the maximum value from every load while simplifying logistics and compliance.
A unique tiered pricing system rewards customers based on the composition and condition of their spent materials, with recovery of Mo value ranging from 20-75%. Evonik’s approach has kept more than 113,000 tons of spent catalysts out of landfill to date.
Acquisition in Action
In one example, spent hydroprocessing catalysts acquired through Evonik’s program were repurposed as feedstock for Excel Rejuvenation Technology (a proprietary process that restores catalytic activity to near-fresh levels). By reusing existing catalyst substrates instead of manufacturing new ones, the process delivers substantial sustainability and cost benefits, including 60% reduction in waste and CO₂ equivalent emissions, and a significant cut in raw material demand.
Conclusion
The way refiners manage spent hydroprocessing catalysts is rapidly evolving; landfilling and basic metal recovery no longer align with the industry’s push toward sustainability, circularity and cost-efficiency.
Evonik’s catalyst acquisition program offers a smarter, integrated alternative that helps refiners reduce waste, reclaim value and improve environmental performance. By recovering reusable metals, enabling regeneration, and diverting material from landfill, the program supports a circular catalyst lifecycle. With deep technical expertise, global reach and a proven track record, Evonik is the ideal partner to help refiners turn spent catalysts into strategic assets, and close the loop.
Jignesh Fifadara, Global Business Director for Hydroprocessing at Evonik,
Peter Douvry, Head of Catalyst Acquisitions and Specialties at Evonik
About Evonik Catalysts
We have been a leader in the catalyst and adsorbents industry for more than 75 years and remain at the forefront of the sector. This is thanks to our ‘complete package’ approach which involves innovative and sustainable products, comprehensive services, and expert customer care. We produce and provide catalysts and adsorbents all over the world.
Get in touch with Evonik Catalysts