Dynamic Pilot Trials

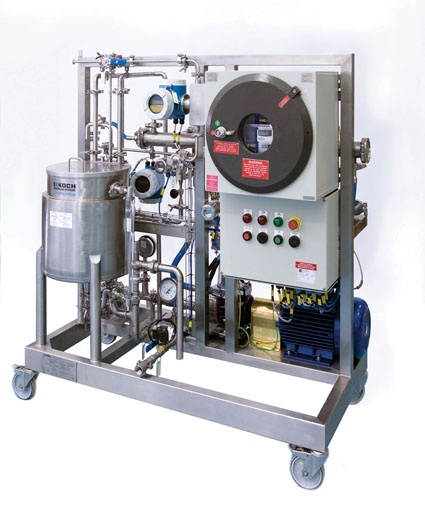
Design Flexibility - Emerging from the current economic crisis with new products and strengthened processes is easier said than done, because development and large-scale implementation require time and large investments. Membrane pilot plants can be a cost and resource effective tool for chemical, pharmaceutical and biotechnological production - and also for the optimization of existing processes.
Cross-flow membrane technology has made great advances in recent decades as a technically innovative and cost-effective separation process to stand alongside conventional separation processes such as distillation, extraction and crystallization. In addition to low investment and operating costs it offers a higher product yield and simplified process management. Membrane filtration falls into four categories: microfiltration (MF), ultrafiltration (UF), nanofiltration (NF) and reverse osmosis (RO). Table 1 shows the corresponding separation ranges or pore sizes, operating pressures and some typical application examples in the chemical, pharmaceutical and biotech industries.
The Path from Idea to Process
The most important component in a membrane process is the membrane to be used. During development the sooner the right membrane is selected, the safer and more successful the next steps and final process will be. In addition to the relevant experience of the membrane manufacturer or supplier, small laboratory membrane systems are a useful way of initially identifying the appropriate membrane (fig. 1). Small quantities (500 ml) of the filtering medium are used for proof of concept experiments. Flatsheet membrane pads with a membrane area of 28 cm2 are operated in cross flow mode - like the future pilot plant and large-scale plant. The gear pump of the KMS Laboratory Cell CF-1 enables the simulation of processes requiring up to nine bar operating pressure. Processes which need up to 35 bar pressure, are simulated by pressurizing the process vessel from an external inert gas source.
After successfully selecting one or more membranes, the next step is to determine the optimal process and operating parameters, such as pressure, temperature, flow velocity, resistance of the membrane process (batch, semi-batch, continuous), performance over a longer period of time, process safety, the number of membrane stages and the appropriate cleaning strategy. An ideal tool for this task is a membrane pilot plant which has been specifically designed for processes in the pharmaceutical, biotech and chemical industries. Piloting with small membrane systems provides a reliable basis for the subsequent up-scaling and verification of the process and allows different operational scenarios and conditions to be simulated. Shortened development time results in reduced costs so that investment to market timescales can be minimized. Membrane pilot plants can also be an ideal tool to optimize existing processes.
Staying Unrestricted Is Key
What are the requirements for a membrane pilot plant in chemical, pharmaceutical or biotech industries? In order to be prepared for as many applications and processes as possible, the installation of MF, UF, NF and RO membranes should be possible. This affects both the selection of membrane housings and pumps. A compact and portable design permits the use in the development and production environment. The use should not be restricted to one product or process at one location. Easily transported to remote sites, it can be employed for a variety of tasks. Flexible connectors allow the use at overseas sites, thus offering international companies a maximum return on their investment.
Compliance with standards such as cGMP and ATEX is a prerequisite. In order to validate plant design and traceability of the materials used, documentation must be comprehensive and complete (FAT, IQ, QC, etc). All materials should be selected so that both aqueous flows as well as organic solvents can be processed.
The provision of an additional membrane housing, which permits serial and parallel operation, is another plus in the selection of this type of equipment. In order to process even small quantities with sufficient volume concentration, the hold-up volume of the plant should be a few liters only. Comprehensive measurement and control devices, a facility to control process temperature, and data logging that allows export to current tools such as Microsoft Excel spreadsheet software or Labview graphical programming software complete the package of an ideal pilot plant. An example of which is the pharmaceutical Spirapro Pharma Pilot Plant from Koch Membrane Systems (KMS). The company has over 35 years experience and is a global leader in separation and filtration products for the food and life science sectors and the chemical industry.
The pilot plant (fig. 2) was developed specifically for the demands in the pharmaceutical and biotech industries, and can operate with one or two membrane housings in series or parallel. The housings are designed for standard spiral membranes of 2540 style and thus - depending on the process and application - allow the use of various spiral membranes of this size. This enables, for example, the filtering of streams that have high acid or alkali concentrations. The organic solvent-stable SelRO NF membranes from KMS can be used for this purpose. The 25-litre process tank can be increased to 100 liters and connection to an external process tank is also possible. The hold-up volume of the plant is five liters. The maximum operating pressure is 40 bar with a speed controlled feed and recirculation pump. To capture the most important operating parameters an operating unit and data logger is incorporated, which allows the export of data via a USB port.
Conclusions
With the Spirapro Pharma Pilot Plant, membrane filtration process development and scale up studies can be accomplished for high value products and especially when only limited volume of material is available during the development phase of a new product. Especially in such troubled economic times, the cost-effective use of existing R&D resources is a key to success in the rapid development of new products and processes. Membrane pilot plants are an ideal tool to optimize existing processes and thus to increase the efficiency.
Company
Koch Membrane SystemsKackertstr. 10
52072 Aachen
Germany
most read
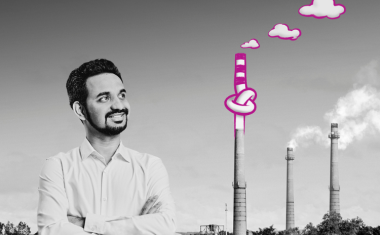
Maximize the Potential of Spent Hydroprocessing Catalysts
A new approach is helping reduce waste, recover value, and deliver on sustainability goals.

ISPE Good Practice Guide: Validation 4.0
The Validation 4.0 Guide provides a comprehensive approach to ensuring product quality and patient safety throughout a pharmaceutical product's lifecycle.
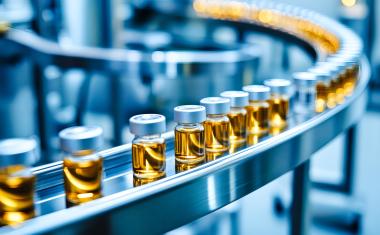
Pharma Outlook 2025
The environment for pharma in 2025 is diverse and challenging: New treatment options are being brought to market in ever shorter cycles.
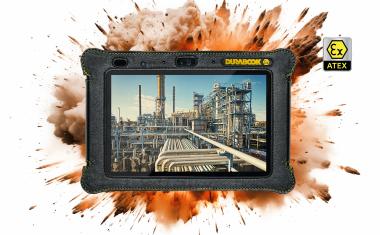
Rugged Tablets: How to Successfully Digitize Hazardous Areas
Digital processes in hazardous areas? Durabook's rugged tablets are ATEX-certified for industrial use.
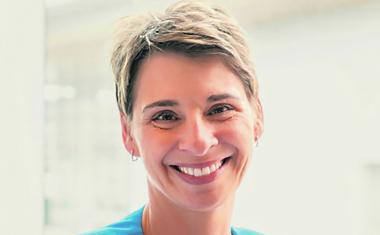
Specialty Chemicals in a Shifting World
Jennifer Abril, President & CEO of SOCMA, discusses the impact of new tariffs and the importance of regional supply networks in the specialty chemical industry.