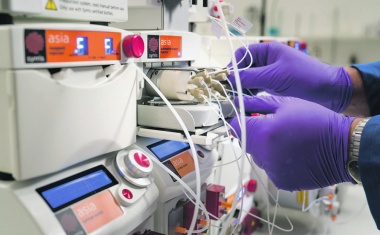
Flow Chemistry in Drug Discovery
For the synthesis of compounds in pharmaceutical applications, it is important to select the most appropriate flow chemistry regime and equipment based on the goals of the application.
For the synthesis of compounds in pharmaceutical applications, it is important to select the most appropriate flow chemistry regime and equipment based on the goals of the application.
Interview with Sridhar Balaram, Founder and CEO of Flownetics Engineering.
For CDMOs, the adoption of flow chemistry can provide a competitive advantage by improving efficiency, safety and quality, while reducing costs and development times.
Headquartered in Cramlington, UK, Sterling Pharma Solutions is a contract development and manufacturing organization (CDMO) that provides a range of services to the global biopharmaceutical industry, including active pharmaceutical ingredient (API) development, scale-up and cGMP manufacturing, as well as antibody drug conjugate (ADC) R&D and clinical-scale GMP manufacturing.
Numerous articles have been published within the last years in chemical science and business media (including this one) on the advantages of continuous reactions, aka flow chemistry.
Japan’s AGI Group, a producer of scientific precision glassware, has acquired flow chemistry company Chemtrix, based in Echt, the Netherlands. Chemtrix’s flow reactor portfolio delivers increased process safety, reduced operating costs and new chemical possibilities at scales ranging from milligrams in the lab through to tons for manufacturing.
Italian CDMO Flamma Group intends to invest $200 million over the next three years to expand its capabilities to meet growing market demand.
Executives and industry experts share their views on drivers as well as barriers for the use of flow chemistry in pharmaceutical manufacturing and the prospect for this technology in their industry sector.
Executives and industry experts share their views on drivers as well as barriers for the use of flow chemistry in pharmaceutical manufacturing and the prospect for this technology in their industry sector.
Given the challenges the pharmaceutical industry is facing – secure material supply, reduce operation cost and increase flexibility, enhance sustainability and safety, innovate and reduce time-to-market – the sector is poised for a breakthrough of flow chemistry.
Executives and industry experts share their views on drivers as well as barriers for the use of flow chemistry in pharmaceutical manufacturing and the prospect for this technology in their industry sector.
Traditional batch chemistry is too inefficient for a sustainable future. Switching batch processing to continuous processing is inevitable if the world is to reach net zero.
Executives and industry experts share their views on drivers as well as barriers for the use of flow chemistry in pharmaceutical manufacturing and the prospect for this technology in their industry sector.
Executives and industry experts share their views on drivers as well as barriers for the use of flow chemistry in pharmaceutical manufacturing and the prospect for this technology in their industry sector.
Executives and industry experts share their views on drivers as well as barriers for the use of flow chemistry in pharmaceutical manufacturing and the prospect for this technology in their industry sector.
Executives and industry experts share their views on drivers as well as barriers for the use of flow chemistry in pharmaceutical manufacturing and the prospect for this technology in their industry sector.
At an online roundtable event hosted by CHEManager, a group of industry experts discussed the reasons why microreaction technology (MRT) has not achieved the status for instance in fine chemicals and active ingredients production that one might expect as well as various business and production aspects of the technology.
After an initial euphoria, the use of microreaction technology stagnated, but it is now on the way to establishing itself in production. A world-scale system is currently being set up in China that uses the Miprowa technology from Ehrfeld Mikrotechnik.
In 2020, the weakness associated with global chemical supply chains was highlighted in a dramatic manner as Covid-19 was designated a global pandemic. As a result, small modular continuous flow plants are gaining attention as an appropriate solution to secure supply chains whilst ensuring safe, sustainable processes are implemented.
The change in many chemical companies’ product portfolio away from commodities to customer-specific specialties is one of the current challenges facing the process industry.
The change in many chemical companies’ product portfolio away from commodities to customer-specific specialties is one of the current challenges facing the process industry.
The change in many chemical companies’ product portfolio away from commodities to customer-specific specialties is one of the current challenges facing the process industry.