Sustainability With Fossil Resources
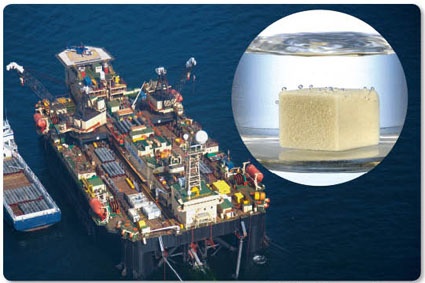
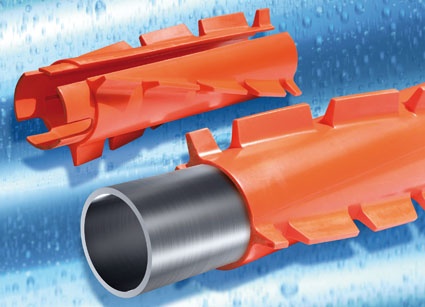
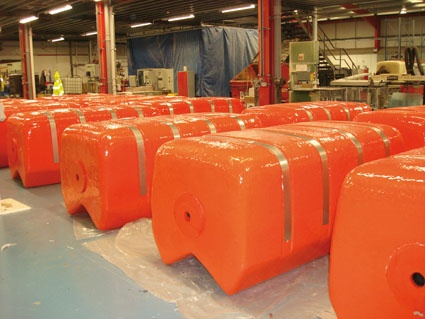
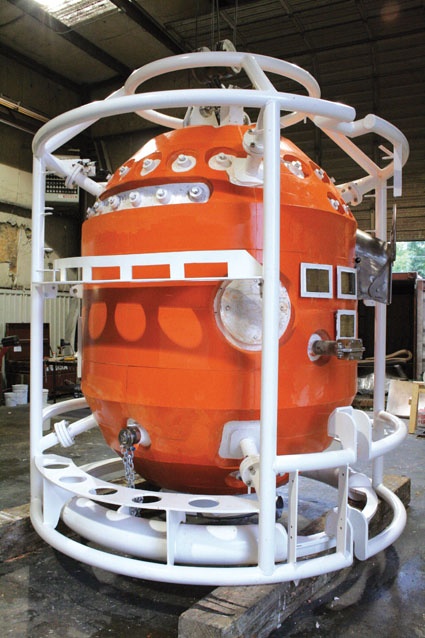
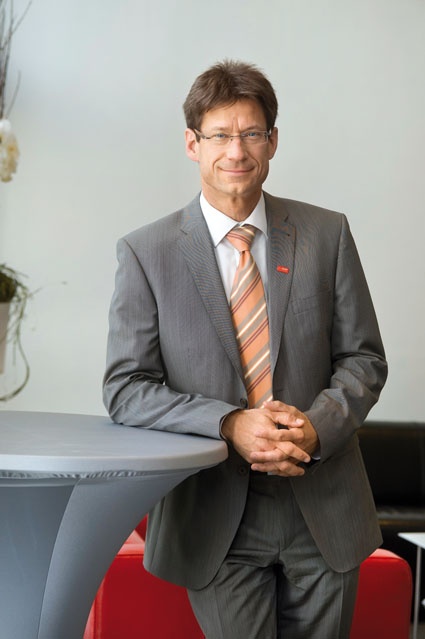
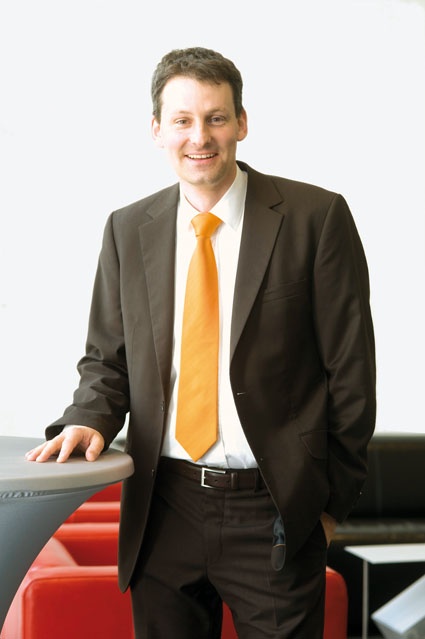
In spite of all the efforts made searching for renewable sources of energy, fossil fuels such as oil and gas will continue to be indispensable in the coming decades. Tapping into offshore sources will play an increasingly significant role. Experts anticipate that the offshore share in the total oil and gas production will triple over the next ten years. Making activities of the offshore industry as safe as possible and being able to utilize such resources in the first place call for the use of reliable high-performance plastics.
Over the past years, BASF Polyurethanes has been expanding its expertise by developing customized polyurethane systems for offshore applications. These polyurethane casting systems consist of two liquid components that react to make up the finished high-performance plastic. The development of these offshore polyurethane systems has been focused on resistance to high temperatures and seawater but also on the use of catalysts that are free of heavy metals. Moreover, the products are extremely tough: They have to be able to withstand high forces while, at the same time, being sufficiently elastic to absorb dynamic loads and impacts.
Protection Against Currents
One application example are vortex-induced vibration (VIV) strakes (Fig. 2), spiral sheaths made of polyurethane (PU) that are affixed to the pipeline rising from the seabed, called riser. The special feature of the strakes, designed and produced by Trelleborg Offshore, is their helical shape, which vertically dissipates the horizontal current forces. Immediately before the pipeline is laid, the strakes are mounted on the riser aboard the pipe-laying vessel, after which the riser is lowered into the sea. While the pipeline is being installed from the ship over the so-called stinger, the enormous weight of the pipeline exposes the strakes to such colossal loads that they are severely deformed. This is why the chemical structure of the polyurethane has to be formulated in such a way that it cannot break. The so-called stinger test making use of a 70-t load has demonstrated that the plastic is robust and its recovery behavior is very good. Under water, the specific shape of the strakes ensures that the pipeline is positioned securely in the water and does not start to vibrate since this could lead to breakage of the pipes.
Mostly, the pipelines are at depths that cannot be reached by the deep-sea divers on their own. Therefore a diving bell has been developed to transport experts to depths of 300 m. The bell was designed as a submersible decompression chamber (Fig. 3). The thermal isolation was performed by Trelleborg Offshore using a so called glass-syntactic polyurethane system from BASF Polyurethanes: The polyurethane is foamed apparently, however true foam would not be able to withstand the hydrostatic pressure underwater and would collapse. This is why the polyurethane matrix is mixed with hollow glass microbeads that are under vacuum, but ensuring that the material can resist the pressure at the same time. These hollow glass microbeads function like miniscule thermos bottles.
Buoyancy Thanks to Polyurethane
New solutions have also been devised for offshore pipelines which are laid over many kilometers and at a depth of over 500 m. Together with the British firm Manuplas BASF Polyurethanes UK has developed a PUR system for subsea buoys and floats (Fig. 4). The moldings are primarily employed as buoyancy and mooring aids for risers in the oil and gas industry. Risers coming from extreme depths are lying on the buoys compensating the weight of the risers and preventing them from the influence of extreme drag forces. The buoys also come into service in case the pipeline needs to be bridged over rocks at the bottom of the sea.
PU Rigid Foam Protects Nord Stream Pipeline
Since April of this year, the crew on the first pipe-laying ship has been working hard on the Baltic Sea, laying the gas lines of the Nord Stream Pipeline Project, which is to run between Vyborg in Russia and Greifswald in Germany. Approximately 200,000 pipes will have to be welded together, and so 200,000 weld seams will have to be sheathed and thus protected against damage. Elastopor H, an open-cell polyurethane rigid foam, has been selected by the Allseas Group to accomplish this mission. The product's strength and processing speed have been refined and optimized.
Over the next two years, the two pipe-laying companies Saipem and the Allseas Group will deploy three ships to lay two pipeline conduits, each 1,220 km long, on the bottom of the Baltic Sea. In April 2010, Saipem's "Castoro Sei" set out to sea with the mission of building a pipeline, carrying aboard polyurethane components. It is anticipated that approximately 2.5 km of pipeline will be laid per day. In August of 2010, the Allseas vessel "Solitaire" has joined the team supplying Elastopor H (Fig. 1).
Quickly and Uniformly Distributed in the Hollow Space
The optimized Elastopor H was developed over the past two years. The polyurethane systems consist of two liquid components that are mixed together and then filled into the hollow space in the sleeve. Subsequently, an exothermal reaction turns the reaction mixture into the actual polyurethane, which is expanded by means of a foaming agent that is also present in the mixture. Due to its good flow properties, the polyurethane system is quickly and uniformly distributed throughout the hollow space. In order to prevent the polyurethane rigid foam from being buoyant, it is configured to be open-celled so that hydrostatic pressure causes it to fill up completely with water. Its dimensional stability is crucial here. The material stands out for its high dry density of 160 kg/m3, which ensures the sophisticated physical properties of this product. After hardening of the PUR system, the weld seam of the pipeline is protected from all sides and can be lowered into the water by the vessel's "stinger". Once the pipeline is finally resting on the seabed, the polyurethane rigid foam can perform its full protective function against mechanical stress. A hammer impact test (performed with a 2 t hammer) demonstrates that even massive blows like collisions with anchors of ships cannot damage the flexible but rigid foam.
Polyurethane Rigid Foam Protects Welded Sites
The steel pipes - PE-coated and sheathed by a layer of steel-reinforced concrete - are welded automatically on the ship during the pipe-laying operation. In the area of the weld seam, however, there is no corrosion protection and, since the concrete sheathing is interrupted at this place, there is no protection against external effects either. Therefore, this sensitive part of the pipeline has to be painstakingly protected. With this in mind, shrink tubing is pulled over the weld site and the interruption of the anti-corrosion layer is thus sealed. A sleeve is put over the concrete sheathing and thus an annular hollow space is formed: This is where the polyurethane components spring into action. The optimized foam is filled into this hollow space.
In 2012, the pipeline is scheduled to be fully operational, accounting for a total capacity of 55 billion m3 of gas per year. It is expected to remain in operation for at least 50 years.