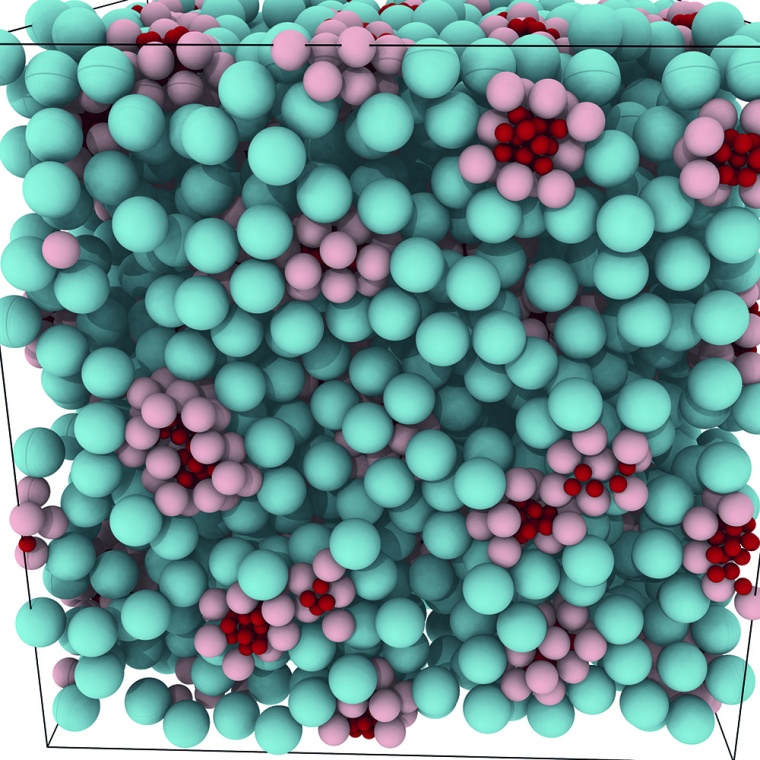
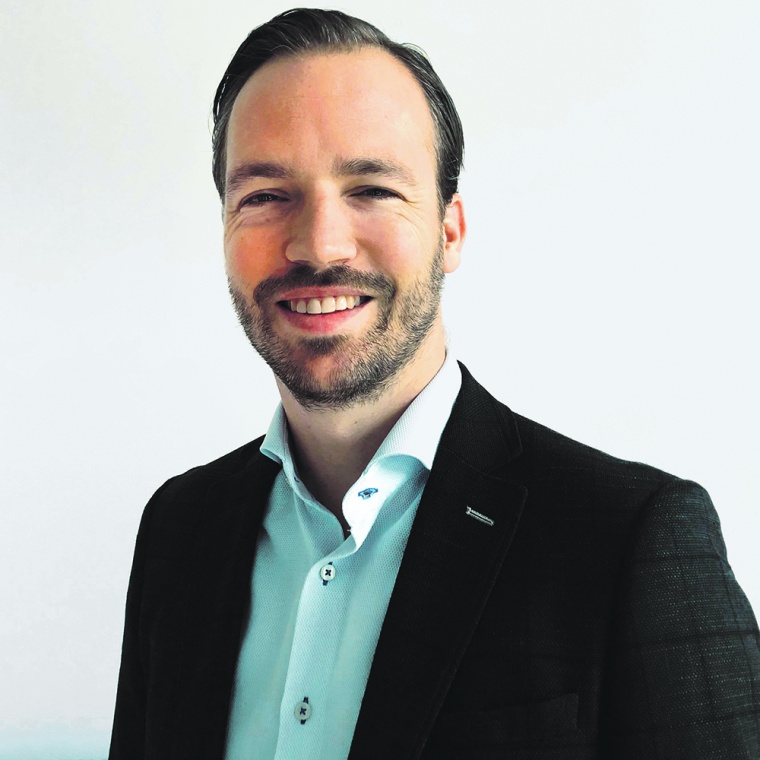
Complex fluids are everywhere. Examples with very specific rheology and transport properties are pharmaceutical components in a mixer, care products, ferrofluids, foodstuff, paint, and slurries. A complex fluid is really any fluid substance that is composed of multiple types of ingredients; for example, liquids, surfactants, solid nano/micro-particles, polymers, solutes/salts. These components come together, due to the laws of physics at the microscale and mesoscale, to form a material with distinctive and sought-after properties. Typical examples of complex fluids that act as a “common denominator” across industries invested in experimental chemistry for their core mission include emulsions, suspensions, (bio-)polymer solutions/melts, gels, pressurized/super-critical fluids (for aerosols/sprays), and liquid crystals.
The critical challenge in formulating a complex fluid is how to determine which ingredients to mix, at which proportions, and under which conditions, in order to create a material with desired properties. Advanced simulations are extremely powerful tools to understand, predict, and improve the rheology and transport of complex fluids and their processing. They provide quantitative insight into the microstructural origins of rheological effects shown by many complex fluids. Existing material formulations can be better understood, and new ones can be prototyped without elaborate synthesis and wet-lab experiments. In product development and prototyping, simulations help to reduce the number of experiments needed to go from initial concept to final product.
Electric Ant Lab (EAL) is a simulation software company founded in 2015 that works at the forefront of predictive fluid modelling. EAL’s scientific mission is to push the boundaries of high-performance simulation, and to create new theoretical frameworks for predicting complex fluid physics. These complicated tools are fashioned into a user-friendly cloud-based simulation platform called RheoCube, geared towards non-expert users in both scientific and industrial contexts. Ralf Kempf asked Jurjen van Rees, the company’s commercial director and one of the two owners, about EAL’s service portfolio and his strategy for the further development of its simulation tools and the expansion of the company’s global activities.
CHEManager: Within five years since its foundation Electric Ant Lab has already established itself as a provider of simulation tools for the process industry. What were the most important milestones in EAL’s development?
Jurjen van Rees: The Dutch start-up ecosystem is very well suited for technical and scientific start-ups. The Dutch government has quite a few excellent programs to help tech start-ups bridge that difficult gap from idea to minimum viable product. This ecosystem is especially active in the Amsterdam area where we are located at the Science Park Amsterdam. This is a vibrant community/campus that hosts a broad range of (bio)tech and software start-ups. It is also a host to a number of Dutch national research institutes and subsequent lab facilities. The University of Amsterdam, where the founder Eric Lorenz came up with the idea for our product RheoCube, is across the street from our office.
Other key milestones were the agreements we made with six early adaptors originating from various industries, but all sharing the common chemical R&D component. Companies like Henkel, Clariant and a well-known manufacturer of flavors and fragrances showed their forward thinking and drive to innovation by supporting Electric Ant Lab so early on in the development of our product RheoCube.
“We basically target every industry
where complex fluids play a role.”
You are developing simulation models for the study of rheology and transport properties of complex fluids. In which industry sectors do such fluids play a role?
J. van Rees: We basically target every industry where complex fluids play a role. The most obvious is the food industry with quite a few very well-known consumer brands. Complex fluids can, for example, be found in the production of ice creams and shelf-life issues in peanut butter. How these foods interact with their packaging over a typical shelf-life time is also crucial to understand. More generally, our target audience is any industry that is developing polymers, coatings, adhesives, paints, specialty chemicals, and all related ingredient suppliers. We even have had successful cases in the oil, gas and fuel-additives markets. As you can imagine, the application is quite broad. So far, we have not been much involved in the pharma, biotech and medical devices industry, but we envision a huge applicability there as well. We already had successes in the prototyping of microfluidic chips with our validated blood-cell model. The downside we experienced in entering the pharmaceutical or medical devices market is the decision-making process on the one hand – long sales cycles are not very pleasant for small companies – and the difficulty to get a conversation started at the right decision making level.
Can you disclose the names of some customers and the projects for which they are using EAL’s expertise?
J. van Rees: Projects are classified of course, but the above-mentioned names of companies who were our early supporters are just a few examples. Our customers are in the European Union and the United States, so taking into account the industries we target the chances are quite high that some of your readers might have stumbled upon us or already our clients. And if they are not, I’d like to invite them to get in touch with me!
“With predictive fluid modelling
the average time spent in the physical labs
can in some cases be decreased by 75%.”
What are the benefits of using a simulation software? How can this tool help companies in the sectors mentioned above?
J. van Rees: There is a two-sided answer to that. If you ask the director or vice president of R&D or even the C-level, the answer is time, cost-savings, faster product-to-market times and a match to their digitalization (of R&D) strategy. If you ask the R&D scientists, formulators and process engineers, it’s the new insights, visualizations, data analyses and validated explanations and to some extent predictions for behavior of their products, ingredients etc.
To put some numbers to the time and cost-saving argument: the average time spent in the physical labs can in some cases be decreased by 75%. Many experiments that take place in an average industrial R&D lab cover a lot of trial-and-error experiments with the goal of explaining and better understanding physical behavior and phenomena, that occur on the single ingredients level or in creating new formulations of products. This is exactly the scale where our simulations add value.
Take a small R&D team of, let’s say, five staff scientists with a total cost of around €125,000-150,000 per year and person, and they can reduce more than half of their time spent preparing samples, setting up experiments and analyzing the results. Time they can spend running more experiments in the same time and creating more validated and accurate data while they’re doing that. This is not so much a cost-saving aspect as it is an improvement of output of that R&D group. The product in which they invest so much groundbreaking science could reach the market faster. A formulator may find better matching ingredients for the goal of their material. Process engineers can solve major issues that are stalling production, and which can be solved in a matter of days instead of weeks, weeks instead of months.
How detailed can the simulations be? Are interactions at the molecular level also covered?
J. van Rees: We aim to capture all of the molecular and physical interactions that occur within the “micro” to “meso” scales.
The microscale is where atoms and molecules live, roughly on the nanometer length scale, and the pico- to nanosecond timescale. Presently, our simulations begin at the scale of hundreds to thousands of molecules, where reality can be well captured with statistical thermodynamics and molecular dynamics. This is just above the level where explicit quantum mechanical detail would need to be considered.
From there, our simulations go up to the mesoscale, which sits on the microsecond and micrometer time and length scales. Here, our simulations represent a complex fluid as many interacting “blobs” of liquid and/or solid, each containing around 1 million molecules. This is the scale where quantitative predictions can be made about the rheological behavior of the mixture.
The beauty of this is of course that you can turn on or off certain physics. For example, some behaviors of complex fluids can be better explained or understood under zero-gravity circumstances. We can switch that off. Or let’s say you are studying the effect of an external field, for example a magnetic field. We have worked on a successful case of a magneto-rheological fluid and applying an external magnetic force field to that fluid. The ability to conditions in the simulation at will has broad applicability; for example, in the automotive industry, one could simulate the fluid in a car’s suspensions, where a sudden viscosity change can have a huge effect on your car going for a smooth ride on the Autobahn. We can basically manipulate any physical behavior known to nature within the time and length scales above. The only boundaries to this are in our own development time needed to construct these physical models, and more importantly for our clients: the computational time to run such a simulation.
“Our goal is to provide
the greatest predictive power
with the least required input of data.”
The creation of accurate simulation models that reliably represent a product requires detailed input on both physical as well as chemical characteristics. Where does the required data come from?
J. van Rees: Our goal is to provide the greatest predictive power with the least required input of data. Nevertheless, our clients usually have a wealth of information about their products and the components in their products. This data is typically readily available in datasheets, or as experimental data that they have already collected. This data is than added by the user to RheoCube when they create new components like polymers, surfactants or particles. We then help our clients assess the scientific performance of RheoCube for their goals, typically by doing validation simulations on related mixtures found in scientific literature. This helps us to build confidence – for our clients and also for ourselves – that RheoCube is a viable tool for scientific work in the particular goal at hand.
In some cases, our clients do not have all the necessary data available. For example, one of the ways that we input the molecular-scale interactions between ingredients in RheoCube is via the “Hansen solubility parameters”. These are like three “name tags”, determined by simple experiments, that describe the essential chemical interactions the ingredient has with other ingredients. To help clients in determining these parameters, we work closely together with Van Loon Chemical Innovations (VLCI) which is also conveniently located at the Science Park Amsterdam. If we send them a few examples, we can feed the collected data into RheoCube for our clients. If we need very specific measurements like particle characterization and particle size distributions, we have quite easy access to the world-class lab facilities surrounding us.
Where do the simulation calculations take place? Does EAL provide the necessary hardware or only the software?
J. van Rees: Detailed simulations do require a lot of computational power – there is no way around that. We realize that this is often a significant hurdle for clients to adopt simulation as a tool. Therefore, we designed RheoCube from the very beginning to integrate with cloud-computing servers from well-known vendors. The simulation code running inside RheoCube makes use of the latest parallelization strategies on multi-core CPUs, as well as GPU parallelization. Our platform also provides estimates on the computing time and costs for simulations.
To add credit to the ground-breaking work of our tech and science team that is led by our founder Eric Lorenz, the capability of running these simulations on cloud-computing infrastructure is really unique to our software. R&D scientists that use RheoCube do not need another PhD in computational physics to use this simulation approach. So, in answer to your question, yes we provide the hardware and the software. Without any local installation. You just need a web-browser. This is what really makes this approach so powerful: RheoCube was designed with and for experimental scientists.
Topics like innovation, sustainability, resource efficiency, and digitalization are driving the chemical industry and related sectors. How are these “megatrends” affecting your business?
J. van Rees: I’d say that we are very early riders of these trend waves. Especially digitalization, if you look at the wet-lab set-ups that often have so many aged analogue processes (including time-consuming trial-and-error work). Why spend weeks waiting for a sample to be stable enough before you can run a viscosity measurement when you can run 10 of these measurements at the same time, with just a few clicks, to get a faster and more informed answer?
Digitization (of R&D) is the most important “megatrend” that is affecting our business. We are mostly successful with contracting companies that have digitalization of R&D as part of their corporate or innovation strategy. For most companies we talk to, innovation is such a part of their DNA that without it, they would not be talking to a tech start-up from Amsterdam in the first place.
How willing is the chemical industry and related sectors to use innovative technologies like simulation tools?
J. van Rees: Very willing, as long as they are open to innovate or have digitization for R&D embedded in their corporate strategy. Of course, it’s also a mindset. A mindset where one is open to new ideas from outside, or new technological developments around computing and using simulation models that are now becoming available outside of academia. Unfortunately, that mindset is not always present, I have to acknowledge, with the exception of a minority of R&D scientists or leadership. However, some industries are more open to these types of new technologies than others. For example, the personal/home care and food industries are far more open to external innovation and collaboration than for example the pharmaceutical industry.
With the current health crisis around Covid-19 that is impacting the entire globe, we found that our tool was suddenly in high demand. With labs being closed or partly accessible, R&D scientists that heard about us came to the realization, that they could move some of their lab work to their home office using a laptop.
That being said, simulation tools on the somewhat larger scale, commonly known as computational fluid dynamics (CFD), are a fairly established market that has been around for decades. These simulations handle length-scales of centimeters and higher, and timescales of seconds and beyond. Especially in the processing environment, this is a broadly used approach. What we usually hear in these surroundings, talking to these scientists or engineers, is roughly translated to: “if CFD can’t do the trick, our multi-scale approach will certainly do it”.
What is your strategy to further develop EAL’s expertise and geographical reach? Are there any specific projects in the pipeline?
J. van Rees: We have yet to contract our first Dutch client, hahaha. But that is mostly a matter of time and will happen eventually. All joking aside, we are currently looking into external financial resources – that is venture capital –in order to focus more on the DACH region, the United States and Canada. Most of our clients are already in these geographical areas, but this really needs more of a local physical presence in order to serve our clients best. Most importantly, at this point in time, we want to expand our client base in these areas in the coming years. You can do a lot of growth-hacking over video-calls, but in the end, you need to see the scientists behind a company like EAL. And vice versa as well. We invest into long-lasting relationships with our clients as they are quite progressive in embedding our solution into their R&D workflow.
We definitely have a few ground-breaking projects up our sleeves, but these will be released and presented in due time.
Our main goal is indeed to expand our user base and to achieve our main goal: unlock the power – and all these years of research and development from our talented team and founder – of complex fluids simulations for scientists across the globe.