Materials Know-How
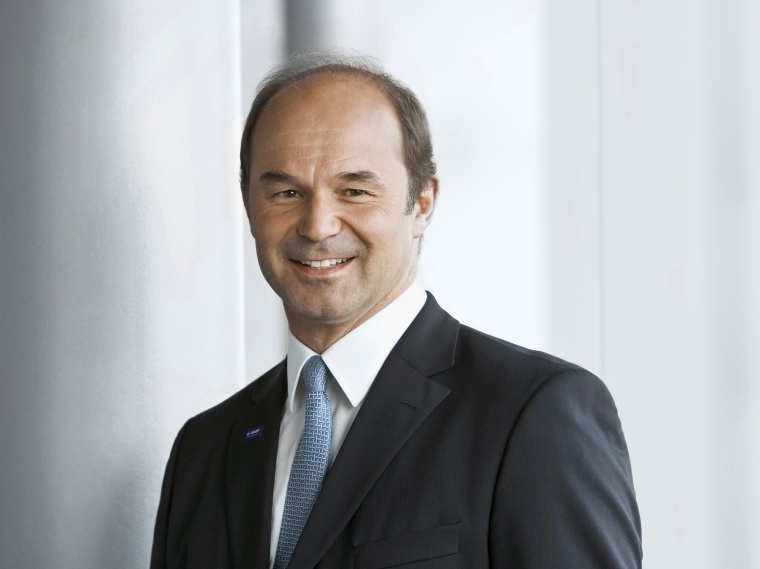
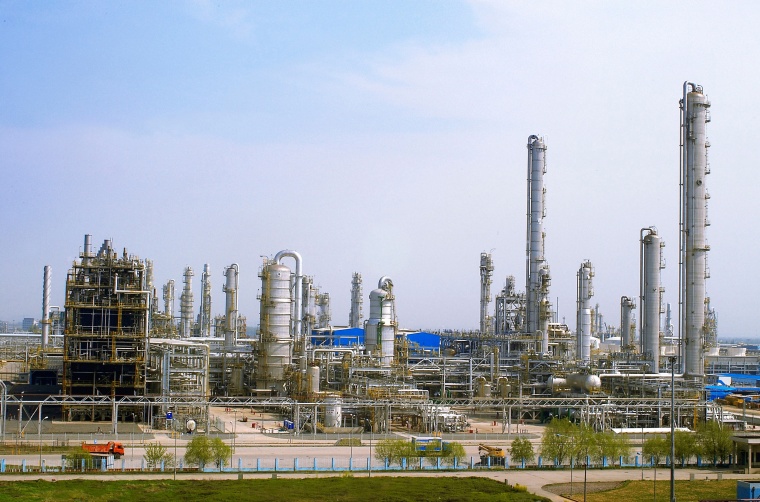
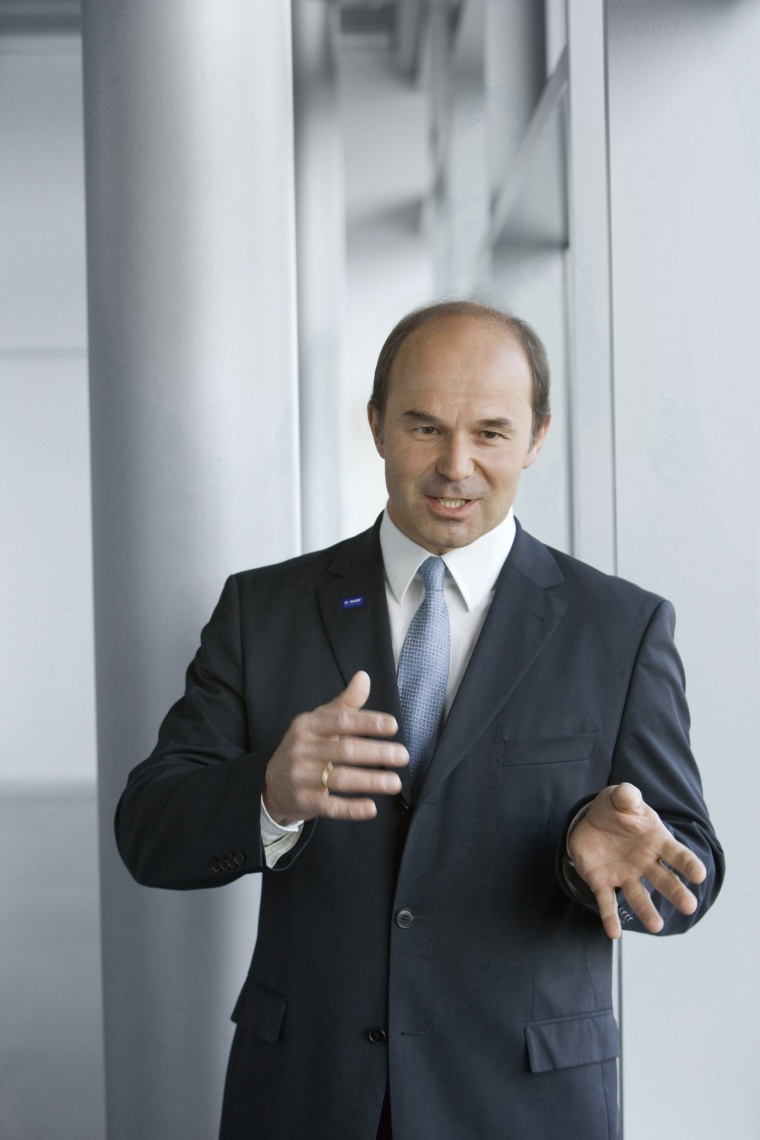
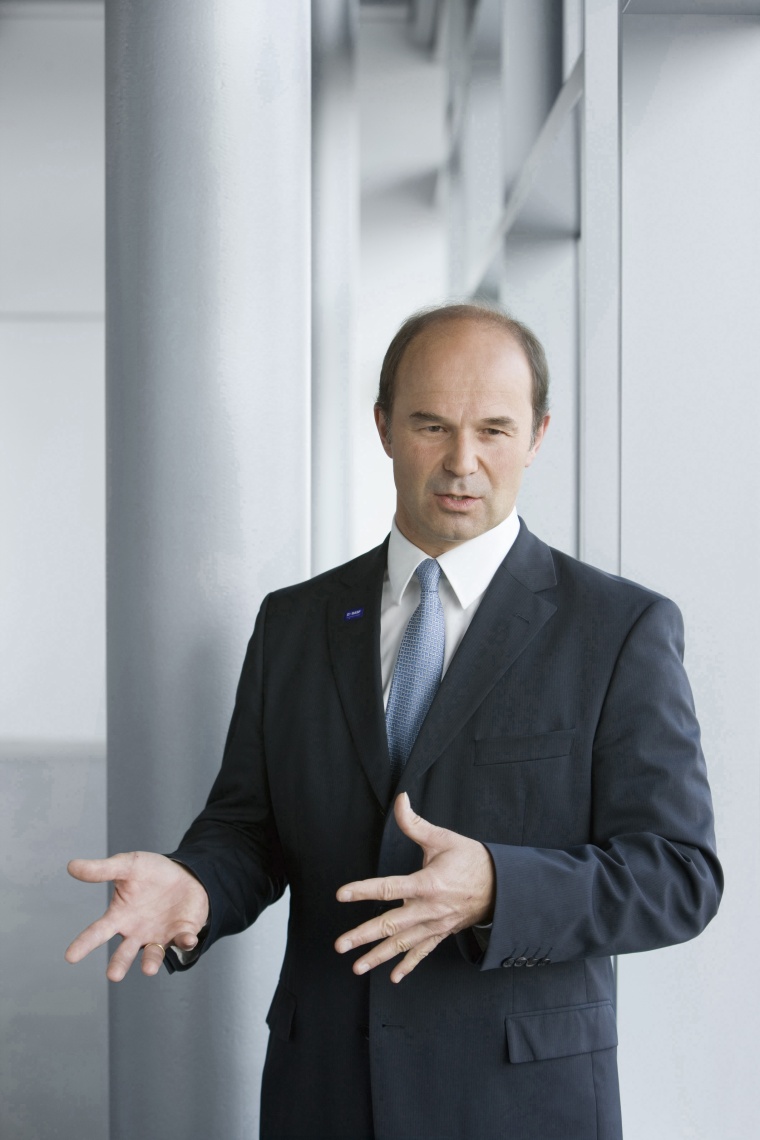
Tangible Synergies - In an organizational move in January of 2013, BASF created the new Performance Materials division. The new group, which is part of the Functional Materials & Solutions segment, includes BASF's engineering plastics, polyurethanes, thermosetting epoxy resins, functional foams, biopolymers, and styrene-based foam products. Reporting sales of €6.5 billion in 2013, the division is active in a huge number of industry sectors. Dr. Martin Brudermüller, Vice Chairman of the Board of Executive Directors of BASF, is responsible for the Performance Materials division. He is also in charge of the Region Asia Pacific headquartered in Hong Kong. Dr. Michael Reubold caught up with him on his growth plans and expansion strategy.
CHEManager International: Dr. Brudermüller, by bundling all specialty polymers in the newly created Performance Materials division, BASF aims to support future growth in the market with its downstream plastics. How will this organizational move help to achieve this goal?
M. Brudermüller: Our Performance Materials division combines materials know-how and the innovative, customized plastics from BASF in one entity which is active in key industry sectors, such as transportation, construction, industrial applications and consumer goods. In keeping with differentiation on the basis of business model and customer requirements, units with a customer and industry sector focus are now separated more clearly from units that focus on chemistry and production.
With their variety of products and their understanding of application-oriented system solutions, BASF material experts can make a significant contribution here. Key drivers of profitability and growth are close collaboration with our customers, the portfolio shift towards solutions and specialties, a constant flow of innovative products and applications and large innovation and R&D capabilities.
With the creation of the Performance Materials division the Polyurethanes business moves into one organization with the other plastics activities. Will you look to leverage synergies between these formerly divided business groups?
M. Brudermüller: Take for example our insulation materials for the construction sector. EPS insulation foams like Neopor and Styrodur are now merged with numerous polyurethane insulation foams from the Elastopor, Elastopir and Elastospray product range. From this huge portfolio, BASF construction experts can recommend the best individual solution. For the automotive field, too, all materials are now under one roof. All relevant lightweight technologies are now also close to each other and will lead to tangible synergies for our customers. The next big step toward replacing metal is continuous-fiber reinforcement of injection-molded structures, based for example on thermoplastic composites. Composites offer an additional weight reduction of up to 60% per part compared to steel. If developing well, this market will have a size of roughly €2 billion in 2030.
BASF is strengthening its specialty polymer business with a number of investments. These include capacity expansions as well as acquisitions. What is currently going on in terms of strategic investments?
M. Brudermüller: Our goal is to continue to grow while remaining profitable, to serve the established markets even better, to participate in attractive growth markets and to develop new business activities. Key investments in specialty polymers include in Korea a new plant for Ultrason, which is widely applied in the electronics, automotive and aerospace industries for the production of heat-resistant, lightweight components. Also in Korea we are constructing a new compounding plant for engineering plastics Ultramid and Ultradur compounds. With our new integrated hub for polyurethane manufacturing in Dahej, India, we aim to ensure local supply for growing markets such as appliances, footwear, automotive and construction.
In terms of geographies, where will the bulk of these investments flow to in the future? Do you see the U.S. regaining attractiveness again due to the shale-gas boom?
M. Brudermüller: The shale gas revolution in the U.S. is attracting investments by chemical companies, because a significant proportion of chemicals are natural gas-based. This is a fundamental change for a significant time period and therefore relevant for long-term investments. The gas price will continue to be substantially lower than in Germany where the gas price is currently at least double. And the energy price difference is even 1:3. As one of the largest chemical companies operating in the U.S. BASF benefits from this significant cost advantage. At our Geismar site in Louisiana we are constructing a world scale plant for the production of formic acid. And we are considering to build a world-scale ammonia plant with Yara at the U.S. gulf coast. In the coming five years, we will invest additional €3 billion in the U.S.
As you just said, BASF is investing not only in its specialty business but also in basic products required for the specialty polymers business. What are the crucial advantages of this backward integration?
M. Brudermüller: In our Performance Materials business we benefit from our high operational and technological expertise in the production of commodities and basic products. Due to backward integration in our plastics production processes, we offer a high degree of security in terms of availability and quality of our specialties. Production at our Verbund sites is highly cost-effective. For that reason, we target investment in the basic products that are so important to our specialty business such as a new world-scale TDI plant in Ludwigshafen, which is due to start operations at the beginning of 2015.
You are responsible for the Asia Pacific region, the most vibrantly growing market in the world. What is BASF's strategy to participate in this growth?
M. Brudermüller: Asia will continue to dominate global growth. We expect that the contribution to world chemicals output in the emerging countries in Asia will have a share of 60% of global production within less than ten years. This means for us a need to build up production in Asia. Our goal is to locally produce approximately 75% of all BASF products we sell in Asia Pacific by 2020. Local production allows us to be closer to our customers, enabling us to address their requirements much more flexibly and improving our supply capabilities.
Together with our partners, we will invest €10 billion in Asia Pacific. This includes large-scale plants for more upstream products in China such as the new MDI plant in Chongqing, plants for acrylic acid, butyl acrylate and super absorbent polymer at our Verbund site in Nanjing, and a world-scale isononanol plant in Maoming.
In downstream products we are also planning to invest more than €360 million in Malaysia together with our partner Petronas to build an integrated aroma ingredients complex.
To serve our local customers with excellent research and development we recently opened our first Innovation Campus Asia Pacific in Shanghai. It is our largest R&D site outside of Germany.
GDP growth in Asian countries has been losing dynamic recently. Did you have to adjust your long-term strategy to this situation or do you believe it is only a rest period before picking up pace again?
M. Brudermüller: Our strategy is for the long term. In particular, BASF believes local innovation and production are important drivers to business growth, and this is reflected in our strategy - innovations from Asia, for Asia, but increasingly also for the world. BASF develops new applications, products and solutions together with our customers in Asia, adapted for Asian needs. Based on our strong global R&D network, we will considerably strengthen our innovation capabilities in Asia Pacific, enabling us to better serve our customers in this region. In particular, this includes electronic materials, agriculture, catalysis, mining, water treatment, polymers and minerals.
BASF will invest in a range of efficiency measures that will save approximately €1 billion annually by 2020. Excellence in functional units, marketing and sales, organization structures, investment processes and operations are the focus areas addressed to establish a competitive advantage for BASF in the region.
BASF's spending on research and development hit another record high of €1.8 billion in 2013. What can we expect to come out of your R&D group in the short and middle term?
M. Brudermüller: We have bundled our polymer and additives research in one technology platform and developed it further into the division Advanced Materials & Systems Research. Advanced materials form the basis for developing multi-material systems such as those we are developing for the growing wind energy market and other areas. We have now established interdisciplinary research groups which specialize in working on lightweight composites from reactive resins and carbon fibers or, to give another example, novel membrane materials with nanopores to filter drinking water.
The holistic systems-based approach in R&D will involve developing tailored solutions in close collaboration with our customers. Cooperation with research institutions and universities is another very important element. Recently, we inaugurated the research initiative "North American Center for Research on Advanced Materials." We succeeded in bringing together researchers from Harvard University, the Massachusetts Institute of Technology and the University of Massachusetts Amherst in this initiative. Research activities include microstructures and nanostructured polymers with new properties. The next step will be to investigate lightweight materials for wind turbines and automobiles, and engineering materials for the construction and energy industries.
The increasing use of biopolymers presents another growth market. BASF plans to expand its business in this area. How do you want to do this?
M. Brudermüller: Resource conservation and climate protection are important drivers of the increased use of renewable resources. We are currently stepping up research into a biodegradable and primarily biobased foam with properties similar to those of EPS for use as packaging for food and electric and electronic goods, an area that is seeing a surge in demand for biobased and biodegradable solutions. However, both supplier and converter have to accept that a product property like 'biobased' incurs additional costs due to the different raw material base and the rather new biorefinery technology.
An innovative product with diverse applications is Ecovio, which contains a high proportion of polylactic acid derived from corn starch. Despite a high renewable raw material content of about 50%, Ecovio is sufficiently stable for numerous applications, including the manufacture of tear-resistant bags, mulch films, coated paper, dishes and cups or coffee capsules.
To respond more effectively in future to customer interest in biobased materials, BASF has developed an innovative mass balance approach. Can you explain what led you to the development of this approach and what results you expect from it?
M. Brudermüller: We want to respond more effectively to our customers' increasing interest in materials based on renewable feedstocks. In cooperation with TÜV Süd we have developed an innovative mass balance approach for the use of renewable feedstocks in the integrated production. The process is available immediately for many products and can be adapted to customers' requirements. Based on this approach, biomass is used as a feedstock in the manufacturing of basic products in existing plants. This biomass share is then allocated to sales products according to their recipes using the new certified methodology. The quality of the products remains unchanged.
The products mass balanced in this manner save fossil raw materials and reduce greenhouse gas emissions, thereby contributing to sustainable development. Existing plants and technologies along the value chain can continue to be used, and the customers' product formulations do not have to be adjusted.
Thus, bio-naphtha and biogas, for example derived from organic waste, are used for the mass balance approach. Our Dispersions & Pigments division has supplied a large adhesives customer with initial amounts of mass-balanced products, dispersions for construction adhesives. TÜV Süd has meanwhile issued certificates for 14 products. These include superabsorbents for diapers, performance polymers for electronic goods and further intermediates.