Connected Work
We are in an increasingly volatile global climate, from health and economic crises, to trade wars on multiple fronts, to political unease, to name just a few.
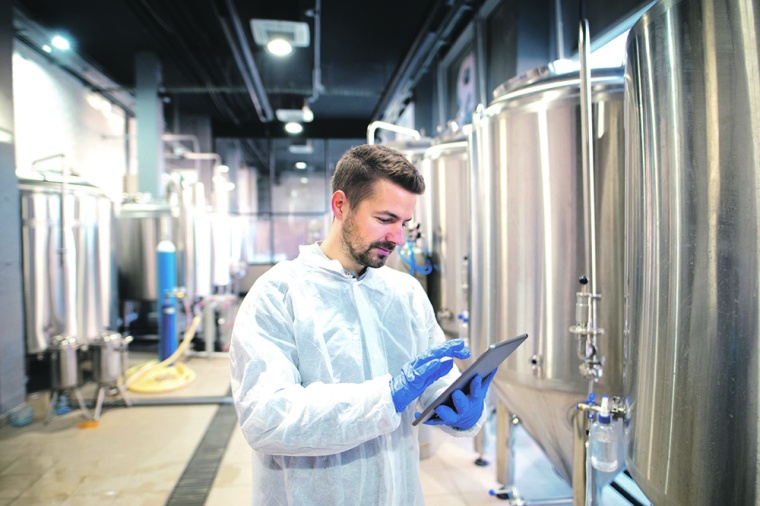
During periods like these, it makes sense that corporations generally shift toward a more conservative stance, taking a “wait-and-see” approach to business decisions. However, instability can provide exceptional opportunities for companies to innovate and accelerate ahead of more conservative competitors. In manufacturing, the Fourth Industrial Revolution is fully upon us. Yet, only about half of manufacturing companies are in the early stages of smart factory transformation, and 20% “have a desire to adopt” digital, but are experiencing blockers. The number of companies just watching rather than acting needs to decrease and those that are already in the midst of digital transformation should consider leveraging this moment to accelerate their journeys. Ralf Kempf asked Lawrence Whittle, CEO of software company Parsable and member of the World Economic Forum, about current challenges of the process industry and why manufacturing leaders must get started on implementing their digital strategies now.
CHEManager: Mr. Whittle, the chemical industry is an essential materials provider for many industries. How is the industry doing in and dealing with the Covid-19 pandemic?
Lawrence Whittle: Chemical companies and the process industry at large are starting to determine how to best adapt to these new realities. Unlike many other industries, however, there is a universal reliance on them to produce so many of the day-to-day items we all need, like health and medical supplies, cleaning products and other consumer packaged goods. Any company making these products is seeing strong demand, and will continue to see that through the pandemic. The biggest challenge for them is related to how their workforce operations respond efficiently and safely to these changing demand patterns.
What, in your opinion, are the greatest challenges for the process industry in the coming months or in the coming year?
L. Whittle: The pandemic will still dominate business decisions for several months ahead, and one of the biggest challenges remains worker safety on the processing plant floor. It‘s critical that organizations put increased emphasis on safety measures to not only better support their frontline workers, but also to strengthen their business. Secondly, these companies have to arm their workers with a more agile approach to work execution.
How will the process industry master these challenges? Or will they not be able to do so at all?
L. Whittle: Connected worker technology is an essential solution to overcoming the safety and operational challenges, ensuring that workers are adhering to safety policies and executing work in the correct sequence so that productivity and quality levels remain as high as possible. Leveraging new mobile technology helps people better execute work through a digital approach — it digitizes work instructions and makes them accessible through mobile devices.
Plant managers can make changes to digital standard operating procedures (SOPs) at any time and make them accessible through mobile devices so that the most up-to-date safety policies and steps are integrated into the work itself. For example, SOPs can include safety guidelines, sending push alerts to workers to remind them to wash their hands before handling equipment, wear masks, and more.
Connected worker technology can also help with social distancing and remote collaboration. It can capture worker data and progress in its system so it knows exactly where certain processes were left with one person and where the next person needs to pick it up. This means a lesser need for close human interaction.
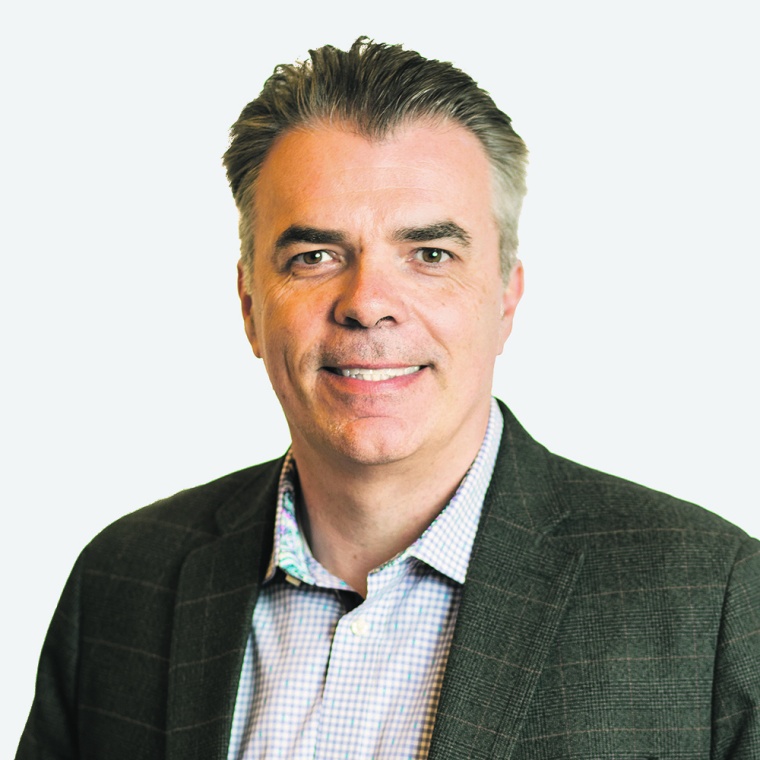
“Connected worker technology is an essential solution to overcoming the safety and operational challenges.”
Which developments and trends, apart from the challenges mentioned, are currently influencing the process industry? Does the corona crisis accelerate these trends?
L. Whittle: Totally independent of the Covid-19 pandemic, there is huge concern — and opportunity — around two large factors. Firstly, sustainable operations, and secondly managing the changing workforce due to a large amount of late career workers retiring from the process industry.
There is more attention now than ever on the excess waste from the beginning to the end of the manufacturing process, as well as the environmental concerns and preservation of resources in manufacturing. The public is demanding more transparency, as are employees and workers themselves. The production efficiencies enabled through technology, and its ability to document gains made or waste averted, will be key to that transparency.
Additionally, the retiring workforce was an issue before the pandemic but now ever-increasing numbers are leaving the workforce with tacit knowledge. Hiring early career people with 10-centimeter binders for onboarding just will not work.
A major problem for the industry could arise from the shortage of skilled workers and young talents. How could this influence the long-term development of the industry?
L. Whittle: To expand on this subject, process companies need to rapidly rethink how they hire, retain and train at a far greater velocity than ever before. Modern digital tools will be a recruiting competitive weapon in the near term and a ‘must have’ in the medium term. Just as baby boomers drove change in the workplace as they began to fill management and executive roles, so, too, will millennials and young talent have an impact on the technology systems and solutions deployed in factories and on shop floors everywhere.
“Modern digital tools will be a recruiting competitive weapon in the near term and a ‘must have’ in the
medium term.”
What role does the World Economic Forum play in tackling the challenges for the process industry mentioned above?
L. Whittle: I‘m a member of the World Economic Forum‘s Platform for Advanced Manufacturing and Production, and we are absolutely addressing these challenges on multiple fronts. We have an active community of over 130 organizations from more than 22 industry sectors to accelerate technology while stimulating innovation, sustainability and employment. A new WEF group that my company, Parsable, is leading, called New Generation Manufacturing Leaders, is putting forth initiatives both internally at their organizations and externally to make manufacturing more sustainable, resilient and inclusive.
How can a platform for connected work support companies in the process industry? What insights can be gained from such a platform — and where are the limits?
L. Whittle: Simply put, connected worker platforms help employees on the shop floor get their job done right the first time and every time. In doing this, they help to uncover data on the human work in your operations, so you can drive continuous improvement. Companies can start to capture the data that‘s not currently captured by any systems, in real time. As you capture that data, it can be used for things like autonomous maintenance — making sure that machines don‘t break down. The systems can inform you when you need to make a change, or you can start to see benchmarking on how long it‘s taking to do a particular task or how many errors you‘re getting around a deviation. The fact that the data is now available in real time means that you can update dynamically that working structure, and then the next time someone executes that work, you‘ve got a brand-new updated version.
The lack of modern digital tools for frontline workers has been a key topic for industrial companies. It‘s now clear that anyone still contemplating operating with paper-based work processes is running both a big risk and missing a big opportunity.