Chemical Labor Productivity Challenge
The chemical industry faces acute labor shortages because the talent pool is shrinking, but the industry remains heavily reliant on manual work. Therefore, realizing labor productivity potential will be decisive for business continuity and future growth.
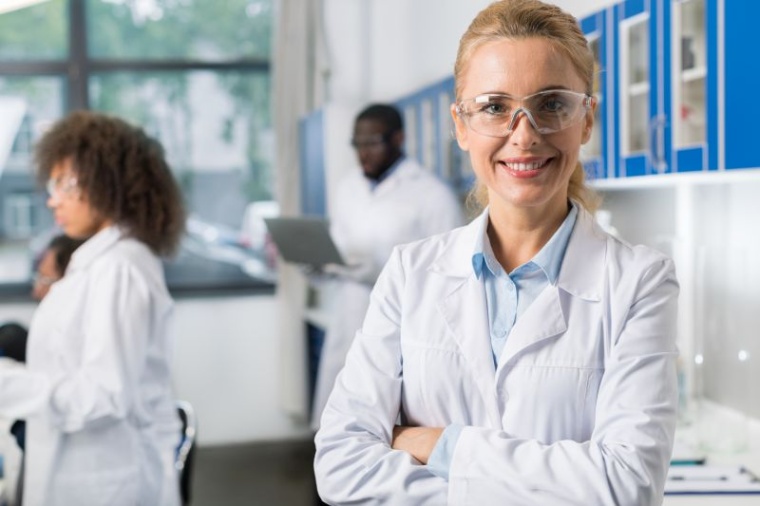
A labor productivity crisis is looming, with Europe at its epicenter. For 15 years, European chemical companies have invested up to 7% of their annual revenues in new plants, equipment and technologies — yet labor productivity has plateaued. Productivity will become an even bigger challenge as demand increases and a retirement wave coincides with flat student enrollment in key fields. Companies can act now to crack the labor productivity conundrum.
The chemical industry faces acute labor shortages because the talent pool is shrinking, but the industry remains heavily reliant on manual work. The underlying issue is that labor productivity (calculated as revenue per full-time equivalent or FTE) is stagnant, according to a recent report published by Accenture. Globally, revenue per FTE has improved by less than 1% per year during the last 15 years. In Europe, labor productivity growth per year has been a bit higher (1.6%), but still lower than the 2.4% average annual inflation rate (fig. 1).
If this trend continues, chemical companies will lack the talent needed for growth. With demand for sustainability-related products predicted to soar by about 70% by 2028, this opportunity is too big to miss.
“Technology alone does not automatically
lead to greater labor productivity.”
Large Investments, Small Improvements
So far, organizations’ efforts to boost productivity haven’t had the desired effect. During the last 15 years, European companies have invested up to 7% of their annual revenues in new plants, better equipment, digital technologies and continuous improvement. However, productivity has remained disappointingly low.
In contrast, at a global level, several other asset-intensive industries have achieved up to six times greater improvements in labor productivity in that same period (fig. 2).
Demographic Shifts Create a Perfect Storm
Labor productivity is set to become an even bigger challenge, especially in Europe, as two pressing issues converge.
One is a looming retirement wave, as 31% of employees at European chemical companies are aged 50 or older and due to retire within the next decade. The problem is particularly acute in Germany, where 38% of the overall workforce is aged 50 or older.
The second issue is that student enrollment in key disciplines such as engineering and IT has plateaued, while demand for these skills continues to rise. This mismatch will create greater competition for a shrinking talent pool.
Technology Isn’t a Silver Bullet
Other asset-intensive industries have demonstrated that capital expenditures can be converted into up to six times greater labor productivity, so what do chemical companies need to do differently to achieve the same or even better results?
The reality is, even though European chemical companies have invested up to 7% of their annual revenues in new technologies and equipment, approaches to labor have remained largely unchanged. Consequently, new plants operate like older ones, with minimal improvements in automation and efficiency.
The key lesson is that technology alone does not automatically lead to greater labor productivity. In parallel, companies need to adjust work processes, methods, roles, recruitment and training strategies to adapt to technology advancements.
How to Crack the Labor Productivity Conundrum
The good news is that chemical companies already have the technology they need to increase labor productivity and address talent challenges. They can make substantial productivity improvements by reinventing roles and reshaping the workforce across three dimensions:
1. Restructuring work to increase labor productivity
When chemical companies build new facilities, they often replicate existing plant designs and organization charts. And when they invest in digital programs, they typically do not reinvent or restructure roles. Without adjusting work processes, methods and roles, new technologies spark only small, incremental improvements, and companies miss out on larger productivity gains.
As an example, imagine that a company has invested in a technology that can automate 20% of a role. If the work isn’t reorganized, the people in the role will do something else with the time gained. But if the company combines roles, it can free one FTE position for every five workers. And that really adds up. If companies can save a few hours for each person across several thousands of roles, they will achieve considerable savings and reduce the need to replace employees as they retire, easing pressure on recruitment.
2. (Re-)Building the expertise to continuously reorganize work
Executives can’t approach reinvention as a contained effort undertaken every few years. Change is constant, so reinvention never ends. Executives need to build the capability to continuously adapt and reinvent as technology advances and creates new possibilities. This includes putting in place people with the capabilities to reorganize work on a role-by-role level, build new teams and unlock labor productivity potential. Implemented successfully, these kinds of changes can convert time savings from automation into reductions in the number of FTEs required to run each plant or function.
“Companies must not underestimate
the magnitude of change required.”
3. Investing in dedicated training and knowledge capture and transfer
Chemical companies need detailed plans focused on: identifying required skills and building them via training; capturing knowledge from retiring employees; and conveying that knowledge to new employees or those taking on new roles. Ultimately, the aim is to shift away from transactional, manual labor toward work focused on analysis, design and execution.
Companies must not underestimate the magnitude of change required. Since labor productivity opportunities affect all business divisions, functions and roles, almost every employee will require some level of training or skilling. To address this need, companies must dramatically expand training programs and transfer knowledge from employees nearing retirement.
A Critical Turning Point
The rapid pace of technological advancements presents a new world of possibilities, but many companies struggle to effectively implement these changes. As chemical companies explore future advancements in technologies — including automation, AI and now generative AI — they must continue to reshape roles, skills and organizational structures to fully benefit from them.
The bottom line is that realizing labor productivity potential will be decisive for business continuity and future growth. It’s time for chemical companies to seriously address labor productivity, tackling it from the board-level down. By doing so, they will be well-positioned to address talent challenges and drive growth in the transition to a low-carbon economy.
Bernd Elser, Senior Managing
Director, Global Chemicals & Natural Resources Lead, Accenture,
Frankfurt am Main, Germany
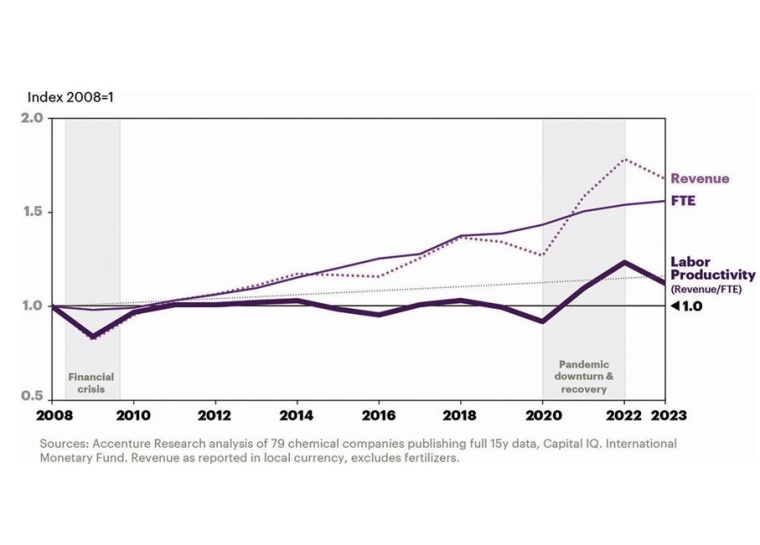
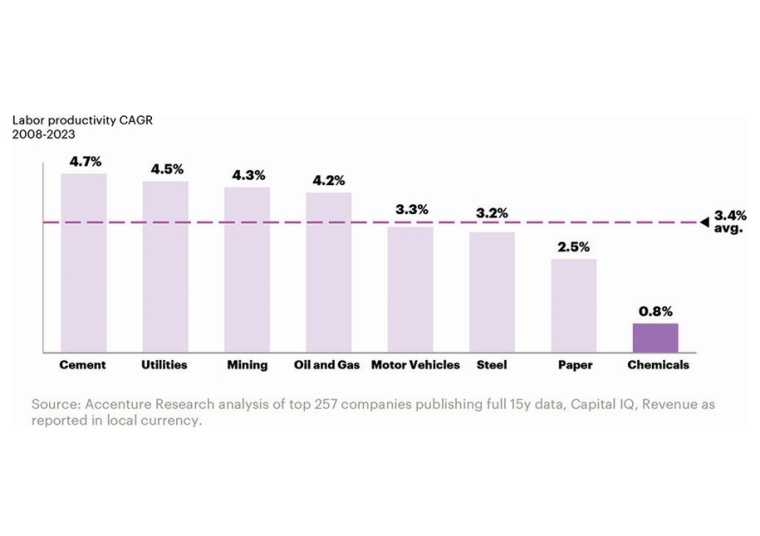