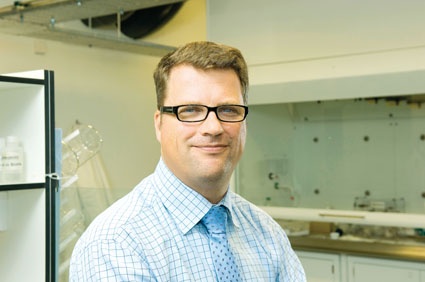

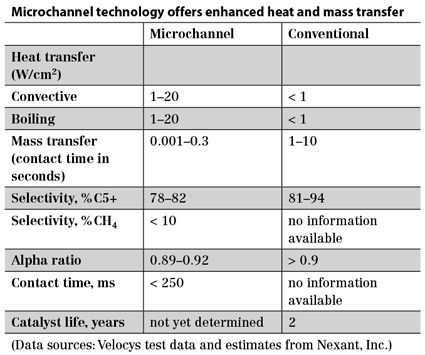
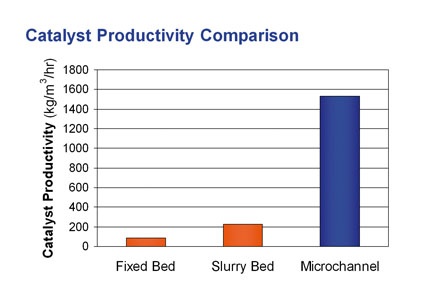
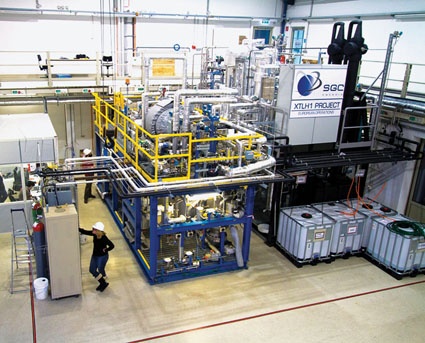
Challenge - The management of waste, including agricultural, forestry and municipal waste is a world-wide challenge. So is the growing need for renewable energy supplies. The use of microchannel reactors to enable the distributed production of biofuels from biomass waste via the biomass to liquids process (BTL) offers one option for solving both problems at once. Derek Atkinson of the Oxford Catalysts Group explains how.
Back in the early 1990s when scientists and engineers at Pacific Northwest National Laboratory (PNNL) in Richland, Washington, U.S., were considering ways to process nuclear waste leftover from the Manhattan Project (1939-1946) and stored in underground tanks sites scattered around Washington state, they came up with a big new concept for tackling the problem: distributed small-scale processing using microchannel reactors. The aim was to develop a way to process the waste in situ rather than transporting it to a large centralized facility. Velocys, Inc., now part of the Oxford Catalysts Group, was set up in 2001 in Plain City, Ohio, to further the development of microchannel reactor technology.
Although the idea of developing microchannel reactors to use for the distributed processing of nuclear waste didn't take off, the concept of using small-scale distributed processing concept using microchannel reactors has. The Oxford Catalysts Group have gone on to develop microchannel reactors for two applications, small-scale gas to liquids (GTL) plants for capturing associated and stranded gas both offshore and onshore, and small-scale biomass to liquids (BTL) plants for the distributed production of biofuels from feedstocks such as municipal, forestry and agricultural waste.
The Fischer-Tropsch (FT) process, in which synthesis gas (syngas), a mixture of carbon monoxide (CO) and hydrogen (H2) is converted into various liquid hydrocarbons using a catalyst at elevated temperatures, plays a key role in both. Because they don't contain aromatics or sulfur-containing contaminants, the liquid fuels produced via FT are typically of higher quality and burn cleaner than petroleum-based diesel and jet fuels, resulting in lower emissions of NOx and harmful particulates. Distributed production systems, which make it possible to produce biofuels in small plants located near the source of the feedstocks and potential markets for the fuel, also reduce carbon emissions by avoiding the need to transport large volumes of waste to central processing facilities.
After winning a number of important awards, including the 2009 ICIS Innovation awards, the 2009 Energy Institute Awards, the CleanEquity Monaco 2010 commercialization award, and the CWC World XTL award 2010 and been shortlisted for others, the technology is now being put to test in the real world.
The first practical demonstration of the use of FT microchannel reactors for BTL - jointly operated by the Oxford Catalysts Group and the Portuguese incorporated company SGC Energia (SGCE) - for the small scale distributed production of biofuels is now mechanically complete and undergoing start up at the biomass gasification facility in the pioneering eco-town, Güssing, Austria. The plant, which will use gasified woodchips from the existing Güssing gasifier, includes an FT microchannel reactor developed by Velocys, combined with a new highly active catalyst developed by the Oxford Catalysts Group.
Small Size - Big Performance
Microchannel process technology is a developing field of chemical processing that enables rapid reaction rates by minimizing heat and mass transport limitations, particularly in highly exothermic reactions, such as FT, or highly endothermic reactions, such as steam methane reforming (SMR).
This improved performance is achieved by reducing the dimensions of the reactor systems. In the FT microchannel reactors that lie at the heart of distributed BTL production systems, the key process steps are carried out reactor blocks that contain arrays of thousands of microchannels, each with diameters in the range of just 0.1-5 mm (fig. 1). In the reactors process channels filled with a highly active FT catalyst developed by Oxford Catalysts are interleaved with water-filled coolant channels.
The small channel diameter enables chemical reactions to be greatly intensified - the reactions occur at 10 to 1,000 times faster than in conventional systems - while still maintaining efficient and precise temperature control (fig. 2). This leads to higher throughput and conversion efficiencies. In contrast to conventional FT plants, where conversion rates of 60% or less are common, FT microchannel reactors achieve conversion rates on the order of 70%. The catalyst enables the reactors to achieve productivities that are orders of magnitude higher (defined as kg/m3/h) for more conventional systems (fig. 3).
BTL Building Blocks
In contrast to conventional FT plants which only work economically at capacities of 30,000 barrels per day (bpd) or higher, plants using small scale FT microchannel reactors are designed to produce 500-2,000 bpd of liquid fuels efficiently and cost-effectively. This is just one of the features that makes microchannel reactors particularly useful for distributed production systems.
Another is their small size- reactor assemblies are roughly 1.5 m in diameter - and modular construction. The entire FT microchannel demonstration plant for the Güssing (fig. 4) demonstration is contained on a skid with a footprint just 20 feet long by 10 feet wide. The modular construction allows for greater flexibility in plant design and means that plant size can be increased by "numbering up," or simply adding more reactors. It also makes the plants more durable and easier to service because maintenance and catalyst replacement can be carried out by replacing individual modules, rather than requiring prolonged shutdown of the entire system. As a result, the capital costs associated with microchannel reactors are relatively low compared to conventional equipment.
Well Worthwhile
The development of microchannel reactors has been a long, challenging - and exciting - process. And best of all, it now looks like bearing fruit. Their small size, ability to handle large volumes of feedstock to produce quality fuels from a variety of waste sources could help enable the distributed production of next generation biofuels to become a viable economic reality and a practical way to reduce CO2 emissions and amount of waste going to landfill in the near future.