“Access to Talent is a Crucial Factor”
New German Site in Alzey is a Cornerstone of Lilly's European Expansion
In an interview with CHEManager, Edgardo Hernandez, President of Lilly Manufacturing, explains the strategy behind the ambitious investment project.
At the end of February, Eli Lilly and Company revealed plans to invest $27 billion in the construction of four new manufacturing sites in the US. These investments bring the company's total worldwide capital expansion commitments to more than $55 billion since 2020. This package includes strategic investments in production facilities in Italy, France and Ireland as well as the new $2.5 billion site in Alzey, Germany, announced in November 2023. In an interview with Michael Reubold during a visit to the Alzey construction site, Edgardo Hernandez, Executive Vice President and President of Lilly Manufacturing Operations, explains the strategy behind these investments and gives an update on specifically the German project.
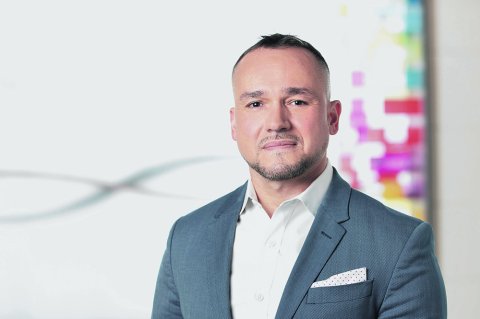
CHEManager: Lilly has launched an unprecedented investment offensive, including the construction of eight new manufacturing sites in the US and two in Europe since 2020. Could you briefly summarize the most important facts about where the new sites will be located and how much you spent on this?
Edgardo Hernandez: Yes, we have announced a more than $55 billion global investment across multiple locations, including Alzey. This investment aims to expand our capacity for producing medicines. Some of these investments are already operational, manufacturing and supplying medicines to patients. The new investments focus on building for the future, particularly in the US, where we are developing new platforms for drug substances, ADCs (antibody-drug conjugates), and RNA. Additionally, we are rebuilding our capabilities for small molecules, as our pipeline had previously shifted to monoclonal antibodies, requiring increased monoclonal capacity. However, we are now witnessing a resurgence of small molecules in our pipeline, and we are excited about building the necessary capacity for the future.
Our preference is to internalize the supply chains.
You're working a lot with CDMOs for the manufacture of small molecules. Do you do it mainly internally?
E. Hernandez: Our preference is to internalize the supply chains. As our molecules' patents expire and demand decreases, we scale down our operations. However, looking to the future, we believe we need to rebuild our capabilities. We always work with trusted partners in the supply chain, including some here in Germany, to supplement our internal resources. These partners are crucial as they help us in various stages of the product lifecycle. Typically, in the late lifecycle, we prefer to outsource molecules to create internal resources for new ones on the horizon.
Since we're here in Alzey, Germany, what's the purpose of this new facility and what is its strategic significance for Lilly in Europe?
E. Hernandez: This facility will be a drug product site, focusing on sterile filling for parenteral products and device assembly, making it one of the largest combination product manufacturers globally. We are building capabilities for current and future platforms here. We chose Germany to tap into the local talent pool and proximity to equipment manufacturers, which allows for quick same-day service. The strategic location near logistics hubs enables efficient resupply of medicines to numerous countries, serving patients globally.
Besides the proximity to suppliers, what other factors do you consider when looking for a new location for a facility? What led to the decision to build the new greenfield site here in Alzey?
E. Hernandez: Access to talent is another crucial factor. Germany excels in STEM fields—science, technology, engineering, and mathematics. When we considered this location, the availability of skilled talent was a significant advantage. Being able to recruit and onboard them efficiently to our facilities is vital. So far, the process has gone exceptionally well, and we are ahead of our recruitment plans. While there is still a way to go, the energy, enthusiasm, and quality of the workforce we've engaged in Germany are impressive.
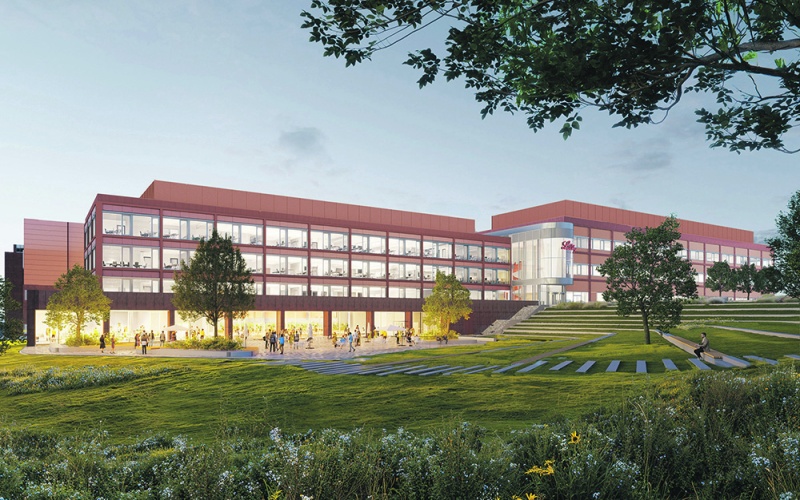
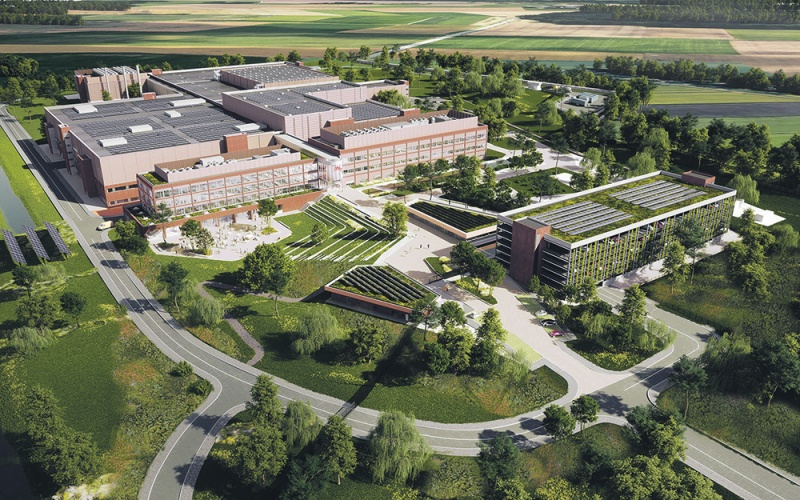
How did the German local or federal authorities support you in terms of incentives, permissions, and approvals so far? Have there been any hurdles?
E. Hernandez: We achieved record speed in obtaining permits and began construction within six months. Both federal and local authorities, including the mayor and city council, have been exceptional partners, helping us navigate the process efficiently. This has been one of the smoothest construction sites we've had, and we are well on the way to keeping to the schedule.
You mentioned in previous interviews concerns about European legislation or changes in legislation regarding IP. Could you elaborate on that?
E. Hernandez: Intellectual property protection is something we continuously work on. When evaluating investment opportunities, we prioritize regions that safeguard our intellectual property, as we invest substantial resources in developing it. This concern isn't exclusive to Europe—it's a global discussion currently taking place.
You said this is one of the smoothest construction sites so far. Could you explain why?
E. Hernandez: Considering the scale of what we're aiming to build here, there will inevitably be challenges. While some issues can stem from the weather, others might arise from the ground conditions, such as compaction. Additionally, we might face shortages in supplies like steel or concrete. These are all potential obstacles we have to navigate.
You broke ground in April last year. Could you share the timeline for the next phases until the facility becomes operational?
E. Hernandez: We plan to complete the foundation work by the end of May this year. After that, we will work on weatherproofing the buildings to protect them from the elements. In December, we aim to start with the interior work on the buildings. We are still looking for support for this. Companies with experience in construction and engineering in the pharmaceutical industry are very welcome to apply. As soon as the interior work has been completed and the equipment is installed, we will qualify it, complete process validation, and submit our findings to regulatory agencies. With these steps, we hope to begin producing medicine for patients by 2027 or 2028. Of course, there are thousands of details involved in reaching these major milestones.
When becoming operational the new site in Alzey will employ up to 1,000 highly skilled workers.
When the facility is operational, you will need a lot of skilled workers. Could you share some insights on how many jobs you will create with this new facility?
E. Hernandez: When becoming operational the new site in Alzey will employ up to 1,000 highly skilled employees such as engineers, operators and scientists, who will leverage state-of-the-art technology, including automation and high-speed manufacturing lines, to produce life-changing medicines. Our goal is to reach around 100 employees by the end of this year, and we will continue to increase that number as equipment arrives, and we need to onboard more skilled employees. We will keep hiring at a fast pace to ensure we are ready for the next phase of the project. Our current progress is well above our target, and we plan to maintain this momentum in the coming years.
There are concerns in European societies about the demographic change and the declining interest in STEM studies. Do you share these concerns or think they will become a challenge for you?
E. Hernandez: We are closely partnering with local universities and colleges, and we were just reviewing this collaboration this morning. We are also working with the Chamber of Commerce or the Federal Employment Agency to generate interest in these careers. Personally, I think these are the coolest jobs in the world, but maybe I'm biased because I'm an engineer. Nevertheless, we continuously strive to educate and spark interest in STEM careers. We've invested significantly in this area and plan to do even more. Our goal is to maintain strong partnerships with educational institutions to foster this interest.
You need a whole bunch of different qualifications to run such a sophisticated facility. Could you elaborate on the types of qualifications required?
E. Hernandez: Our future workforce here will include microbiologists, chemists, engineers, pharmacists, and other professionals. Each of these roles is essential because we require a diverse set of skills for tasks such as quality control, quality assurance, and process science.
Experience wanted!
Lilly is still looking for companies with experience in construction and engineering in the pharmaceutical industry for the interior fit-out of the buildings.
Inquiries and applications to Lilly GermanyYou have already started recruiting. Where do you look, and which tools are you using for recruitment? Do you also look across borders, like in France?
E. Hernandez: Generally, when we recruit talent, we prioritize cultural fit. We have a strong culture centered around operational excellence, with a mission focused on safety first and quality always. Therefore, we seek individuals who align with our Lilly values of integrity, respect for people, and excellence. If candidates possess these traits, we can provide the necessary technical training. Part of our approach involves hiring talent here in Germany and sending them to our facilities in France, Italy, and the US to gain skills and experience. As long as candidates have basic technical knowledge and align with our values, we are willing to invest in their careers.
It's very appealing to work for a pharmaceutical company because you can do good for patients. Also, working at such a modern new site is very appealing to many, especially young people.
E. Hernandez: Absolutely. We focus on early career individuals and have also managed to hire many experienced professionals. Their knowledge and experiences enrich our culture. We strive to incorporate what they bring and continually improve. Our motto is to make things better and better. It's essential to us. Diversity of cultures and different ages or even working styles, it's important to integrate all of these aspects for an innovative team.
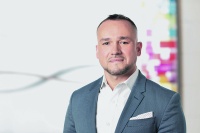
ABOUT
Edgardo Hernandez is Executive Vice President at Eli Lilly and Company and President of Manufacturing Operations. His Lilly career started in 2005 as engineering services leader and later as site head of various production sites. From 2018 to 2021, he served as Senior Vice President responsible for global parenteral manufacturing, emerging markets manufacturing, drug-product contract manufacturing, packaging, and distribution operations. Ed provided oversight for manufacturing sites in 12 countries across North and South America, Europe, and Asia; that manufacture the final parenteral product formulations of Lilly medicines. Ed Hernandez holds bachelor’s and master’s degrees in chemical engineering from the University of Puerto Rico and North Carolina State University, respectively.