Silicone Recycling without Loss of Quality
Interview with Klara Yoon, Tina Rose and Stephan Enthaler, New Dawn
Berlin, Germany-based start-up company New Dawn Silicones —formerly known under the name We Are Galaktika — has developed a resource-efficient chemical recycling technology that allows silicones to be reused without loss of quality. With this idea in the field of sustainable chemistry, the start-up addresses one of the most pressing environmental problems. The use of innovative technology makes it possible to use end-of-life silicones as the starting material for new, high-quality silicones, thus contributing to a circular economy that saves energy and resources while also having a more positive climate footprint compared to the use of new raw material. The founders are supported by the International Sustainable Chemistry Collaborative Centre (ISC3).
CHEManager: Originally, you wanted to produce a more sustainable menstrual cup, in the meantime this has evolved to become an innovative recycling technology for used silicones. What prompted you to change course?
Tina Rose: My passion is the circular economy and our drive from the beginning was to reduce the carbon footprint of silicone and contributing to ensuring that the conditions of a circular economy are also applied in the silicone industry. Everything else follows these overarching goals. The extension of our basic idea from a single product to silicone recycling for many applications, came about through our participation in the Circular Economy Incubator of Impact Hub Berlin. Among other things, we carried out impact calculations and very quickly realized that we could not limit it to menstrual cups if we want to make a difference in our carbon footprint. In the end, with Stephan Enthaler we met exactly the person who was still missing from our puzzle.
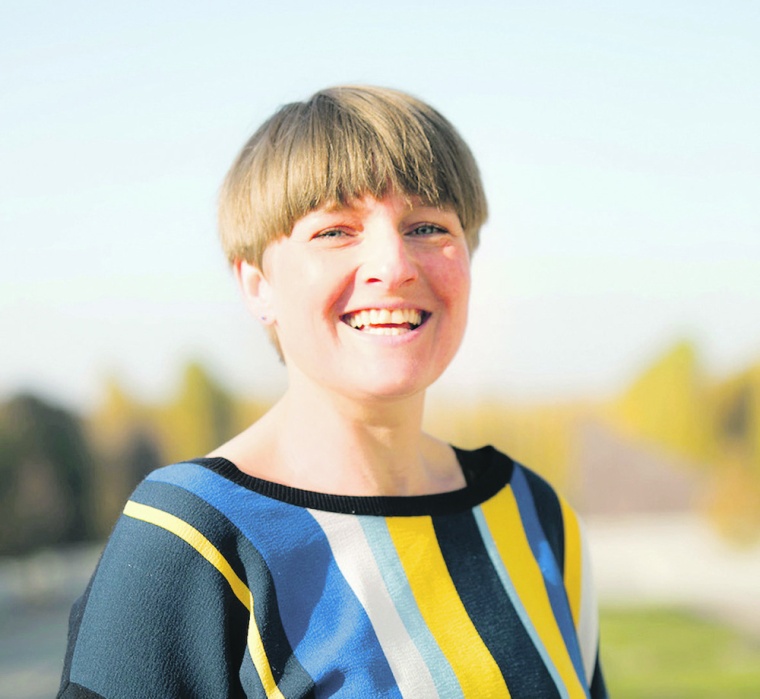
Klara Yoon: Stephan shares our values and, with his research in the field of sustainable chemistry, brought us the right building block: the technology with which we can recycle silicones. That’s why we always talk about a ‘magic fit’ when we look back on that first meeting.
What is special about recycling silicones and what makes the process so particularly sustainable?
Stephan Enthaler: Unlike the classic mechanical recycling route, in which new products are physically formed from plastic waste, which can result in quality losses and make it difficult to separate additives, we have opted for a chemical recycling method for silicone waste. In this process, silicones are broken down into smaller units at the molecular level, purified and later reassembled into new silicone. As a result, the recycled silicone obtained has a consistent or higher quality, or the properties can be customized for the customer, id est, it is theoretically possible to obtain high-quality medical technology products from silicone waste using chemical recycling (upcycling), for example. In addition, there are also advantages in terms of resource efficiency, energy efficiency, CO2 footprint, etc. compared to the new production of the silicone, for example, from silicon dioxide and fossil resources, so that chemical recycling methods can contribute to a resource-conserving circular economy.
T. Rose: In addition to the obvious savings in resources and CO2, our product will also contribute to the ESG goals of companies and industries that use silicones in their products and production.
How does your passion, the circular economy, come into play here?
K. Yoon: The circular economy is the key point of our idea, but not possible without a take-back scheme. It’s always a combination of technology and access to end-of-life material.
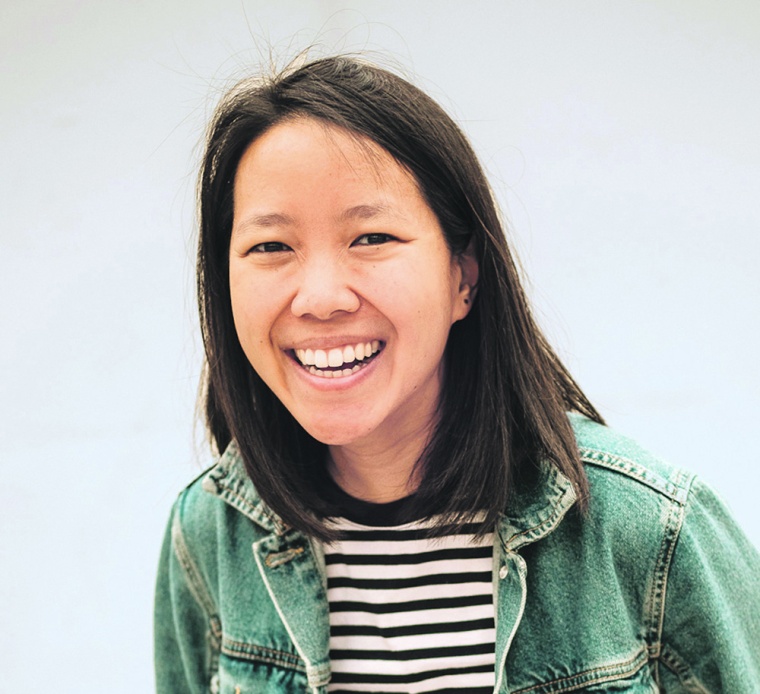
T. Rose: Exactly, and that’s why we’re also working on proofs of concept in three areas: Firstly, in the manufacturing industry, for example with the recycling of cable sheathing as well as silicone applications in machines. Secondly, in medical technology and the care sector — here we are working on a take-back scheme. And thirdly, household waste, which still presents us with the greatest challenge due to the organization of the take-back scheme. We’re still in the early stages here, but we’re already in dialogue with the waste management industry in many areas.
What is the next step on your way?
S. Enthaler: There are initial concrete inquiries from medical technology, the automotive industry, etc. We are in the process of recycling industrial silicone waste and collecting more data. Our medium-term goal is to demonstrate a circular economy approach for a selection of silicone products based on chemical recycling.
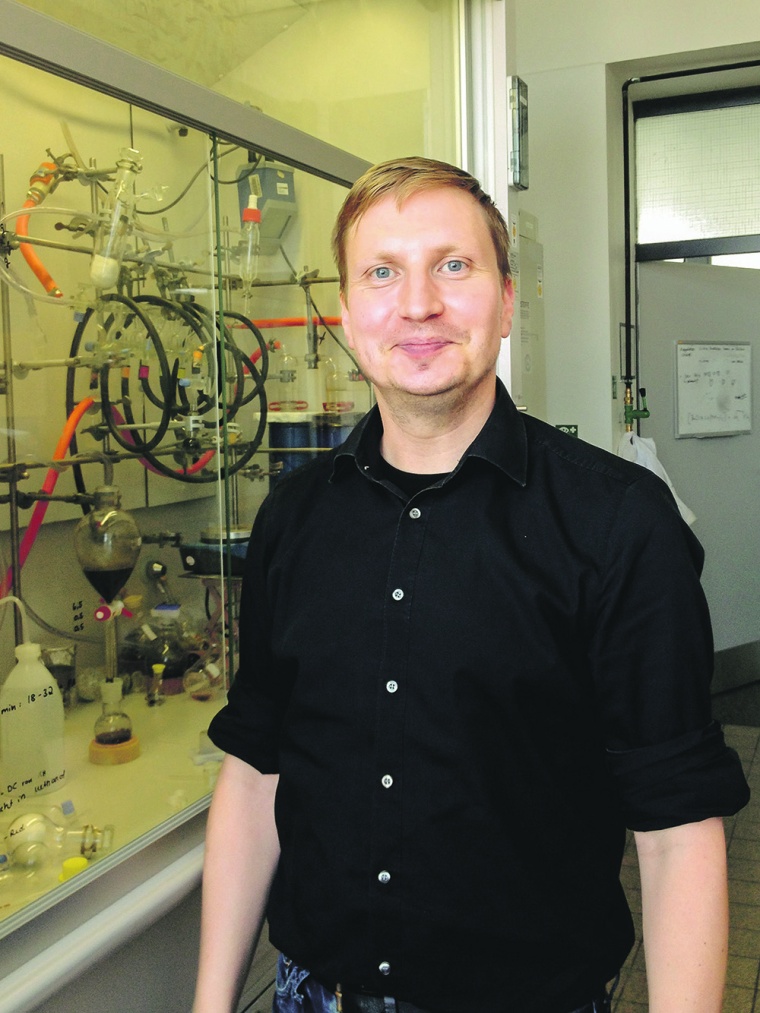
K. Yoon: Another milestone after winning the ISC3 Innovation Challenge is the development of mentioned proofs of concept with global companies from the pharmaceutical industry and automotive sectors. The contact has been established through coaches and mentors and increased visibility — not least through the support of the ISC3, which has enabled us to present our idea to a broader professional audience worldwide and to investors with know-how and experience beyond the chemical industry.
T. Rose: We are currently looking for funding to take the next step: a test facility to transfer our laboratory process to mini plant level in 2023 to further improve the process and collect even more data.
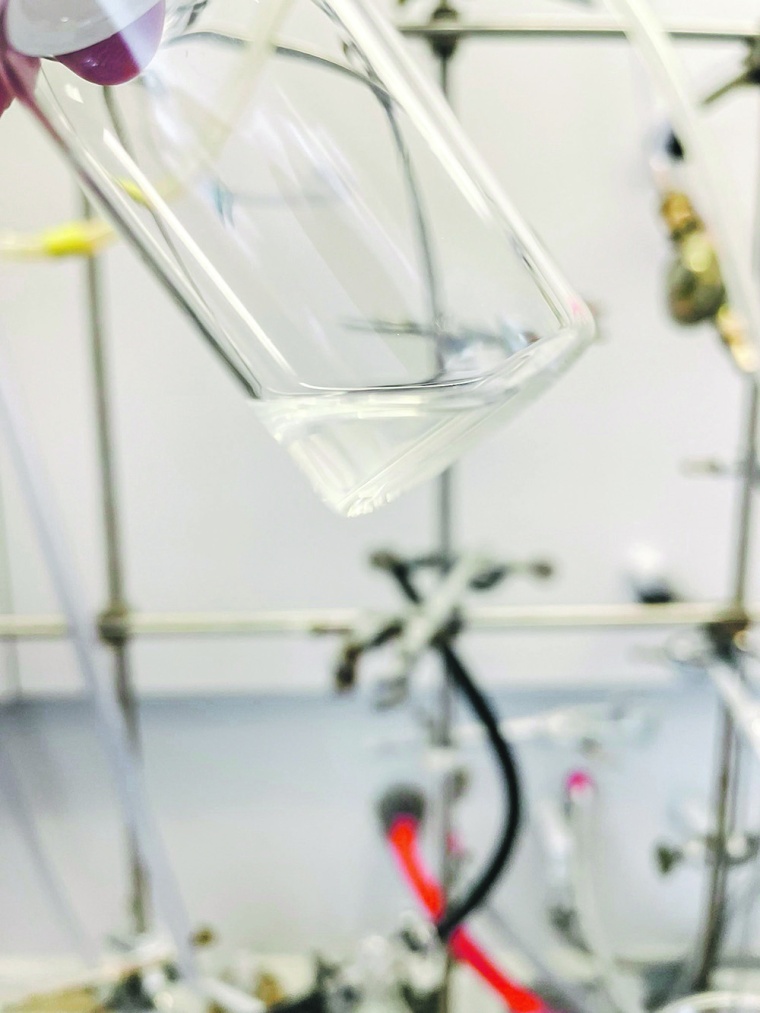
Business Idea
Silicone Recycling Technology
The female-led start-up New Dawn Silicones (aka We Are Galaktika) from Germany has developed a resource-efficient chemical recycling technology for end-of-life silicones and is thereby tackling one of the most pressing environmental problems of our society.
The innovative technology is a beneficial building block for a circular silicone economy. In more detail, end-of-life silicones collected from customers were successfully converted in the initial depolymerization step to low-molecular weight compounds/monomers solvent-free, at low temperature and within short reaction times.
Different types of monomers can be obtained depending on the molecular structure of the parent silicones, e.g., linear, linked or cross-linked silicones. The monomers were collected by reactive distillation; therefore, all types of internal and external contaminations (e.g., additives, plastics) present in the silicone waste are separated by the distillation process and the monomers are obtained in excellent purities. During the distillation process the monomers can be already converted by polymerization to new (recycled) high quality, e.g., cyclic silicones, which are applicable as a platform for all types of silicone products (e.g., medicinal or food grade). Importantly, the technology is easily scalable and is designed following the requirements of sustainable and resource-efficient chemistry.
Lately, the company finalized the lab process which will be submitted for patent application in Q1/2023. They are currently raising money for building a mini plant to collect data, optimize processes at plant level and then run, operate, and test it with the waste from partners. The long-term goal is to license the technology which is planned for 2026, after the scale up with the pilot plant.
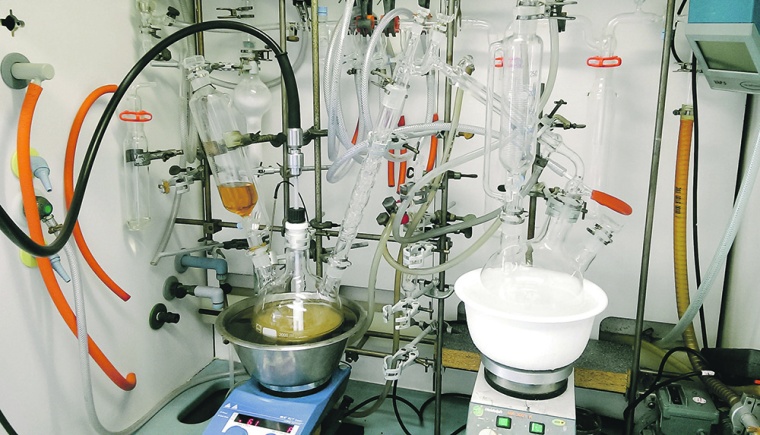
Elevator Pitch
Milestones and Roadmap
The waste caused by end-of-life silicones is an underestimated environmental problem of our society. New Dawn Silicones’ vision is to transform the linear silicone industry into a circular one by using existing resources more effectively.
They not only reduce the carbon footprint by 60% compared to the production of virgin silicone but contribute to the conservation of biomass and diversity.
The mission is to completely close the material cycle for silicone products and to be able to also recycle multi-component materials.
Thus, compared to other silicone recycling processes, for instance mechanical recycling, New Dawn’s silicone comes out with the same quality as the virgin silicone.
Milestones
2021
- Project kick-off under the name We Are Galaktika
2022
- Joining the incubator program „Circular Together“ of Impact Hub Berlin
- Winner of the ISC3 Innovation Challenge
2023
- Name Change to New Dawn
- Silicones
- Seven Proof of concepts with partners from various industries (automotive, medical, silicone molding etc)
Roadmap
Q1: Patent application and founding of New Dawn Silicones GmbH
Q2: Pre-Seed funding
Q3: Building mini plant
2023
- 2t/y Etermal Silicone
- Seed funding
2025
- Pilot plant, 1,000 t/y Eternal
- Silicone
2026
- Licensing of the technology
2028
- 64.000 t/y Eternal Silicone with licensees/10% of EU Market