Safe Testing with Digital Fingerprint
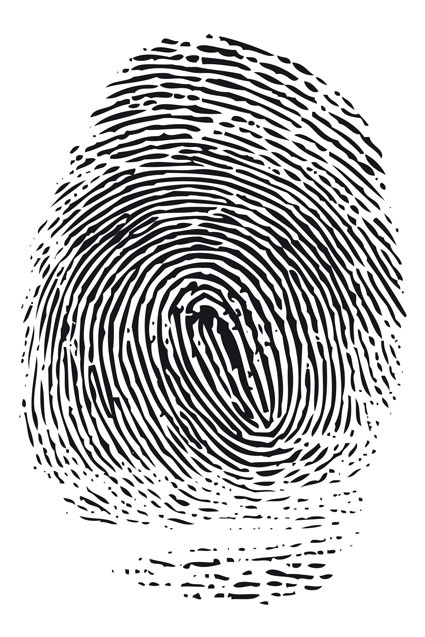
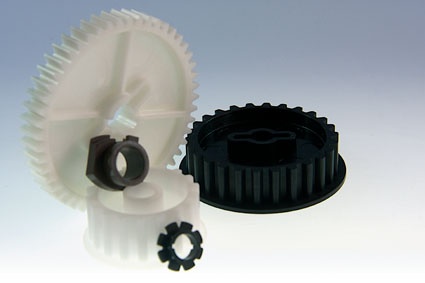
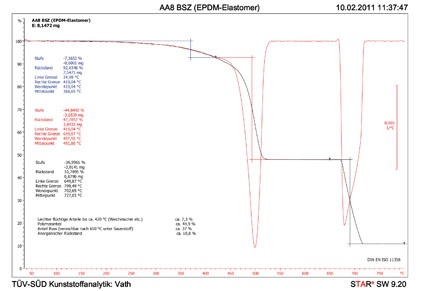
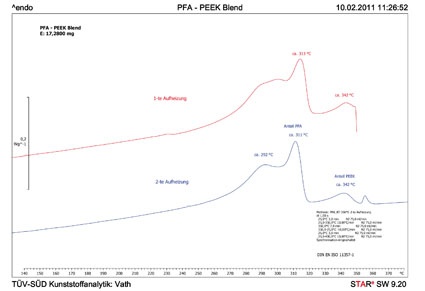
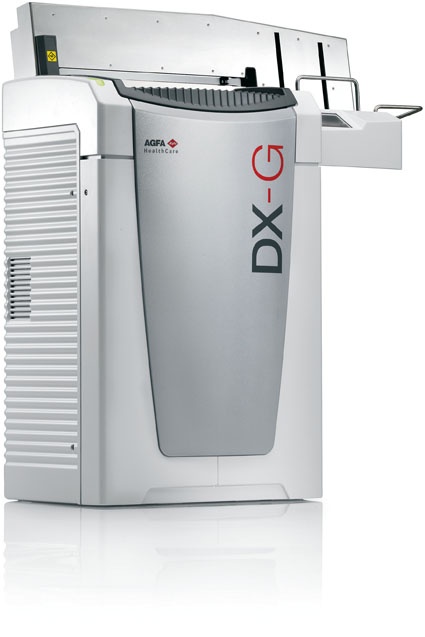
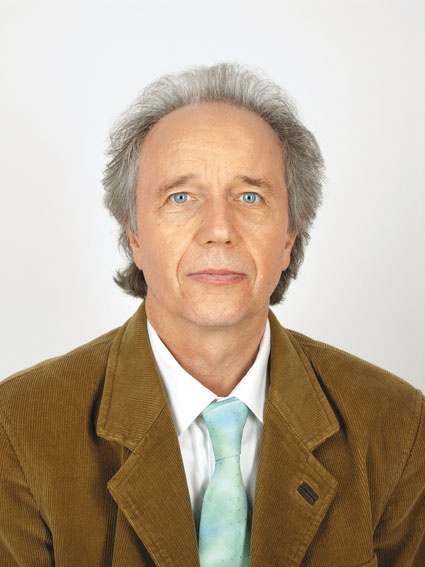
VIP-Visions In Plastics - High-performance polymers are increasingly used in medical technology applications. Incoming goods inspections must be optimised to ensure reliable and cost-effective validation of the special properties of these innovative plastics. On behalf of a manufacturer of medical devices, TÜV Süds polymer professionals developed optimised incoming inspection.
Safety and functional reliability are more important in medical technology than in almost any other industry sector. As materials, innovative plastics play a special role in this context. Today, they account for significantly more than 50% of all materials used in medical technology. High-performance polymers are increasingly replacing metals - not only for disposable products such as syringes and catheters, but also for long-term components and equipment. This development is due in particular to the increasingly sophisticated material properties that can be realised by using these specialist plastics.
These include but are not limited to wear and friction properties, flammability rating and resistance to the high temperatures, X and gamma radiation which are used for purposes including sterilisation of medical devices. Polymers further offer increasingly light weight and freedom of design - two advantages for which demand is also growing. Materials used for medical devices must generally offer a combination of several functions, e.g. the material must be sterilisable while also offering transparency and electrical conductivity.
Legal Requirements at a Glance
While high innovation rates in the medical devices sector increase the race to improve the properties of high-performance polymers, manufacturers of clinical equipment have to meet strict national and international standards and directives. In a sector where safety is of paramount importance, the quality assurance of high-tech plastics is high on the agenda. Medical device manufacturers face the challenge of ensuring thorough yet cost-effective verification that the supplied plastic components fulfil the special properties required. This reduces the liability risks, offering protection against significant additional costs.
Agfa-Gevaert HealthCare GmbH is one of the leading suppliers of integrated imaging systems to be used in radiology, orthopedics, cardiology and mammography. Many of the high-performance plastic components, including bearings, ports, parts of casings and cogwheels, are made by external suppliers. Selection of the right type of material is critical for design and must take into account all requirements that must be fulfilled by the component later on, including joining properties, paintability, load and flammability rating.
To obtain a reliable, premium-quality component, the right type of design must be combined with the right type of material. Deviation from the defined material type involves the risk of early component failure in the form of premature wear or even fracture. The consequences are generally customer complaints and loss of reputation.
To ensure a high level of quality and safety for its clinical solutions, Agfa-Gevaert prioritises effective quality management for the supplied components. Quality management must not only ensure that the components have the required load rating, but also determine their compliance with certain limit values. If excessive levels of heavy metals or flame retardants which are not approved for use in a medical device are found, manufacturers may have to stop delivery or recall their products.
Also important in this context are 'UL listings'. These certification marks are issued by Underwriters Labratories (UL), a third-party certification organization, and list the materials which demonstrably meet applicable safety regulations. Manufacturers using a material that is not, or not fully, UL listed risk a ban of their products abroad.
Optimised Incoming Inspection
In this case, the challenges for quality assurance lie in the special properties of the technical plastics. Validation of these properties in conventional incoming inspection is often far too complex and costly. Agfa-Gevaert commissioned the experts at the TÜV SÜD Institute for Plastics to apply tailored positive material identification (PIM) to verify that the supplied components meet the special quality requirements. In a first step, the experts use samples of each type of plastic provided by the manufacturers as the basis for recording reference spectra and curves for each type of plastic. They then save these spectra and curves in a database for later use. Once this is done, the components supplied to the processing companies can be analysed in detail. For this purpose, the experts rely particularly on infrared spectroscopy and thermogravimetry (TG), but also on differential scanning calorimetry (DSC) and energy-dispersive X-ray fluorescence (EDX) analysis.
Positive Material Identification Based on a Combination of Methods
Infrared spectroscopy is a physical analysis method which uses infrared light to excite vibrations in the molecules of a plastic material. In infrared spectroscopy, part of the radiation is absorbed by the molecules while the remainder is transmitted unhindered through the material. The amount of light absorbed or transmitted can be measured and plotted in absorption or transmission spectra. With the help of these spectra, the experts can then identify possible non-conformities with the specified type of plastic.
In thermogravimetry (Fig. 1) the test specimens are heated at a pre-defined temperature and in inert gas atmosphere until pyrolysed. Inert gases are chemically inactive and prevent the specimen from combusting. In the inert gas atmosphere, the organic matrix of the plastic evaporates and the accompanying weight loss is recorded. In a second step of the analysis, the inert gas is replaced by oxygen, causing the soot in the sample to burn off and leave the inorganic components. On the basis of this result, the plastics specialists can then determine the quantitative composition of the samples. Subsequently, the quality of the inorganic residue (glass fibre, glass balls etc.) can be analysed under a stereomicroscope.
Differential scanning calorimetry (DSC) (Fig. 2) is a thermoanalytical technique based on heat flow measurement. The procedure uses two identical sample dishes: one dish holds the sample while the other, the 'reference dish', remains empty. Both dishes undergo a pre-defined temperature program during which exothermal and endothermal effects are measured. As the sample changes the thermal performance of the first dish, measurement provides different values. The difference between the measured values of the two dishes equals the change in heat flow and provides information about properties of the sample including its oxidation stability, processing quality, purity, glass transition, reaction kinetics, degree of cure, crystallinity, and softening and melting behaviour.
Last but not least, energy-dispersive X-ray fluorescence spectroscopy (EDX) enables quantitative analysis of substances in excess of RoHS limits to be performed. RoHS stands for Restriction of the Use of Certain Hazardous Substances and covers EC directive 2002/95/EC on the restriction of the use of certain hazardous substances in electrical and electronic equipment and its transposition into national law. The quantitative analysis is aimed at heavy metals including lead, mercury and cadmium, and bromium, which is used as a flame retardant.
Thorough Coordination
The targeted combination of several analytical methods increases both the efficiency and the reliability of validation. The results can be summarized in an analysis package, which then provides a digital fingerprint of a certain type of plastic. This fingerprint permits the experts to reliably identify and validate the high-tech polymer. In the case of compliance, the component can then be approved.
A decisive factor for the successful quality assurance of high-performance polymers is the targeted selection and coordination of analytical methods customised to the types of plastic to be tested. Incoming goods inspection by means of a sampling approach minimises the risk of premature component failure for manufacturers.
The success of positive material identification by means of a combination of the above analytical methods in particular shows that cost-effectiveness and safety need not be mutually exclusive. The third-party experts from the Institute for Plastics have over 40 years of experience and support manufacturers and processing companies in exploiting the full potential of high-performance polymers even in cases involving complex terms of reference.