High Level Chemical Logistics
As an independent system of uniform third party assessments, SQAS — Safety and Quality Assessment System —was initiated to evaluate the performance of logistics service providers and chemical distributors.
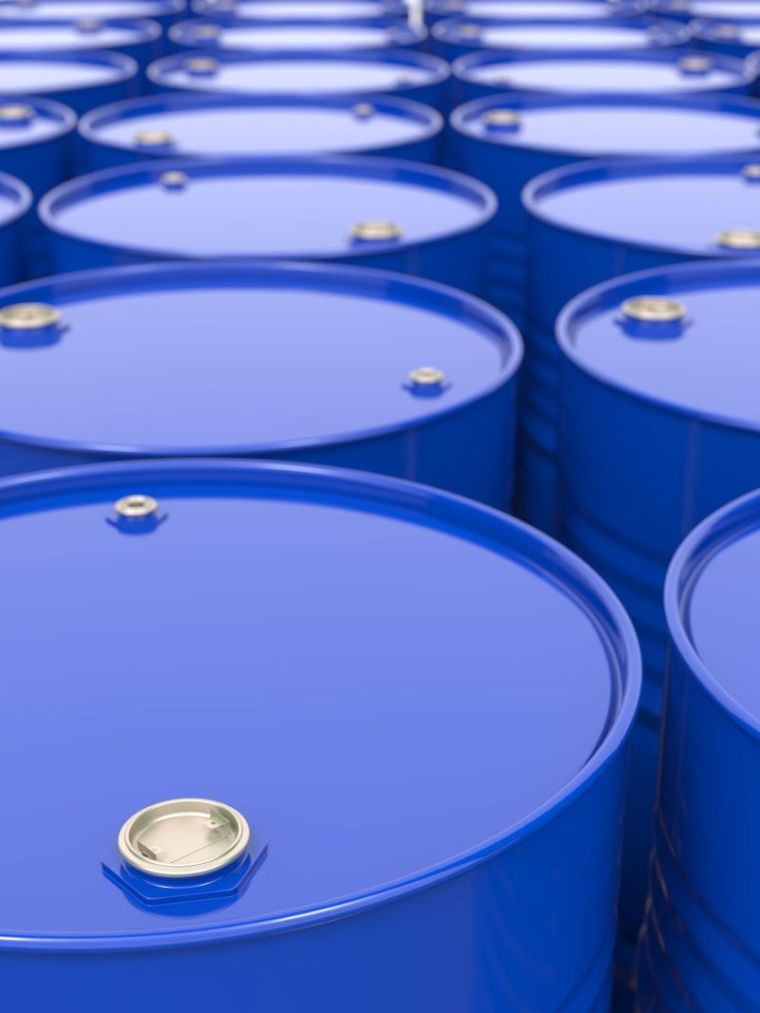
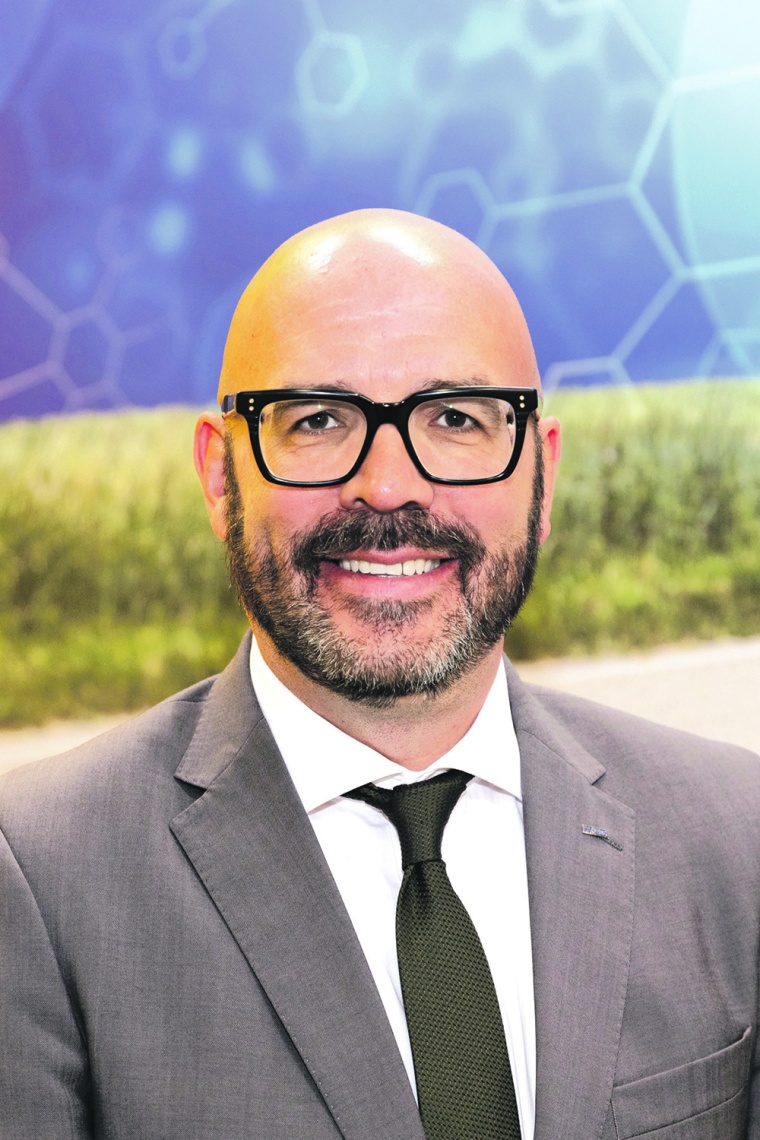
Furthermore, it serves a more reliable partnership between logistics service providers and the chemical industry. In the network of logistics specialist Dachser, 27 branches have already been SQAS assessed. Recently, the San Sebastián location in Spain has joined them.
The Spanish chemical industry continues to grow. For last year, the Spanish trade association FEIQUE forecast a revenue increase of 2.6% to € 67.6 billion for chemical products. Spanish chemical companies generate about 60% of their revenue abroad. This makes them an important driver of Spain’s export industry.
It’s wide of the mark to say that all chemical products are dangerous goods. However, when Dachser Iberia introduced its own dangerous goods system on the Iberian Peninsula about 5 years ago, it put itself in a very good position to support this growth in Spain’s chemical industry. Independent parties like to confirm that the Dachser Chem-Logistics industry solution offers considerable expertise. After recently going through the SQAS assessment procedure for logistics services, the San Sebastián branch has joined the list of Spanish locations as an SQAS assessed company.
High Transparency
SQAS started out as a joint initiative by chemical companies and the European Chemical Industry Council (CEFIC) to develop a transparent process that ensures logistics providers adhere to the highest standards regarding quality, safety, the environment, and social responsibility. This involves having independent experts assess the companies using a standardized questionnaire.
Back in 2016, Dachser Barcelona became the first branch in Spain to go through an SQAS assessment.
“The SQAS assessment is particularly important for us as the local chemical industry needs a strong and reliable logistics partner especially for export. The most important export countries for our customers in the chemical sector here are Germany, France, Italy, and Poland,” explains Antonio Garrido, team leader External Assessment & ADR European Logistics at Dachser Iberia in Madrid. Exports account for around 23% of total revenue with chemical products in Spain.
Garrido adds that successfully getting through an SQAS assessment is a challenge. The central element is a detailed questionnaire divided into several general topics: management system and responsibility, risk management, human resources, as well as performance analysis and management review.
High Standards
At Dachser’s head office in Kempten SQAS expert Nicole Sommerlatte and her team support the preparation and completion of the assessment in the European branches, including San Sebastián. “This guarantees that we never lose sight of business practice and that any improvement potential we identify can always be transferred to other branches,” states Sommerlatte.
This also means that the in-house aims are often set even higher than those of the independent auditors. All reports have to be renewed regularly: Therefore, ten reassessments were conducted in 2019 and six more are planned for this year, along with two first assessments.
Altogether, 27 branches have already been SQAS assessed in Dachser’s European network, with no differences between regions. The most important effect of such a special evaluation is that it improves in-house controls and processes. With appropriate training in improved processes, employees can carry out their tasks safely and deliver better quality. And that applies to downstream service providers as well. Garrido acknowledges: “SQAS implementation is another way for us to reinforce our position as preferred partner for companies in the chemical industry.” (sa)
Interview with Michael Kriegel, Dachser: Milestone for Transparent Cooperation
Michael Kriegel, Department Head of Dachser Chem-Logistics, gives some insights about the relevance of SQAS for both sides — the chemical industry as well as the logistics provider. CHEManager editor Sonja Andres asked the questions.
CHEManager: Mr. Kriegel, what does SQAS mean in detail?
Michael Kriegel: Back in 1994, Europe’s chemical industry created SQAS — a milestone for transparent cooperation with logistics providers. Based on a single standardized questionnaire for the whole of Europe, it paves the way for sound partnerships with the chemical industry. It is undisputed that the chemical industry places higher demands on its logistics providers than other industry segments, especially in terms of quality and safety. I see SQAS as the entry ticket for a logistics company to begin working with the chemical industry.
For us, SQAS doesn’t simply mean completing a one-time audit; it’s rather a philosophy, a daily standard that we consistently live by in the company. Three years after a site’s initial audit, a reassessment is conducted. It’s much more challenging to demonstrate that something you’ve already implemented is still in effect than it is to achieve a certain standard once, which is what makes SQAS valuable for Dachser.
Why did Dachser choose to audit branches all over Europe?
M. Kriegel: Almost 40 chemical companies throughout Europe are members of the SQAS Service Group. A valid SQAS assessment is a requirement for working with them. If, after winning a tender, a logistics provider cannot present such an assessment, the contract will stipulate that they must arrange for an audit to be performed within a certain period of time.
15 years ago Dachser recognized that SQAS was a way to present its existing uniform standards transparently to the outside world. In the past, Dachser has always been able to implement the requirements quickly and successfully. The development of our European SQAS sites shows this very clearly. In 2010, for example, we had 14 branches assessed according to SQAS Transport Service. Today that number has grown to 27 branches in eight European countries. In addition, three of our sites have been assessed according to SQAS Warehouse. We achieved above-average results in all assessments. One way to tell how much importance the company attaches to this topic is the fact that they created an own central head office position to coordinate and support the audits together with the branches.
A good example of how quickly and successfully audits can be implemented is Dachser Iberia. In 2013 the long-standing joint venture partner was acquired and integrated into the European network. After the successful implementation of our own dangerous goods organization, we had the first branch in Barcelona audited according to SQAS Transport Service in 2016. Since then, two more successful assessments have followed on the Iberian Peninsula.
What are the benefits for chemical companies choosing a logistics service provider with SQAS?
M. Kriegel: Thanks to SQAS, all companies in the chemical industry can be sure that their logistics provider delivers very high standards of quality, environmental management, health, and safety, and that it is committed to living up to its corporate social responsibility. And that the provider regularly proves this in accordance with a standardized European framework.
Moreover, companies that are also a member of the SQAS Service Group not only have the opportunity to read up on all the assessment details at any time, but they can also take part in the assessments in person to see for themselves how high the standards are. That’s really the most transparent and effective way to evaluate a logistics provider.
Chemical Companies and their Logistics Service Providers
Safety & Quality Assessment for Sustainability (SQAS) is a system of uniform third party assessments to evaluate the performance of logistics service providers (LSPs) and chemical distributors. SQAS assessments cover quality, safety, security, environment and CSR (corporate social responsibility). The SQAS assessment reports allow chemical companies to evaluate their logistics service providers according to their own standards and requirements.
SQAS, managed by CEFIC, the European Chemical Industry Council, is a key element of Responsible Care in logistics operations.
Chemical companies use the SQAS system in support of the risk management of their logistics activities as part of product stewardship. The reports provide a good insight in the strengths and weaknesses of their (potential) service providers. The assessment reports can help chemical companies in their selection processes of new service providers and for the ongoing evaluation of the standards and performance of existing cooperations.